- May 1, 2025
- Posted by: feinuojixie
- Category: Injection Molding News
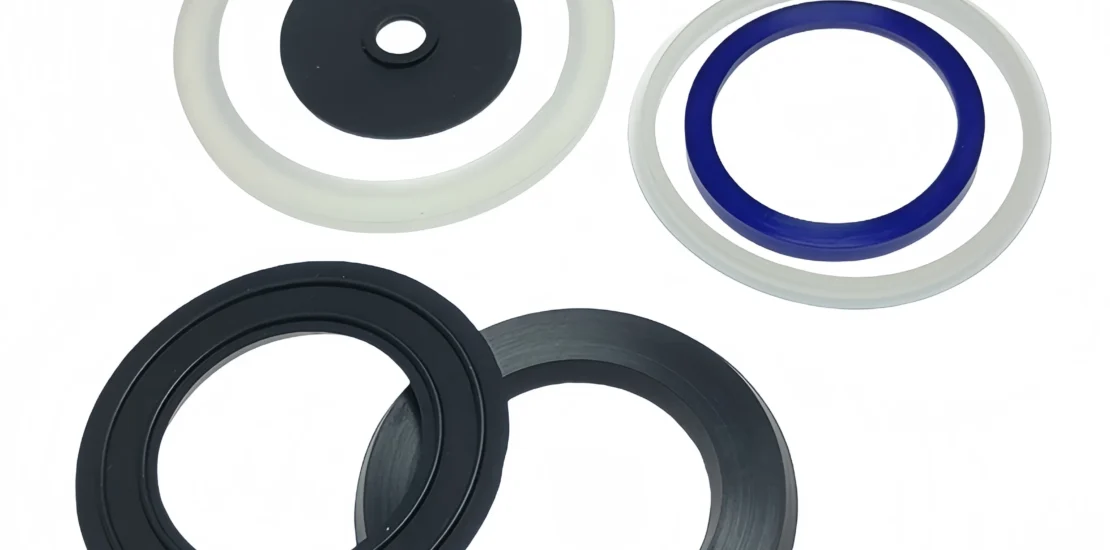
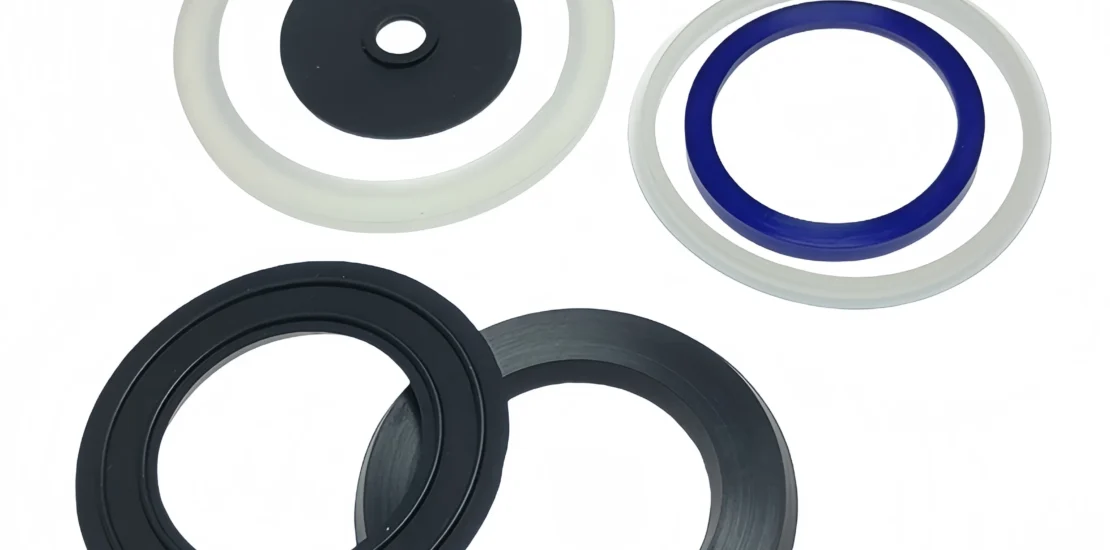
As the world shifts toward a greener future, the automotive industry stands at the forefront of change. Consumer demand for eco-friendly cars has never been higher, prompting manufacturers to rethink every aspect of vehicle production. Among these changes, injection molding automotive part manufacturing plays a pivotal role. By adopting sustainable production methods, manufacturers can significantly reduce their carbon footprint while maintaining the high standards of performance and safety expected in today’s vehicles. This article delves into how sustainable injection molding practices are shaping the future of eco-friendly cars, starting from the very parts that form their foundation.
Understanding Injection Molding for Automotive Part Production
Injection molding is a highly versatile manufacturing process used to create a wide range of automotive part with precision and efficiency. The process involves injecting molten material, typically plastic or composite, into a mold where it cools and hardens into the desired shape. In the context of automotive manufacturing, injection molding is crucial because it enables mass production of complex, durable parts while minimizing waste. From dashboards to door panels, many essential components of a vehicle are produced using this method. With the right approach, injection molding automotive part production not only delivers quality but also offers an opportunity to align with sustainable manufacturing practices.
The Role of Material Selection in Sustainable Injection Molding
Choosing the right material is fundamental to achieving sustainability in injection molding automotive part production. Traditional plastics derived from fossil fuels contribute significantly to environmental degradation. To counter this, manufacturers are increasingly turning to recyclable, biodegradable, and bio-based materials. Polymers such as polylactic acid (PLA) and recycled polypropylene are gaining popularity because they reduce dependency on virgin resources and lower greenhouse gas emissions. Additionally, innovative composite materials that incorporate natural fibers like hemp or flax provide the strength required for automotive part while enhancing biodegradability. Sustainable material selection is not just an environmental imperative; it also reflects a brand’s commitment to responsible production.
Energy-Efficient Practices in Injection Molding Automotive Part Manufacturing
Sustainability in injection molding automotive part production extends beyond material choices to include energy-efficient manufacturing practices. Traditional hydraulic injection molding machines are being replaced by all-electric models that consume significantly less energy. Furthermore, advancements in process optimization, such as better temperature control and shorter cycle times, directly reduce the carbon footprint of production. Facilities are also investing in renewable energy sources to power their operations, making the entire production cycle greener. Implementing these energy-saving techniques not only benefits the environment but also results in cost savings and increased competitiveness in a market that increasingly values eco-conscious practices.
Lightweight Automotive Part: The Key to Greener Vehicles
One of the most impactful contributions of injection molding to sustainable automotive manufacturing is the production of lightweight automotive part. Reducing a vehicle’s weight directly enhances fuel efficiency and decreases emissions over its lifetime. Injection molding enables the creation of intricate, lightweight designs that maintain structural integrity without adding unnecessary mass. For example, reinforced plastics and specialized composites allow for thinner, stronger components. The ability to design lighter parts without compromising performance is a crucial factor in developing vehicles that meet stringent environmental standards while satisfying consumer expectations for safety and durability.
Innovations Transforming Injection Molding Automotive Part Production
The field of injection molding automotive part production is undergoing a revolution fueled by technological innovations. Smart manufacturing systems equipped with sensors and AI analytics provide real-time monitoring and optimization of production processes. Automation reduces human error and ensures consistent quality, while digital twin technology enables virtual simulation and testing of molds before physical production, minimizing material waste. Additionally, additive manufacturing techniques are being integrated with injection molding to produce more complex and customized parts efficiently. These innovations are not just enhancing productivity—they are setting new benchmarks for environmental responsibility across the automotive industry.
Case Study: Automotive Companies Leading the Way with Sustainable Injection Molding
Several leading automotive brands are already showcasing the potential of sustainable injection molding automotive part strategies. For instance, BMW has incorporated natural fiber composites into its vehicle interiors, reducing both weight and environmental impact. Similarly, Ford has partnered with suppliers to develop parts made from recycled ocean plastics, demonstrating a commitment to circular economy principles. These companies prove that sustainable practices are not only achievable but also provide competitive advantages in the marketplace. Their success stories serve as powerful examples for other manufacturers seeking to integrate sustainability into their production models.
Future Trends: What’s Next for Sustainable Injection Molding Automotive Part Manufacturing
Looking ahead, several exciting trends are poised to further revolutionize sustainable injection molding automotive part production. The development of fully biodegradable polymers offers the promise of automotive parts that naturally decompose at the end of their life cycle. Closed-loop recycling systems, where used parts are reclaimed and reprocessed into new components, are gaining traction. Advances in mold design, including modular molds and 3D-printed molds, are improving efficiency and reducing material waste. As regulatory pressures increase and consumer expectations evolve, innovation in sustainable manufacturing will become even more critical to the success of the automotive industry.
Building the Future of Eco-Friendly Cars with Sustainable Manufacturing
Sustainable injection molding for automotive part is more than a trend—it is a necessity for the future of eco-friendly cars. From material selection to energy-efficient production and groundbreaking innovations, every step of the injection molding process offers opportunities to reduce environmental impact. Automotive manufacturers that embrace these practices are not only contributing to a healthier planet but also positioning themselves as leaders in a rapidly changing industry. By investing in sustainable injection molding today, the automotive sector can drive us all toward a greener, more sustainable tomorrow.