- May 6, 2025
- Posted by: feinuojixie
- Category: Injection Molding News
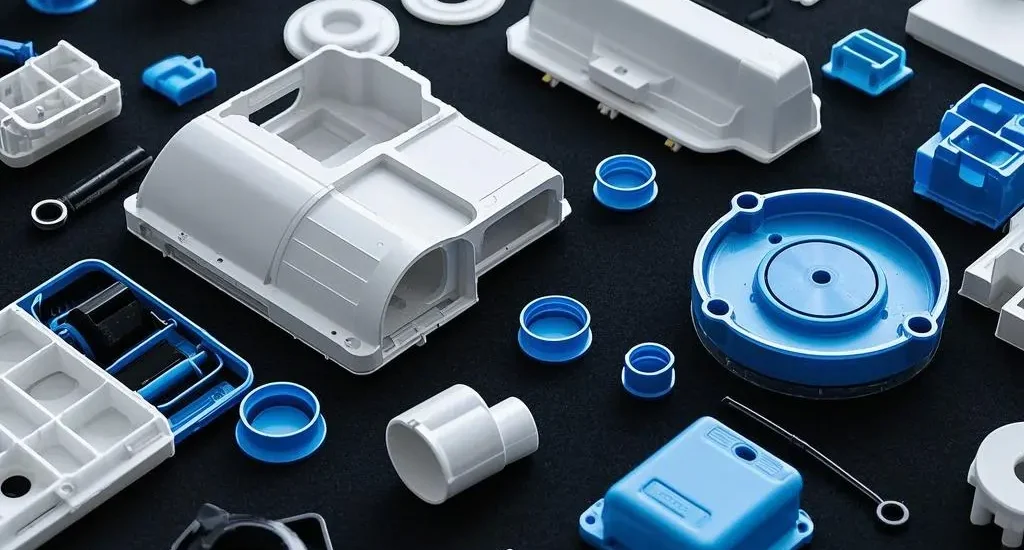
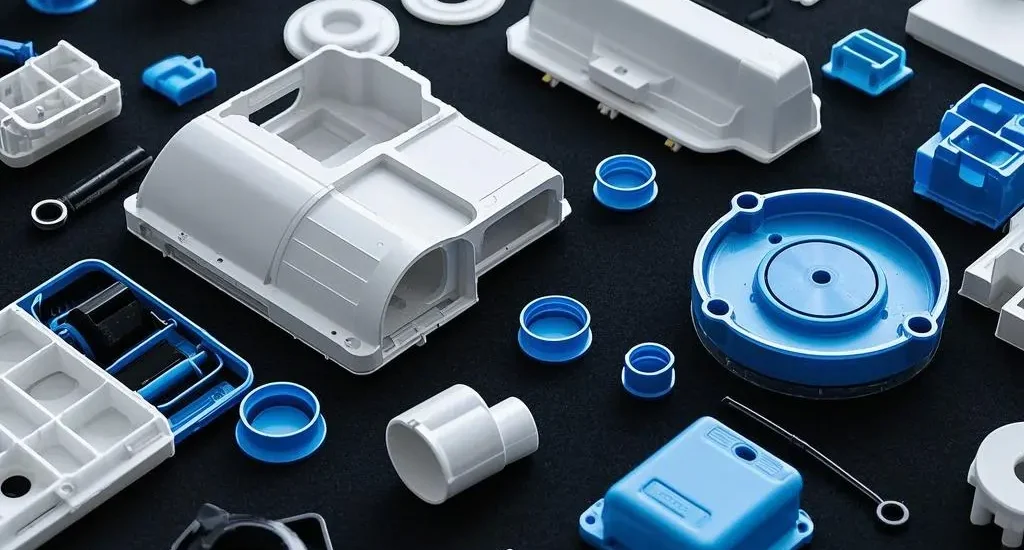
Large part injection molding is gaining traction as a game-changing solution for producing oversized plastic components in a wide range of industries. From automotive body panels to large storage containers and industrial equipment housings, this process allows manufacturers to scale up production while maintaining exceptional accuracy and structural integrity. One of its key attractions lies in its ability to replace multi-piece assemblies with single, robust components—significantly reducing manufacturing complexity and cost. As global markets demand higher production volumes and more sophisticated product designs, large part injection molding is quickly becoming a cornerstone of modern manufacturing strategy. Its combination of strength, repeatability, and efficiency positions it as an indispensable technique in the production of durable, high-performance plastic parts.
Understanding the Fundamentals of Large Part Injection Molding
Large part injection molding is a specialized manufacturing process designed to produce sizable plastic components using high-tonnage injection molding machines. Unlike standard molding, this process involves much larger molds, higher clamping forces, and precise control of material flow to fill expansive cavities. The machines used often exceed 1,000 tons of clamping force and require advanced engineering to ensure consistent quality. Materials like polypropylene, ABS, and high-impact polystyrene are commonly used due to their flowability and strength. Additionally, mold design plays a crucial role—incorporating large gates, balanced runner systems, and sophisticated cooling strategies to prevent defects. Understanding these technical elements is essential for maximizing efficiency and part integrity during production.
Key Benefits of Large Part Injection Molding in Modern Manufacturing
The benefits of large part injection molding are numerous, particularly for manufacturers aiming to scale operations without sacrificing quality. One major advantage is the reduction of part assemblies. Instead of joining multiple small pieces, a single molded part can achieve the same structural function—saving labor and minimizing potential points of failure. The process also offers superior strength and dimensional stability, especially when reinforced materials are used. Tight tolerances are achievable even at large scales, making it suitable for precision-dependent applications. Moreover, once the tooling is in place, the process enables fast cycle times and high repeatability, reducing long-term production costs. For companies producing high volumes, the return on investment can be significant.
Design Freedom and Customization Opportunities with Large Part Injection Molding
Large part injection molding provides engineers and designers with considerable creative flexibility. Because the process supports the integration of complex geometries and functional features into a single mold, it allows for streamlined part designs that minimize additional assembly or machining. Ribs, bosses, and undercuts can be molded in directly, offering structural enhancements and aesthetic appeal without added cost. Customization is also achievable through tooling modifications, insert molding, and overmolding techniques. This design adaptability is particularly valuable in industries where performance and visual impact must go hand in hand, such as automotive interiors or consumer goods with large-format plastic shells.
Limitations and Challenges of Large Part Injection Molding
Despite its many advantages, large part injection molding is not without challenges. The most prominent limitation is the high initial investment. Tooling and machine costs can be substantial, especially when complex molds or multi-cavity designs are required. Additionally, the process demands significant floor space and specialized equipment, which not all facilities can accommodate. There are also engineering concerns, such as the difficulty of ensuring uniform material flow in large molds, which can lead to warping, sink marks, or incomplete fills. Thick-walled parts pose another issue, as they require longer cooling times and can be prone to internal stress or shrinkage. These technical and financial factors must be carefully evaluated before committing to a project.
When to Choose Large Part Injection Molding Over Alternative Methods
Choosing large part injection molding over other manufacturing methods depends on several criteria. If the project involves high production volumes, complex geometries, and a need for consistent quality, injection molding is likely the superior option. In contrast, processes like thermoforming or CNC machining may be more cost-effective for short runs or simpler parts. Blow molding may be better suited for hollow or tubular products. When evaluating options, considerations should include total lifecycle cost, production speed, mechanical properties of the end product, and the availability of suitable machines and tooling. A thorough cost-benefit analysis helps ensure the most efficient and effective method is selected.
Industry Examples: Real-World Applications of Large Part Injection Molding
Numerous industries rely on large part injection molding to produce durable, functional components. In automotive manufacturing, dashboard panels, bumpers, and under-hood elements are commonly molded using this method for their strength and uniformity. The construction sector uses it to produce large siding panels, electrical enclosures, and water tanks. In the logistics industry, pallets, bins, and containers benefit from the high load-bearing capacity of molded plastic. Consumer product companies use it for appliances, outdoor furniture, and recreational equipment. These real-world examples highlight the versatility of the process and its capacity to meet diverse manufacturing needs across sectors.
Future Outlook: Innovation in Large Part Injection Molding Technology
The future of large part injection molding is being shaped by continuous innovation. Advances in simulation software now allow engineers to model and optimize material flow, reducing the risk of defects before production even begins. Machine manufacturers are developing more energy-efficient and automated systems capable of handling larger molds with greater precision. Sustainable materials and recycled resins are also gaining popularity, helping companies meet environmental targets while maintaining product performance. Smart sensors and IoT integration are improving real-time monitoring and quality control. As these technologies evolve, large part injection molding will continue to offer broader applications, enhanced efficiency, and lower environmental impact.
Striking the Balance Between Scale, Cost, and Complexity
Large part injection molding is a powerful tool for manufacturers looking to produce robust, complex plastic components at scale. Its benefits—design flexibility, high strength, reduced part counts, and production efficiency—make it a go-to solution for many applications. However, its limitations, including high upfront costs and engineering complexities, require careful planning and expertise. By understanding both sides of the equation, manufacturers can make informed decisions that align with their operational goals. As technology advances and demand for large-format plastic parts grows, this process will remain an essential pillar in the future of industrial production.