- April 29, 2025
- Posted by: feinuojixie
- Category: Injection Molding News
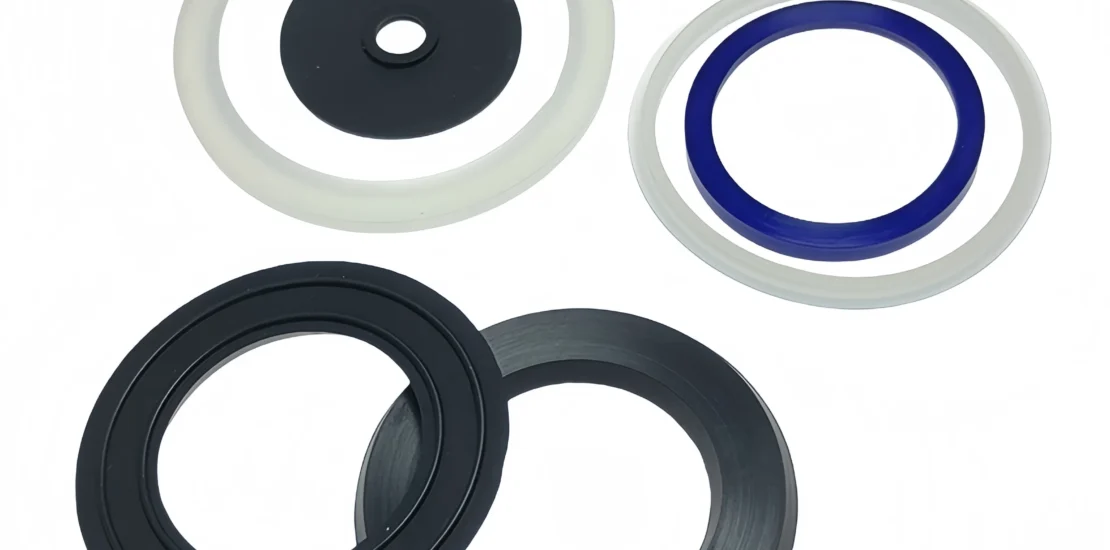
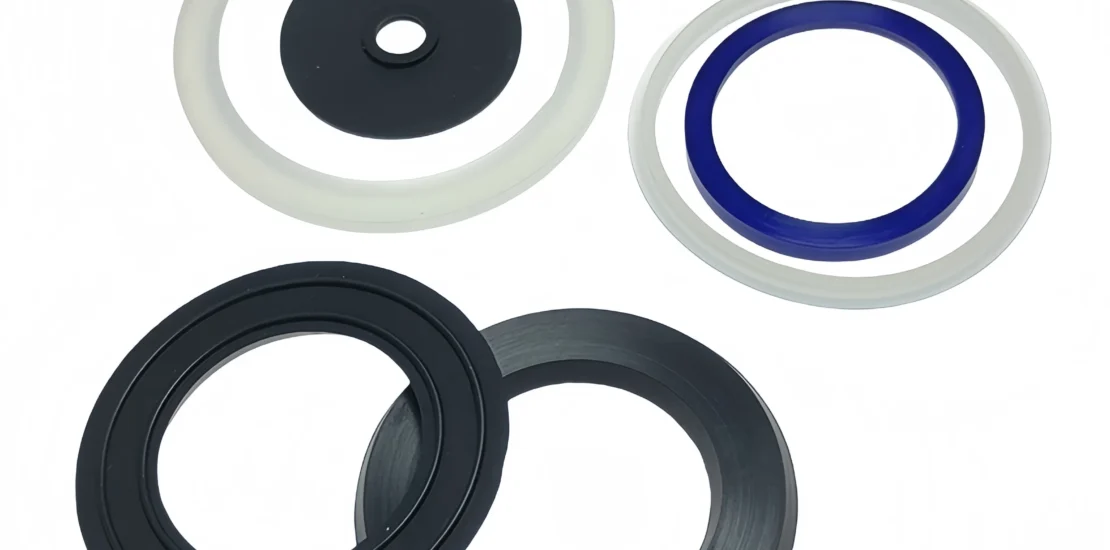
Modern automotive design is more than just sleek lines and aerodynamic curves—it’s a complex intersection of engineering, creativity, and advanced manufacturing. At the heart of this transformation lies a powerful yet often overlooked process: injection molding automotive parts. From the smallest interior trim to intricate engine components, injection molding helps turn imaginative designs into high-performing vehicle parts. It bridges the gap between concept and production, enabling automakers to meet increasing demands for speed, efficiency, and innovation. In this article, we explore how injection molding shapes the automotive industry from the ground up—quite literally.
Designing for Performance: Why Injection Molding Matters
When designing a vehicle, engineers must balance creativity with functionality. Injection molding provides the flexibility needed to create intricate automotive part designs without sacrificing strength or performance. Unlike traditional methods that may require multiple assembly steps or compromise on design detail, injection molding allows for seamless integration of complex shapes and structures in a single, repeatable process. This is especially valuable during early design stages, where rapid iteration and testing are essential. Automotive parts made through injection molding can be quickly prototyped, evaluated, and refined—accelerating development timelines and reducing costly design errors.
From Sketch to Structure: Integrating Injection Molding into the Design Process
The success of injection molding automotive parts depends heavily on early collaboration between design and manufacturing teams. Engineers must consider mold design, part geometry, and material behavior from the very beginning. Features such as draft angles, wall thickness, and rib placement are optimized for moldability while maintaining structural performance. This integration ensures that the final product not only looks good but also performs well under real-world conditions. By embedding manufacturing considerations into the design process, automakers reduce delays and ensure smoother transitions from concept to production.
Material Matters: Choosing the Right Polymer for Automotive Parts
Material selection is critical in determining how an automotive part will perform. Different polymers offer unique benefits, such as heat resistance, impact strength, and flexibility. For example, polyamide (nylon) is commonly used for engine covers due to its high thermal stability, while polypropylene may be chosen for interior trim because of its lightweight and cost-effectiveness. The diversity of materials available for injection molding automotive parts allows designers to tailor each component’s properties to its specific function. In some cases, materials can even be blended or reinforced with fibers to meet demanding performance standards.
Precision in Practice: Tolerances, Complexity, and Consistency
One of the standout features of injection molding is its ability to produce parts with tight tolerances and consistent quality across large volumes. This is particularly important in automotive manufacturing, where each part must fit perfectly with others on the assembly line. Complex features like undercuts, snap fits, and fluid channels can be molded directly into the part without additional machining. By minimizing variability and reducing the need for secondary operations, injection molding ensures that every automotive part meets strict performance and safety requirements.
Cost, Speed, and Scale: Economic Advantages of Injection Molding
Cost-efficiency is a driving factor in the popularity of injection molding within the automotive sector. Once the mold is created, each subsequent part can be produced quickly and at a low marginal cost. This makes injection molding ideal for high-volume production runs. In addition, the process minimizes waste by using just the right amount of material, and leftover plastic can often be recycled for future use. Combined with shorter production cycles and less manual labor, injection molding enables automakers to respond quickly to market demands while controlling costs.
Quality Assurance: Ensuring Safety and Standards
Injection molded automotive parts must meet rigorous quality and safety standards before they can be used in vehicles. Advanced inspection methods, such as coordinate measuring machines (CMMs) and optical scanners, are employed to verify dimensional accuracy. Functional testing ensures that parts can withstand temperature changes, vibrations, and mechanical stress. Furthermore, many manufacturers pursue industry certifications—such as IATF 16949—to demonstrate their commitment to quality management. These quality controls ensure that every injection molded part contributes to the vehicle’s overall reliability and performance.
Innovation on the Assembly Line: Future Trends in Injection Molding
As the automotive industry embraces electric vehicles and sustainable practices, injection molding continues to evolve. One major trend is the adoption of lightweight composite materials that reduce vehicle weight without compromising strength. Biodegradable and bio-based plastics are also gaining traction, helping reduce environmental impact. In addition, smart manufacturing technologies—such as real-time monitoring and AI-driven defect detection—are making injection molding more intelligent and responsive. These innovations promise to further enhance the capabilities and value of injection molding automotive parts in the years ahead.
Driving the Future with Injection Molding Automotive Parts
From initial design sketches to final assembly, injection molding plays a vital role in shaping the modern vehicle. Its unmatched versatility, efficiency, and precision make it an essential process for producing high-quality automotive parts at scale. As consumer expectations continue to rise and the industry pushes toward greener, smarter vehicles, injection molding will remain a cornerstone of automotive innovation. By seamlessly connecting design vision with manufacturing execution, it helps drive the future of mobility—one molded part at a time.