- March 4, 2025
- Posted by: feinuojixie
- Category: Injection Molding News
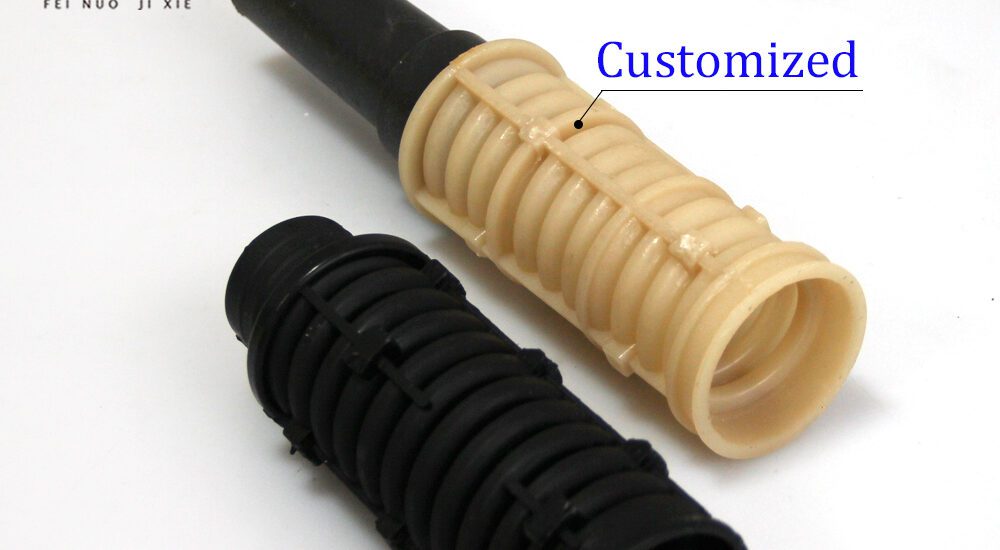
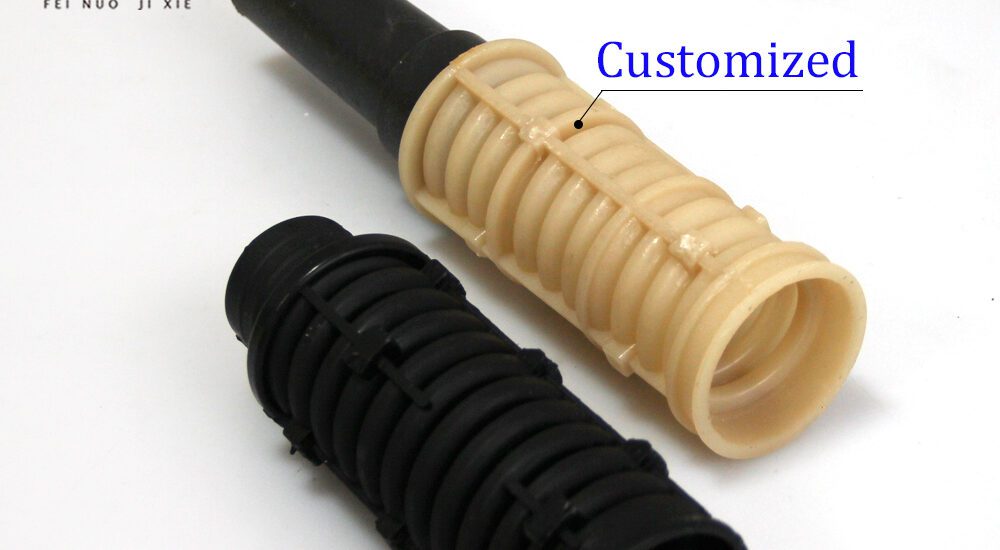
Injection molded part manufacturing is a cornerstone of modern industry, playing a vital role in the production of everyday items across automotive, medical, electronics, and consumer goods sectors. This process enables the mass production of complex, durable, and high-quality plastic components with remarkable efficiency.
From the initial concept to the final product, the journey of an injection molded part involves meticulous planning, material selection, precision engineering, and rigorous quality control. Understanding each stage of this process not only highlights the technological sophistication behind these components but also showcases the endless possibilities of injection molding in shaping the future of manufacturing.
This blog will take you through the entire lifecycle of an injection molded part, exploring its design, production, finishing, and real-world applications. Whether you’re an engineer, manufacturer, or simply curious about how everyday plastic products come to life, this comprehensive guide will offer valuable insights into the fascinating world of injection molding.
Understanding Injection Molded Part Design
The foundation of any high-quality injection molded part lies in its design. A well-optimized design ensures durability, functionality, and cost-effectiveness. Engineers must consider several factors to prevent defects and enhance performance.
Key aspects of injection molded part design include:
- Material selection: Choosing the right plastic impacts strength, flexibility, and heat resistance.
- Wall thickness: Maintaining uniform thickness prevents warping and sink marks.
- Draft angles: Slight tapers allow easy ejection from the mold, reducing stress on the part.
- Undercuts and ribs: These features add strength without excessive material use but require careful mold design.
Computer-Aided Design (CAD) software plays a crucial role in optimizing the initial concept. Engineers use simulations to analyze stress points, material flow, and cooling times before proceeding to manufacturing, minimizing costly design errors.
Material Selection: Choosing the Right Resin
Selecting the right material is a critical decision that affects an injection molded part’s performance, appearance, and longevity. Different plastics offer unique properties suited for various applications.
Common materials used in injection molding include:
- ABS (Acrylonitrile Butadiene Styrene): Impact-resistant and widely used in automotive and electronics.
- Polypropylene (PP): Lightweight and resistant to chemicals, ideal for packaging and medical devices.
- Polycarbonate (PC): Transparent, durable, and heat-resistant, commonly used in eyewear and electronics.
- Nylon: Strong and wear-resistant, often found in mechanical components.
Factors such as flexibility, heat tolerance, and cost influence material selection. Advanced resin blends can enhance properties like UV resistance, flame retardance, and antimicrobial effects, making injection molded parts even more versatile.
The Mold Creation Process: Engineering Precision
Mold creation is the most critical and expensive step in injection molding. A well-designed mold ensures consistency, efficiency, and high-quality output.
The mold-making process involves:
- Designing the mold: Engineers develop precise cavity and core shapes based on the part’s geometry.
- Selecting mold materials: Steel molds offer durability for high-volume production, while aluminum molds are suitable for short runs.
- Manufacturing the mold: CNC machining and Electrical Discharge Machining (EDM) create intricate details and smooth surfaces.
Depending on production needs, molds can be single-cavity (producing one part at a time) or multi-cavity (allowing multiple parts per cycle), improving efficiency.
The Injection Molding Process: Turning Raw Material into Reality
Once the mold is ready, the actual production process begins. Injection molding consists of several key steps:
- Clamping: The two halves of the mold close tightly under high pressure.
- Injection: Heated plastic is injected into the mold cavity at high speed.
- Cooling: The plastic solidifies as it cools, ensuring structural integrity.
- Ejection: The finished part is pushed out of the mold, ready for post-processing.
Controlling parameters such as temperature, pressure, and cycle time is essential to avoid defects like warping, flash, or air bubbles. Automated systems monitor these factors in real-time, ensuring precision and repeatability.
Quality Control and Testing: Ensuring Perfection
To maintain consistency and reliability, rigorous quality control is necessary. Inspection and testing ensure that each injection molded part meets industry standards.
Common quality control measures include:
- Dimensional checks: Using calipers and coordinate measuring machines (CMM) to verify measurements.
- Surface inspection: Detecting defects like sink marks, flow lines, and discoloration.
- Mechanical testing: Assessing impact resistance, tensile strength, and durability.
Advanced technologies like AI-driven vision systems and X-ray analysis help detect hidden defects, further improving quality assurance.
Post-Processing and Finishing Touches
After molding, some parts require additional finishing to enhance their appearance and performance. Post-processing techniques include:
- Trimming and deburring: Removing excess plastic from edges.
- Painting and coating: Adding color, UV protection, or texture.
- Laser engraving: Marking logos or serial numbers for branding and traceability.
These steps refine the final product, making injection molded parts suitable for diverse applications.
Applications of Injection Molded Part in Various Industries
Injection molding is a preferred manufacturing method across multiple industries due to its efficiency and versatility.
- Automotive: Used for dashboards, bumpers, and engine components, reducing weight and improving fuel efficiency.
- Medical: Essential for producing sterile equipment like syringes, prosthetics, and surgical instruments.
- Consumer electronics: Found in smartphone casings, laptop keyboards, and connectors.
- Packaging: Used for lightweight yet durable containers, caps, and bottles.
This widespread adoption highlights the significance of injection molded parts in modern life.
Future Trends in Injection Molded Part Manufacturing
Innovation continues to drive the evolution of injection molding, making production more sustainable and efficient. Emerging trends include:
- Eco-friendly materials: Biodegradable and recycled plastics are reducing environmental impact.
- 3D printing for molds: Accelerating prototyping and enabling complex mold designs.
- Smart factories: Integrating AI, robotics, and IoT to optimize production.
These advancements are shaping the future of injection molding, making it more cost-effective and sustainable.
Conclusion
The journey of an injection molded part, from concept to final product, is a complex yet highly refined process. Every stage—from design and material selection to mold manufacturing, production, and quality control—plays a crucial role in ensuring high performance and durability.
As industries continue to innovate, injection molding remains at the forefront of efficient manufacturing, enabling mass production of reliable and cost-effective plastic components. By leveraging new technologies and sustainable materials, businesses can unlock even greater potential in this ever-evolving field.