- May 3, 2025
- Posted by: feinuojixie
- Category: Injection Molding News
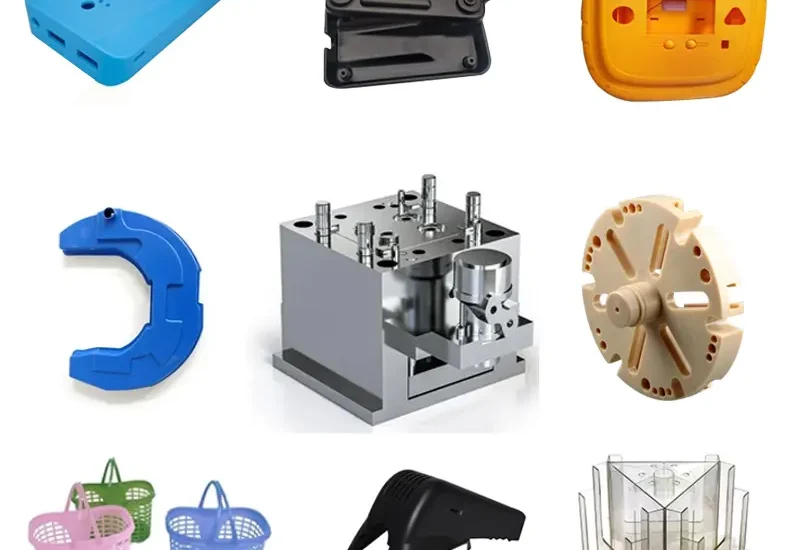
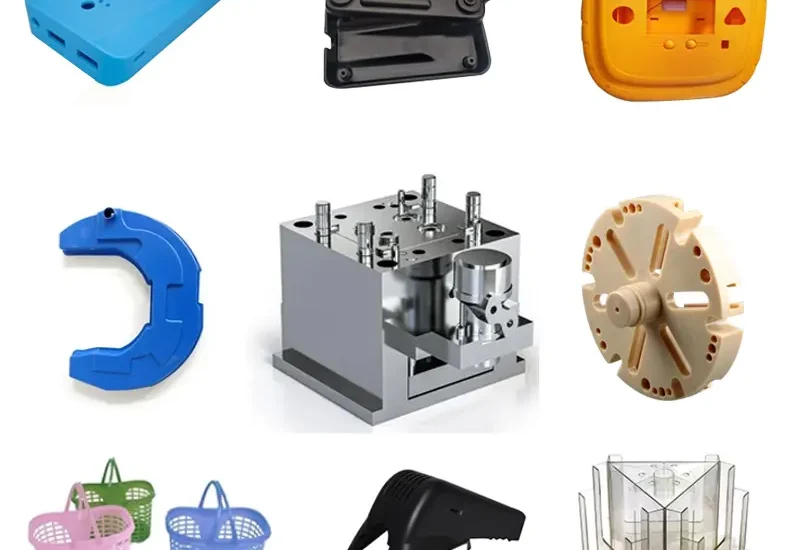
Plastic injection molding is one of the most widely used manufacturing processes in the world today, enabling the production of a wide variety of parts used across different industries. From automotive components to everyday consumer products, plastic injection molded parts play a critical role in our daily lives. The process, which involves injecting molten plastic into a mold to create parts with intricate shapes, has revolutionized the manufacturing industry by offering cost efficiency, speed, and precision.
In this article, we’ll take a deep dive into the fascinating world of plastic injection molding, exploring the entire journey of a plastic part from its conceptualization to its final creation. Whether you’re a manufacturer, engineer, or simply curious about how these parts come to life, this blog will offer a comprehensive understanding of the process and the magic behind plastic injection molded parts.
The Conceptualization Phase: Turning Ideas into Designs
The journey of creating a plastic injection molded part begins long before the plastic ever touches a mold. The conceptualization phase is where product ideas start to take shape. This stage is crucial because it transforms abstract ideas into concrete designs that are ready for production. It involves extensive planning and collaboration between designers, engineers, and stakeholders to ensure the product will function as intended, be manufacturable, and meet all the necessary standards.
At the heart of the conceptualization process is the creation of a design blueprint, which is usually generated using advanced computer-aided design (CAD) software. The design must consider factors like the product’s intended use, the material’s properties, and the complexities of the final shape. Engineers must also account for potential challenges, such as undercuts or thin walls, that may complicate the molding process. Proper planning at this stage can save significant time and cost during later stages of production.
Designing the Perfect Mold: The Foundation of a Quality Part
Once the product design is finalized, the next step in the plastic injection molding process is designing the mold itself. The mold is the core of the injection molding process, and its design directly affects the quality, precision, and overall functionality of the final part. The goal of mold design is to create a cavity that accurately reflects the part’s intended shape while also ensuring that it can be easily filled with molten plastic.
Several factors are taken into account during mold design, including the material choice, the complexity of the part, and the number of cavities required to produce multiple parts in one cycle. The mold needs to be designed with high precision to ensure uniformity and to avoid defects like warping or uneven thickness. Moreover, mold designers must consider the cooling system that will allow the part to solidify evenly, ensuring that it meets the required strength and durability standards.
Materials Matter: Selecting the Right Plastic for Injection Molding
The selection of plastic material is a crucial part of the injection molding process. There are a wide variety of plastics to choose from, each with unique properties that make them suitable for specific applications. Common materials include thermoplastics like polyethylene, polystyrene, and polypropylene, which are widely used due to their versatility, ease of molding, and affordability.
Choosing the right material depends on the desired characteristics of the finished part. For example, if the part needs to be lightweight yet strong, materials like nylon or acetal may be used. If resistance to high temperatures is necessary, materials such as polycarbonate or PEEK might be the best options. The chosen material also impacts factors such as the part’s durability, flexibility, and overall cost.
In addition to performance considerations, sustainability is becoming an increasingly important factor in material selection. Manufacturers are exploring biodegradable plastics and materials made from renewable resources to reduce the environmental footprint of their products. As the demand for eco-friendly solutions grows, the material selection process continues to evolve.
The Injection Molding Process: Turning Concepts into Physical Products
With the mold designed and materials chosen, the next step is the injection molding process itself. This step involves injecting molten plastic into the mold cavity under high pressure, where it cools and solidifies into the final part. The injection molding machine controls critical variables like temperature, pressure, and injection speed to ensure the part takes the correct shape and retains its structural integrity.
The injection molding process begins when plastic pellets are fed into the machine’s hopper. From there, they are heated to a molten state and injected into the mold at high pressure. The plastic fills the mold cavity and takes the shape of the part. Once the plastic cools and solidifies, the mold opens, and the part is ejected.
Factors such as injection speed, mold temperature, and cooling rate all play a significant role in ensuring the plastic flows correctly into the mold, avoiding defects like air pockets or incomplete filling. Precision at this stage is essential for producing parts that meet exact specifications.
Precision and Quality Control: Ensuring Every Part Meets Standards
Achieving precision and maintaining high-quality standards are paramount in the plastic injection molding process. Even slight variations in the mold or material can lead to defects that affect the part’s functionality. This is why rigorous quality control measures are implemented throughout the molding process.
One of the main techniques used for quality control is sampling, where parts are tested for dimensional accuracy and consistency. If any deviations from the design specifications are detected, adjustments are made to the machine settings, mold, or material to correct the issue. In addition, advanced technologies such as in-line inspection systems and computer vision can help identify defects in real-time, ensuring that only parts meeting the required standards are sent for further processing.
Quality control doesn’t stop with the molding process itself. Each part is often subjected to additional testing for properties such as tensile strength, impact resistance, and flexibility to ensure it will perform as expected in its end-use environment.
Post-Processing and Finishing Touches: Enhancing the Final Product
After a plastic part is molded, it often requires post-processing to enhance its appearance and functionality. Post-processing can include a variety of techniques, such as trimming excess plastic, adding colors or coatings, or even assembling multiple molded parts together to form a final product.
Trimming involves removing any excess material left behind from the molding process, known as flash. This is typically done by hand or with automated cutting tools. Parts can also undergo painting, surface texturing, or even metallization to improve their aesthetic appeal or to provide additional functionality, such as corrosion resistance or enhanced grip.
In some cases, plastic injection molded parts are combined with other materials, such as metal inserts or electronic components, during the assembly process. This is common in industries like automotive and electronics, where components need to be integrated into larger systems.
Applications and Benefits of Plastic Injection Molded Parts
Plastic injection molded parts are found in nearly every industry, from automotive and medical to consumer electronics and packaging. Their versatility and ability to be mass-produced quickly and cost-effectively make them ideal for a wide range of applications.
For example, in the automotive industry, injection molded parts are used for everything from dashboards and bumpers to under-the-hood components. In medical devices, precision parts are created for tools and equipment that require high standards of reliability and hygiene. The consumer electronics sector also relies heavily on injection molded parts for housings and internal components.
The benefits of plastic injection molding are clear: it offers high production efficiency, the ability to create complex shapes, and cost-effective manufacturing for both small and large volumes. Additionally, the process allows for a high degree of customization in terms of material choice, color, and finish.
Future Innovations in Plastic Injection Molding
As technology continues to advance, the plastic injection molding industry is evolving rapidly. Automation and robotics are increasingly being integrated into the molding process, allowing for greater precision, speed, and cost savings. These advancements are also contributing to a rise in the use of additive manufacturing techniques, such as 3D printing, to create molds or even some final parts directly.
Sustainability is another area of innovation, with the development of biodegradable plastics and more efficient recycling processes. As consumer demand for environmentally friendly products grows, the injection molding industry is embracing new technologies and materials that reduce waste and energy consumption.
The future of plastic injection molding also lies in the development of smart manufacturing systems, where machines communicate with each other to optimize the production process in real-time. These systems have the potential to dramatically improve efficiency and reduce downtime, making plastic injection molding an even more attractive option for manufacturers worldwide.
The Magic Behind Plastic Injection Molding
Plastic injection molding is a truly magical process that transforms simple plastic pellets into precise, functional parts used in a multitude of applications. From concept to creation, the journey of a plastic injection molded part is one that involves careful planning, expert design, and cutting-edge technology. Through the meticulous design of molds, the selection of appropriate materials, and a precision-driven manufacturing process, the final part emerges as a high-quality product ready to meet the demands of modern industries.
As innovations in technology continue to shape the industry, the potential for plastic injection molded parts is only expanding. With its cost-effectiveness, versatility, and ability to produce complex designs, plastic injection molding will undoubtedly remain a cornerstone of manufacturing for years to come.