- March 14, 2025
- Posted by: feinuojixie
- Category: Injection Molding News
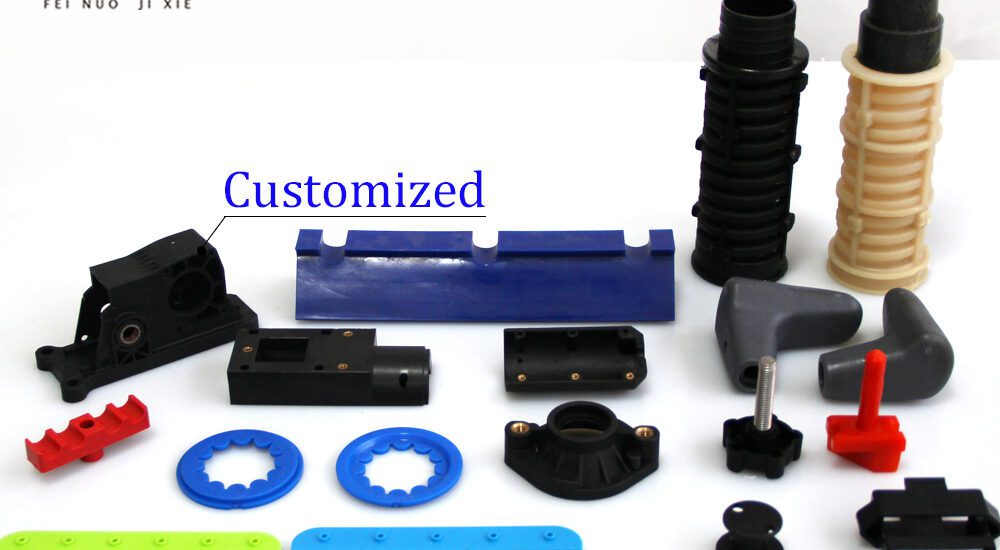
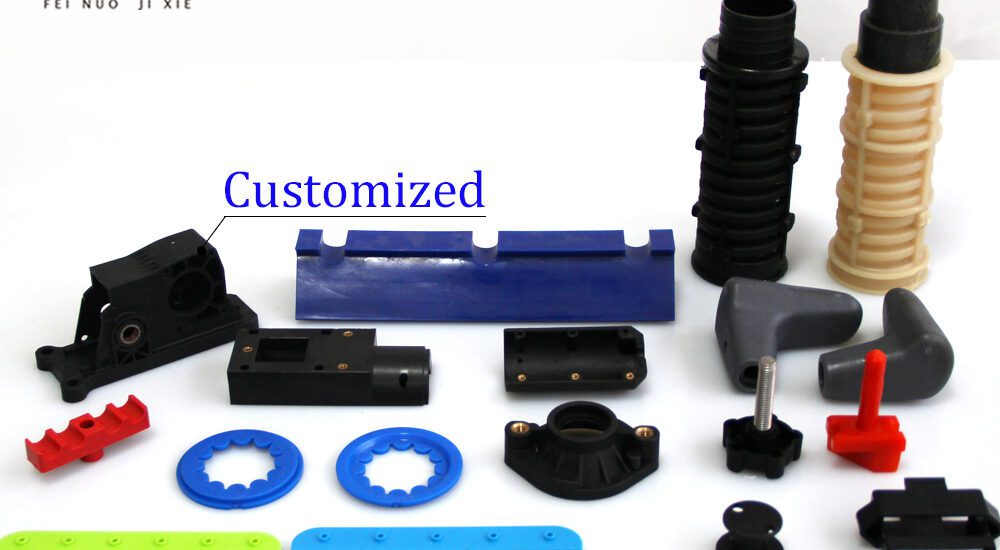
ABS injection moulding is a cornerstone of modern manufacturing, enabling the efficient production of durable, cost-effective, and precisely engineered plastic parts. This process is widely used in industries such as automotive, consumer electronics, and medical devices due to the exceptional properties of ABS. With its high impact resistance, excellent thermal stability, and ease of moulding, ABS has become the go-to material for creating complex and reliable components.
From the initial design phase to full-scale production, ABS injection moulding offers unmatched versatility and efficiency. Engineers and manufacturers rely on this technique to develop innovative products with high precision and repeatability. This article explores the entire journey of ABS injection moulding, from material selection and design optimization to manufacturing best practices and future industry trends.
Understanding ABS Injection Moulding
ABS injection moulding is a highly efficient manufacturing process that transforms raw ABS material into complex, high-performance components. ABS (Acrylonitrile Butadiene Styrene) is a thermoplastic polymer known for its excellent impact resistance, durability, and ease of processing. Compared to other plastics, ABS offers a unique balance of strength, flexibility, and aesthetic appeal, making it an ideal choice for a wide range of applications.
The ABS injection moulding process involves heating the plastic to a molten state, injecting it into a mould cavity under high pressure, and then allowing it to cool and solidify into the desired shape. This method ensures precision, repeatability, and cost efficiency, making it a preferred technique for mass production.
The Design Phase: Creating the Perfect ABS Injection Moulding Product
The success of ABS injection moulding starts with a well-optimized design. Engineers use advanced CAD (Computer-Aided Design) software to create precise 3D models of the moulded parts. These digital designs help manufacturers visualize the final product, identify potential weak points, and make necessary modifications before production begins.
A critical aspect of the design phase is mould flow analysis, which simulates how the molten ABS will fill the mould cavity. This analysis helps predict potential issues such as air traps, weld lines, or incomplete filling, allowing designers to refine the mould for maximum efficiency. Additionally, factors like wall thickness, draft angles, and rib placement must be carefully considered to enhance product strength and minimize defects.
Material Selection: Why ABS Stands Out in Injection Moulding
ABS is preferred for injection moulding due to its exceptional combination of properties:
- Impact Resistance: ABS can withstand sudden shocks and mechanical stress, making it ideal for protective casings and structural components.
- Thermal Stability: The material maintains its integrity over a wide temperature range, ensuring reliability in various environments.
- Surface Finish: ABS produces smooth, glossy surfaces that are easy to paint, texture, or coat for enhanced aesthetics.
- Cost-Effectiveness: Compared to high-performance engineering plastics, ABS offers an excellent balance of quality and affordability.
In some cases, additives such as glass fibers or flame retardants are incorporated into ABS to enhance its properties for specific applications. For example, reinforced ABS is used in automotive parts that require higher strength and rigidity.
The Manufacturing Process: Turning ABS into High-Quality Products
The ABS injection moulding process involves several key steps:
- Material Preparation: ABS pellets are dried to remove moisture, preventing defects like bubbles and voids.
- Melting and Injection: The plastic is heated to a molten state and injected into a precisely machined mould cavity at high pressure.
- Cooling and Solidification: The moulded part is rapidly cooled to ensure dimensional accuracy and strength.
- Ejection and Finishing: Once solidified, the part is ejected from the mould and may undergo secondary processes such as trimming, painting, or assembly.
To achieve high-quality results, manufacturers must carefully control processing parameters, including temperature, injection speed, and cooling time. Even small deviations can impact the final product’s structural integrity and surface finish.
Applications of ABS Injection Moulding Across Industries
ABS injection moulding is widely used across various industries due to its versatility and performance:
- Automotive: ABS is used in dashboards, interior trims, and bumpers due to its impact resistance and lightweight properties.
- Consumer Electronics: Laptop casings, remote controls, and gaming consoles benefit from ABS’s durability and aesthetic appeal.
- Medical Devices: ABS is used for enclosures, housings, and components that require hygiene and precision.
- Toys and Household Products: Many everyday items, from LEGO bricks to kitchen appliances, are manufactured using ABS injection moulding.
These diverse applications highlight the material’s adaptability and widespread acceptance in modern product design.
Advantages of ABS Injection Moulding for Manufacturers
ABS injection moulding offers several benefits that make it a preferred choice for manufacturers:
- High Efficiency: The process allows for rapid production with minimal material waste.
- Cost-Effectiveness: ABS is affordable, and its recyclability reduces overall manufacturing costs.
- Precision and Consistency: Injection moulding ensures uniformity and tight tolerances, ideal for large-scale production.
- Design Flexibility: Complex geometries, fine details, and customized finishes are easily achievable.
These advantages enable businesses to produce high-quality products while maintaining competitive pricing in the market.
Challenges and Solutions in ABS Injection Moulding
Despite its numerous advantages, ABS injection moulding presents some challenges:
- Shrinkage and Warping: Uneven cooling can cause dimensional inconsistencies, which can be mitigated through optimized mould design and temperature control.
- Surface Defects: Issues like sink marks and weld lines can be minimized by adjusting injection pressure and cooling rates.
- Material Degradation: Overheating ABS can lead to discoloration and brittleness, which can be prevented through precise temperature management.
By implementing proper quality control measures and leveraging advanced moulding technologies, manufacturers can overcome these challenges and achieve superior results.
Future Trends in ABS Injection Moulding
The ABS injection moulding industry is continuously evolving with technological advancements:
- Sustainable Materials: Development of bio-based and recycled ABS alternatives to reduce environmental impact.
- Automation and AI: Smart injection moulding machines equipped with AI-driven monitoring systems for improved efficiency and defect detection.
- 3D Printing Integration: Hybrid approaches combining injection moulding with additive manufacturing for rapid prototyping and customization.
These trends are shaping the future of ABS injection moulding, making it more sustainable, efficient, and adaptable to modern manufacturing needs.
Conclusion
ABS injection moulding remains a powerful and indispensable manufacturing process, offering unmatched precision, efficiency, and versatility. From the initial design phase to full-scale production, this technique enables businesses to create durable, high-quality products at competitive costs. With continuous advancements in materials, automation, and sustainability, ABS injection moulding will continue to drive innovation across multiple industries.
Manufacturers looking to leverage the benefits of ABS injection moulding should invest in advanced design techniques, high-quality moulds, and process optimization strategies. By doing so, they can stay ahead of the competition and deliver superior products to the market.