- April 27, 2025
- Posted by: feinuojixie
- Category: Injection Molding News
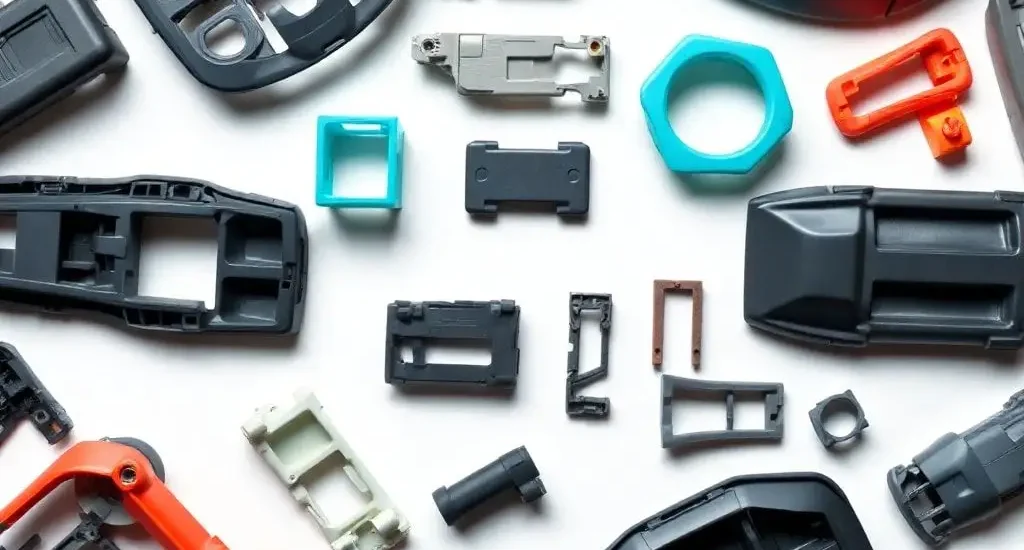
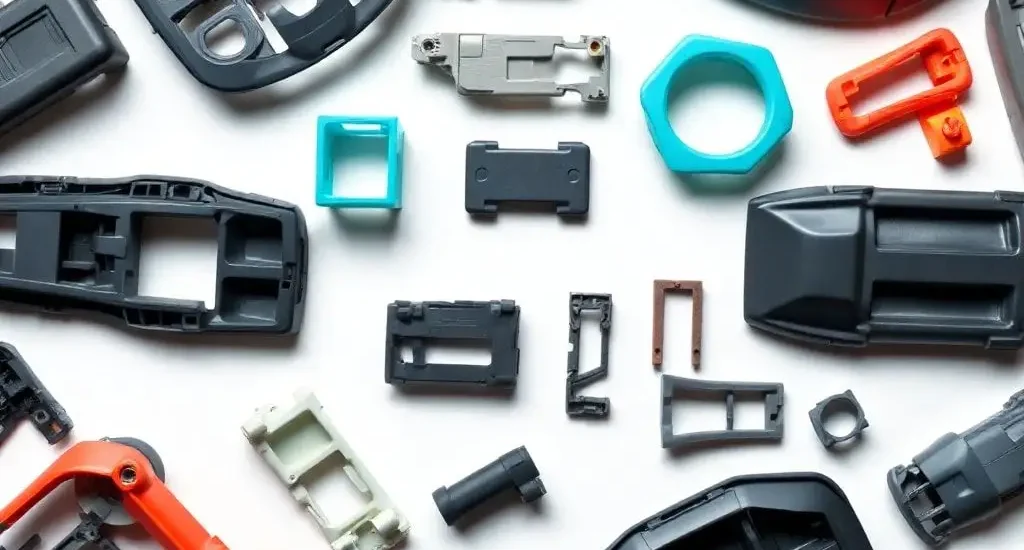
Behind the seamless function of our smartphones, the reliability of life-saving medical devices, and the durability of automotive components lies a silent workforce—precision injection parts. These intricately designed elements are critical to the success of countless products we rely on every day, yet they often go unnoticed. Precision injection parts bridge the gap between conceptual innovation and practical application, ensuring that design visions translate into reliable, high-performing realities. Their hidden power lies not only in their technical sophistication but also in their profound impact across multiple industries, fueling advancements that shape the future. Understanding their journey from mold to market unveils a world of meticulous craftsmanship, cutting-edge technology, and relentless pursuit of perfection.
Understanding the Basics: What Are Precision Injection Parts?
Precision injection parts are meticulously engineered components created through the process of injection molding. In this method, molten material—typically plastic or composite—is injected into a custom mold where it cools and solidifies into a precise shape. What differentiates regular components from precision injection parts is the degree of accuracy achieved, often measured in microns. Precision ensures that each part performs exactly as intended, without margin for error. From the casing of a smartphone to internal medical devices, precision injection parts are the unsung foundation that guarantees functionality, safety, and durability.
From Concept to Creation: The Lifecycle of Precision Injection Parts
The journey of precision injection parts begins with an idea. Engineers and designers collaborate to create detailed blueprints that consider every dimension, tolerance, and material property. Once the design is finalized, the next phase is mold creation, a sophisticated process often involving CNC machining and EDM technology. The mold must be crafted with extreme accuracy because even minor flaws can result in defective parts. After mold fabrication, the injection molding process starts, where material is injected under high pressure into the mold cavity. Quality control measures such as dimensional inspection, mechanical testing, and visual analysis ensure that only the best injection parts move forward into mass production.
Why Precision Matters: The Critical Role of Tolerances in Injection Parts
In the world of precision injection parts, tolerance is everything. Tolerance refers to the acceptable deviation from a part’s specified dimensions. A component slightly too large or too small can cause catastrophic failure, especially in industries like aerospace, healthcare, and automotive where stakes are incredibly high. For instance, in a medical device, a misfit part could compromise patient safety. Tight tolerances ensure interoperability with other components, maintain system integrity, and support optimal performance under demanding conditions. Precision is not just a standard; it is a necessity for ensuring that injection parts meet stringent industry requirements.
Material Matters: Choosing the Right Substances for Injection Parts
Selecting the right material is fundamental to the success of any precision injection parts project. Different applications demand different material properties such as flexibility, thermal resistance, strength, or chemical stability. Common choices include thermoplastics like ABS, polycarbonate, and PEEK, each offering unique advantages. Advanced industries may require high-performance composites or biodegradable materials for sustainable innovation. Material selection impacts not only the durability and performance of the final injection parts but also influences the efficiency of the molding process and the overall project cost. A deep understanding of material science is critical to producing parts that excel in their intended environments.
Innovations Driving the Future of Precision Injection Parts
The world of precision injection parts is constantly evolving, fueled by technological advancements. Micro-molding allows for the production of extremely small parts used in medical implants and miniature electronics. Automation and smart manufacturing technologies enhance consistency and reduce human error, leading to higher quality outcomes. Meanwhile, sustainable practices such as the use of recycled materials and energy-efficient machinery are gaining momentum. Innovations like metal injection molding (MIM) and overmolding expand the possibilities even further, enabling the creation of complex, multi-material parts. As industries demand greater precision and efficiency, the future of injection parts promises to be even more dynamic and transformative.
Real-World Impact: Industries Powered by Precision Injection Parts
Precision injection parts are vital across a multitude of industries. In the automotive sector, they are used for critical components such as connectors, housings, and gears, contributing to vehicle safety and performance. In healthcare, they are indispensable in surgical instruments, diagnostic devices, and drug delivery systems, where absolute reliability is non-negotiable. Consumer electronics depend on them for sleek designs and durable structures, while industrial machinery relies on their strength and endurance. Each application showcases how precision injection parts are not merely components but integral elements that enable technological progress and enhance everyday life.
Challenges and Solutions in the World of Injection Parts
Despite the many advantages, manufacturing precision injection parts comes with challenges. Issues like shrinkage, warping, and surface defects can compromise quality. Advanced simulation software helps predict and mitigate these problems before production begins. Mold maintenance is another critical aspect; worn or damaged molds can produce flawed parts. Regular inspection and refurbishment are essential to maintain high standards. Additionally, achieving ultra-tight tolerances demands continuous monitoring and process adjustments. Leading manufacturers invest heavily in cutting-edge equipment and highly skilled personnel to navigate these challenges, ensuring that every injection part meets exacting specifications.
The Business Advantage: How Precision Injection Parts Speed Up Time to Market
Time to market can determine a product’s success or failure. Precision injection parts help companies accelerate this process by offering consistency, repeatability, and reduced assembly times. Well-designed parts often eliminate the need for secondary operations like machining or fitting, cutting down production timelines significantly. Moreover, fewer defects mean less downtime and lower costs associated with rework or recalls. Companies that leverage high-quality injection parts enjoy a competitive advantage, delivering superior products faster and more efficiently than those relying on less precise manufacturing methods.
The Future is Molded by Precision
Precision injection parts are the silent architects behind modern innovation. Their hidden power lies in their ability to transform ideas into tangible, reliable products across countless industries. As technology continues to advance, the demand for even greater precision, sustainability, and efficiency will drive new breakthroughs in injection molding. Understanding and mastering the complexities of creating precision injection parts is not just about manufacturing excellence—it is about shaping the future itself. From mold to market, the journey of these parts is a testament to human ingenuity, craftsmanship, and the relentless pursuit of perfection.