- April 11, 2025
- Posted by: feinuojixie
- Category: Injection Molding News
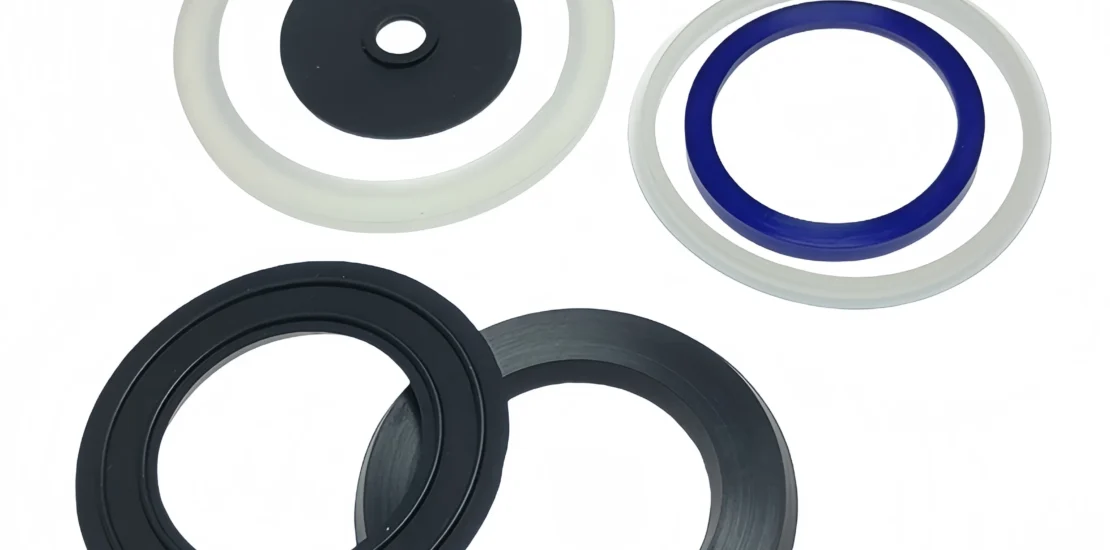
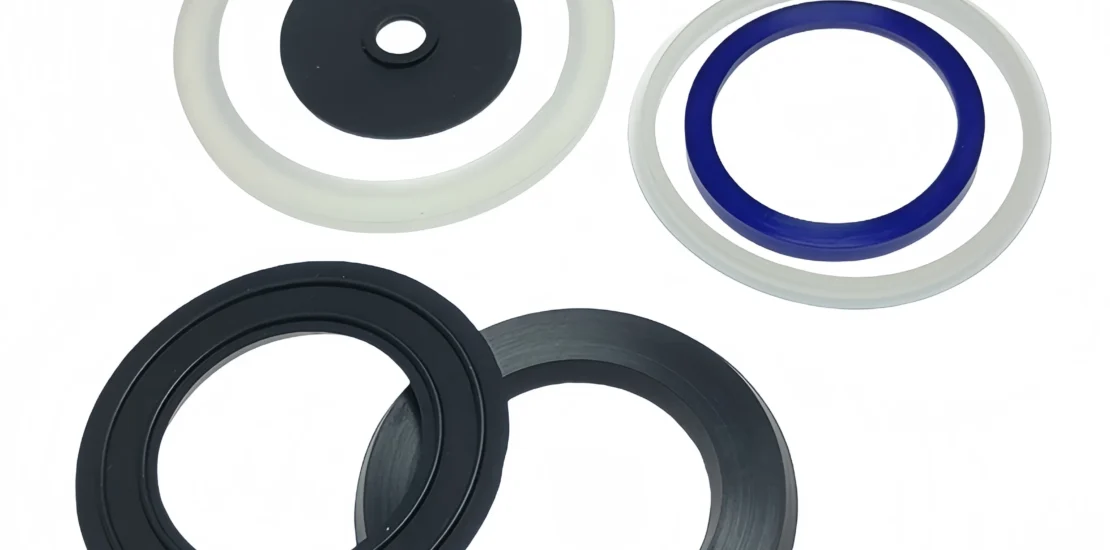
In today’s fast-paced industrial world, staying ahead means more than just keeping up—it means anticipating challenges before they arise. Future-proofing is no longer a buzzword; it’s a necessity for businesses aiming to survive and thrive in competitive markets. With shorter product life cycles, rising customer expectations, and constant technological evolution, manufacturers must adopt solutions that are adaptable, efficient, and resilient.
One such solution lies in the strategic use of plastic injection molding part. These components form the backbone of countless products, from automotive assemblies to precision medical devices. More than just a fabrication method, plastic injection molding is a gateway to scalable production, design agility, and high-performance output. As industries shift toward smarter, more sustainable operations, advanced plastic injection molding part stands out as a proven approach to building a future-ready production line.
The Role of Plastic Injection Molding Part in Industrial Innovation
Plastic injection molding part plays a pivotal role in driving innovation across multiple industries. In automotive manufacturing, it enables the production of lightweight, durable components that enhance fuel efficiency. In medical device fabrication, it supports the creation of precise, sterile tools and components. Electronics manufacturers rely on this process to deliver intricate casings and assemblies with millimeter-level accuracy. The versatility of plastic injection molding part lies in its ability to transform complex design ideas into tangible, high-quality products with repeatable consistency. This makes it an essential tool for innovators pushing the boundaries of performance and efficiency.
Design Flexibility and Material Versatility
One of the most significant advantages of plastic injection molding part is the extraordinary design freedom it offers. Engineers and designers can create complex geometries and fine details that are difficult or impossible to achieve with traditional methods. From undercuts to textured surfaces, the molding process allows for intricate customization without compromising structural integrity. In addition, manufacturers can choose from a vast library of thermoplastic materials—each offering specific properties such as heat resistance, impact strength, or chemical stability. This level of versatility empowers companies to optimize parts for their intended environment and functionality, making the design process both creative and strategic.
Consistency and Quality Control at Scale
For any manufacturer, maintaining consistent quality across thousands or even millions of units is critical. Plastic injection molding part excels in this area by offering exceptional repeatability. Once the mold is perfected, every part produced follows the same specifications with minimal variation. Modern molding systems are equipped with sensors and automation that monitor temperature, pressure, and cycle times in real-time. This data-driven approach enables instant adjustments, minimizing defects and maximizing product reliability. With robust quality control protocols in place, manufacturers can meet rigorous industry standards while keeping customer satisfaction high.
Cost-Efficiency and Long-Term Value
While the initial cost of mold creation can be substantial, the long-term economics of plastic injection molding part are highly favorable. Once the mold is developed, production costs per unit drop significantly, especially at high volumes. The process minimizes material waste, shortens production cycles, and reduces manual labor—all of which contribute to a leaner, more profitable operation. In addition, the durability and low maintenance needs of molded components reduce the need for costly repairs or replacements. Businesses that invest in high-quality plastic injection molding part often see strong returns, both financially and operationally.
Sustainability in Plastic Injection Molding Part
Sustainability is becoming a top priority for manufacturers worldwide. The plastic injection molding process has evolved to support this shift through innovations in eco-friendly materials and efficient resource use. Biodegradable and recycled plastics are increasingly used to reduce environmental impact without sacrificing performance. Many injection molding machines now come with energy-saving technologies and closed-loop systems that reclaim excess material. These improvements make plastic injection molding part a more sustainable option, aligning environmental responsibility with economic goals. Companies adopting green manufacturing practices can also boost their brand image and appeal to eco-conscious consumers.
Integration with Smart Manufacturing and Industry 4.0
Industry 4.0 is reshaping production, and plastic injection molding part is at the forefront of this transformation. Modern molding systems can be integrated into smart factory environments where machines communicate, self-optimize, and predict maintenance needs. Data analytics and machine learning are being used to enhance process efficiency, improve part accuracy, and forecast production issues before they occur. With remote monitoring and cloud-based control systems, manufacturers gain better visibility and agility in operations. By embracing smart manufacturing, plastic injection molding part not only meets current demands but also scales effortlessly into the future.
Future Trends in Plastic Injection Molding Part Technology
The future of plastic injection molding part is shaped by continuous innovation. One emerging trend is micro-molding—producing ultra-small components for fields like microelectronics and biomedical devices. Another is the rise of hybrid tooling, which combines traditional metal molds with 3D-printed inserts to reduce cost and lead times. Material science is also advancing rapidly, introducing high-performance polymers with enhanced durability and functionality. Additionally, intelligent mold design and simulation software allow engineers to optimize part performance before physical production begins. These trends indicate that plastic injection molding part will remain a cornerstone of advanced manufacturing for decades to come.
Choosing the Right Partner for Advanced Plastic Injection Molding Part
To fully leverage the benefits of plastic injection molding part, selecting the right manufacturing partner is essential. A reliable provider will offer not only production capabilities but also engineering support, prototyping services, and post-production finishing. Look for partners with a proven track record, ISO-certified processes, and investment in the latest technology. Collaborative development can lead to better part design, improved performance, and cost savings. Whether you’re scaling a new product or optimizing an existing one, the right partner ensures your project is executed with precision and professionalism.
Investing in Plastic Injection Molding Part for Long-Term Success
In a world where agility, innovation, and efficiency define success, plastic injection molding part stands as a powerful solution for future-proof manufacturing. Its blend of design flexibility, consistent quality, and scalability makes it an invaluable asset for businesses across all sectors. As technology continues to evolve, so too will the capabilities of injection molding—offering even greater opportunities to innovate and lead. By adopting advanced plastic injection molding part today, manufacturers not only meet the challenges of the present but also position themselves for sustainable, long-term growth.