- March 12, 2025
- Posted by: feinuojixie
- Category: Injection Molding News
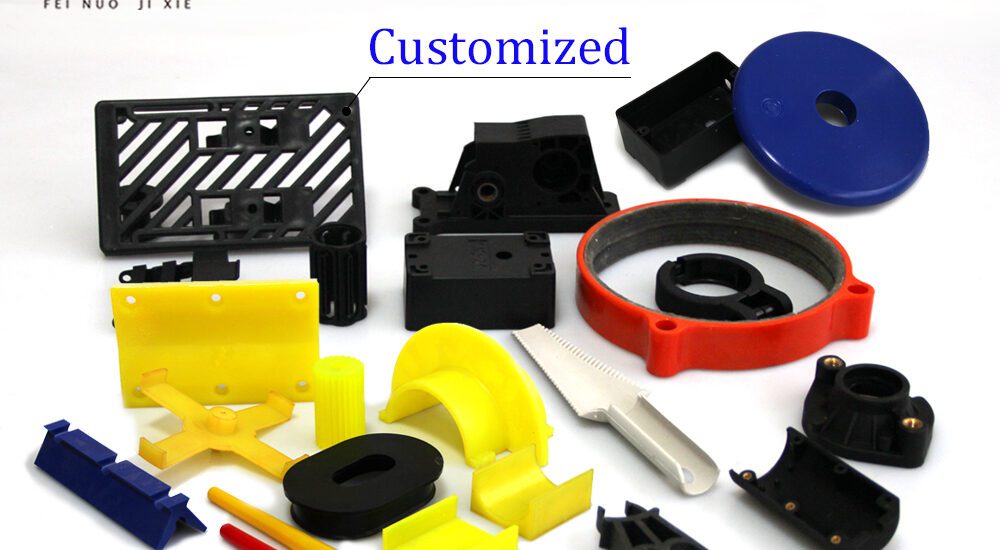
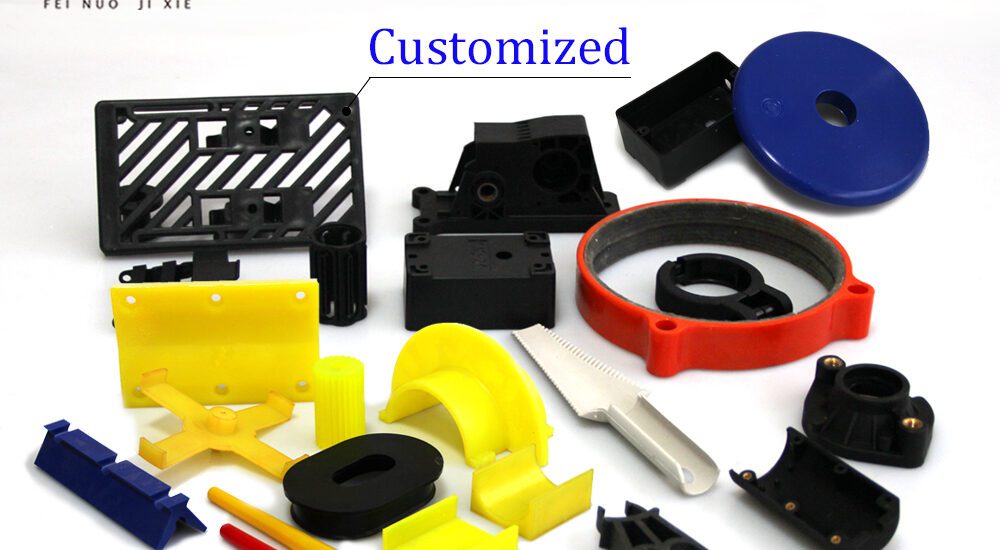
The automotive industry is constantly evolving, with manufacturers seeking innovative materials and techniques to enhance vehicle performance, safety, and efficiency. One of the most groundbreaking advancements in recent years is ABS injection moulding. This method has revolutionized how cars are built by offering a perfect balance of strength, flexibility, and lightweight properties.
Acrylonitrile Butadiene Styrene (ABS) is a high-performance thermoplastic that has become a preferred choice for many automotive applications. From dashboard panels to exterior trims, ABS injection moulding allows for the creation of durable and aesthetically appealing components with remarkable precision. Unlike traditional metal parts, ABS-based components contribute to fuel efficiency and reduce overall production costs, making them an essential part of modern vehicle manufacturing.
In this article, we will explore how ABS injection moulding is transforming the automotive industry. From improving vehicle durability and reducing weight to enhancing design versatility and manufacturing efficiency, this technology is playing a crucial role in shaping the cars of the future.
The Basics of ABS Injection Moulding
What is ABS Injection Moulding?
ABS injection moulding is a manufacturing process that involves heating Acrylonitrile Butadiene Styrene (ABS) resin to a molten state and injecting it into a mould to form precise automotive components. This method allows for mass production of complex parts with high accuracy, making it a cost-effective and reliable solution for car manufacturers. ABS is known for its impact resistance, heat stability, and ease of customization, making it a preferred material for various applications in vehicle production.
Why ABS is Preferred in Automotive Manufacturing
ABS injection moulding has become a staple in the automotive sector due to the unique properties of ABS plastic. Unlike metals, ABS offers flexibility, making it resistant to cracks under stress. Additionally, it is lightweight, which contributes to improved fuel efficiency. Its smooth surface finish allows for easy painting, plating, and texturing, enabling manufacturers to produce both functional and visually appealing car parts.
Enhancing Vehicle Durability with ABS Injection Moulding
High Impact Resistance for Safety and Longevity
One of the primary reasons ABS injection moulding is widely used in the automotive industry is its excellent impact resistance. Components made from ABS can absorb shocks and withstand heavy stress, making them ideal for safety-critical parts such as bumpers, fenders, and interior panels. This durability enhances the lifespan of vehicles while providing passengers with better protection in the event of a collision.
Weather and Chemical Resistance for Extended Lifespan
ABS components are designed to endure harsh environmental conditions, including extreme temperatures, UV exposure, and chemical exposure from oils and cleaning agents. Unlike some materials that degrade over time, ABS maintains its structural integrity, ensuring long-lasting performance. This makes it ideal for exterior parts such as mirror housings, grilles, and trims, which must withstand constant exposure to the elements.
Reducing Vehicle Weight with ABS Injection Moulding
Lighter Components for Better Fuel Efficiency
A significant advantage of ABS injection moulding is its ability to reduce vehicle weight. Compared to traditional metal components, ABS parts are significantly lighter, helping automakers produce more fuel-efficient vehicles. By reducing the overall weight of a car, ABS components contribute to lower fuel consumption, making them an essential material in modern automotive engineering.
The Role of ABS in Electric Vehicle Innovation
As the demand for electric vehicles (EVs) grows, automakers are continuously seeking ways to enhance battery efficiency and performance. One of the key strategies is weight reduction. ABS injection moulding plays a crucial role in EV development by providing lightweight yet durable components. By replacing heavier materials with ABS, manufacturers can extend the driving range of electric cars while maintaining structural integrity and passenger safety.
Cost-Effectiveness and Efficiency in Manufacturing
Lower Production Costs with ABS Injection Moulding
ABS injection moulding is a cost-efficient manufacturing process that allows for large-scale production without compromising quality. The ability to produce multiple identical parts quickly reduces manufacturing costs and increases efficiency. This makes ABS an attractive choice for automakers looking to balance quality with affordability.
Rapid Production Cycles and Minimal Waste
The injection moulding process enables manufacturers to produce complex components with minimal material waste. Unlike traditional machining, which often results in excess material loss, ABS injection moulding ensures optimal material usage. Additionally, ABS is recyclable, allowing for sustainable manufacturing practices that align with the industry’s push toward eco-friendly production.
Aesthetic and Functional Advantages in Automotive Design
Versatile Finishing Options for Premium Appeal
One of the standout features of ABS injection moulding is its ability to accommodate various finishing techniques. ABS can be painted, plated with chrome, or textured to achieve a high-end appearance. This versatility allows automakers to enhance the visual appeal of vehicles without the need for additional materials. For example, ABS is commonly used in dashboards, door panels, and decorative trims to create a sophisticated interior design.
Ergonomic and Comfortable Interiors with ABS Components
Beyond aesthetics, ABS injection moulding enhances comfort and functionality in vehicle interiors. The material’s smooth texture and flexibility make it ideal for producing soft-touch panels, armrests, and control buttons. Additionally, ABS is used to manufacture steering wheel covers and gear shift knobs, ensuring a comfortable grip and improved user experience.
The Future of ABS Injection Moulding in the Automotive Industry
Advancements in Sustainable ABS Materials
As the automotive industry shifts toward sustainability, researchers are developing eco-friendly ABS variants. These include bio-based ABS and recycled ABS, which help reduce the carbon footprint of vehicle production. With growing environmental regulations, automakers are increasingly adopting sustainable materials, making ABS injection moulding an even more attractive choice for the future.
Integration with Smart Car Technologies
With the rise of smart vehicles and autonomous driving, ABS injection moulding is evolving to meet new technological demands. The material’s ability to integrate with electronic components makes it ideal for housing sensors, touchscreens, and control modules. As cars become more connected and technologically advanced, ABS will play a crucial role in supporting next-generation vehicle innovations.
The Lasting Impact of ABS Injection Moulding on Automotive Manufacturing
ABS injection moulding has transformed the automotive industry by offering a perfect combination of durability, lightweight properties, cost-effectiveness, and design flexibility. Its ability to enhance vehicle performance, improve fuel efficiency, and support advanced automotive technologies makes it a cornerstone of modern car manufacturing.
As the industry continues to innovate, ABS injection moulding will play an even greater role in shaping the future of automotive design and production. With ongoing advancements in sustainable materials and smart vehicle integration, this technology will remain at the forefront of automotive engineering, driving the industry toward a more efficient and eco-friendly future.