- March 13, 2025
- Posted by: feinuojixie
- Category: Injection Molding News
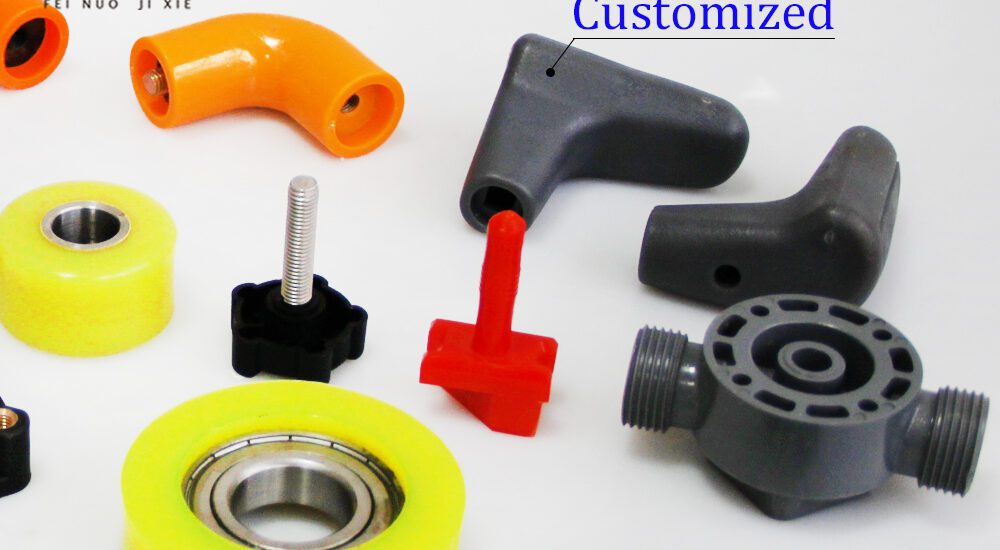
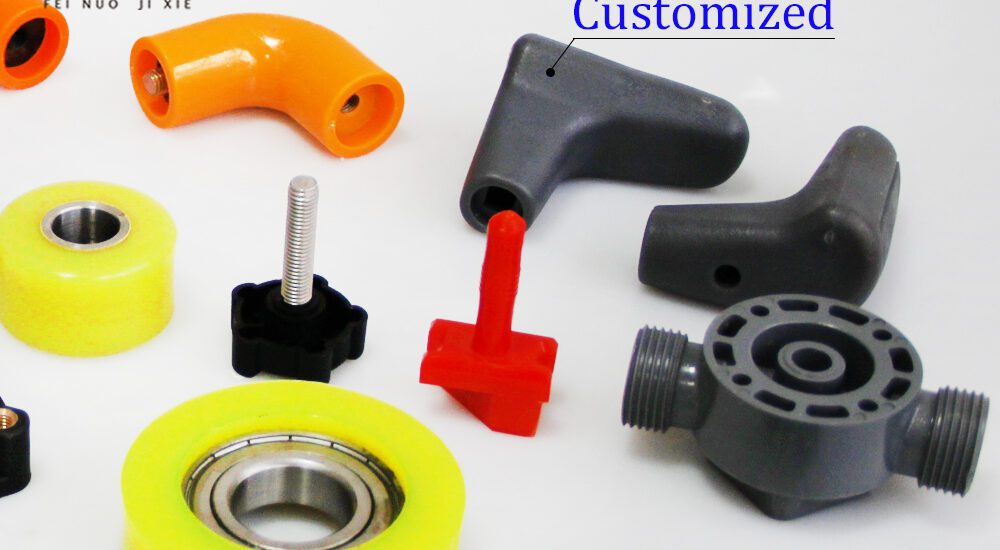
ABS injection moulding is a widely used manufacturing process that plays a crucial role in producing high-quality plastic components with precision and efficiency. This technique is essential in industries such as automotive, electronics, and consumer goods, where durable and lightweight materials are in high demand.
The process of ABS injection moulding significantly streamlines production by enabling rapid manufacturing, reducing material waste, and ensuring consistent product quality. By utilizing automated systems and advanced mould designs, manufacturers can produce complex components with minimal effort and maximum efficiency.
This article explores how ABS injection moulding optimizes the manufacturing process, reduces costs, and provides sustainable solutions for various industries. From understanding its core principles to examining its applications and future trends, we will uncover why this technique remains a top choice in modern manufacturing.
Understanding ABS Injection Moulding
ABS injection moulding is a manufacturing process that utilizes Acrylonitrile Butadiene Styrene (ABS), a thermoplastic polymer known for its strength, impact resistance, and flexibility. This process involves injecting molten ABS material into a mould cavity, allowing it to cool and solidify into the desired shape.
ABS is a preferred material in injection moulding due to its excellent balance of toughness, heat resistance, and cost-effectiveness. It can be easily shaped into complex designs while maintaining high durability. The basic steps in ABS injection moulding include material preparation, melting, injection into the mould, cooling, and ejection. Each of these steps plays a vital role in ensuring efficiency and precision in production.
How ABS Injection Moulding Improves Efficiency
One of the primary reasons manufacturers opt for ABS injection moulding is its ability to streamline production and enhance efficiency.
- Fast Production Cycles – ABS injection moulding allows for rapid cycle times, significantly reducing manufacturing lead times. The process is highly automated, enabling quick and continuous production.
- Precision and Consistency – Modern moulding machines ensure accurate replication of designs, minimizing defects and improving product quality. This reduces the need for additional finishing work.
- Material Waste Reduction – Advanced mould designs optimize material usage, leading to minimal scrap and lower production costs. Any excess ABS can often be recycled and reused in subsequent moulding cycles.
By optimizing these factors, ABS injection moulding enhances overall productivity, making it an ideal choice for high-volume manufacturing.
Cost-Effectiveness of ABS Injection Moulding
ABS injection moulding is not only efficient but also highly cost-effective. Several factors contribute to its affordability:
- Lower Material Costs – Compared to alternative plastics, ABS is relatively inexpensive while still offering superior mechanical properties.
- High Production Efficiency – The ability to produce large quantities of parts in a short time reduces labor and operational costs.
- Long-Lasting Moulds – ABS-compatible moulds are designed for durability, allowing repeated use without frequent replacements. This minimizes tooling costs over time.
For businesses looking to maximize output while minimizing expenses, ABS injection moulding presents a practical and profitable solution.
Applications of ABS Injection Moulding in Different Industries
Due to its versatility, ABS injection moulding is widely used across multiple industries:
- Automotive Industry – ABS is commonly used for dashboards, interior trims, bumpers, and structural components, offering a balance of strength and lightweight properties.
- Electronics Industry – The durability and electrical insulation properties of ABS make it ideal for casings, connectors, and other electronic components.
- Consumer Goods – Household products, toys, and kitchen appliances are often made using ABS injection moulding due to its impact resistance and aesthetic appeal.
The adaptability of ABS in different sectors highlights its importance in modern manufacturing.
Environmental Benefits of ABS Injection Moulding
Sustainability is a growing concern in the manufacturing industry, and ABS injection moulding contributes to eco-friendly production in several ways:
- Reduced Material Waste – The precise moulding process ensures minimal excess material, reducing plastic waste.
- Recyclability – ABS can be reprocessed and reused, promoting a circular economy and reducing environmental impact.
- Development of Eco-Friendly ABS – Manufacturers are investing in biodegradable and bio-based ABS alternatives to enhance sustainability.
These environmental benefits make ABS injection moulding a responsible choice for businesses aiming to reduce their carbon footprint.
Challenges and Solutions in ABS Injection Moulding
Despite its advantages, ABS injection moulding comes with certain challenges:
- Warping and Shrinkage – Temperature fluctuations can cause dimensional inconsistencies in moulded parts. Solution: Maintaining optimal moulding conditions and using uniform cooling systems can minimize these defects.
- Surface Defects – Issues such as sink marks and flow lines may occur. Solution: Adjusting injection speed, pressure, and mould temperature can help achieve a smooth finish.
- Quality Control – Ensuring consistent product quality can be challenging. Solution: Implementing rigorous inspection and testing procedures ensures defect-free manufacturing.
By addressing these challenges, manufacturers can achieve high-quality results with ABS injection moulding.
Future Trends in ABS Injection Moulding
As technology advances, ABS injection moulding continues to evolve:
- Smart Moulding Technologies – The integration of sensors and automation enhances precision and real-time quality monitoring.
- Sustainable Innovations – The development of biodegradable ABS and energy-efficient moulding processes is shaping the future of environmentally friendly manufacturing.
- Industry 4.0 Integration – AI-driven moulding systems and data analytics are improving efficiency and reducing production downtime.
These trends indicate that ABS injection moulding will remain a key player in modern manufacturing, adapting to new challenges and innovations.
Conclusion
ABS injection moulding is a highly efficient and cost-effective manufacturing method that streamlines production across various industries. Its ability to produce high-quality, durable, and precision-engineered components makes it an ideal choice for businesses seeking to optimize manufacturing processes.
With its benefits in efficiency, cost reduction, and sustainability, ABS injection moulding is set to play a crucial role in the future of plastic manufacturing. As innovations continue to enhance its capabilities, businesses can leverage this technology to stay ahead in a competitive market.