- March 25, 2025
- Posted by: feinuojixie
- Category: Injection Molding News
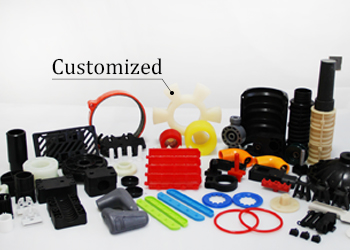
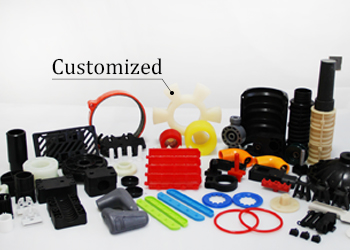
In the world of modern manufacturing, turning an idea into a functional product requires precision, efficiency, and the right materials. ABS injection moulding is a powerful technology that enables designers and manufacturers to bring their creative visions to life with remarkable accuracy and durability. Whether it’s automotive parts, consumer electronics, or household appliances, ABS injection moulding plays a crucial role in producing high-quality, cost-effective components.
This process combines the versatility of Acrylonitrile Butadiene Styrene (ABS) with the efficiency of injection moulding, offering manufacturers a reliable way to produce complex shapes with minimal waste. By heating and injecting molten ABS into moulds, manufacturers can mass-produce items with exceptional detail, strength, and consistency.
As industries continue to demand innovative solutions, ABS injection moulding remains at the forefront of product development, helping businesses transform ideas into reality with speed and precision. In this article, we will explore the fundamentals of ABS injection moulding, its benefits, applications, and the latest advancements shaping the future of this transformative technology.
Understanding ABS Injection Moulding
What Is ABS Injection Moulding?
ABS injection moulding is a manufacturing process that utilizes Acrylonitrile Butadiene Styrene (ABS) to create durable and high-precision plastic components. ABS is a thermoplastic polymer known for its excellent impact resistance, heat stability, and flexibility, making it ideal for various applications. The injection moulding process involves melting ABS pellets and injecting the liquid plastic into a mould to form complex and detailed shapes.
This method is widely used across industries due to its ability to produce high-quality products with consistent results. From automotive interiors to consumer electronics, ABS injection moulding ensures that manufacturers can meet the demands of modern product design while maintaining cost efficiency.
The Science Behind ABS Injection Moulding
ABS injection moulding follows a step-by-step process to transform raw material into finished products:
-
Material Preparation: ABS plastic granules are fed into the injection moulding machine and heated until they reach a molten state.
-
Mould Design: A precisely engineered mould is created to shape the molten ABS into the desired form.
-
Injection Process: The molten ABS is injected into the mould cavity under high pressure to ensure every detail is captured.
-
Cooling and Solidification: Once injected, the material cools and hardens into its final shape.
-
Ejection and Finishing: The finished component is ejected from the mould and undergoes post-processing for quality assurance.
This efficient process allows for mass production of intricate and durable plastic parts with minimal waste, making ABS injection moulding a preferred choice in manufacturing.
Key Benefits of ABS Injection Moulding
Durability and Strength
ABS injection moulding produces components that are highly resistant to impact, scratches, and wear. This makes ABS ideal for applications that require toughness and longevity, such as automotive parts, protective casings, and industrial tools. The combination of Acrylonitrile for chemical resistance, Butadiene for toughness, and Styrene for rigidity results in a material that can withstand daily use without compromising performance.
High Precision and Detail
One of the main advantages of ABS injection moulding is its ability to produce complex shapes with extreme accuracy. The moulding process allows for fine details, tight tolerances, and intricate designs, making it ideal for components that require exact specifications, such as medical devices and consumer electronics. The precision of this method ensures that every piece is identical, reducing errors and inconsistencies in mass production.
Cost-Effectiveness and Mass Production
ABS injection moulding is a highly efficient process that minimizes material waste and labor costs. Once a mould is created, manufacturers can produce thousands or even millions of identical components at a low cost per unit. This makes it a cost-effective solution for large-scale production, allowing businesses to maximize their profitability without sacrificing quality.
Versatility in Applications
ABS injection moulding is used across various industries due to its adaptability and reliability. Some of the key sectors benefiting from this technology include:
-
Automotive: Used for dashboards, interior trim, and protective covers.
-
Electronics: Essential for smartphone cases, remote controls, and computer housings.
-
Healthcare: Utilized in medical device enclosures and laboratory equipment.
-
Household Goods: Common in kitchen appliances, furniture, and toy manufacturing.
The versatility of ABS injection moulding makes it a go-to solution for manufacturers looking to create durable and visually appealing products.
The Role of ABS Injection Moulding in Product Development
From Concept to Prototype
One of the greatest advantages of ABS injection moulding is its ability to facilitate rapid prototyping. Engineers and designers can create functional prototypes quickly, allowing them to test and refine their designs before committing to full-scale production. This process significantly reduces development time and ensures that the final product meets performance and quality standards.
Scalability and Manufacturing Efficiency
Once a prototype is finalized, ABS injection moulding makes it easy to scale up production to meet market demands. The process is designed for high-volume manufacturing, ensuring that businesses can produce large quantities of their products without compromising on quality. This scalability is crucial for industries that require consistent and reliable production output.
Innovations in ABS Injection Moulding
Advanced Moulding Techniques
Recent advancements in ABS injection moulding have introduced new techniques that enhance product design and functionality. Some of these innovations include:
-
Gas-Assisted Injection Moulding: Improves material distribution and reduces product weight while maintaining strength.
-
Multi-Shot Moulding: Enables the combination of different materials or colors in a single product, expanding design possibilities.
-
Micro Moulding: Allows for the production of extremely small and precise components for medical and electronic applications.
These advancements continue to push the boundaries of what is possible with ABS injection moulding, making it a valuable technology for modern manufacturing.
Sustainable Practices in ABS Injection Moulding
As environmental concerns grow, manufacturers are adopting sustainable practices in ABS injection moulding to reduce their carbon footprint. Some eco-friendly initiatives include:
-
Recycling ABS Waste: Collecting and reusing scrap ABS materials to minimize plastic waste.
-
Energy-Efficient Machines: Utilizing modern injection moulding machines that consume less energy while maintaining high production efficiency.
-
Biodegradable Alternatives: Exploring new formulations that enhance the recyclability of ABS products.
By integrating sustainability into ABS injection moulding, manufacturers can reduce waste, conserve resources, and contribute to a greener future.
Conclusion
ABS injection moulding is a transformative technology that turns ideas into reality with precision, efficiency, and durability. Its ability to produce high-quality components at scale makes it an essential process for industries ranging from automotive and electronics to healthcare and consumer goods.
With continuous advancements in moulding techniques and sustainable practices, ABS injection moulding remains at the forefront of modern manufacturing. Businesses looking to innovate and streamline production can leverage this technology to bring their concepts to life while maintaining cost efficiency and environmental responsibility.
By understanding the benefits and potential of ABS injection moulding, companies can unlock new opportunities for product development, ensuring long-term success in an ever-evolving market.