- April 25, 2025
- Posted by: feinuojixie
- Category: Injection Molding News
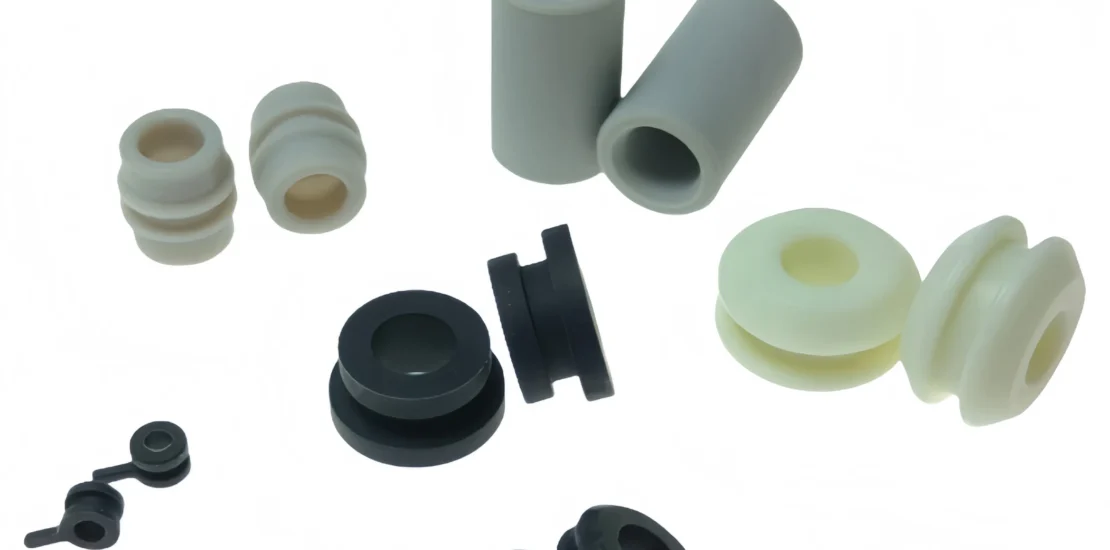
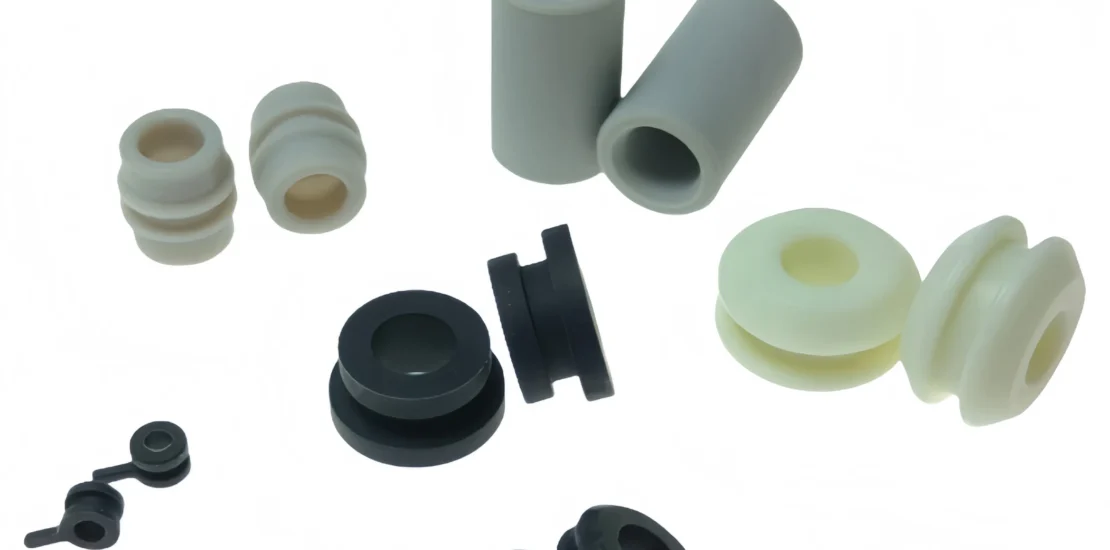
In today’s fast-paced manufacturing environment, the smallest components can have the biggest impact. Among these, injection parts stand out as essential elements that influence everything from speed to precision on the production line. Often overlooked, these parts form the backbone of countless processes across industries—from automotive to medical devices. As demand for higher quality and tighter tolerances increases, the importance of using high-quality injection parts has never been more critical. When selected and applied properly, they don’t just perform a task—they drive transformation.
Precision in Every Mold: The Foundation of Efficiency
High-quality injection parts bring an unmatched level of precision to manufacturing. Every detail of an injection mold—from cavity design to surface finish—affects the final product. When parts are manufactured with consistent dimensions and tight tolerances, they reduce the chances of defects and eliminate unnecessary rework. This level of accuracy translates directly into faster cycle times and a more predictable production flow. Over time, these incremental efficiencies can lead to significant operational improvements.
Reducing Downtime with Durable Injection Parts
Durability is a hidden strength of well-made injection parts. Inferior components are prone to wear, cracking, or deformation under pressure, which leads to unscheduled downtime and rising maintenance costs. High-quality injection parts, on the other hand, are typically built from superior materials such as hardened steel or advanced polymers, ensuring longer service life and better performance under stress. By minimizing breakdowns and maintenance interruptions, durable parts keep your production line moving without costly pauses.
Streamlining Workflow Through Better Compatibility
Compatibility is critical when injection parts are expected to integrate with complex machinery and systems. Poorly designed parts can cause misalignments, slow down operations, or even damage equipment. High-quality injection parts are engineered for seamless fit and function. Whether they’re used in automated assembly lines or specialized tooling setups, these parts enhance workflow continuity by eliminating bottlenecks and reducing the need for constant adjustment. The result is a smoother, more synchronized production environment.
Elevating Product Quality from the Inside Out
The quality of your final product often reflects the quality of the parts behind it. When high-quality injection parts are used, the end result is more refined, structurally sound, and visually consistent. This is especially important in industries such as electronics, healthcare, and consumer goods, where both performance and appearance matter. Precision components contribute to uniformity in shape, strength, and finish—factors that elevate brand perception and reduce customer complaints.
Cost Efficiency Beyond the Surface
At first glance, investing in high-quality injection parts may seem like a higher upfront cost. However, the long-term savings are substantial. These parts reduce material waste, prevent frequent stoppages, and lower the likelihood of defective products reaching the market. Furthermore, consistent part quality simplifies inventory management and reduces the time needed for quality checks. When you calculate the total cost of ownership, premium injection parts often outperform their cheaper counterparts by a wide margin.
Meeting Industry Standards with Confidence
Many industries operate under strict regulatory and performance standards. Whether it’s ISO certifications, FDA approvals, or automotive safety regulations, high-quality injection parts can help ensure compliance. Reputable manufacturers understand these requirements and produce parts that meet or exceed industry benchmarks. Using such parts not only ensures regulatory alignment but also enhances trust with clients and partners. It signals that your production line is built on reliability and professionalism.
Sustainability Benefits of Quality Injection Parts
Sustainability is no longer optional—it’s a competitive advantage. High-quality injection parts contribute to greener operations in multiple ways. Their extended lifespan reduces the frequency of replacements and the waste associated with worn-out parts. Better performance means lower energy consumption during production. And by decreasing the rate of defective goods, manufacturers can reduce the amount of scrap material. Altogether, this supports a more environmentally responsible approach to manufacturing.
Choosing the Right Partner for Injection Parts
Not all suppliers offer the same level of expertise or commitment to quality. Selecting the right partner for your injection parts is crucial. Look for manufacturers with a strong track record, transparent quality control processes, and the ability to offer customized solutions. Ask about material certifications, testing procedures, and post-sale support. A reliable partner doesn’t just deliver parts—they provide peace of mind, helping you maintain consistency and excellence across your entire operation.
The Hidden Power of High-Quality Injection Parts
High-quality injection parts might be small in size, but their influence is immense. From improving production speed and product integrity to reducing costs and supporting sustainability, these components serve as the quiet catalysts behind successful manufacturing lines. By investing in better injection parts, businesses gain more than just performance—they unlock the potential to innovate, grow, and lead in a competitive market. In the end, it’s not just about making things—it’s about making things better.