- March 3, 2025
- Posted by: feinuojixie
- Category: Injection Molding News
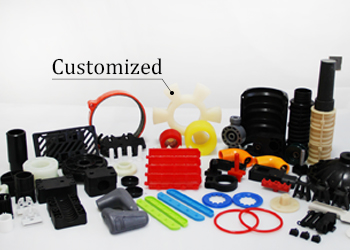
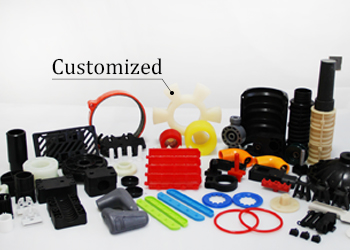
Injection molded parts have become an integral part of modern manufacturing, playing a crucial role in shaping product design and enhancing performance across industries. This manufacturing process allows for high precision, consistency, and scalability, making it an ideal choice for producing complex components. As industries strive for efficiency and innovation, injection molded parts continue to redefine what is possible in product development.
The Evolution of Injection Molded Parts in Manufacturing
Injection molding has a long history that dates back to the late 19th century. Initially developed for simple plastic products, the process has undergone significant advancements, allowing for the mass production of highly complex components. Early injection molding machines were limited in capability, but modern technologies have introduced high-speed production, multi-material molding, and enhanced precision. Innovations such as computer-aided design (CAD) and automated quality control have further refined the process, making injection molded parts indispensable in various industries.
Why Injection Molded Parts Are Essential for Modern Product Design
Injection molded parts are vital in product design due to their unmatched precision and repeatability. Unlike traditional manufacturing methods, which may lead to inconsistencies, injection molding ensures that every part meets exact specifications. This precision is particularly valuable in industries like medical devices and electronics, where small deviations can affect functionality. Additionally, injection molded parts enable designers to create intricate geometries that would be difficult or impossible to achieve using other methods. This flexibility opens up new possibilities in product innovation and aesthetics.
Material Selection and Its Impact on Injection Molded Parts
The choice of material plays a crucial role in determining the performance of injection molded parts. Manufacturers have access to a wide range of materials, including thermoplastics, thermosetting polymers, and elastomers, each offering unique properties. For example, polycarbonate is favored for its strength and impact resistance, while polypropylene is valued for its lightweight and chemical resistance. Material selection influences factors such as durability, flexibility, and heat tolerance, allowing manufacturers to tailor injection molded parts for specific applications. Advances in material science continue to expand the possibilities, introducing eco-friendly and high-performance options.
How Injection Molded Parts Enhance Product Performance
Injection molded parts offer numerous performance advantages that contribute to product reliability and longevity. Their superior mechanical properties, such as high strength-to-weight ratio and resistance to wear, make them ideal for demanding applications. For example, in the automotive sector, lightweight injection molded parts improve fuel efficiency without compromising durability. In medical devices, biocompatible materials ensure safety and reliability. The ability to create seamless, single-piece components also reduces the risk of failure caused by weak joints or seams, further enhancing overall performance.
Cost Efficiency and Scalability in Production
One of the key advantages of injection molded parts is their cost efficiency, particularly for large-scale production. While the initial mold development can be expensive, the per-unit cost decreases significantly as production volumes increase. This makes injection molding a cost-effective solution for industries requiring high-volume manufacturing. Additionally, automation and advanced mold-making techniques have streamlined the process, reducing labor costs and minimizing material waste. The ability to rapidly produce identical components ensures efficiency in supply chains and accelerates time-to-market for new products.
Customization and Design Flexibility with Injection Molded Parts
Injection molding offers remarkable flexibility in design, allowing manufacturers to create customized components tailored to specific needs. The process accommodates a variety of colors, textures, and finishes without the need for secondary processing. This is particularly valuable in consumer goods, where aesthetics play a crucial role in product appeal. Furthermore, manufacturers can integrate features such as threaded inserts, hinges, and multi-material layers directly into the injection molded parts, reducing the need for assembly and enhancing functionality.
Industry Applications of Injection Molded Parts
The versatility of injection molded parts has led to widespread adoption across multiple industries. In the automotive sector, they are used for everything from interior panels to under-the-hood components, improving vehicle performance and fuel efficiency. In the medical field, injection molded parts play a critical role in the production of syringes, surgical instruments, and implantable devices. The consumer electronics industry relies on injection molded parts for durable casings, connectors, and ergonomic designs. Even the aerospace industry benefits from lightweight, high-strength components that contribute to overall efficiency and safety. These diverse applications highlight the transformative impact of injection molding in modern product development.
Sustainability and Eco-Friendly Innovations in Injection Molded Parts
As sustainability becomes a global priority, the injection molding industry is embracing eco-friendly innovations. The use of biodegradable and recycled materials is on the rise, reducing plastic waste and environmental impact. Energy-efficient molding techniques, such as electric injection molding machines, help lower energy consumption. Additionally, advancements in biopolymers provide sustainable alternatives to traditional plastics without compromising performance. These efforts ensure that injection molded parts contribute to a greener, more sustainable future.
The Future of Injection Molded Parts in Product Design
The future of injection molded parts is driven by continuous advancements in technology. The integration of smart materials, such as shape-memory polymers and conductive plastics, is opening new frontiers in product functionality. 3D printing and hybrid molding techniques are enabling greater design freedom and rapid prototyping, reducing development time for new products. Additionally, artificial intelligence and automation are improving process efficiency, ensuring even higher precision and quality control. As these innovations progress, injection molded parts will continue to redefine the possibilities in product design and manufacturing.
Conclusion
Injection molded parts have revolutionized product design and performance, offering unmatched precision, efficiency, and versatility. Their ability to create complex, high-quality components at scale makes them indispensable across industries. As material innovations and sustainable practices continue to evolve, injection molding remains at the forefront of modern manufacturing. By embracing new technologies, manufacturers can push the boundaries of design and performance, ensuring that injection molded parts continue to shape the future of product development.