- April 11, 2025
- Posted by: feinuojixie
- Category: Injection Molding News
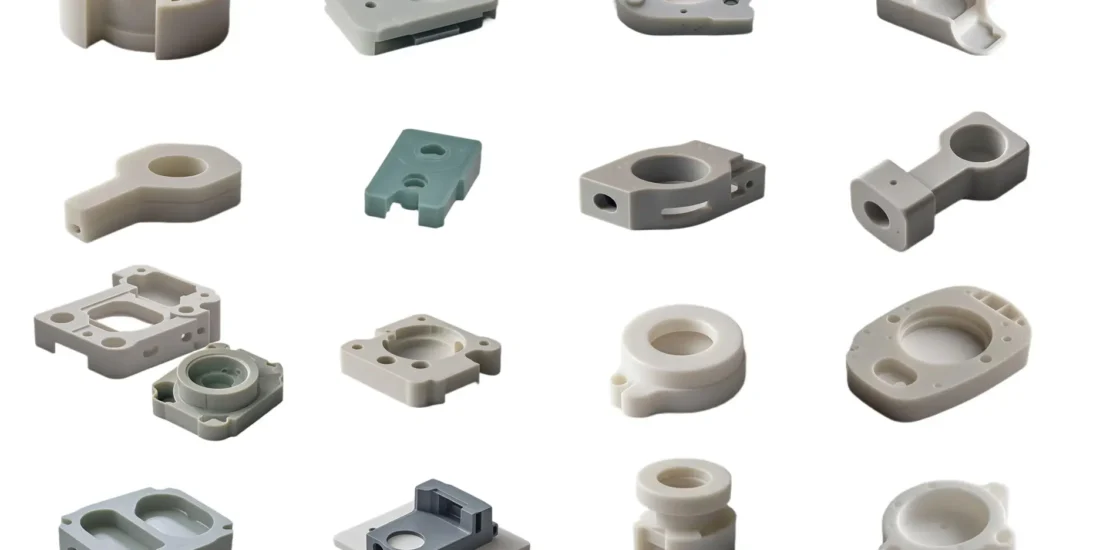
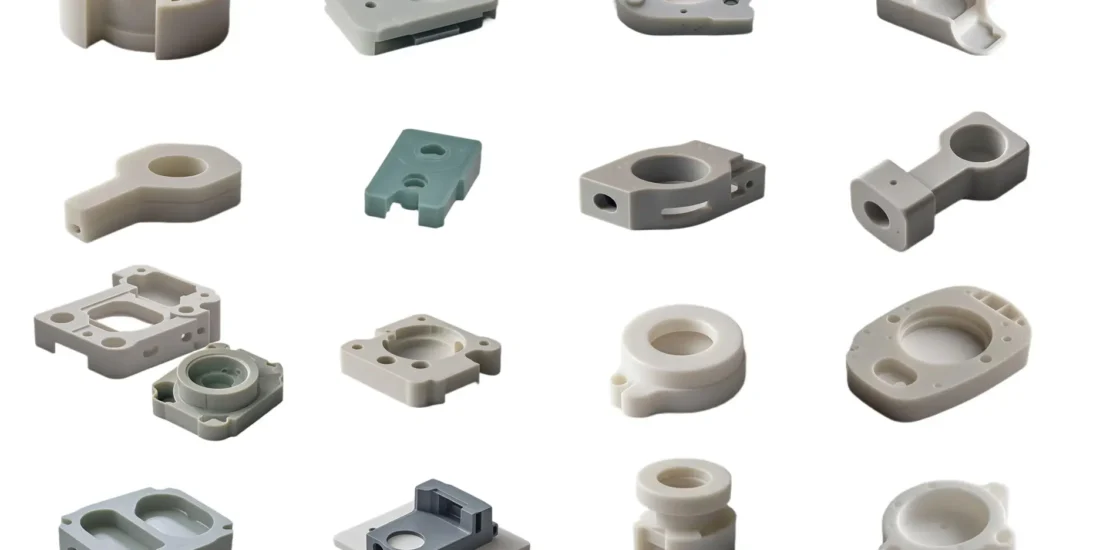
Over the past century, car manufacturing has undergone a dramatic transformation. From the early days of hand-assembled metal frames to today’s advanced automation and precision engineering, the industry has consistently evolved to meet growing consumer demands and technological advancements. One of the most significant shifts in recent years has been the widespread adoption of plastic injection molding parts. These components are rapidly replacing traditional metal parts across various sections of a vehicle—not only because they’re lighter and more cost-effective, but because they offer unmatched versatility in design and function.
In an era where fuel efficiency, safety, and sustainability are more critical than ever, plastic injection molding parts have emerged as a cornerstone of modern automotive engineering. They’re helping manufacturers innovate faster, reduce production costs, and meet stringent environmental regulations—all without compromising on quality or performance. As we look to the future of mobility, it’s clear that injection molding will continue to play a central role in shaping how cars are made, how they function, and how they evolve.
The Science Behind Plastic Injection Molding Parts
Plastic injection molding is a manufacturing process that involves injecting molten plastic material into a specially designed mold. Once the material cools and solidifies, it takes the shape of the mold cavity, forming a precise and durable component. This process is particularly suited for producing high volumes of identical parts with tight tolerances, making it ideal for the automotive industry.
The reliability and repeatability of plastic injection molding parts are key reasons why this method has gained prominence. It allows for the integration of complex geometries that would be difficult or expensive to achieve with traditional materials like metal. From small clips to entire dashboard frames, the technology enables manufacturers to deliver strong, lightweight components that perform under pressure.
Benefits of Plastic Injection Molding Parts in Automotive Design
One of the biggest advantages of plastic injection molding parts is their ability to reduce vehicle weight. Lightweight vehicles consume less fuel and emit fewer pollutants, aligning with global efforts toward cleaner transportation. Yet, this weight reduction doesn’t mean compromising strength. Modern thermoplastics used in injection molding offer excellent mechanical properties, including impact resistance and thermal stability.
Cost-efficiency is another critical benefit. Once the mold is created, manufacturers can produce thousands—or even millions—of identical parts at a fraction of the cost of traditional methods. Furthermore, plastic injection molding parts can be easily customized to fit specific design needs, allowing automakers to innovate with shape, texture, and functionality in ways that were previously impossible or cost-prohibitive.
Key Car Parts Now Produced Using Plastic Injection Molding
The reach of plastic injection molding parts extends across nearly every area of a vehicle. In the interior, parts like dashboard panels, air vents, door handles, and center consoles are frequently molded to ensure ergonomic design and sleek aesthetics. These components can be textured, colored, or finished to create a luxurious feel while remaining durable.
Exterior parts also benefit from this method. Bumpers, mirror housings, grilles, and light covers are commonly injection molded to combine strength with aerodynamic design. Their resistance to corrosion and ease of painting or coating make them ideal for standing up to environmental wear and tear.
Under the hood, functional parts such as coolant reservoirs, engine covers, fuse boxes, and cable holders are also being made using plastic injection molding. These parts often endure high heat and pressure, and engineering-grade plastics provide the necessary resilience while reducing overall vehicle weight.
Sustainability and Plastic Injection Molding Parts
Sustainability is a major driving force behind the increased use of plastic injection molding parts. Many manufacturers are turning to recycled or bio-based plastics to reduce reliance on fossil fuels. These eco-friendly materials not only lower the carbon footprint but also maintain the performance required for demanding automotive applications.
Moreover, the injection molding process itself is highly efficient, producing minimal waste compared to subtractive manufacturing methods. Excess plastic can often be reground and reused, making the process inherently more sustainable. This aligns perfectly with the automotive industry’s shift toward circular economy principles and long-term environmental responsibility.
Technological Innovations Enhancing Injection Molding
The future of plastic injection molding parts is being shaped by exciting new technologies. 3D printing, for example, is being used to rapidly create prototype molds, significantly cutting development time. This allows engineers to test and refine parts quickly before mass production.
Advanced machinery now incorporates smart sensors and AI-driven controls that monitor pressure, temperature, and cycle times in real-time, ensuring consistently high quality with every molded piece. Additionally, techniques like multi-material molding and insert molding are enabling the integration of metal reinforcements or electronic components directly into plastic parts, creating hybrid structures that are lighter and smarter.
Challenges and Future Potential of Plastic Injection Molding Parts
While plastic injection molding offers many advantages, it also comes with certain challenges. The upfront cost of tooling can be high, which makes it more suitable for high-volume production runs. However, as tooling technologies evolve and become more accessible, even small and mid-size manufacturers are starting to adopt this method.
Material limitations also remain a consideration. Not all plastics can match the strength or temperature resistance of metals. But breakthroughs in polymer science are quickly closing this gap. With ongoing research into high-performance thermoplastics, future plastic injection molding parts may rival or even surpass traditional materials in many aspects.
As the industry moves toward electric vehicles and autonomous driving, the demand for lightweight, high-functionality parts will only increase. Plastic injection molding is perfectly positioned to meet these demands, thanks to its adaptability, precision, and potential for integrating sensors and electronics.
The Road Ahead for Car Manufacturing
Plastic injection molding parts are no longer just a manufacturing option—they’re a strategic asset for the automotive industry. They enable faster innovation, lower production costs, and contribute to more sustainable vehicle designs. As new technologies and materials continue to emerge, this process will become even more vital to the creation of next-generation cars.
From the sleek interiors of luxury sedans to the functional components powering electric vehicles, plastic injection molding is reshaping how we think about car parts. It’s a transformation that’s not only redefining automotive engineering but also paving the way for a smarter, greener, and more efficient future on the road.