- April 22, 2025
- Posted by: feinuojixie
- Category: Injection Molding News
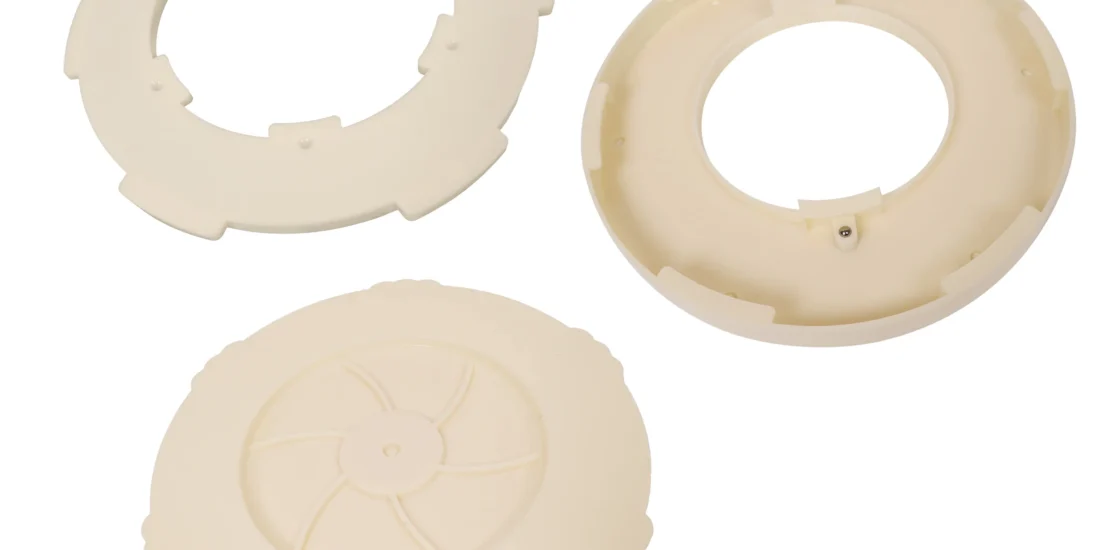
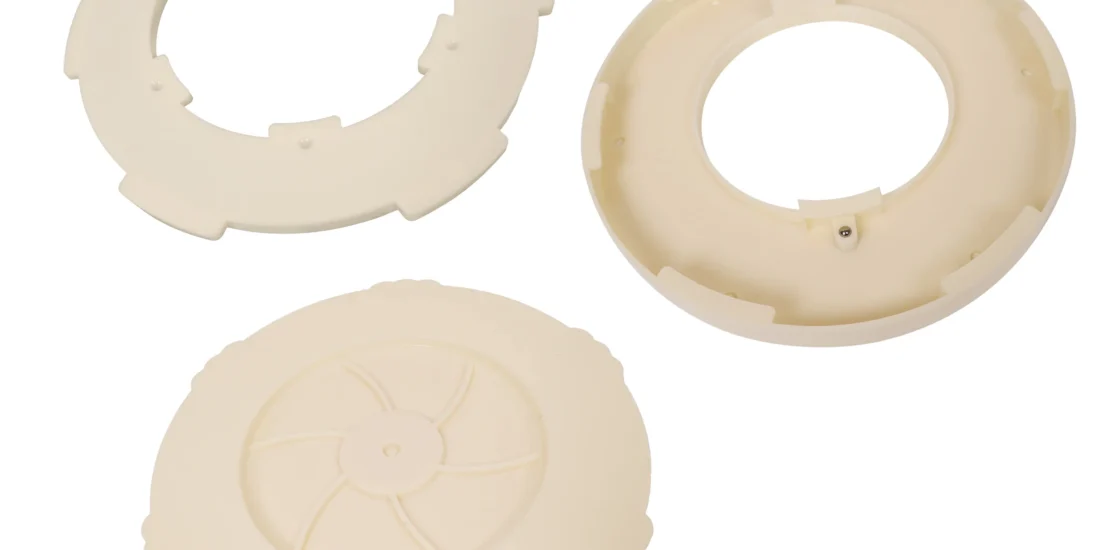
In today’s rapidly advancing industrial landscape, injection moulding stands out as a cornerstone technology for producing plastic parts with precision, efficiency, and adaptability. From everyday consumer goods to highly technical components used in aerospace and medical devices, the influence of injection moulding is nearly ubiquitous. What was once a niche manufacturing method has now evolved into a global standard, enabling companies to meet high demands while maintaining quality and cost control. As innovation continues to drive new expectations in performance and sustainability, injection moulding proves not only resilient but essential to shaping the future of plastic parts.
The Basics of Injection Moulding and Its Role in Manufacturing
Injection moulding is a manufacturing process that involves injecting molten material into a mould cavity, where it cools and solidifies into the final shape. This technique is especially well-suited for plastic parts due to the versatility and consistency of the process. The cycle begins with plastic pellets being melted, followed by high-pressure injection into a custom-designed mould. Once cooled, the mould opens, and the formed part is ejected.
What makes injection moulding unique is its ability to produce large quantities of identical plastic parts with minimal variation. Whether it’s a smartphone casing or an automotive dashboard component, the process delivers exceptional repeatability. For industries demanding reliability and speed, injection moulding has become the backbone of production.
Why Injection Moulding is Ideal for Precision Plastic Parts
When it comes to creating intricate and highly detailed plastic parts, injection moulding excels where other manufacturing methods fall short. The process supports complex geometries, undercuts, and delicate features, all with high dimensional accuracy. Advanced computer-aided design (CAD) software and precision-engineered steel moulds allow for the creation of components that meet stringent tolerances, especially critical in sectors like electronics and healthcare.
In addition, the automation capabilities of injection moulding ensure consistent output, reducing the margin for human error. This level of precision is vital not only for product functionality but also for brand reputation, especially in industries where failure is not an option.
Material Versatility in Injection Moulding for Plastic Parts
Injection moulding supports an impressive array of thermoplastics and polymers, each with specific characteristics suited to different applications. Whether a manufacturer needs flexibility, rigidity, thermal resistance, or biocompatibility, there’s a material that fits the requirement.
Commonly used materials include ABS, polycarbonate, polyethylene, nylon, and thermoplastic elastomers. More advanced or custom formulations are also available for highly specialized plastic parts. This material diversity ensures that injection moulding remains adaptable as new performance demands arise in various industries.
Cost-Effectiveness and Scalability of Injection Moulding Plastic Parts
One of the major advantages of injection moulding is its scalability. Although the initial investment in mould design and tooling can be high, the cost per part decreases significantly with higher production volumes. For mass production of plastic parts, no other process offers the same level of economic efficiency.
Automation also plays a key role in reducing labor costs and increasing production speed. Once set up, machines can run continuously with minimal supervision, ensuring high throughput and rapid return on investment. For businesses seeking to scale quickly while maintaining product quality, injection moulding offers a compelling solution.
Sustainability in Injection Moulding: Greener Plastic Parts for the Future
As sustainability becomes a central concern for consumers and regulators alike, injection moulding is evolving to meet environmental challenges. Many manufacturers are incorporating recycled plastics into their production lines without compromising product performance. Additionally, bio-based and biodegradable polymers are gaining popularity as eco-conscious alternatives.
Technological advancements in mould design and machine efficiency also reduce material waste and energy consumption. By optimizing cycle times and reusing excess plastic through closed-loop systems, the environmental impact of injection moulding is steadily decreasing, positioning it as a forward-thinking approach for creating plastic parts.
Innovations Driving the Future of Injection Moulding in Plastic Parts
The future of injection moulding is being shaped by innovations that enhance precision, speed, and connectivity. Smart manufacturing, powered by Industry 4.0 technologies, integrates sensors and data analytics into injection moulding machines. This enables real-time monitoring, predictive maintenance, and adaptive process controls that improve quality and reduce downtime.
Other breakthroughs include micro-moulding, which produces ultra-small and detailed plastic parts for use in electronics and medical devices, and multi-material moulding, which combines different plastics into a single part. These innovations expand the possibilities for product design and performance, pushing the boundaries of what plastic parts can do.
Applications Across Industries: Where Injection Moulding Plastic Parts Excel
Injection moulding has proven indispensable across a broad range of industries. In the automotive sector, it’s used for everything from interior panels to engine components, offering durability and lightweight alternatives to metal. The medical industry relies on it for sterile, high-precision devices such as syringes, catheters, and diagnostic housings.
In consumer electronics, injection moulding enables sleek, compact enclosures and intricate internal parts. Meanwhile, aerospace and defense sectors benefit from its strength-to-weight ratio and design flexibility. The adaptability of injection moulding ensures that it meets the unique demands of each industry, helping to drive innovation and performance forward.
Why Injection Moulding Will Continue to Shape Tomorrow’s Plastic Parts
As industries evolve and product expectations rise, injection moulding remains a vital process for the development of high-performance plastic parts. Its unmatched combination of precision, efficiency, material flexibility, and scalability makes it a future-proof solution in an ever-changing market.
The ongoing integration of sustainability practices and smart technologies will only enhance its capabilities, allowing manufacturers to create better, greener, and more innovative plastic parts. For companies seeking to stay competitive and responsive to global trends, injection moulding is not just a tool—it is a strategic advantage that will shape the future.