- March 28, 2025
- Posted by: feinuojixie
- Category: Injection Molding News
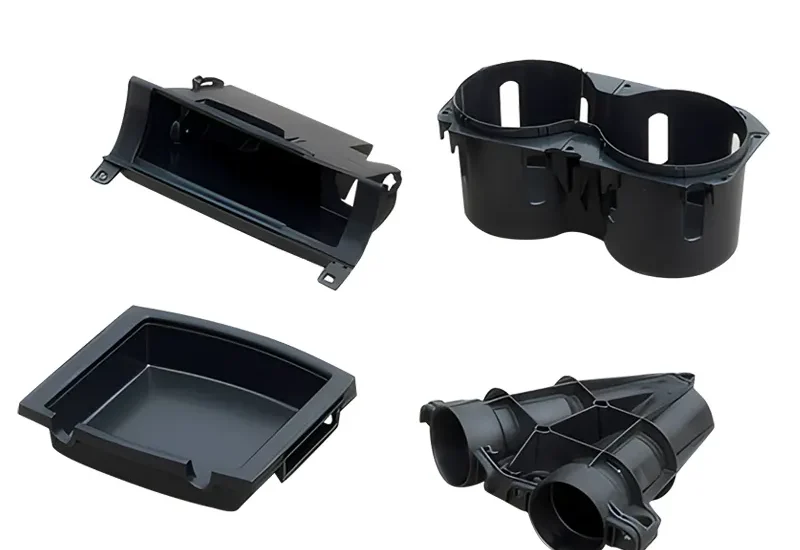
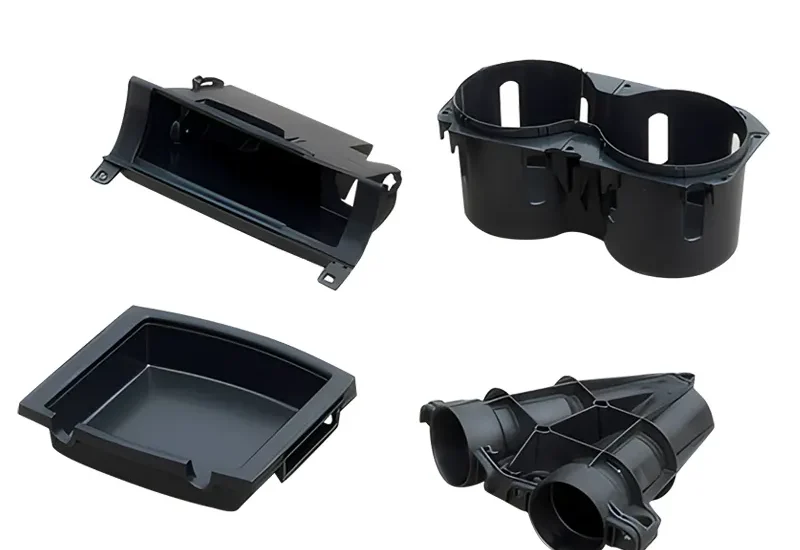
PC ABS injection moulding is a widely used manufacturing process that brings together the best qualities of polycarbonate (PC) and acrylonitrile butadiene styrene (ABS). This unique combination results in a material that is not only strong and impact-resistant but also flexible and aesthetically appealing. In today’s competitive market, where product durability and design matter equally, PC ABS injection moulding offers an ideal solution for industries ranging from automotive and electronics to consumer goods and medical devices.
This article explores how PC ABS injection moulding strikes the perfect balance between strength, flexibility, and aesthetics, making it an indispensable choice for manufacturers looking to create innovative and high-performance products.
Understanding PC ABS Injection Moulding
PC ABS injection moulding is a manufacturing process that utilizes a blend of polycarbonate (PC) and acrylonitrile butadiene styrene (ABS) to produce high-performance plastic components. PC contributes strength and heat resistance, while ABS enhances flexibility and processability. The combination results in a material that is durable, easy to mold, and visually appealing.
The process involves heating the PC ABS material until it becomes a molten state and then injecting it into a mold cavity. Once cooled and solidified, the final product retains the desired shape, exhibiting excellent mechanical and aesthetic properties. This makes PC ABS injection moulding a preferred method for creating complex and high-quality plastic components across multiple industries.
The Strength of PC ABS Injection Moulding
One of the most significant advantages of PC ABS injection moulding is its exceptional strength. The inclusion of polycarbonate gives the material high impact resistance, allowing it to withstand heavy loads and external pressures without cracking or breaking.
Products manufactured using PC ABS injection moulding maintain structural integrity under demanding conditions, making them ideal for applications where durability is crucial. For example, the automotive industry relies on PC ABS for interior and exterior components such as dashboards, door panels, and bumpers. Similarly, electronic device manufacturers use PC ABS injection moulding to produce robust casings that protect delicate internal components from damage.
The Flexibility of PC ABS Injection Moulding
Flexibility is another key feature of PC ABS injection moulding. The presence of ABS in the blend enhances the material’s processability, allowing manufacturers to create intricate and lightweight designs with ease. Unlike some rigid plastics, PC ABS can be molded into thin-walled structures without compromising strength, making it a versatile choice for complex applications.
Moreover, PC ABS injection moulding ensures consistent performance across a range of temperatures. Whether exposed to extreme heat or cold, the material retains its mechanical properties, making it suitable for outdoor applications, automotive components, and industrial equipment that experience fluctuating environmental conditions.
The Aesthetic Advantages of PC ABS Injection Moulding
Beyond strength and flexibility, PC ABS injection moulding also offers impressive aesthetic benefits. The material supports smooth and glossy finishes, making it an excellent choice for consumer-facing products that require a premium look and feel. Manufacturers can enhance the visual appeal of PC ABS components by incorporating textures, coatings, or custom colors during the moulding process.
For instance, electronic devices such as smartphones, laptops, and gaming consoles often feature PC ABS housings that provide both durability and an attractive appearance. The ability to produce visually appealing products without sacrificing strength further solidifies PC ABS injection moulding as a leading choice in modern manufacturing.
Applications of PC ABS Injection Moulding in Different Industries
PC ABS injection moulding is widely used across various industries due to its unique combination of properties. Some key applications include:
-
Automotive: Dashboards, center consoles, door panels, and exterior trims benefit from the impact resistance and design flexibility of PC ABS injection moulding.
-
Electronics: Many gadgets, including smartphone casings, laptop bodies, and electrical connectors, are manufactured using PC ABS due to its excellent insulation and durability.
-
Medical: PC ABS injection moulding is used in medical devices and equipment housings, providing a balance of lightweight construction, durability, and chemical resistance.
-
Consumer Goods: From household appliances to sports equipment, PC ABS injection moulding is essential for producing stylish, sturdy, and long-lasting products.
Why Choose PC ABS Injection Moulding for Manufacturing
PC ABS injection moulding offers a unique balance of strength, flexibility, and aesthetics, making it a superior choice for manufacturers. Compared to other plastics, PC ABS provides enhanced impact resistance, better thermal stability, and greater design freedom.
Additionally, sustainability is becoming a crucial consideration in modern manufacturing. PC ABS injection moulding supports recyclability, allowing manufacturers to reduce waste and create environmentally friendly products. The efficiency of the injection moulding process also helps lower production costs by minimizing material wastage and reducing cycle times.
Conclusion
PC ABS injection moulding is a powerful solution for producing durable, flexible, and visually appealing plastic components. Its ability to combine strength and impact resistance with processability and aesthetic versatility makes it a top choice for industries such as automotive, electronics, medical, and consumer goods.
By leveraging the advantages of PC ABS injection moulding, manufacturers can create high-quality products that meet the demands of modern consumers. Whether designing protective casings for electronic devices or durable parts for vehicles, PC ABS injection moulding delivers unmatched performance and reliability.