- May 2, 2025
- Posted by: feinuojixie
- Category: Injection Molding News
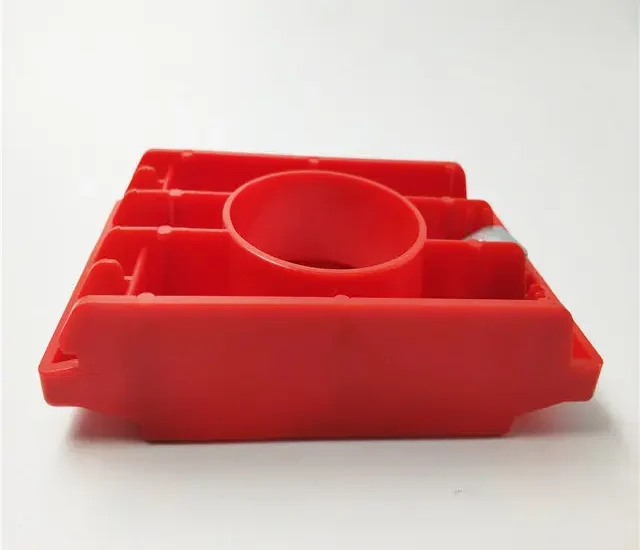
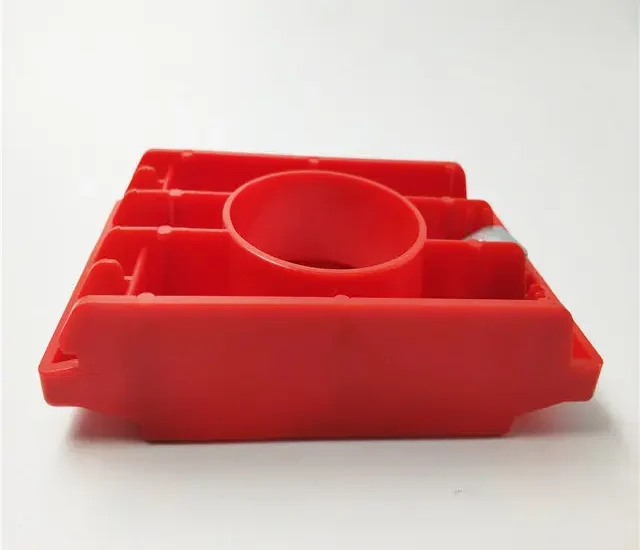
Plastic injection molded parts may not often make headlines, but they are quietly revolutionizing the way we manufacture everything from life-saving medical tools to next-generation consumer gadgets. These components are created through a precise, high-volume manufacturing process that injects molten plastic into a mold, resulting in products that are not only consistent in quality but also cost-effective and highly adaptable. Over the last few decades, they have become essential in nearly every sector—from healthcare and automotive to aerospace and electronics. This silent evolution is shaping the modern world by making innovation more accessible, manufacturing more scalable, and products more efficient.
Plastic Injection Molded Parts in Everyday Life
Plastic injection molded parts are embedded in countless items we encounter every day, often without us realizing it. From the ergonomic handle of a toothbrush to the durable casing of a coffee maker, these parts provide functionality, comfort, and aesthetic appeal. Their use allows for complex shapes and intricate designs to be produced quickly and affordably, enabling manufacturers to meet high consumer demands without sacrificing quality. Whether it’s home appliances, toys, or packaging, plastic injection molded parts help make modern convenience possible at scale.
Why Plastic Injection Molded Parts Are Essential in Medical Technology
In the medical field, precision, hygiene, and reliability are non-negotiable. Plastic injection molded parts play a crucial role in ensuring these standards are met. They are used in syringes, inhalers, diagnostic equipment, and even implantable devices. The ability to produce sterile and complex components in large volumes makes them indispensable to the medical industry. Additionally, the compatibility of medical-grade plastics with sensitive biological environments enables innovation in patient care and surgical precision. Their consistent performance is a quiet but vital contributor to advancing healthcare worldwide.
The Automotive Industry’s Transformation Through Plastic Injection Molded Parts
Modern vehicles are a blend of advanced technology, safety engineering, and sleek design—all of which rely heavily on plastic injection molded parts. From dashboards and interior trim to engine components and lighting housings, these parts help reduce vehicle weight, which in turn improves fuel efficiency and reduces emissions. They also enhance crash safety by enabling energy-absorbing designs. Manufacturers favor them not only for their versatility and durability but also for their ability to support large-scale production with tight tolerances. As cars become smarter and more efficient, plastic injection molded parts are driving the transformation.
Plastic Injection Molded Parts Driving Innovation in Consumer Electronics
The demand for smaller, lighter, and more powerful electronic devices has accelerated the use of plastic injection molded parts in this sector. Smartphones, laptops, gaming consoles, and wearable devices all rely on finely engineered plastic components for structural integrity, thermal management, and aesthetic design. These parts allow for intricate internal layouts and seamless exterior finishes, giving manufacturers the flexibility to innovate rapidly. With trends like miniaturization and modular design, plastic injection molded parts have become fundamental to achieving sleek, user-friendly tech products.
Sustainability and Efficiency: The Green Potential of Plastic Injection Molded Parts
As industries worldwide face mounting pressure to reduce their environmental footprint, plastic injection molded parts are undergoing a green transformation. Advances in biodegradable resins, recycled materials, and closed-loop manufacturing systems are making these parts more sustainable. Efficient production methods also minimize waste and energy use. Additionally, because these parts are lightweight and strong, they contribute to reduced material consumption and lower transportation emissions. The evolution of eco-friendly plastics and smarter designs is aligning this manufacturing method with the global push for sustainability.
The Role of Plastic Injection Molded Parts in the Future of Aerospace
Aerospace engineering demands materials that are lightweight, durable, and capable of withstanding extreme conditions. Plastic injection molded parts meet these requirements while offering significant cost and weight savings over traditional metal components. They are now used in everything from cabin interiors and ducting systems to electrical housings and structural brackets. Their application reduces overall aircraft weight, which directly impacts fuel efficiency and carbon emissions. As space exploration and commercial aviation evolve, these parts are poised to play an even greater role in pushing the boundaries of aerospace innovation.
Customization and Prototyping: The Agile Power of Plastic Injection Molded Parts
In an age of rapid innovation and personalized products, the adaptability of plastic injection molded parts is a key asset. They are ideal for creating prototypes quickly and affordably, allowing companies to test and iterate designs before mass production. Modern mold-making techniques and digital design tools enable a high degree of customization, from medical implants tailored to individual patients to specialized enclosures for electronic startups. This agility supports faster product development cycles and opens the door to niche applications that were once economically unfeasible.
The Future Molded in Plastic
Plastic injection molded parts are far more than simple components—they are the building blocks of modern progress. Their presence across diverse industries demonstrates their unmatched versatility, efficiency, and potential for innovation. As materials science advances and sustainability becomes a central concern, these parts are evolving to meet the demands of the future. Whether shaping the next generation of medical breakthroughs, transportation systems, or digital devices, plastic injection molded parts will remain at the core of how we design, produce, and live in the world of tomorrow.