- April 30, 2025
- Posted by: feinuojixie
- Category: Injection Molding News
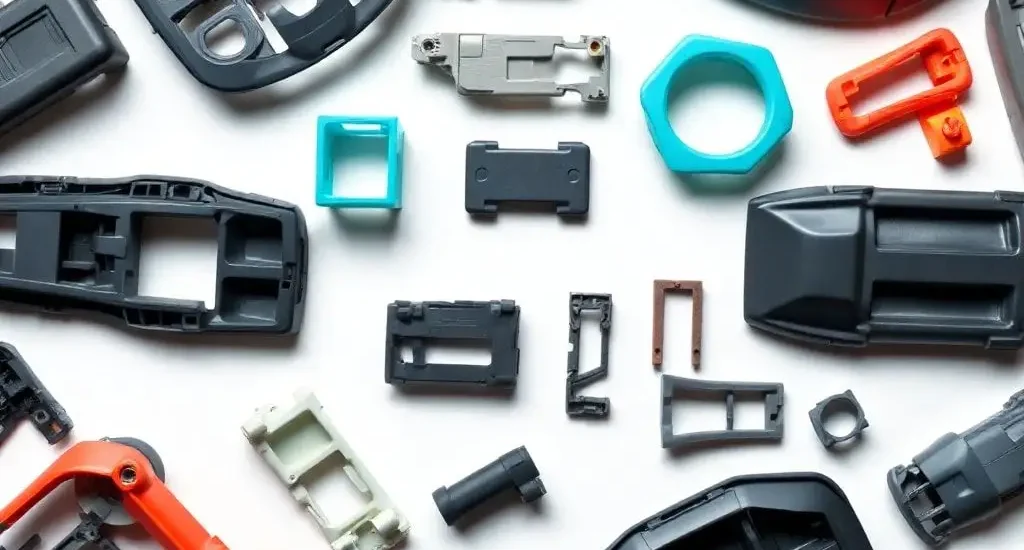
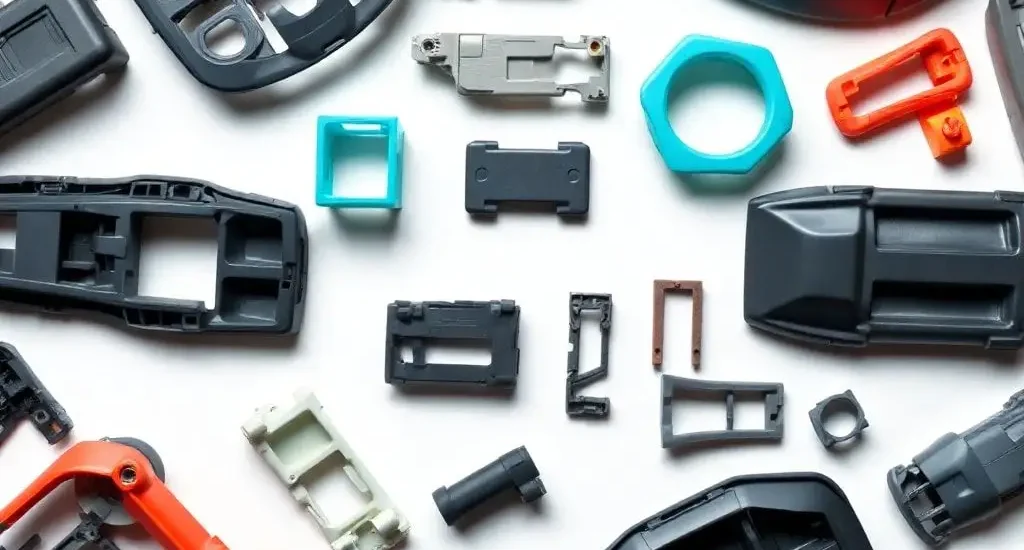
Large part injection molding is a cornerstone technology in industries such as automotive, construction, agriculture, and aerospace. Whether manufacturing dashboards, outdoor equipment housings, or large appliance panels, the ability to produce high-quality, structurally sound large parts consistently is a competitive advantage. However, achieving perfection in large part injection molding is far from simple. The process brings a host of technical challenges that demand deep expertise, advanced tools, and rigorous process control.
From ensuring even material distribution in massive molds to dealing with the complexities of long cooling times and intense clamp force requirements, manufacturers must navigate a minefield of potential pitfalls. This article explores the most common challenges in large part injection molding and presents smart, proven solutions that can help you master the process and deliver flawless results. Whether you’re refining an existing process or embarking on a new large part project, these insights will guide your path toward precision and success.
Understanding the Scope of Large Part Injection Molding
Large part injection molding involves creating plastic components that are physically large in size, often exceeding several feet in length or width. These parts are commonly found in automotive body panels, industrial containers, utility vehicle components, and infrastructure-related products. Unlike smaller molded parts, large parts require molds with greater surface area, increased shot size, and highly robust injection molding machines.
Beyond the equipment, large part molding brings unique complexities in design, processing, and material behavior. The stakes are higher—any defect can be costly due to the size of the part and the material used. Success hinges on a combination of precise engineering, thorough planning, and strict quality control.
Key Challenges in Large Part Injection Molding
Material Flow and Fill Consistency
One of the most critical challenges in large part injection molding is achieving uniform material flow. Large molds demand high-volume plastic injection and balanced runner systems to ensure all areas fill evenly. Inadequate flow can result in short shots, voids, or weld lines that compromise structural integrity and visual appeal. Variations in wall thickness further complicate the process, increasing the likelihood of imbalanced flow or pressure drops across the mold.
Tooling Complexity and Mold Design
Designing a mold for a large part is an engineering challenge in itself. These molds are often multi-cavity or feature complex geometry that requires advanced cooling layouts, strategic gating, and proper venting. Factors such as shrinkage rates, parting lines, and ejection methods must be considered in greater detail than for smaller parts. A poorly designed mold can lead to dimensional inaccuracy, flashing, or long cycle times that reduce efficiency.
Cycle Time and Cooling Efficiency
Due to their mass and size, large parts naturally require longer cooling periods. This extended cooling time can dramatically increase the overall cycle time if not managed properly. Non-uniform cooling can also result in internal stress and warpage. Efficient thermal management—achieved through optimized water channels, baffles, and heat-conductive materials—is essential to keep production lean while maintaining part quality.
Machine Capability and Clamp Force Requirements
Large part injection molding demands machines with significant shot capacity, long tie bars, and high clamp force. Insufficient clamp force can lead to mold separation and flash, especially when dealing with high-pressure resin flows. Machine selection must align precisely with the mold’s specifications, including mold weight, injection pressure, and platen size. Oversizing or undersizing the machine can result in wasted energy or inconsistent molding outcomes.
Part Warpage and Dimensional Stability
Achieving dimensional accuracy in large parts is particularly difficult due to material shrinkage and cooling gradients. Warpage is a common issue that leads to assembly problems, performance defects, or rejection of the final product. Asymmetric designs or inconsistent wall thicknesses make this even more pronounced. Proper design techniques and controlled processing parameters are necessary to ensure that the final part retains its intended shape and dimensions.
Proven Solutions to Overcome These Challenges
Advanced Simulation and Mold Flow Analysis
Modern simulation tools allow engineers to visualize material behavior before any physical mold is built. Mold flow analysis helps identify potential filling issues, air traps, weld lines, and cooling inefficiencies. By digitally simulating the injection process, engineers can optimize gate placement, runner design, and material selection early in development—reducing costly trial-and-error during production.
Segmented Mold Heating and Cooling
Temperature control is critical to producing consistent large parts. Segmented cooling and heating systems allow for precise thermal management across the mold’s surface. This approach ensures uniform shrinkage and minimizes internal stress, especially in complex or asymmetric parts. By maintaining tight temperature control zones, manufacturers can reduce cycle times and improve part quality.
Use of High-Performance Materials
The right material choice can significantly affect the success of large part injection molding. High-flow resins improve fill performance, while glass-filled or impact-resistant polymers offer added strength without excessive warpage. Engineers must consider not only mechanical properties but also flow characteristics, shrinkage rates, and thermal behavior to ensure optimal performance.
Precision Mold Machining and Maintenance
Large molds must be built with exceptional precision. Even minor deviations in machining can lead to flashing, misalignment, or uneven parting lines. Equally important is ongoing mold maintenance, which includes cleaning vents, polishing surfaces, and verifying alignment. A well-maintained mold maintains part consistency and extends mold life, offering better return on investment.
Operator Training and Process Standardization
Human expertise remains a critical factor. Skilled operators who understand the nuances of large part injection molding can make real-time adjustments, recognize early signs of defects, and maintain process discipline. Standardizing work instructions, documenting best practices, and providing continuous training are essential for consistent output and long-term quality assurance.
Case Studies: Success Stories in Large Part Injection Molding
One example comes from an automotive manufacturer that faced warpage issues in bumper molding. By switching to a segmented cooling system and fine-tuning the mold flow, they reduced cycle time by 15% and eliminated dimensional defects. Another company in the agricultural sector improved material distribution for large utility panels by implementing a flow simulation during design, resulting in a 98% first-pass yield rate.
These cases illustrate how attention to process and design details can solve major issues in large part injection molding—and drive both quality and efficiency improvements.
Driving Excellence in Large Part Injection Molding
Achieving perfection in large part injection molding is a multifaceted challenge. It demands a blend of technology, expertise, and process control. By understanding common pitfalls—such as material flow issues, warpage, and tool complexity—and applying proven solutions like simulation, advanced temperature control, and skilled labor, manufacturers can elevate their capabilities.
Precision is not a luxury in large part injection molding—it’s a necessity. Investing in the right tools, training, and engineering practices enables companies to not only meet expectations but exceed them. As demand for large, durable, cost-effective plastic parts grows, those who master this art will lead the future of plastic manufacturing.