- April 2, 2025
- Posted by: feinuojixie
- Category: Injection Molding News
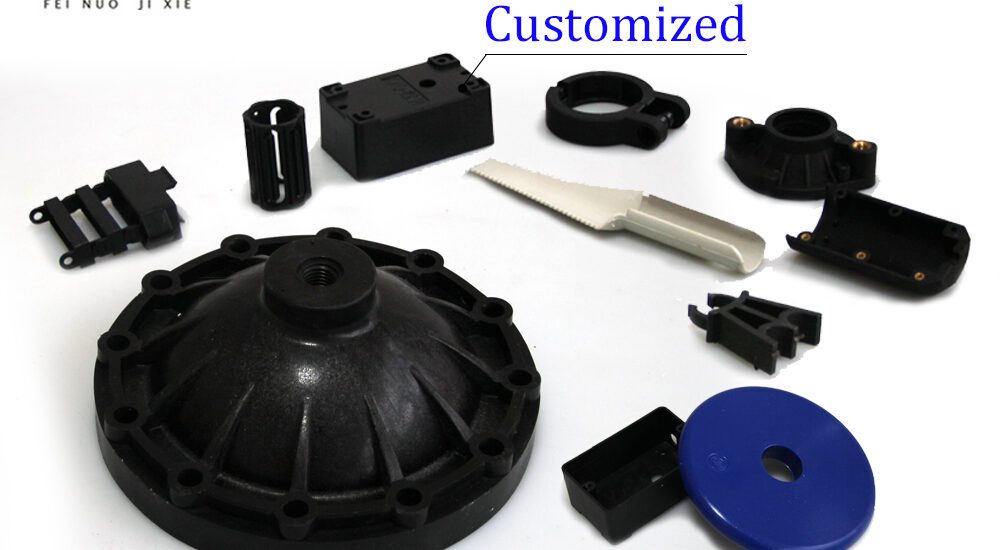
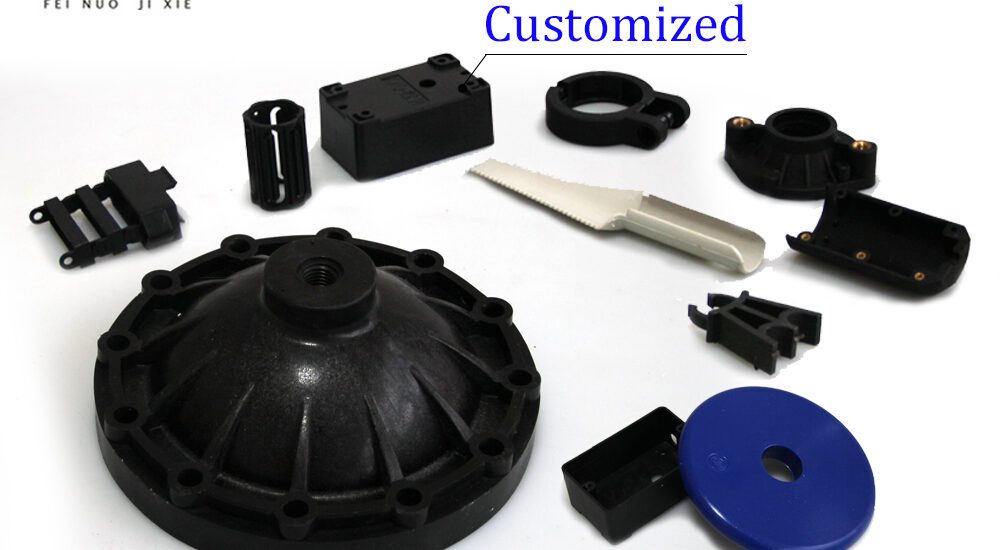
Injection machine part plays a crucial role in the efficiency and productivity of plastic molding operations. These components endure constant stress, high temperatures, and continuous use, making them susceptible to wear and tear. Proper maintenance and care are essential to prolong their lifespan, ensuring consistent performance and reducing costly downtime. This article provides a comprehensive guide on the best practices to keep injection machine part in optimal condition.
Understand the Common Causes of Wear and Tear
Several factors contribute to the deterioration of injection machine part. Friction, heat, and pressure from prolonged operation accelerate the wear process. Improper lubrication leads to increased resistance and component damage, while contamination from dust, dirt, and plastic residue can interfere with functionality. Neglecting routine maintenance further exacerbates these issues, leading to premature part failure. Understanding these factors helps in implementing preventive measures.
Regular Cleaning to Prevent Damage
Dirt and debris accumulation can severely impact injection machine part performance. Regular cleaning is necessary to remove contaminants that cause malfunctions or inefficiencies. Use manufacturer-recommended cleaning agents to avoid corrosion or material degradation. Ensure that all machine parts, including molds, screws, and nozzles, are free from plastic residue and dust. Implementing a strict cleaning schedule can significantly improve the longevity of these components.
Lubrication Best Practices for Optimal Performance
Proper lubrication reduces friction and prevents excessive wear on injection machine part. Select lubricants specifically designed for high-temperature and high-pressure applications. Ensure even application of lubricants to moving components such as bearings, gears, and hydraulic systems. Over-lubrication or under-lubrication can both cause issues, so follow the manufacturer’s guidelines for optimal results. Establishing a regular lubrication routine helps maintain smooth machine operation.
Routine Inspection and Early Detection of Issues
Regular inspections allow early detection of potential problems before they escalate into costly repairs. Look for visible signs of wear, such as cracks, rust, leaks, or unusual noises during operation. Use a maintenance checklist to systematically assess key components, ensuring no issue goes unnoticed. Preventive maintenance helps avoid unexpected breakdowns, extending the service life of injection machine part.
Proper Storage and Handling of Spare Part
Incorrect storage conditions can compromise the quality of spare part before they are even used. Store components in a clean, dry environment away from extreme temperatures and humidity. Organize spare part systematically to prevent misplacement or accidental damage. Following manufacturer-recommended storage practices preserves part integrity and ensures they remain functional when needed.
Timely Replacement of Worn-Out Part
Delaying the replacement of worn-out part can lead to machine inefficiencies and unexpected failures. Monitor the operational lifespan of key components and replace them before they become a liability. Identify high-quality replacement part that meet original specifications to ensure compatibility and durability. Investing in timely replacements prevents major disruptions and keeps the injection machine running smoothly.
Training Operators to Minimize Equipment Strain
Operator handling directly impacts the longevity of injection machine part. Proper training ensures that employees use machines correctly, minimizing unnecessary strain on components. Encourage best practices such as gradual start-ups, avoiding overloading, and adhering to maintenance protocols. Providing regular training sessions enhances operational efficiency and prolongs the service life of machine part.
Upgrading and Retrofitting for Better Durability
Technological advancements in injection machine part offer improved durability and efficiency. Upgrading to modern materials, such as wear-resistant alloys and high-performance coatings, can significantly extend part lifespan. Retrofitting older machines with newer components enhances performance and reduces the frequency of part replacement. Assessing the cost-benefit of upgrades helps in making informed decisions for long-term equipment health.
Conclusion
Extending the lifespan of injection machine part requires a proactive approach to maintenance and care. Regular cleaning, lubrication, inspections, and timely replacements are key to ensuring smooth machine operation. Proper training of operators and exploring upgrade options further contribute to enhanced durability and efficiency. By implementing these best practices, manufacturers can reduce operational costs, prevent downtime, and maximize the productivity of their injection molding systems.