- May 4, 2025
- Posted by: feinuojixie
- Category: Injection Molding News
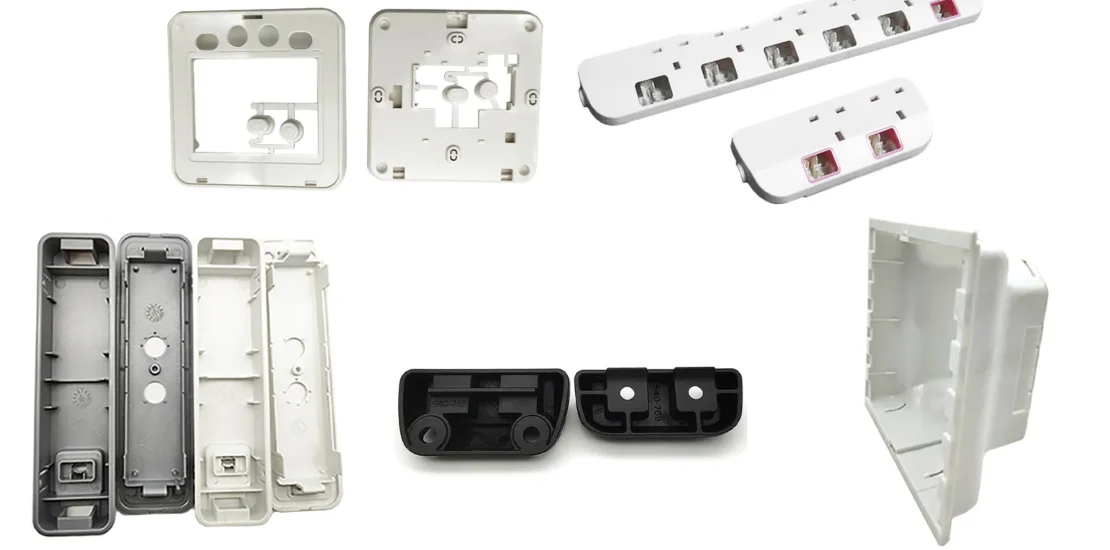
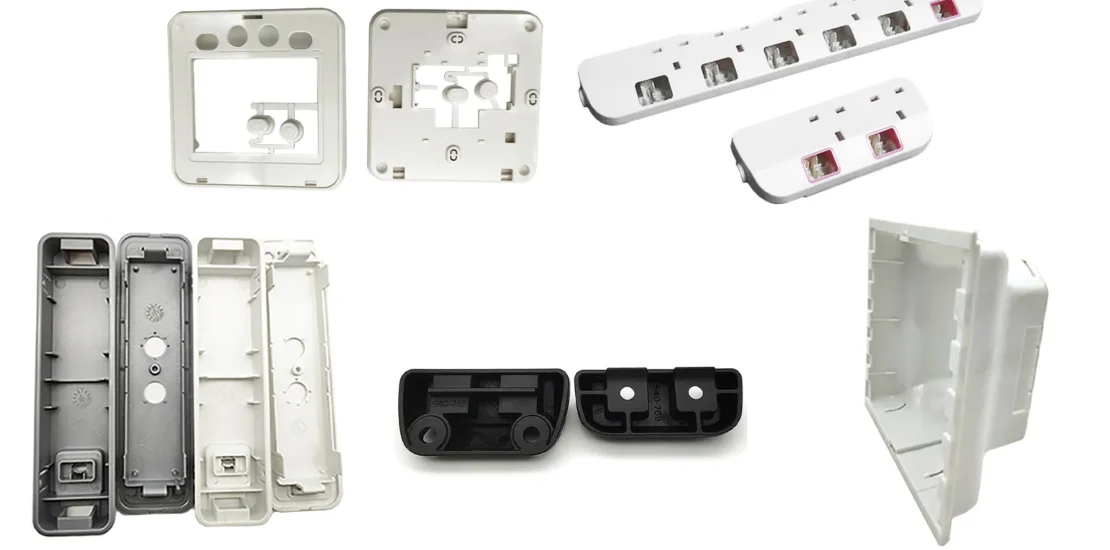
Plastic injection molded parts are the cornerstone of countless products, from everyday consumer goods to high-performance industrial components. However, not all molded parts are created equal. Whether you’re a seasoned engineer or a newcomer to the manufacturing world, knowing how to spot a top-tier plastic injection molded part can save you from costly mistakes and ensure that your products meet the highest standards. In this article, we’ll dive deep into the key factors that define a high-quality plastic injection molded part, providing expert tips and insights that will help you identify the best of the best every time.
Understanding Plastic Injection Molded Part Quality
When it comes to plastic injection molded parts, quality is paramount. A top-tier part is one that performs flawlessly under its intended conditions, lasts through extensive use, and meets strict design specifications. To understand the quality of a molded part, it’s essential to recognize the features that make it stand out. These include precision in dimensions, a smooth surface finish, consistent strength, and no defects or imperfections.
In addition, high-quality injection molded parts are manufactured using state-of-the-art technologies and controlled processes that minimize variation. This consistency in production results in parts that not only look good but also function reliably. By understanding what makes a part high-quality, you’ll be able to quickly identify the ones that meet the highest standards, ensuring that your products are up to the task.
Material Selection: The Foundation of Quality
The material used in a plastic injection molded part is one of the most critical factors affecting its overall quality. Different materials offer various properties, such as strength, flexibility, resistance to heat, or impact resistance, depending on the requirements of the part. Common materials like ABS, polycarbonate, and nylon all have distinct advantages that contribute to the part’s performance.
For example, polycarbonate is known for its durability and impact resistance, making it ideal for automotive or safety equipment. Meanwhile, ABS is often used for parts requiring good mechanical strength and ease of post-processing. Understanding how each material impacts the performance and longevity of a plastic injection molded part is crucial for ensuring quality.
When assessing a part’s quality, it’s important to verify that the right material has been selected for the specific application. Materials that are improperly chosen for the design’s requirements may compromise the part’s integrity, resulting in failures during use.
Design and Engineering: A Critical Influence on Part Quality
Design and engineering play a pivotal role in the production of top-tier plastic injection molded parts. One of the most important factors to consider is design for manufacturing (DFM). DFM involves optimizing the part’s design to ensure that it is cost-effective to produce, durable, and easy to mold. A well-designed part minimizes the risk of defects and ensures that the injection molding process runs smoothly.
Advanced engineering tools like Computer-Aided Design (CAD) software are essential in creating precise, intricate designs that align with both functional and aesthetic requirements. CAD allows engineers to simulate the molding process, test designs, and predict potential issues before production begins. This level of precision ensures that the final part is a true reflection of the design and meets the highest standards.
In addition, the part’s wall thickness, rib design, and gating system can all affect the quality of the final product. Ensuring that these elements are optimized can help achieve a uniform, defect-free molded part.
Molding Process: Ensuring Precision and Perfection
The injection molding process itself is key to achieving a high-quality part. Precision in molding is determined by several factors, including cycle time, temperature, pressure, and the specific molding machine used. Each of these variables must be controlled carefully to avoid defects like warping, air bubbles, or incomplete filling.
The molding machine type also plays a significant role in part quality. High-end machines are capable of producing parts with tighter tolerances and greater consistency. For example, electric injection molding machines are often more precise and produce fewer defects than hydraulic machines, making them ideal for parts requiring exact specifications.
A top-tier molded part should have consistent dimensions, a smooth finish, and structural integrity. Variations in temperature or pressure during molding can result in parts that are weak or have defects that are difficult to detect initially but lead to long-term failures.
Finishing and Post-Processing: The Final Touch for Top-Tier Parts
Once the plastic injection molded part has been produced, the finishing and post-processing stages ensure that it meets the final quality standards. Finishing techniques, such as trimming, polishing, painting, and coating, are essential for improving the aesthetic appeal and durability of the part. For example, a polished surface can make a part look more professional and increase its resistance to wear and tear.
Post-processing can also include methods like ultrasonic welding or assembly, which may be necessary to achieve a final functional part. The quality of these finishing processes is just as important as the molding itself, as any imperfections in the finishing can affect the part’s performance and visual appeal.
Testing and Inspection: Ensuring Consistent Excellence
A top-tier plastic injection molded part is only one that has undergone rigorous testing and inspection. Various tests can be used to measure key properties like strength, flexibility, and durability, ensuring that the part will perform as expected under real-world conditions.
Dimensional testing ensures that the part fits perfectly within its intended application, while functional tests simulate actual use conditions to ensure reliability. Additionally, inspection methods like visual checks, pressure testing, and material analysis can identify defects that may not be visible initially but could cause long-term issues.
Top-tier suppliers will have comprehensive quality control processes in place to inspect every part thoroughly before it reaches the customer, ensuring that only the best products are delivered.
Signs of a Top-Tier Plastic Injection Molded Part
So, how do you spot a top-tier plastic injection molded part? Look for several key characteristics that define quality:
-
Surface Finish: A smooth, even surface with no noticeable defects like cracks, bubbles, or scratches.
-
Dimensional Accuracy: The part should have precise measurements that align with the design specifications.
-
Consistency: Each part should look and perform the same as every other part in the batch, with minimal variation.
-
Strength and Durability: The part should be able to withstand the stresses of its intended use without cracking or degrading.
By paying attention to these factors, you can quickly identify high-quality plastic injection molded parts that will deliver excellent performance and longevity.
Choosing the Right Supplier for Quality Parts
Selecting the right supplier is crucial in ensuring that you receive top-tier plastic injection molded parts. A reliable supplier should have a proven track record of producing high-quality parts, a commitment to continuous improvement, and the ability to meet your specific requirements.
When evaluating potential suppliers, ask about their experience, quality control processes, and capabilities in terms of material selection, design, and production technology. Don’t hesitate to ask for samples or references to confirm their ability to deliver the best quality parts.
Choosing a supplier with the right expertise ensures that your parts will be manufactured to the highest standards and perform reliably in the field.
Conclusion
In conclusion, spotting top-tier plastic injection molded parts requires a thorough understanding of the factors that contribute to quality. From material selection to design, molding, finishing, and inspection, each stage in the manufacturing process plays a vital role in determining the final product’s performance. By keeping these key elements in mind, you can confidently identify parts that will deliver durability, precision, and long-term value. When choosing suppliers, remember that expertise, attention to detail, and a commitment to quality are essential for ensuring that you receive the best possible parts for your projects. By following the insights shared in this article, you can become a pro at identifying top-tier plastic injection molded parts every time.