- April 1, 2025
- Posted by: feinuojixie
- Category: Injection Molding News
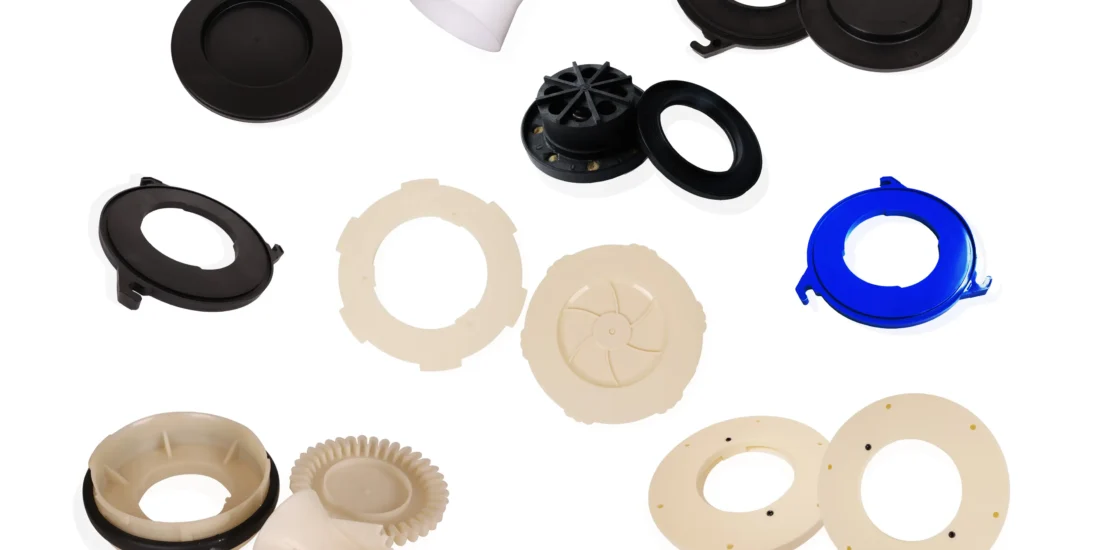
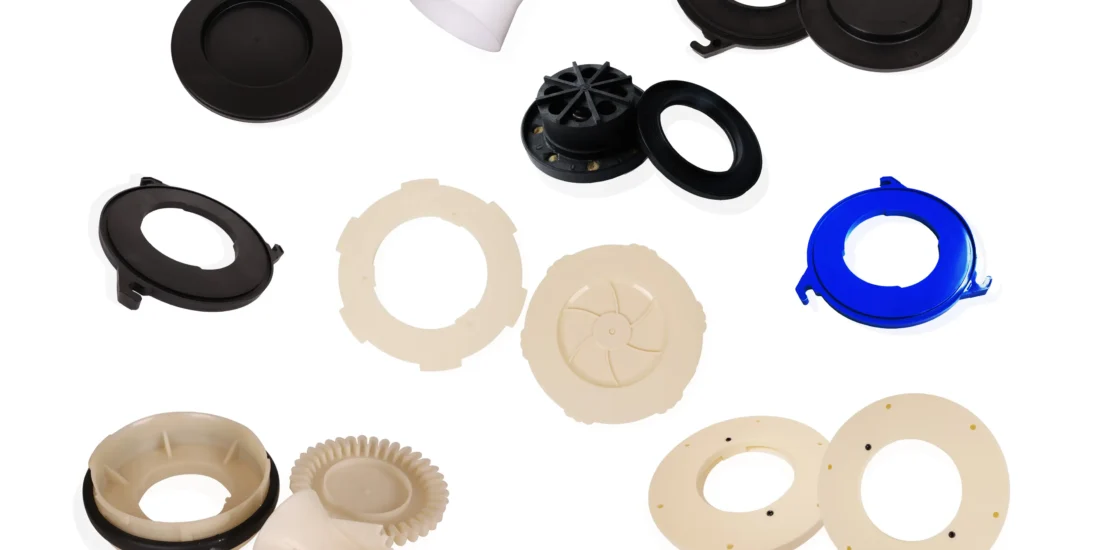
Injection machine parts play a crucial role in the injection molding process, ensuring the efficient production of high-quality plastic products. Each part of an injection machine has a specific function that contributes to the precision and speed of manufacturing. Understanding these components is essential for machine operators, maintenance technicians, and manufacturers who want to optimize their production process.
This guide explores key injection machine parts, explaining their roles and how they work together to create molded products. Whether you are new to injection molding or looking to enhance your knowledge, this article will provide valuable insights into the core components of an injection machine.
Injection Unit: The Core of Material Processing
The injection unit is where the raw material undergoes melting and is prepared for injection into the mold. Several key components within the injection unit work together to process the material and ensure it is delivered to the mold cavity in the correct form.
-
Hopper
The hopper is where raw plastic material (usually in the form of pellets) is stored before being introduced into the injection unit. It serves as the first stage in the material handling process, ensuring that a constant supply of raw material is available for injection. The hopper must be kept clean and free of contaminants to prevent defects in the final product. -
Barrel
The barrel is a heated cylinder that houses the screw and is responsible for melting the plastic material. The material enters the barrel from the hopper, and as it moves through the barrel, it is heated to its molten state by the application of heat from electric heaters. The barrel must maintain a precise temperature to ensure that the material melts evenly and does not degrade. -
Screw
The screw is a rotating shaft inside the barrel that mixes and pushes the molten plastic forward toward the nozzle. As the screw turns, it shears the material, increasing its temperature and ensuring that it is fully melted. The screw also plays a critical role in mixing any additives or colorants that may be included in the material. The design of the screw is crucial for achieving the correct melt flow and pressure required for efficient injection. -
Nozzle
The nozzle is the final point of delivery for the molten plastic. Located at the end of the barrel, the nozzle injects the molten plastic into the mold cavity under high pressure. The nozzle must provide a smooth and consistent flow of material to ensure proper filling of the mold. Additionally, the nozzle needs to maintain a constant temperature to prevent the material from solidifying prematurely.
Clamping Unit: Holding the Mold in Place
The clamping unit is responsible for securely holding the mold together during the injection process. This unit ensures that the mold is tightly closed when the injection occurs, preventing leakage and ensuring the accuracy of the final product.
-
Clamping Mechanism
The clamping mechanism is a mechanical system that applies force to keep the mold halves securely together during injection. It provides the necessary force to hold the mold closed while the molten plastic is injected. If the clamping force is insufficient, the mold may open during injection, leading to defects like flash or incomplete parts. The clamping mechanism is powered either hydraulically or electrically, depending on the machine design. -
Tie Bars
Tie bars are sturdy metal rods that support the clamping unit and ensure that the mold remains in alignment during the injection process. These bars provide the necessary rigidity to withstand the pressure exerted by the molten plastic as it enters the mold. -
Mold Plates
The mold plates are the surfaces that hold the mold halves in place. They are typically made from durable steel or aluminum and are designed to withstand high temperatures and pressures. The front and rear mold plates support the stationary and moving halves of the mold, respectively. These plates also help distribute the clamping force evenly across the mold, ensuring proper part formation.
Mold System: Creating the Desired Shape
The mold system is where the shape of the final product is formed. This system consists of the mold cavity and associated components that work together to shape and cool the injected material.
-
Fixed and Moving Mold Halves
The fixed mold half is stationary and contains the cavity that defines the shape of the molded part. The moving mold half, on the other hand, moves to allow the molded part to be ejected once the injection cycle is complete. The alignment and precision of these mold halves are essential to creating parts with accurate dimensions and smooth surfaces. -
Ejector System
After the plastic has cooled and solidified, the ejector system pushes the molded part out of the mold. The ejector system consists of pins or plates that apply force to the part, allowing it to be removed without damaging the mold or the product. In some cases, air pressure may also be used to assist in part ejection. -
Cooling Channels
Cooling is a critical part of the injection molding process. Cooling channels run through the mold and circulate a cooling fluid (typically water) to reduce the temperature of the molded part. Proper cooling ensures that the material solidifies correctly, preventing warping or dimensional changes in the part. The design and placement of the cooling channels are key factors in achieving uniform cooling and minimizing cycle times.
Hydraulic and Electrical Components: Powering the Machine
Injection machines require both hydraulic and electrical power to operate efficiently. These systems control the movements of the machine’s various parts, including the clamping unit, injection unit, and other auxiliary components.
-
Hydraulic System
The hydraulic system provides the force required to operate the clamping unit and injection system. It uses pressurized oil to drive pistons and cylinders, which are responsible for moving the clamping plates, screw, and nozzle. The hydraulic system must maintain a constant pressure to ensure precise control of these movements. -
Electric Motors
Electric motors are used to drive the various mechanical components of the injection machine. These motors power the screw, the clamping unit, and the hydraulic pump (if the machine is equipped with a hybrid or all-electric system). Electric motors are favored for their energy efficiency and precise control of movements. -
Control Panel
The control panel is the operator’s interface with the injection machine. It allows the user to adjust various parameters, including temperature, injection pressure, and cycle time. The control panel may also include safety features, diagnostic tools, and programmable settings for different types of injection molding processes.
Auxiliary Equipment: Supporting the Molding Process
Several auxiliary systems are essential for ensuring the efficiency and quality of the injection molding process. These components provide additional support for temperature regulation, material handling, and part handling.
-
Temperature Controller
A temperature controller maintains the mold temperature at the optimal level for the injection process. This is essential for achieving consistent part quality, as temperature fluctuations can lead to defects such as warping or incomplete filling of the mold. Temperature controllers can regulate both the mold and the material temperature, ensuring that both remain within a specific range. -
Material Dryer
Plastic materials can absorb moisture from the air, which can negatively impact the molding process. A material dryer is used to remove excess moisture from the plastic pellets before they are introduced into the injection machine. This step helps prevent issues like surface defects, bubbles, or weak parts caused by water in the material. -
Conveyor System
Once the molded part is ejected from the mold, it is typically transported to a secondary processing area. A conveyor system helps move the parts efficiently from one stage to another, reducing the need for manual labor and increasing overall productivity.
Common Issues and Maintenance Tips
Like any complex machinery, injection machines can experience wear and tear over time. Understanding common issues and performing regular maintenance can help extend the life of the injection machine parts.
-
Screw Wear
Over time, the screw can experience wear, particularly in the threads and flights. This can lead to issues such as inconsistent material flow or improper mixing of additives. Regular inspection and maintenance are key to identifying signs of wear early. -
Inconsistent Heating
Heating issues in the barrel or nozzle can lead to material degradation or poor mold filling. It is important to regularly calibrate the temperature sensors and heating elements to ensure proper functionality. -
Hydraulic Leaks
Hydraulic leaks can occur due to seal wear or damage to hoses. Leaks should be addressed immediately, as they can cause a loss of pressure, affecting the clamping and injection cycles. Regular inspection of the hydraulic system is essential for detecting and fixing leaks. -
Routine Maintenance
Performing regular maintenance on injection machine parts, including cleaning, lubrication, and calibration, helps ensure optimal performance. Operators should follow the manufacturer’s recommended maintenance schedule to prevent unplanned downtime and costly repairs.
Conclusion
Injection machine parts are essential components that work together to produce high-quality molded products. Understanding the function of each part and how they contribute to the molding process is crucial for optimizing efficiency, minimizing defects, and ensuring longevity of the machine. Regular maintenance and proactive care of these parts are critical for maintaining peak performance. By focusing on both the key components and proper maintenance practices, manufacturers can improve production output and reduce costs in the long run.