- April 2, 2025
- Posted by: feinuojixie
- Category: Injection Molding News
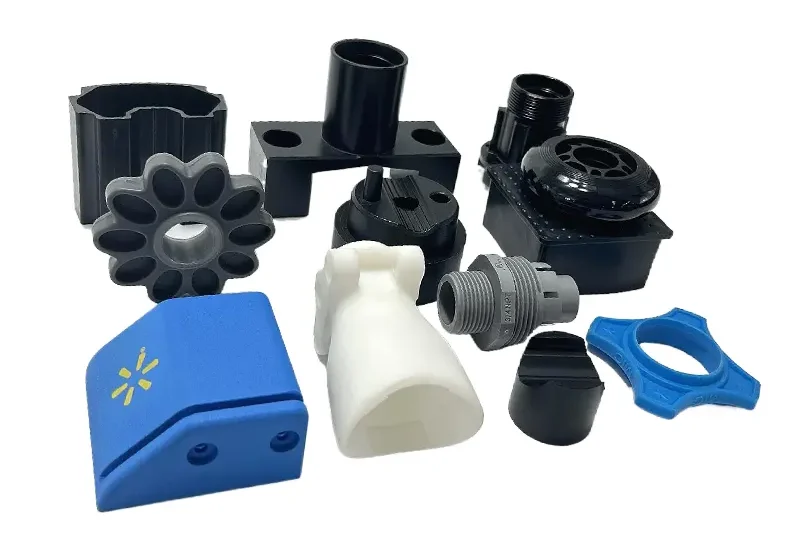
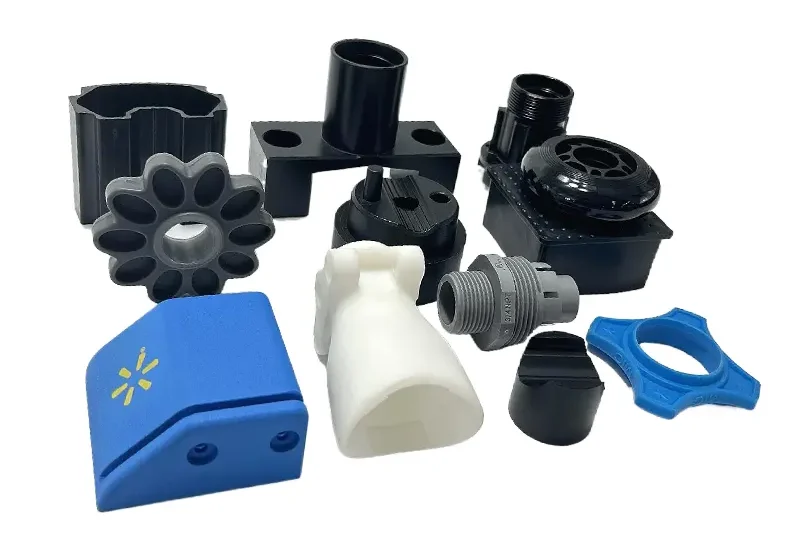
Injection molding is a widely used manufacturing process for producing plastic components with high precision and efficiency. Understanding injection machine parts is crucial for optimizing production, reducing downtime, and maintaining product quality. Each component in an injection machine plays a vital role in ensuring smooth operation, from melting raw materials to shaping and cooling the final product.
In this guide, we will break down the essential injection machine parts, explaining their functions and how they contribute to maximum efficiency. Whether you are a manufacturer, technician, or industry enthusiast, mastering the structure and operation of these components can enhance your understanding of the injection molding process.
An injection machine is a complex system composed of multiple interconnected components, each contributing to the overall efficiency of the molding process. The machine is typically divided into three primary sections: the injection unit, the clamping unit, and the mold system. These sections work together to ensure precise material processing, controlled injection, and stable mold operation.
A well-structured injection machine is designed to provide durability and long-term stability. The frame, which houses the various components, must be strong enough to withstand high pressures during operation. Additionally, the alignment of moving parts plays a crucial role in ensuring precision and reducing wear and tear over time.
Injection Unit: The Heart of the Process
The injection unit is responsible for melting plastic material and injecting it into the mold. This section contains several key parts that determine the efficiency and quality of the injection process.
Hopper
The hopper is the entry point of the machine, where raw plastic material (usually in the form of granules or pellets) is fed into the system. Some hoppers are equipped with drying systems to remove moisture from the plastic before processing, preventing defects in the final product.
Barrel and Heater Bands
Once the plastic enters the barrel, it is heated to a specific temperature using heater bands. These bands ensure even heat distribution, allowing the plastic to melt consistently without degradation. Proper temperature control in this stage is crucial for maintaining material integrity.
Screw and Check Valve
The screw is a rotating component that moves plastic forward while simultaneously mixing and compressing it. The check valve at the end of the screw ensures that molten plastic flows in the correct direction, preventing backflow and ensuring a consistent injection process.
Nozzle
The nozzle is the final component in the injection unit, acting as a pathway through which molten plastic enters the mold. It must be designed to prevent leakage and allow smooth material flow. Some machines have temperature-controlled nozzles to maintain the ideal viscosity for injection.
Clamping Unit: Ensuring Mold Stability and Precision
The clamping unit holds the mold in place and applies the necessary force to keep it securely closed during injection. This ensures that the plastic takes the correct shape without leakage or deformation.
Clamping Mechanism
Injection machines use either hydraulic or mechanical clamping systems to apply pressure to the mold. The required force depends on the size and complexity of the mold, as well as the type of plastic being used.
Toggle System vs. Hydraulic Clamping
-
Toggle System: Uses a series of levers to generate clamping force. It is energy-efficient and works well for high-speed molding cycles.
-
Hydraulic Clamping: Uses hydraulic pressure to apply force evenly across the mold, providing high precision and consistency.
Platen and Tie Bars
The platen is a flat surface that holds the mold in place, while tie bars provide structural support and ensure proper alignment. These components must be robust to withstand continuous high-pressure cycles.
Mold System: Shaping the Final Product
The mold system is where the plastic takes its final shape. A high-quality mold ensures precision, consistency, and smooth surface finishes.
Core and Cavity
The core and cavity are the two halves of the mold that shape the plastic part. The cavity forms the outer surface, while the core defines internal details. These components must be precisely machined for accurate molding.
Ejector System
Once the plastic solidifies, the ejector system pushes the finished product out of the mold. This is done using ejector pins or plates that apply controlled force to avoid damaging the part.
Cooling and Venting System
Cooling channels within the mold help regulate temperature and speed up the solidification process. Proper venting prevents air pockets and ensures complete filling of the mold cavity.
Hydraulic and Electrical Systems: Powering the Machine
The hydraulic and electrical systems work together to control various machine functions, including movement, temperature regulation, and injection speed.
Hydraulic Pumps and Valves
Hydraulic pumps generate the pressure needed for injection and clamping. Valves regulate this pressure to ensure smooth operation.
Servo Motors and Control Panels
Modern injection machines use servo motors for precise control over movement and speed. Control panels allow operators to adjust settings, monitor performance, and troubleshoot issues.
Sensors and Safety Features: Ensuring Reliable Operation
To maintain consistent production quality and protect both the machine and its operators, injection machines are equipped with advanced sensors and safety mechanisms.
Temperature Sensors and Pressure Gauges
These sensors monitor conditions within the injection unit and mold system. If temperatures or pressures exceed safe limits, the machine can automatically adjust settings or shut down to prevent damage.
Safety Doors and Emergency Stops
Most machines have safety doors that prevent access to moving parts during operation. Emergency stop buttons allow immediate shutdown in case of malfunctions or accidents.
Maintenance and Troubleshooting for Maximum Efficiency
Regular maintenance is essential for preventing breakdowns and ensuring long-term efficiency.
Routine Maintenance Checks
-
Inspect heater bands and replace any damaged units.
-
Lubricate moving parts to reduce friction and wear.
-
Clean the hopper and barrel to prevent material contamination.
Common Issues and Solutions
-
Uneven Injection: May be caused by temperature fluctuations or blockages in the nozzle.
-
Flashing (Excess Plastic on Edges): Could result from excessive injection pressure or mold misalignment.
-
Short Shots (Incomplete Filling): Might be due to low injection speed or air trapped in the mold.
Future Trends in Injection Machine Parts
Advancements in injection machine technology are continually improving efficiency and sustainability.
Advanced Materials for Durability
New materials such as reinforced steel alloys and ceramic coatings are being used to extend the lifespan of key components, reducing wear and tear.
Smart Injection Technology
With the integration of AI and IoT, modern injection machines can automatically optimize settings based on real-time data. This reduces material waste, improves cycle times, and enhances overall production quality.
Conclusion
Understanding injection machine parts is essential for maximizing efficiency and ensuring high-quality production. Each component, from the injection unit to the mold system, plays a critical role in shaping the final product. Regular maintenance and knowledge of troubleshooting techniques can help prevent costly downtime and improve overall performance.
As technology advances, injection machines are becoming more precise, efficient, and automated. Staying informed about the latest innovations can help manufacturers maintain a competitive edge in the industry. By mastering the functions and maintenance of injection machine parts, businesses can achieve better productivity, reduced costs, and superior product quality.