- April 1, 2025
- Posted by: feinuojixie
- Category: Injection Molding News
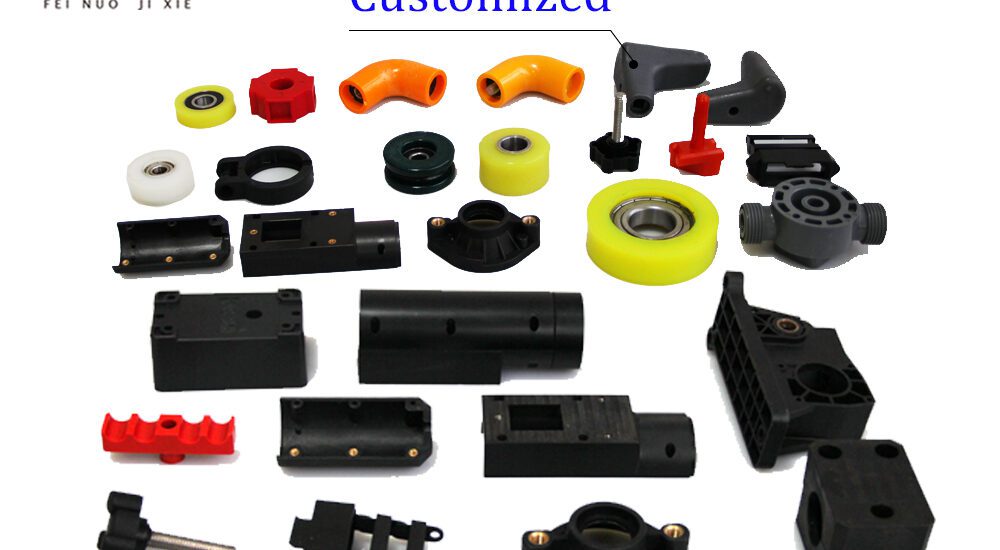
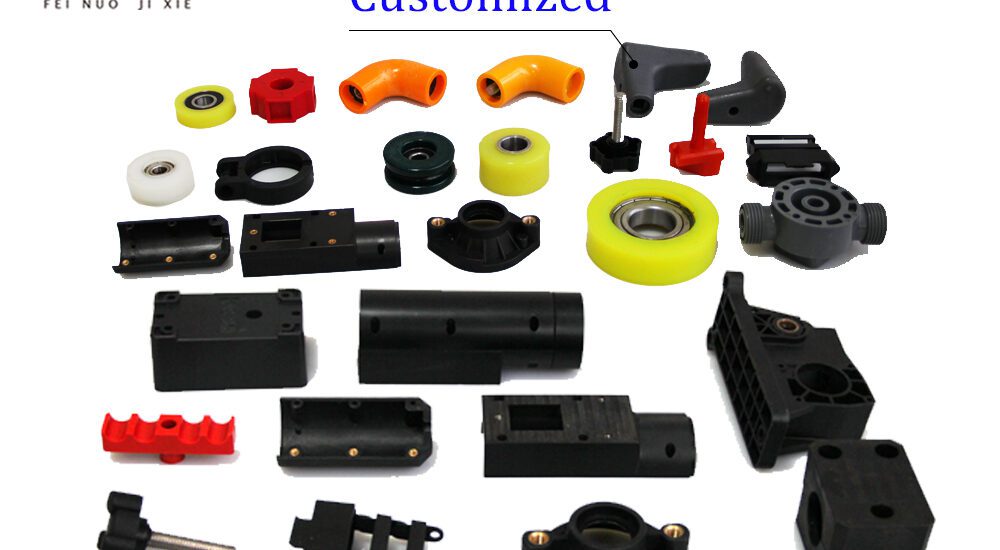
Injection machines are integral to manufacturing industries, especially those involved in producing plastic components. These machines must operate efficiently to maintain product quality and minimize operational costs. A critical factor in achieving such performance is the quality and condition of the individual machine parts. Regularly upgrading key injection machine parts can significantly enhance productivity, minimize waste, and extend the machine’s lifespan. This blog explores the must-have upgrades for better performance, focusing on the crucial parts that play a role in optimizing injection molding operations.
Understanding the Key Injection Machine Parts
Before diving into upgrades, it’s essential to understand the critical parts of an injection machine. At the core of any injection molding system are components like the barrel, screw, nozzle, clamping system, hydraulic systems, and controllers. Each part plays a distinct role in the injection process, from melting raw materials to injecting them into molds. Ensuring that these parts work seamlessly together is key to achieving optimal results.
Enhancing Injection Efficiency with Upgraded Machine Parts
Injection efficiency is the backbone of a productive manufacturing process. Cycle time, material flow, temperature control, and injection speed all hinge on the machine’s parts working in harmony. Upgrading certain injection machine parts can significantly impact these factors, leading to reduced energy consumption, less material waste, and a faster overall production process. For example, replacing older components with newer, high-quality ones can result in more precise control over injection speed and temperature regulation.
Injection Machine Part: Why You Should Prioritize the Barrel
The barrel is an essential part of an injection machine, responsible for heating the raw materials and transporting them toward the injection mold. Its performance directly impacts the consistency and quality of the molded parts. Upgrading the barrel ensures that the material is heated more efficiently, reducing cycle times and energy consumption. A high-quality barrel also prevents common issues such as material degradation, which can lead to defective parts. Investing in a high-quality barrel will improve throughput while minimizing maintenance costs.
Injection Machine Part: The Nozzle and Its Impact on Performance
The nozzle is the part where the molten material exits the injection machine and enters the mold. It significantly influences the speed and precision of the injection process. A worn or improperly sized nozzle can cause uneven material flow, leading to defects in the final product. Upgrading to a high-performance nozzle ensures a smoother material flow, better injection speed, and higher-quality parts. It can also prevent clogging issues, ensuring the machine operates smoothly for longer periods.
Upgrading the Screw for Better Performance
The screw is responsible for mixing, melting, and conveying the plastic material within the barrel. An efficient screw design ensures that the material is thoroughly mixed and reaches the correct temperature before injection. By upgrading to a screw that is designed for higher performance, manufacturers can reduce energy consumption, improve melt quality, and decrease cycle times. This also leads to fewer material waste issues and better overall part consistency.
The Importance of a Robust Injection Machine Controller
The controller acts as the brain of the injection machine, regulating the various components to ensure precise and accurate performance. It manages temperature, injection speed, pressure, and other critical parameters. Upgrading the controller can improve the machine’s responsiveness and accuracy, reducing errors and improving production consistency. Modern controllers offer features like automated monitoring, real-time adjustments, and predictive maintenance alerts, which can significantly boost operational efficiency.
Improving Mold Clamping Systems for Better Results
The clamping system holds the mold in place during the injection process. Its performance is crucial to the overall quality of the molded parts, as improper clamping can cause defects such as warping, misalignment, or insufficient filling. Upgrading the mold clamping system allows for better control over the molding process, ensuring more consistent part quality and faster cycle times. Enhanced clamping systems also reduce the likelihood of mold damage, which can be costly to repair.
Injection Machine Parts: Optimizing Hydraulic Systems
Hydraulic systems provide the necessary force to operate the injection machine’s moving parts. The performance of these systems directly affects the machine’s speed, power, and overall efficiency. Upgrading hydraulic components, such as pumps, valves, and hoses, can improve machine performance by providing faster response times and more stable pressure. Hydraulic upgrades also reduce the risk of leaks and other failures, contributing to the machine’s overall longevity.
Choosing the Right Cooling System for Your Injection Machine
Efficient cooling is essential for maintaining the quality and speed of the injection molding process. Cooling systems remove excess heat from the mold and machine components, ensuring that parts solidify at the correct rate. Upgrading to an advanced cooling system can reduce cycle time and improve part quality by preventing overheating. Better cooling also minimizes the risk of thermal damage to the mold and machine, which can cause expensive downtime.
Maintenance and Longevity: The Long-Term Benefits of Upgrading Injection Machine Parts
Upgrading injection machine parts not only boosts immediate performance but also extends the lifespan of the machine. High-quality, modern parts are designed to withstand wear and tear, reducing the need for frequent repairs. This can significantly lower maintenance costs and minimize machine downtime, ensuring consistent production output. Regular upgrades are also essential for keeping the machine aligned with the latest industry standards and technological advancements.
Investing in Quality Injection Machine Parts for Better Performance
Investing in high-quality injection machine parts can have a profound impact on the overall performance of your production line. By prioritizing upgrades to critical components such as the barrel, nozzle, screw, and controller, you can achieve faster cycle times, better part quality, and reduced operational costs. Regular updates and careful maintenance are crucial for ensuring that your machine operates at peak performance for years to come.