- February 20, 2025
- Posted by: feinuojixie
- Category: Injection Molding News
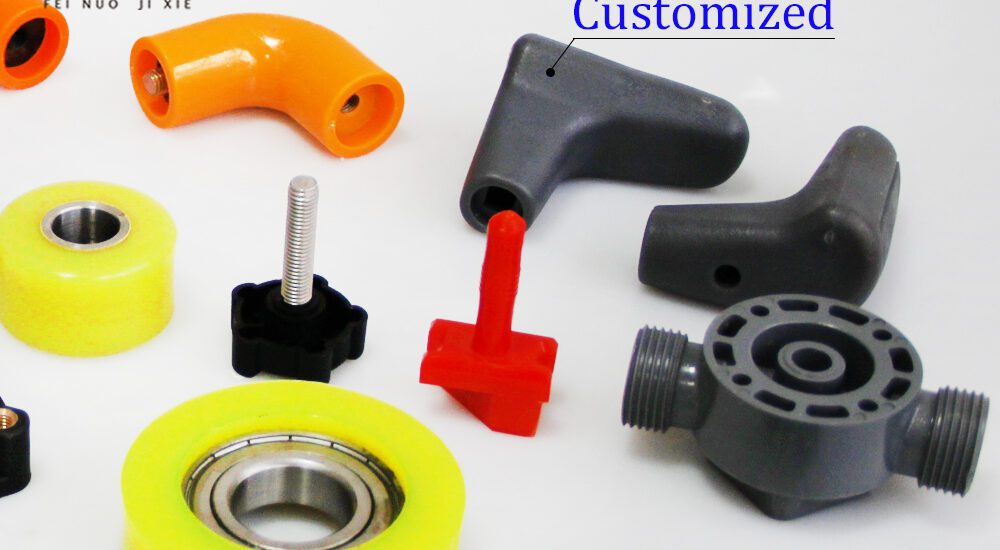
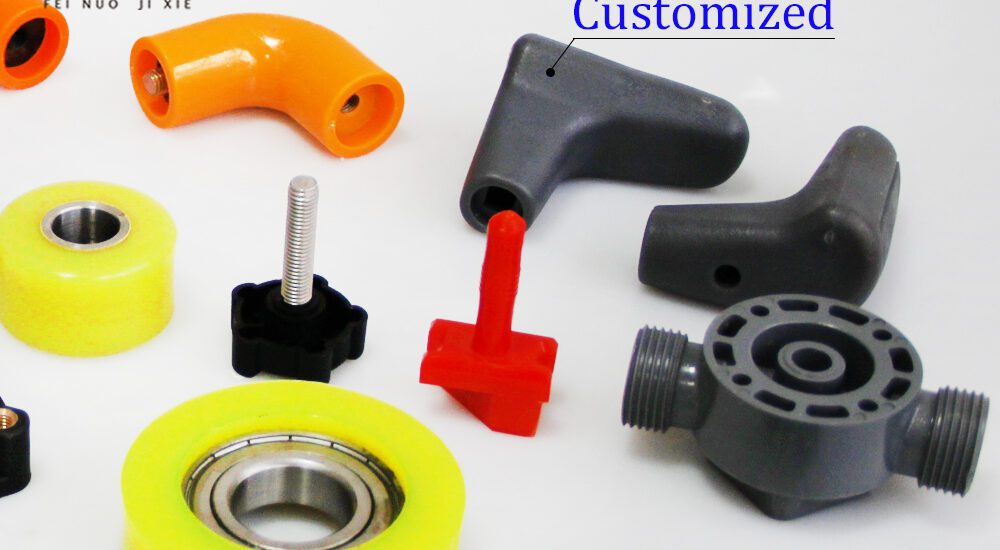
In the ever – evolving landscape of modern manufacturing, injection molded parts have emerged as a cornerstone of precision engineering. These parts are everywhere, from the tiny components in our smartphones to the large structural elements in automobiles. Their ubiquity is a testament to their importance and the remarkable capabilities they offer.
What are Injection Molded Parts?
At its core, injection molding is a manufacturing process where molten material, typically plastic, is injected into a mold cavity. The mold is carefully designed to the exact shape of the desired part. Once the material cools and solidifies, the mold opens, and the finished injection molded part is ejected. This process allows for the creation of complex shapes with high repeatability. For example, the production of a small plastic toy or a large plastic container can be achieved through injection molding, with each part being virtually identical to the next.
Unrivaled Precision
One of the most remarkable aspects of injection molded parts is the precision they offer. Modern injection molding machines are equipped with advanced control systems that can maintain tight tolerances. Tolerances as low as ±0.001 inches can be achieved in many cases. This level of precision is crucial in industries like aerospace, where even the slightest deviation in a part’s dimensions can have catastrophic consequences. The use of high – quality molds and precise machinery ensures that injection molded parts meet the exact specifications required for a wide range of applications.
Material Diversity
Another strength of injection molding is the vast array of materials that can be used. Plastics are the most common, but the options include everything from commodity plastics like polyethylene and polypropylene to high – performance engineering plastics such as polycarbonate and nylon. Each material has its own unique properties, such as strength, heat resistance, and chemical resistance. For instance, in the medical industry, biocompatible plastics are used to create injection molded parts like syringes and medical devices, while in the automotive industry, heat – resistant plastics are chosen for under – the – hood components.
Wide – ranging Applications
Injection molded parts find their way into countless industries. In the automotive sector, they are used for interior components like dashboards, exterior parts like bumpers, and engine components. In the medical field, they are used to manufacture surgical instruments, prosthetics, and diagnostic equipment. The electronics industry relies on injection molded parts for enclosures, connectors, and small components in circuit boards. The versatility of injection molded parts makes them an essential part of these industries’ manufacturing processes.
Cost – effectiveness
When it comes to large – scale production, injection molding is highly cost – effective. Once the initial investment in the mold is made, the cost per part is relatively low. This is because the injection molding process is highly automated, allowing for high – volume production with minimal labor costs. Additionally, the ability to use a variety of materials means that manufacturers can choose the most cost – effective option without sacrificing quality. For example, a company producing millions of plastic consumer products can benefit greatly from the cost – savings offered by injection molding.
Process Innovations
The field of injection molding is constantly evolving. New technologies such as multi – shot injection molding, which allows for the combination of different materials in a single part, are emerging. Gas – assisted injection molding is another innovation that helps to create parts with complex geometries and reduced internal stress. These advancements not only improve the quality of injection molded parts but also open up new possibilities for product design.
Challenges and Solutions
Despite its many advantages, injection molding does face some challenges. Issues like warping, sink marks, and flash can occur during the molding process. However, with proper mold design, material selection, and process control, these problems can be mitigated. For example, using cooling channels in the mold to ensure even cooling can prevent warping, and adjusting the injection pressure can reduce the occurrence of flash.
Future Outlook
Looking ahead, the future of injection molded parts is bright. With the continued development of new materials and manufacturing technologies, injection molding will become even more precise, efficient, and versatile. We can expect to see injection molded parts being used in new and emerging industries, such as 3D printing support structures and advanced robotics components.
Conclusion
Injection molded parts truly represent precision engineering at its best. Their ability to offer high precision, material diversity, wide – ranging applications, cost – effectiveness, and continuous innovation makes them an indispensable part of modern manufacturing. Whether you’re an engineer, a manufacturer, or simply someone interested in the wonders of modern production, understanding injection molded parts is key to appreciating the complexity and ingenuity behind the products we use every day.