- March 3, 2025
- Posted by: feinuojixie
- Category: Injection Molding News
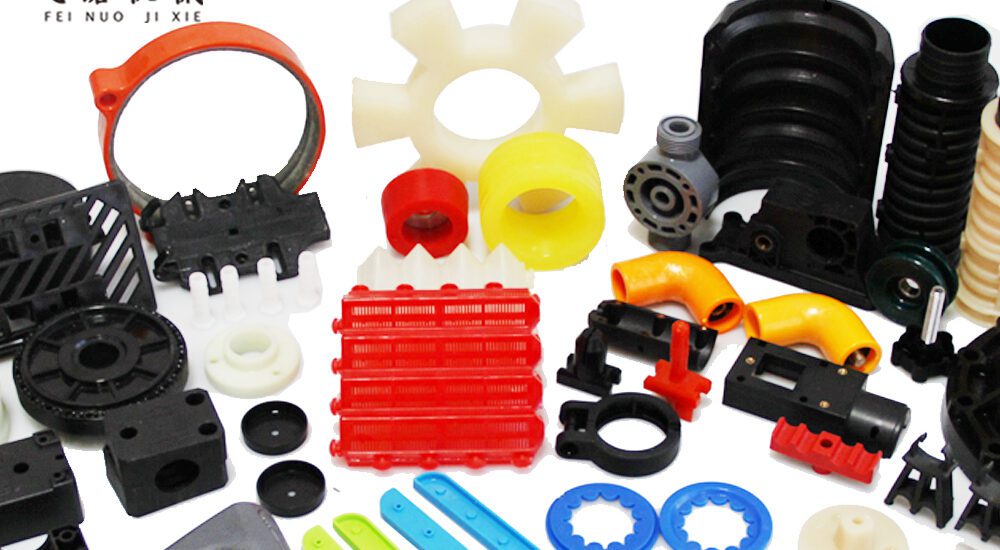
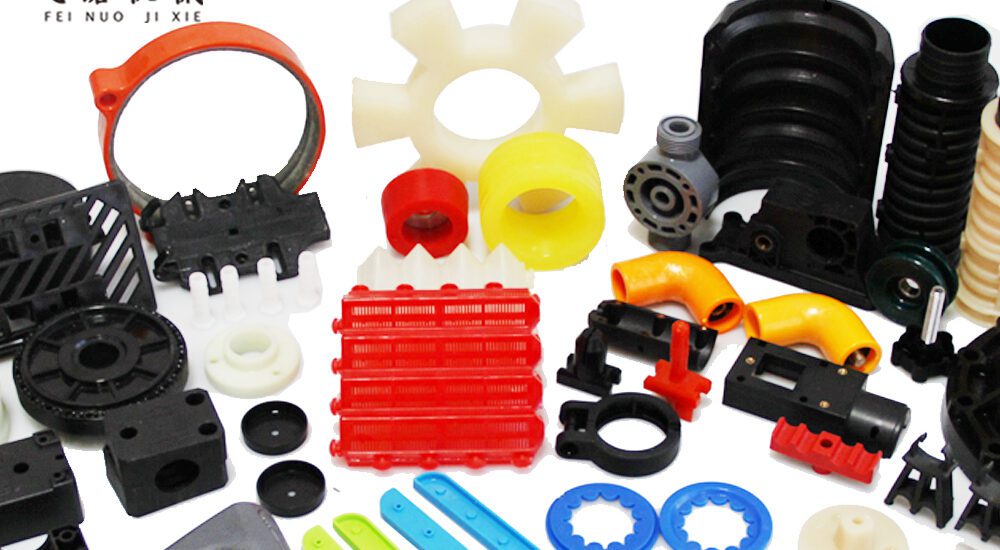
Injection molded part has revolutionized the manufacturing industry by offering a cost-effective and highly efficient production method. Whether in automotive, medical devices, electronics, or consumer goods, injection molding plays a critical role in producing precise and durable components at scale.
One of the key advantages of using injection molded part is its ability to streamline production while significantly reducing cost. Unlike traditional manufacturing techniques, injection molding enables mass production with minimal material waste, reduced labor, and optimized efficiency. As businesses continue to seek faster, more reliable, and budget-friendly manufacturing solutions, injection molded part remains the preferred choice for achieving these goals.
In this article, we will explore how injection molded part enhances production efficiency, lowers costs, and adapts to industry innovations. Understanding these aspects will help manufacturers make informed decisions and leverage the full potential of injection molding for their products.
Understanding Injection Molded Part and Its Manufacturing Process
Injection molded part is created through an advanced manufacturing process that involves injecting molten material into a pre-designed mold cavity. This method is widely used due to its precision, repeatability, and ability to produce complex shapes with minimal waste.
The process begins with material selection, where thermoplastics, thermosets, or elastomers are chosen based on the product’s requirements. The raw material is heated until it reaches a liquid state, then injected into a high-pressure mold. Once cooled and solidified, the part is ejected, inspected, and ready for use. This automated process ensures consistent quality and fast production, making injection molded part an essential component in many industries.
How Injection Molded Part Streamlines Production
One of the biggest advantages of injection molded part is its ability to streamline production. The process is highly efficient, allowing manufacturers to produce thousands or even millions of identical parts in a short time.
- Faster Production Cycles: Injection molding allows rapid manufacturing, significantly reducing lead times compared to traditional methods like machining or casting.
- Reduced Labor Costs: Since the process is highly automated, it requires minimal human intervention, lowering labor expenses while maintaining precision.
- Integration of Automation: Robotics and AI-driven systems further enhance efficiency by optimizing mold designs, reducing errors, and ensuring smooth operation.
With these benefits, manufacturers can produce high-quality injection molded part at a faster pace, meeting demand while maintaining consistent product quality.
Reducing Cost with Injection Molded Part
In addition to streamlining production, injection molded part also helps reduce overall manufacturing costs. Several factors contribute to its cost-effectiveness:
- Material Efficiency: The precision of injection molding minimizes material waste, ensuring that raw materials are utilized effectively.
- Lower Per-Unit Cost: The high-volume nature of injection molding means that the cost per part decreases as production increases, making it ideal for mass production.
- Energy Efficiency: Modern injection molding machines are designed to consume less energy, further reducing operational expenses.
By leveraging these advantages, businesses can achieve significant savings while maintaining high product quality and consistency.
Choosing the Right Material for Injection Molded Part
Selecting the right material is crucial to ensuring the performance and durability of injection molded part. Some common materials used in injection molding include:
- Thermoplastics: These materials, such as ABS, polycarbonate, and polypropylene, are highly versatile, durable, and recyclable.
- Thermosets: These are heat-resistant materials that provide excellent structural integrity but cannot be remelted after molding.
- Elastomers: Used for flexible and rubber-like parts, elastomers provide excellent shock absorption and resilience.
When choosing a material, manufacturers should consider factors such as strength, flexibility, cost, and environmental impact to ensure optimal performance.
Design Optimization for Injection Molded Part
Optimizing the design of injection molded part is essential for enhancing efficiency and reducing defects. A well-designed mold minimizes production issues and ensures consistent quality.
- Minimizing Defects: Proper mold design prevents warping, sink marks, and weak points, leading to higher product reliability.
- Reducing Material Usage: Techniques like ribbing and hollowing out unnecessary areas help lower material costs without compromising strength.
- Enhancing Durability: Reinforcing key structural areas ensures that parts remain strong and functional under various conditions.
By focusing on design optimization, manufacturers can maximize the benefits of injection molded part while maintaining superior product performance.
Innovations in Injection Molded Part Manufacturing
Advancements in technology continue to improve the efficiency and capabilities of injection molding. Some of the latest innovations include:
- Smart Manufacturing: Real-time monitoring and AI-driven adjustments improve quality control and reduce downtime.
- 3D Printing for Prototyping: Rapid prototyping with 3D printing allows manufacturers to test mold designs before full-scale production.
- Advanced Mold Materials: New high-performance mold coatings extend mold lifespan and improve production efficiency.
These innovations help manufacturers produce injection molded part faster, more efficiently, and with greater precision.
Common Challenges in Injection Molded Part Production and How to Overcome Them
Despite its advantages, injection molding comes with certain challenges that manufacturers must address to ensure optimal production.
- Warping and Shrinkage: These defects occur due to uneven cooling; proper mold design and material selection help minimize the risk.
- Sink Marks and Voids: Adjusting injection pressure and cooling rates can prevent these defects from affecting the final product.
- Quality Control Issues: Implementing rigorous testing and inspection procedures ensures consistent quality across all parts.
By identifying and resolving these challenges, manufacturers can maintain high production standards and maximize the benefits of injection molded part.
Future Trends in Injection Molded Part Industry
The future of injection molding is driven by technological advancements and sustainability efforts. Some key trends shaping the industry include:
- Sustainable Materials: The use of biodegradable and recycled materials is gaining popularity to reduce environmental impact.
- AI-Driven Manufacturing: Artificial intelligence helps optimize mold design, improve quality control, and enhance overall efficiency.
- Expansion into New Industries: From medical implants to aerospace components, injection molding continues to expand into new markets.
By staying ahead of these trends, manufacturers can ensure they remain competitive and innovative in the evolving landscape of injection molded part production.
Conclusion
Injection molded part plays a crucial role in modern manufacturing by streamlining production and reducing cost. Its efficiency, precision, and scalability make it an ideal solution for businesses looking to optimize their production processes.
By leveraging automation, material efficiency, and innovative design, manufacturers can produce high-quality injection molded part with minimal waste and lower costs. As technology continues to advance, the industry will see even greater improvements in sustainability, efficiency, and product innovation.