- February 28, 2025
- Posted by: feinuojixie
- Category: Injection Molding News
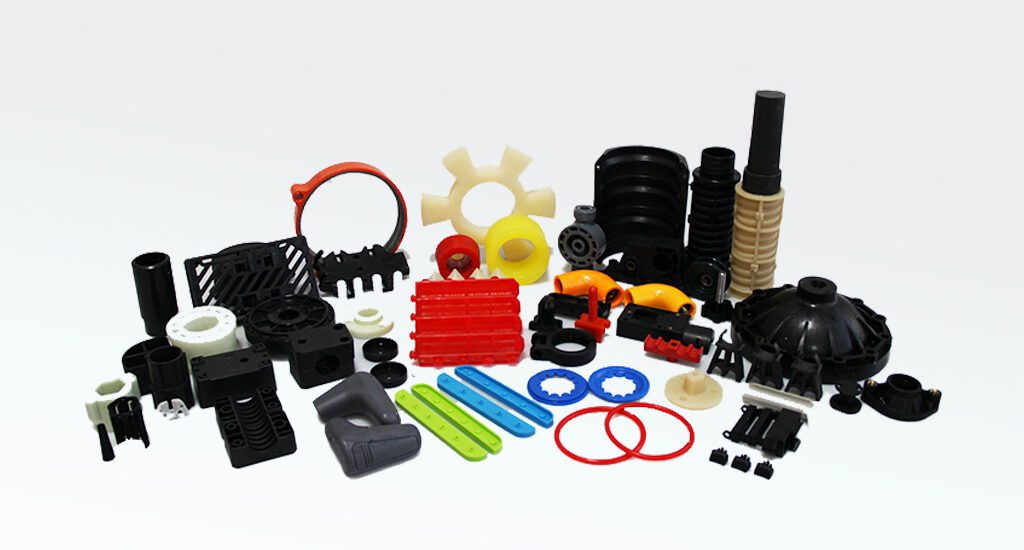
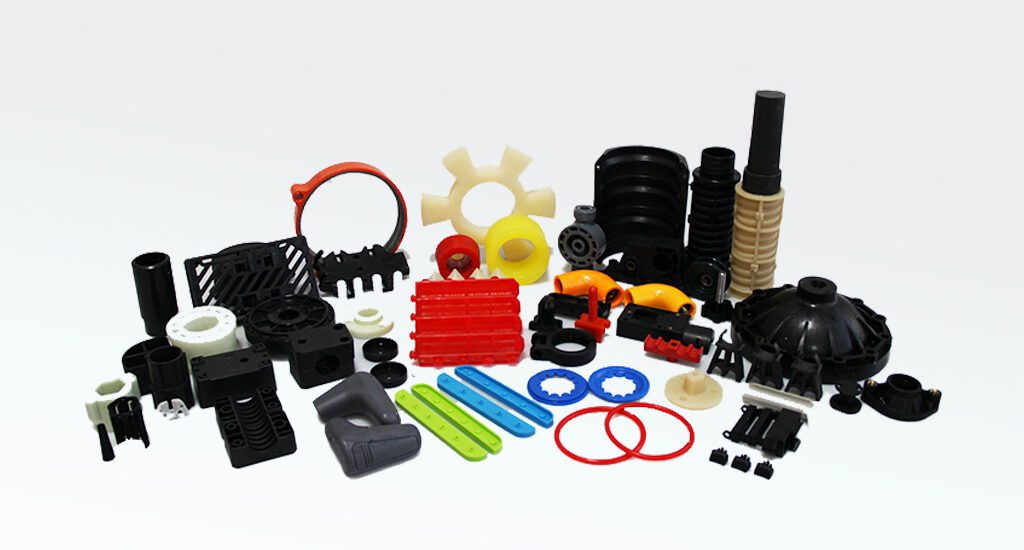
In today’s rapidly evolving manufacturing landscape, businesses are faced with numerous choices when it comes to production methods. Two primary options are injection molded parts and traditional manufacturing techniques. While traditional methods have served industries for years, injection molding has been increasingly adopted for its efficiency, cost-effectiveness, and design flexibility. But what makes injection molded parts a clear winner in many industries, and why are businesses choosing them over conventional approaches?
This article will explore the benefits and drawbacks of both methods, comparing them in terms of speed, cost, material choices, precision, and environmental impact. By the end, you’ll understand why injection molded parts are often the preferred choice for modern manufacturers and what this could mean for your business.
What Are Injection Molded Parts?
Injection molding is a highly versatile and widely used manufacturing process that involves injecting molten material (usually plastic) into a pre-designed mold to form a part. The material is then allowed to cool and solidify, taking the shape of the mold. This process allows for the mass production of parts with great accuracy and consistency.
Injection molded parts are commonly used in industries such as automotive, electronics, medical devices, consumer goods, and packaging. From plastic containers to intricate components in high-performance vehicles, injection molding plays a critical role in producing everything from simple to highly complex parts.
The Traditional Manufacturing Process: A Look Back
Traditional manufacturing methods include processes such as machining, casting, forging, and stamping. These techniques, while effective for certain applications, often require more manual labor, lead to higher material waste, and involve longer production times.
Machining, for example, involves removing material from a solid block to create the desired shape. While this method can be highly precise, it is typically slower and more costly, especially when producing large volumes. Similarly, casting and forging, though useful for making large or heavy parts, can be limited in terms of the shapes and sizes they can produce.
These traditional processes have their place, particularly for specific types of parts, but their inherent limitations make them less suitable for the demands of modern, large-scale manufacturing.
Efficiency: Speed and Cost
One of the most significant advantages of injection molded parts over traditional manufacturing is efficiency. The injection molding process is designed for high-speed mass production, making it ideal for producing large quantities of parts in a short amount of time. This speed translates into lower production costs, especially when running high volumes.
Traditional manufacturing methods, on the other hand, can be more time-consuming and labor-intensive. Machining, for instance, can take longer to produce each part, especially when complex designs are involved. As a result, the cost per unit tends to be higher for small and large production runs compared to injection molding, which offers greater efficiency through automation.
Design Flexibility and Complexity
Injection molding offers a level of design flexibility that traditional manufacturing struggles to match. Complex geometries, intricate details, and multi-functional components can be produced with ease through injection molding. This is because the mold used in the injection process can be designed with fine details, allowing manufacturers to create highly sophisticated parts that would be difficult or impossible to achieve with traditional methods.
In contrast, traditional manufacturing techniques such as casting or machining often face limitations when it comes to producing highly detailed or intricate designs. Machining, for example, may struggle with producing parts that have undercuts or complex internal features without adding substantial costs or time.
Material Variety and Strength: Injection Molded Part vs. Traditional Materials
Injection molding is compatible with a wide range of materials, including various types of plastics, metals, and composites. These materials can be tailored to meet specific performance requirements, such as strength, flexibility, and heat resistance. Injection molded parts are often used for high-performance applications, where material properties such as impact resistance and chemical stability are critical.
Traditional manufacturing also uses a variety of materials, but the range of available options may not be as extensive, particularly when considering the versatility of plastics in injection molding. For industries that require materials with specific properties, injection molding can offer a greater variety of options.
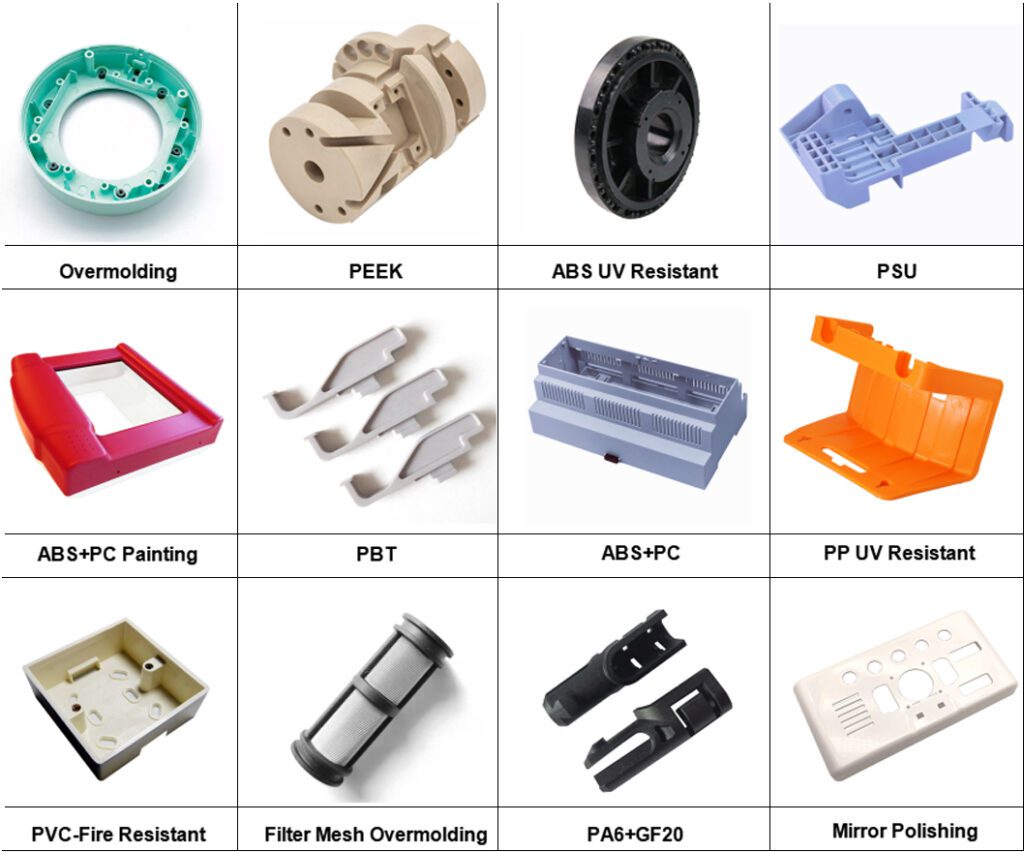
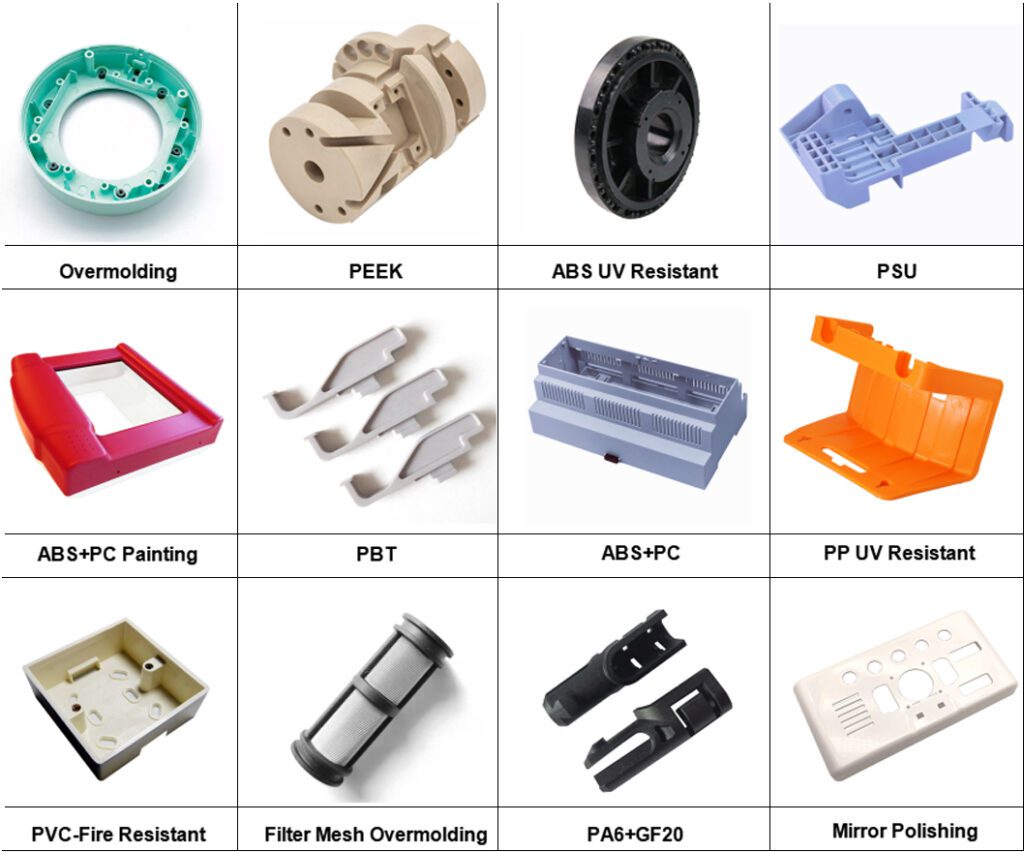
Precision and Quality Control: A Close Look
Precision is one of the standout advantages of injection molding. The process allows for tight tolerances and high consistency, ensuring that each part produced is virtually identical to the last. This level of precision is critical in industries like aerospace, automotive, and medical devices, where parts must meet stringent specifications.
Traditional manufacturing methods, while capable of producing precise parts, often struggle to maintain this level of consistency, particularly when producing large volumes. Variations in material properties, human error, and the limitations of older machinery can affect the overall quality of the product, leading to higher scrap rates and rework.
Environmental Impact: Sustainability Considerations
In an era of increasing environmental awareness, sustainability is becoming a key factor in manufacturing decisions. Injection molding has several environmental benefits, including reduced material waste. The injection process is highly efficient, with minimal excess material. Additionally, many injection-molded parts can be made from recyclable materials, making them more sustainable.
Traditional manufacturing methods, on the other hand, often result in more material waste. For example, machining processes generate significant amounts of scrap material, which can be costly to dispose of. Additionally, some traditional methods, such as casting, may require more energy and generate higher levels of emissions.
Cost-Effectiveness for Small and Large Batches
One of the misconceptions about injection molding is that it’s only cost-effective for large production runs. While it’s true that injection molding is ideal for mass production, it can also be a cost-effective solution for small batch production, particularly when the part design is already established.
Traditional manufacturing methods, however, often struggle with the cost efficiency of small batches. The setup time for machining, casting, or forging processes can make them prohibitively expensive for low-volume production. Injection molding, with its ability to quickly produce parts once the mold is created, provides flexibility for both small and large production runs.
The Future of Manufacturing: Trends and Advancements in Injection Molding
As technology continues to advance, the injection molding process is also evolving. New innovations such as 3D injection molding and smart molding technologies are making it possible to produce even more complex parts with greater efficiency and reduced costs. The integration of automation, artificial intelligence, and advanced material science is also pushing the boundaries of what injection molded parts can achieve.
Traditional manufacturing methods, while still valuable in some contexts, are unlikely to keep pace with these advancements. As industries demand more complex, cost-effective, and sustainable solutions, injection molding is poised to dominate the manufacturing sector.
Why Injection Molded Parts are a Clear Winner
When it comes to efficiency, precision, material versatility, and sustainability, injection molded parts clearly outperform traditional manufacturing techniques in many industries. The ability to produce complex designs at high volumes with minimal waste makes injection molding the go-to method for modern manufacturing. Businesses looking to stay competitive in an increasingly demanding marketplace should seriously consider transitioning to injection molded parts to meet the needs of their customers and clients.