- April 17, 2025
- Posted by: feinuojixie
- Category: Injection Molding News
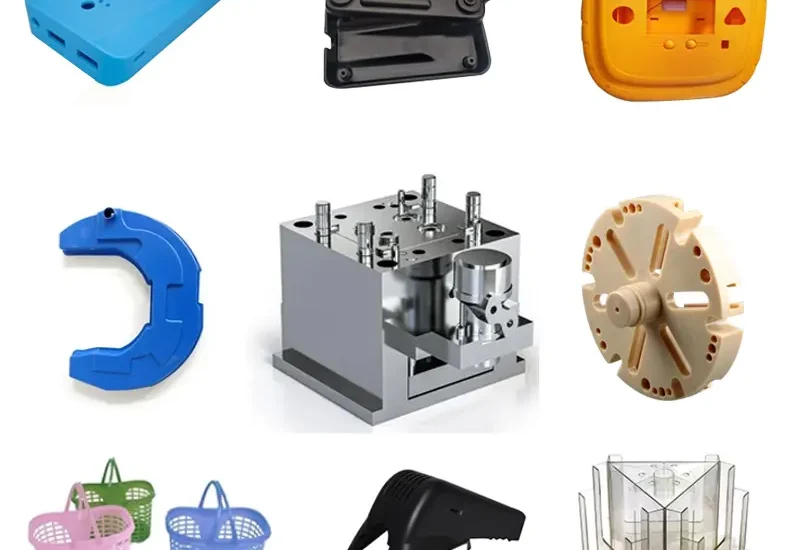
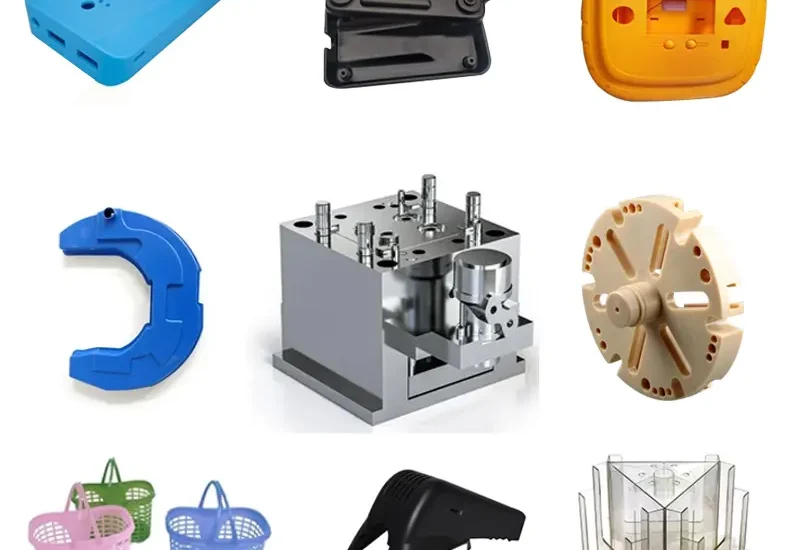
When you pick up your smartphone, drive your car, or open a kitchen appliance, chances are you’re interacting with something made using an injection molding part. These components are found in nearly every modern product, often hidden from view, but absolutely essential to function and form. The reason is simple: injection molding delivers unmatched precision, cost-efficiency, and scalability. Whether it’s a lightweight housing, a structural bracket, or a detailed connector, injection molding parts make it possible to mass-produce complex components with extraordinary consistency. As industries continue to demand faster production times, higher quality, and smarter designs, the importance of injection molding parts only grows. In this article, we break down exactly what makes these parts so indispensable and explore the impact they have across the manufacturing world.
What Is an Injection Molding Part?
An injection molding part is a component manufactured by injecting molten material—usually plastic—into a precisely machined mold cavity. Once cooled and solidified, the part is ejected, perfectly shaped according to the mold design. This method enables the creation of intricate, durable parts at high volumes with minimal post-processing. Materials used often include thermoplastics like ABS, polycarbonate, and nylon, though specialized polymers and even metal powders (in metal injection molding) are sometimes utilized. The versatility of the process makes injection molding parts ideal for applications that require both strength and precision.
Why Injection Molding Parts Are Key to Product Success
In any product, the quality of its components directly affects the overall performance and longevity. Injection molding parts deliver exceptional uniformity, which ensures every unit performs identically. This is vital for industries where reliability is non-negotiable, such as aerospace or medical devices. Moreover, these parts can be produced with extremely tight tolerances and complex geometries, which may be impossible or cost-prohibitive with other manufacturing methods. Their structural integrity and finish quality help reduce failures, improve customer satisfaction, and maintain brand reputation.
Design Considerations That Define a Great Injection Molding Part
Crafting a high-performing injection molding part starts at the design stage. Factors like uniform wall thickness help avoid warping and sink marks, while adding draft angles ensures smooth ejection from the mold. Features such as ribs and bosses provide structural strength without increasing material usage. Gating and runner systems must also be optimized to control how the material flows, ensuring the part fills completely without air pockets or short shots. A well-designed part not only functions better but also lowers manufacturing costs and cycle time.
Industries That Rely Heavily on Injection Molding Parts
Injection molding parts are vital across a wide spectrum of industries. In automotive, they’re used in dashboards, bumpers, and under-the-hood components. In healthcare, they form critical parts like syringe bodies, surgical tools, and casings for medical devices. Consumer electronics depend on them for precision housing, buttons, and connectors. Even aerospace companies use them for lightweight, durable interior parts. These parts are the common thread that connects high-tech innovation with practical functionality in nearly every sector.
Benefits of Using Injection Molding Parts in Mass Production
One of the standout advantages of using injection molding parts is scalability. Once the mold is created, thousands—or even millions—of parts can be produced with consistent quality and minimal human intervention. The cycle time for each part is incredibly short, often just seconds, making it ideal for mass production. The process also generates little waste, as excess material can often be reground and reused. This efficiency leads to lower per-unit costs, making injection molding a go-to choice for companies seeking speed without compromising quality.
Customization and Innovation in Modern Injection Molding Parts
Today’s injection molding technology goes far beyond standard shapes and simple parts. Engineers can now simulate flow dynamics before tooling begins, ensuring the part will mold perfectly under real-world conditions. Advanced materials like glass-filled polymers, flame-retardant resins, and even bio-based plastics allow for tailored performance. Custom textures, transparency levels, and color matching further elevate product appearance and branding. The result? Injection molding parts that are not only functional but also highly innovative and market-ready.
Common Challenges and How to Overcome Them
Despite its many strengths, the injection molding process is not without challenges. Warping can occur if cooling is uneven or if material flow is unbalanced. Sink marks result from thick sections cooling at different rates. Flash happens when molten material escapes the mold cavity. These issues can affect part quality and usability. However, most problems are preventable with proper mold design, material selection, and machine calibration. Working with experienced mold designers and process engineers is key to overcoming these hurdles and achieving high-quality results.
Sustainability and the Future of Injection Molding Parts
Sustainability is increasingly influencing how injection molding parts are produced. Manufacturers are now incorporating recyclable and biodegradable plastics, using energy-efficient machinery, and implementing closed-loop systems to reduce material waste. Some companies also offer take-back programs for plastic components, turning end-of-life parts into raw materials for new ones. As environmental responsibility becomes a competitive edge, injection molding is evolving to meet both performance and sustainability goals.
Conclusion: Small Parts, Big Impact
Injection molding parts might be small in size, but their impact on modern manufacturing is enormous. They enable innovation, drive cost efficiencies, and deliver the reliability that today’s industries demand. From the tiniest gear in a watch to the structural panel in an automobile, these parts power products that shape our daily lives. As materials and technology continue to advance, the role of injection molding parts will only grow—offering more possibilities, better performance, and smarter design for the future.