- May 1, 2025
- Posted by: feinuojixie
- Category: Injection Molding News
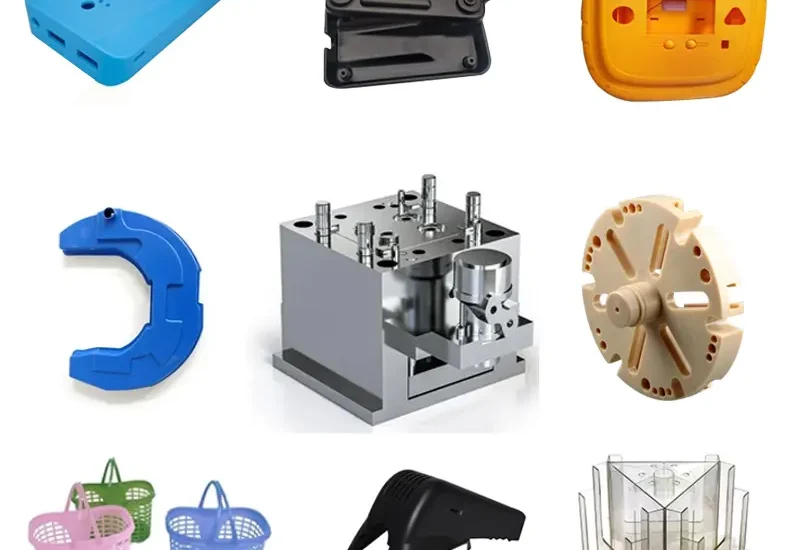
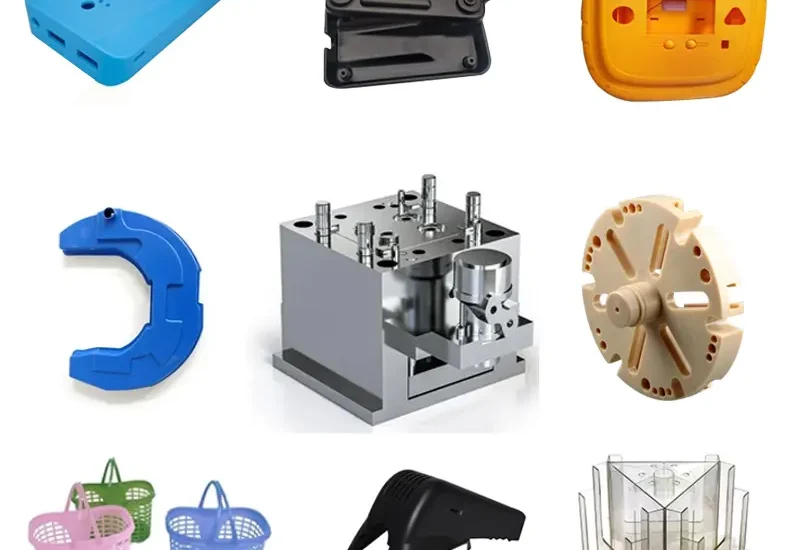
In the fast-paced world of automotive manufacturing, the pressure to innovate is stronger than ever. Automakers are constantly seeking methods that reduce costs, accelerate production, and improve the quality of vehicle components. Among the many manufacturing strategies, two approaches dominate the conversation: injection molding automotive parts and traditional manufacturing techniques. While traditional methods such as casting and machining have served the industry for decades, injection molding is rapidly gaining traction as a modern alternative. This article explores how these two approaches compare—and which one is better suited to meet the evolving demands of today’s automotive industry.
Understanding Injection Molding for Automotive Parts
Injection molding is a manufacturing process that involves injecting molten material into a mold to form complex shapes with high precision. In the context of automotive production, this method is commonly used to create lightweight, durable plastic parts such as dashboards, bumpers, and interior panels. The process is highly repeatable, making it ideal for large-scale production. One of the key advantages of injection molding automotive parts is its ability to maintain tight tolerances while offering design flexibility and material efficiency.
Traditional Manufacturing in the Automotive Industry
Traditional manufacturing refers to time-tested processes like casting, forging, stamping, and machining. These methods have been the backbone of automotive production since the industry’s inception. Cast iron engine blocks, machined brake rotors, and forged suspension arms are examples of parts typically made through conventional means. These techniques are well-suited for metal components that demand high strength and wear resistance. However, traditional methods often involve longer production cycles, higher labor costs, and more complex tooling requirements.
Material Considerations: Plastics vs Metals
A major distinction between injection molding and traditional manufacturing lies in the materials used. Injection molding automotive parts typically rely on engineering-grade plastics such as ABS, polycarbonate, and nylon. These materials offer excellent chemical resistance, weight reduction, and design versatility. On the other hand, traditional processes often use metals like aluminum, steel, and cast iron, known for their structural integrity and durability. While metals may be preferred for high-stress applications, plastics are increasingly used for components where weight savings and corrosion resistance are critical.
Design Flexibility and Complexity
Injection molding excels in producing parts with intricate geometries and integrated features. Automotive designers can incorporate clips, ribs, and undercuts into a single molded component without the need for secondary assembly. This capability reduces both assembly time and part count. Traditional manufacturing, by contrast, can struggle with highly complex designs, often requiring multiple steps or additional machining. For this reason, injection molding automotive parts offer greater creative freedom in both function and aesthetics.
Production Efficiency and Time-to-Market
One of the standout benefits of injection molding is its speed. Once the mold is created, parts can be produced in seconds, allowing for rapid scaling. This efficiency makes it ideal for high-volume production runs commonly seen in the automotive industry. Traditional manufacturing methods, although effective for certain applications, usually involve longer cycle times and more setup complexity. The time-to-market advantage of injection molding automotive parts can be a decisive factor in competitive markets where speed matters.
Cost Analysis: Initial vs Long-Term Expenses
Injection molding does require significant upfront investment in mold tooling, which can be costly and time-consuming to produce. However, the long-term benefits include low per-unit costs and minimal material waste. For large production volumes, this makes injection molding a cost-effective choice. Traditional methods may offer lower initial costs, especially for prototyping or short runs, but often incur higher labor and material expenses over time. The overall cost efficiency of injection molding becomes more apparent as production scales.
Durability and Performance in Automotive Use
When it comes to durability, injection molding automotive parts are engineered to withstand the demands of modern vehicles. Advanced polymers can resist high temperatures, UV exposure, and chemical corrosion. While traditional metal parts still dominate in areas requiring extreme strength—like powertrain components or chassis elements—plastics are proving sufficient for many structural and cosmetic applications. The right material selection ensures that molded parts perform reliably over the vehicle’s lifespan.
Sustainability and Environmental Impact
Sustainability is an increasingly important factor in manufacturing decisions. Injection molding supports greener practices through the use of recyclable plastics and energy-efficient machines. Some manufacturers are also exploring bio-based polymers for automotive parts. In contrast, traditional metalworking processes are generally more energy-intensive and produce more waste byproducts. Injection molding automotive parts can contribute to a lower carbon footprint when optimized for recycling and energy use.
Case Studies: Industry Use of Injection Molding Automotive Parts
Major automotive brands are turning to injection molding for both cost and performance advantages. For example, companies like Toyota and BMW have adopted molded plastic fuel system components and under-the-hood brackets to reduce weight and improve fuel efficiency. Tesla uses large-scale injection molding to produce body components, streamlining production and reducing part count. These real-world applications demonstrate the practicality and innovation possible with injection molding automotive parts.
When Traditional Manufacturing Still Wins
Despite its advantages, injection molding is not always the ideal solution. Traditional manufacturing still plays a crucial role in areas requiring ultra-high strength or specialized alloys. For example, crankshafts, engine blocks, and heavy-duty suspension parts are better suited to casting and forging. Additionally, for low-volume or custom parts, traditional methods may be more practical due to the high cost of mold development.
Choosing the Right Method for the Right Part
There is no one-size-fits-all solution in automotive manufacturing. The decision between injection molding automotive parts and traditional manufacturing depends on multiple factors: material needs, production volume, complexity, and performance requirements. Injection molding offers unparalleled efficiency and design freedom for many plastic components, while traditional methods retain their value in high-strength metal parts. As automotive design continues to evolve, combining both methods strategically will be key to driving innovation, performance, and sustainability.