- March 5, 2025
- Posted by: feinuojixie
- Category: Injection Molding News
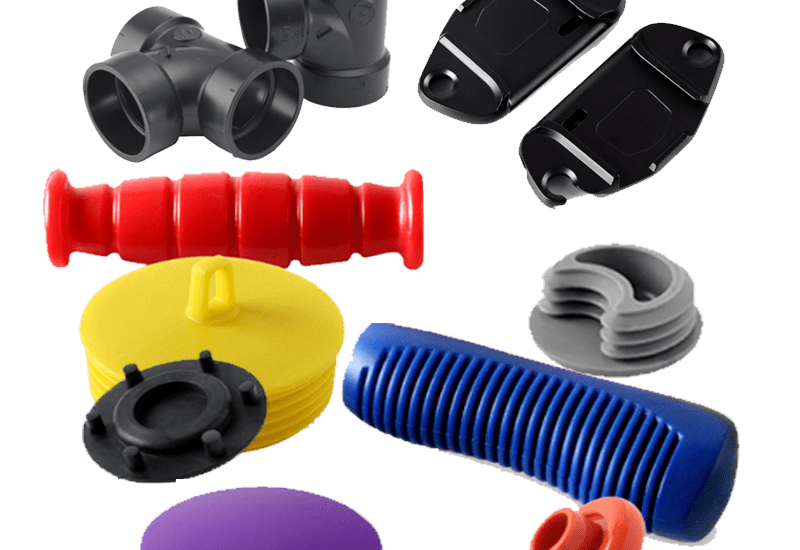
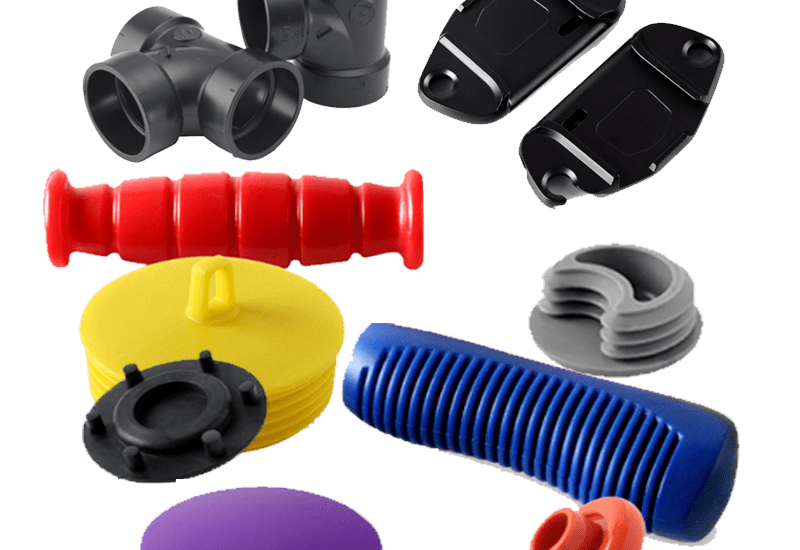
Injection moulding is a widely used manufacturing process that involves injecting molten plastic into a mould to form parts with precise shapes and sizes. It is essential for producing high-quality plastic parts across various industries, including automotive, electronics, and consumer goods. The method ensures high efficiency, repeatability, and versatility, making it one of the preferred techniques for large-scale plastic production. Whether you’re looking to create a small batch or a high-volume production run, understanding the importance and advantages of injection moulding is crucial to streamlining production processes.
Understanding the Injection Moulding Process: A Step-by-Step Breakdown
The injection moulding process consists of several distinct stages that ensure a seamless production of plastic parts. The process begins with the preparation of raw material, typically in the form of plastic pellets. These pellets are heated in an injection moulding machine until they become molten, allowing them to be injected into a custom-designed mould under high pressure. The molten plastic is then allowed to cool and solidify inside the mould before being ejected as a finished plastic part.
Key equipment in injection moulding includes the injection unit, which melts and injects the plastic, and the clamping unit, which holds the mould in place during injection. Depending on the size and complexity of the part being produced, multiple injection points may be used to ensure uniform distribution of molten plastic. Additionally, various materials can be used in injection moulding, including thermoplastics, thermosets, and elastomers, depending on the desired properties of the finished part.
The Benefits of Injection Moulding for Plastic Part Production
One of the primary reasons injection moulding is preferred for plastic part production is its efficiency and speed. Once the mould is created, the process can produce large quantities of parts quickly, making it ideal for mass production. The ability to produce high volumes of plastic parts with consistent quality ensures that manufacturers can meet tight deadlines and lower production costs.
In addition to cost-effectiveness, injection moulding offers precise control over part dimensions, enabling manufacturers to produce complex shapes with high accuracy. This precision ensures the parts fit perfectly and meet the required specifications without the need for further finishing or assembly. Another benefit is its versatility—whether the part requires intricate details or simple shapes, injection moulding can accommodate a wide variety of designs and material types.
Factors to Consider When Designing Plastic Parts for Injection Moulding
The design of a plastic part plays a crucial role in the success of the injection moulding process. Several factors should be considered during the design phase to ensure the parts are manufacturable and meet the desired performance standards. For instance, the inclusion of draft angles is essential to allow easy ejection of the part from the mould. Without these angles, the part may become stuck in the mould, leading to production delays.
Wall thickness is another important factor. Parts with uniform wall thickness are easier to mould and less prone to defects such as warping or sink marks. Uneven wall thickness can result in stress concentrations, causing the part to deform during cooling. Additionally, the overall geometry of the part should be designed to optimize the flow of molten plastic and prevent defects like short shots or air traps.
Material selection is also critical in determining the final performance of the part. Different materials have varying properties, such as flexibility, heat resistance, and strength. It’s essential to choose a material that aligns with the functional requirements of the part while also being compatible with the injection moulding process.
Common Challenges in Injection Moulding and How to Overcome Them
While injection moulding is highly efficient, it does come with its share of challenges. Common issues include warping, sink marks, surface defects, and short shots. Warping occurs when a part cools unevenly, causing it to deform. Sink marks, on the other hand, are depressions on the surface of the part caused by uneven cooling of thicker sections. These problems can be minimized by carefully controlling the cooling rate and adjusting the mould design.
Surface defects, such as scratches or discoloration, can occur due to poor mould conditions or improper material handling. Ensuring the mould is clean and properly maintained, along with using high-quality materials, can help reduce these issues. In cases where short shots occur, it’s often due to insufficient molten plastic being injected into the mould. This can be avoided by adjusting injection pressure or modifying the mould design.
Technological advancements, such as the use of simulation software to predict and address issues before production, can help manufacturers identify and resolve potential problems early in the process. Additionally, advancements in monitoring systems, like sensors and cameras, allow for real-time inspection of the production process to prevent defects before they occur.
Choosing the Right Injection Moulding Equipment for Your Plastic Part Production
Selecting the right injection moulding equipment is essential to ensuring the efficiency and success of the production process. There are several types of injection moulding machines, including hydraulic, electric, and hybrid models. Hydraulic machines are widely used for large parts that require high clamping forces, while electric machines offer high precision and energy efficiency, making them ideal for smaller parts and complex geometries.
When choosing a machine, manufacturers need to consider the size, complexity, and material requirements of the parts being produced. The injection unit must be capable of melting and injecting the plastic effectively, while the clamping unit should be able to handle the force required to hold the mould together during the injection process. Key features to look for in an injection moulding machine include precision controls, fast cycle times, and the ability to handle multiple material types.
Injection Moulding vs Other Plastic Manufacturing Techniques: Why It’s a Preferred Choice
While there are several other plastic manufacturing methods available, injection moulding is often the preferred choice due to its efficiency, flexibility, and ability to produce complex parts. Compared to extrusion, which is limited to creating simple shapes like tubes or sheets, injection moulding can produce intricate and detailed plastic parts in a wide range of shapes and sizes.
Thermoforming, another alternative, involves heating a plastic sheet until it becomes pliable and then forming it into a mould. While thermoforming is useful for producing larger parts, it lacks the precision and complexity of injection moulding. For high-volume, high-precision plastic part production, injection moulding stands out as the most effective method.
Future of Injection Moulding in Plastic Part Production: Trends and Innovations
The future of injection moulding is filled with exciting innovations and trends that will shape the industry. Automation and artificial intelligence (AI) are becoming increasingly integrated into the injection moulding process, allowing for more precise control over the production cycle. These technologies enable manufacturers to identify potential issues early and make real-time adjustments, improving overall efficiency and reducing downtime.
Sustainability is also a growing focus in the injection moulding industry. Manufacturers are looking for ways to reduce waste and minimize energy consumption during production. The use of recycled plastics and bio-based materials is on the rise, helping to create more eco-friendly plastic parts without compromising on performance. Additionally, advancements in 3D printing are allowing for the rapid prototyping of injection moulds, speeding up the design phase and reducing time-to-market.
How Injection Moulding Plastic Part Production Can Streamline Your Manufacturing Process
Injection moulding offers unmatched advantages in terms of speed, cost-effectiveness, and precision. By choosing the right equipment, designing parts for optimal manufacturability, and addressing common challenges, manufacturers can streamline their production processes and deliver high-quality plastic parts at scale. As the industry continues to evolve with new technologies and sustainable practices, injection moulding remains a cornerstone of modern manufacturing. Whether you’re producing a small batch or mass-producing parts, injection moulding can provide the reliability and efficiency needed to stay competitive in today’s market.