- March 26, 2025
- Posted by: feinuojixie
- Category: Injection Molding News
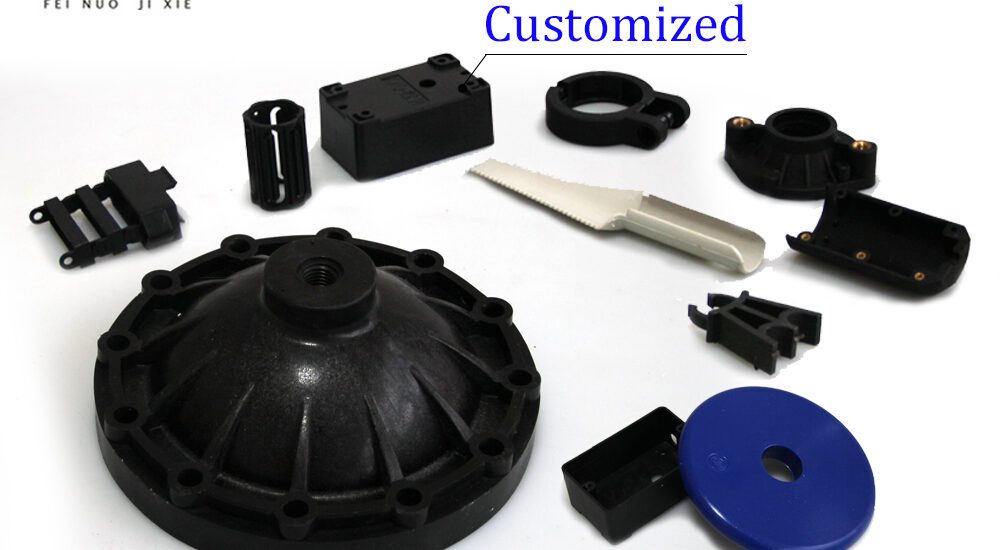
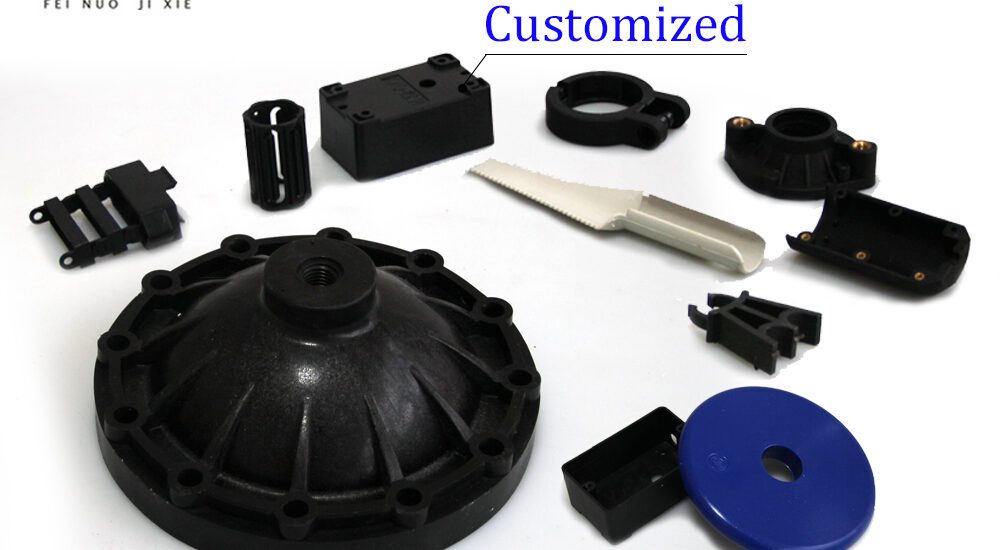
ABS injection moulding has long been a cornerstone of plastic manufacturing, providing industries with a durable, cost-effective, and versatile solution for producing high-quality plastic components. Acrylonitrile Butadiene Styrene (ABS) is widely used across industries such as automotive, consumer electronics, medical devices, and construction due to its excellent impact resistance, high rigidity, and smooth surface finish.
As demand for precision-engineered plastics continues to rise, manufacturers are exploring new innovations in ABS injection moulding to enhance efficiency, sustainability, and product performance. From advanced material formulations to cutting-edge moulding technologies, the industry is witnessing rapid transformation. This article explores the latest developments in ABS injection moulding and what the future holds for plastic manufacturing.
The Evolution of ABS Injection Moulding
ABS injection moulding has undergone significant advancements since its inception, enabling manufacturers to produce complex and highly durable plastic parts with improved efficiency.
-
Early Applications in Manufacturing
ABS was first introduced in the mid-20th century and quickly gained popularity due to its unique balance of strength, flexibility, and ease of processing. Early applications included automotive interior components, telephone casings, and household appliances. -
Technological Improvements Enhancing Production
Over the years, the adoption of computer-aided design (CAD) and computer-aided manufacturing (CAM) has significantly improved mould precision, reducing material waste and enhancing product consistency. The introduction of high-speed injection moulding machines has also accelerated production cycles, allowing manufacturers to meet growing consumer demands. -
Key Benefits of ABS in Injection Moulding
One of the primary reasons ABS remains a preferred material is its outstanding mechanical properties. It offers high impact resistance, good chemical stability, and the ability to withstand varying environmental conditions. Additionally, ABS injection moulding allows for seamless colour customisation, making it ideal for aesthetic and functional applications.
Advanced Materials in ABS Injection Moulding
Material innovation is at the forefront of the ABS injection moulding industry, with researchers developing new ABS formulations to enhance performance and sustainability.
-
High-Performance ABS Compounds
Manufacturers are incorporating additives such as glass fibres and flame retardants to improve ABS’s strength, thermal stability, and resistance to UV degradation. These advanced compounds enable ABS injection moulding to be used in demanding applications such as aerospace and medical equipment. -
Sustainable and Bio-Based ABS Alternatives
As environmental concerns grow, the industry is shifting toward sustainable solutions. Bio-based ABS blends derived from renewable resources are gaining traction, offering reduced carbon footprints without compromising performance. Additionally, recycled ABS is being integrated into production processes to minimise plastic waste and promote a circular economy.
Cutting-Edge Moulding Technologies
Technological advancements are revolutionising ABS injection moulding, enabling manufacturers to achieve higher precision, efficiency, and cost-effectiveness.
-
Automation and AI-Driven Optimisation
The integration of robotics and artificial intelligence (AI) in ABS injection moulding is streamlining production by automating repetitive tasks, minimising errors, and optimising material usage. Smart sensors and real-time monitoring systems enhance process control, ensuring consistent quality. -
Precision Control Systems
Innovations in mould temperature regulation and pressure control are reducing defects such as warping, shrinkage, and surface imperfections. This allows for the production of intricate and dimensionally stable parts with greater accuracy. -
Hybrid and Multi-Material Moulding
New hybrid moulding techniques enable manufacturers to combine ABS with other polymers or materials such as metal inserts, expanding design possibilities for multi-functional products. This approach is particularly beneficial for electronic housings and automotive components that require both structural integrity and lightweight properties.
Sustainability in ABS Injection Moulding
Sustainability has become a top priority in modern plastic manufacturing, driving significant advancements in eco-friendly ABS injection moulding processes.
-
Incorporation of Recycled ABS
Many manufacturers are incorporating post-consumer and post-industrial recycled ABS into their production cycles, reducing reliance on virgin plastics. This not only lowers manufacturing costs but also contributes to global sustainability initiatives. -
Energy-Efficient Moulding Processes
The introduction of energy-efficient servo-driven injection moulding machines has significantly reduced power consumption. Advanced heating and cooling systems optimise cycle times, further decreasing energy waste. -
Circular Economy Approaches
Companies are exploring closed-loop recycling systems where end-of-life ABS products are collected, reprocessed, and reintegrated into new products. This model ensures sustainable material use while reducing landfill waste.
Industry Applications and Future Trends
ABS injection moulding is playing a pivotal role in various industries, with future trends shaping its ongoing evolution.
-
Automotive Industry
The demand for lightweight, impact-resistant materials has led to increased use of ABS in vehicle interiors, dashboards, and exterior trim components. Electric vehicle (EV) manufacturers are also leveraging advanced ABS formulations to improve battery housing designs. -
Consumer Electronics
ABS injection moulding is widely used for producing durable casings for smartphones, laptops, and gaming consoles. With the rise of smart devices, manufacturers are focusing on electrostatic discharge (ESD)-safe ABS materials to protect sensitive electronic components. -
Medical and Healthcare Innovations
The medical sector is adopting ABS for applications such as diagnostic device housings, surgical instruments, and protective equipment due to its biocompatibility and easy sterilisation. Future advancements may include antimicrobial ABS formulations to enhance patient safety. -
Industry 4.0 and Smart Manufacturing
The integration of IoT and data analytics is transforming ABS injection moulding into a more intelligent and connected process. Predictive maintenance, automated quality control, and real-time production monitoring are set to define the next era of plastic manufacturing.
Conclusion
The landscape of ABS injection moulding is evolving rapidly, driven by advancements in material science, automation, and sustainability. From high-performance ABS compounds to AI-driven production enhancements, the industry is pushing the boundaries of what plastic manufacturing can achieve.
As consumer demands shift towards more eco-friendly and high-precision solutions, manufacturers must continue to embrace innovation to stay competitive. With the integration of recycled materials, smart technologies, and energy-efficient processes, ABS injection moulding is poised to remain a vital component of the future of plastic manufacturing.