- May 6, 2025
- Posted by: feinuojixie
- Category: Injection Molding News
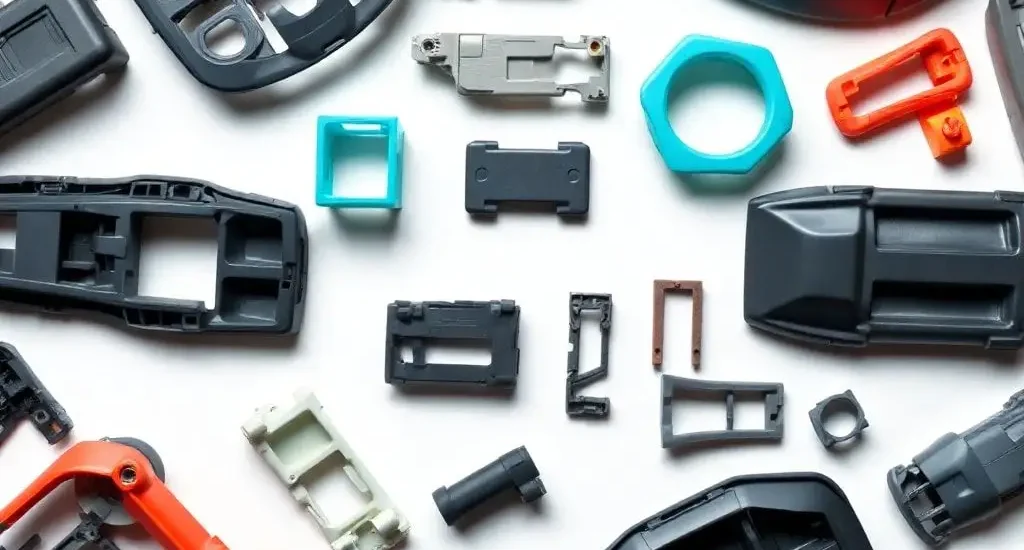
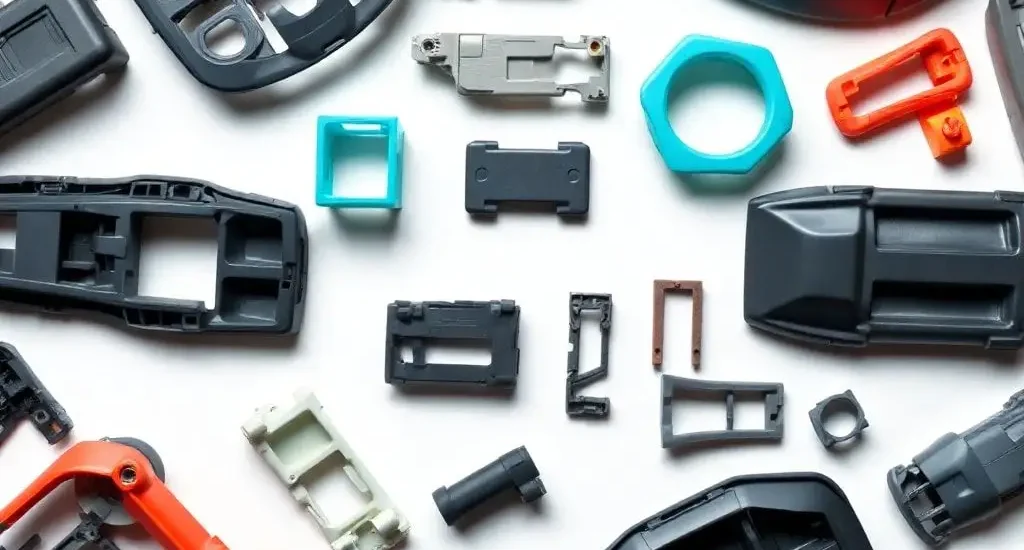
In today’s competitive manufacturing environment, businesses are constantly searching for ways to enhance production efficiency and reduce costs—without compromising quality. Large part injection molding has emerged as a compelling solution for companies that require robust, precise, and high-volume production of sizable plastic components. From automotive bumpers to industrial containers, the demand for larger, more complex parts continues to rise. This method not only enables streamlined manufacturing but also minimizes the need for assembly by producing fully integrated parts in a single mold cycle. As industries seek scalable and reliable production options, large part injection molding stands out as a strategic choice worth exploring.
What Is Large Part Injection Molding? A Beginner’s Overview
Large part injection molding is a specialized manufacturing process used to produce oversized plastic components through high-pressure injection of molten resin into custom-designed molds. Unlike conventional injection molding that focuses on smaller items, this method is designed to handle parts that are physically large or have high structural requirements. These parts often range from automotive panels to pallets and structural enclosures. The core principle remains the same—inject, cool, and eject—but the scale, machinery, and tooling involved are significantly larger and more complex.
Key Industries Benefiting from Large Part Injection Molding
Multiple industries are leveraging the strengths of large part injection molding to achieve efficient production and superior part performance. The automotive sector uses it to manufacture dashboards, bumpers, and grilles. The logistics industry benefits from molded pallets and containers that are durable yet lightweight. Agricultural equipment makers use it for housing parts and panels that must endure harsh outdoor conditions. Even construction and infrastructure projects rely on molded components for drainage systems and modular structures. These sectors value the method’s ability to deliver consistent quality at scale.
The Advantages of Large Part Injection Molding for Business Efficiency
Businesses adopting large part injection molding enjoy several key advantages. First, the process allows the production of large, single-piece parts that reduce or eliminate the need for assembly, saving labor and minimizing error. Second, it supports high-volume manufacturing, which drives down per-unit costs over time. Third, molded parts typically have excellent dimensional stability and strength, especially when engineered resins are used. Finally, the process provides great flexibility in terms of design complexity, enabling the creation of integrated features like ribs, bosses, and snap fits directly in the mold.
Design Considerations for Large Part Injection Molding
Successful large part injection molding begins with thoughtful part and mold design. Designers must pay special attention to wall thickness uniformity to avoid warping or sink marks. Proper draft angles should be included to facilitate part ejection. Gate placement, cooling channels, and ribbing must be strategically engineered to support consistent material flow and reduce cycle time. Because defects in large parts can result in high material losses, simulation tools are often used to predict flow patterns and optimize the mold before production begins.
Material Selection: Choosing the Right Resin for Your Large Part
Material choice plays a crucial role in the performance and durability of large molded parts. Common resins include polypropylene (PP) for general-purpose applications, high-density polyethylene (HDPE) for impact resistance, and polycarbonate (PC) for optical clarity and toughness. Engineering-grade plastics like ABS or nylon are used when mechanical strength or thermal stability is required. The resin selected must be compatible with the part’s intended environment, mechanical demands, and expected lifespan. Additives such as UV stabilizers or flame retardants can also be incorporated to enhance performance.
Is Your Product a Good Fit for Large Part Injection Molding?
Not every product is suitable for this process, so it’s important to evaluate your specific needs. Ideal candidates are products that require high volumes, consistent quality, and large dimensions. Ask yourself: Is the product size beyond standard molding capabilities? Does your design benefit from being made as a single piece? Can you justify the initial tooling investment with long-term production volume? Are you replacing metal or multi-piece assemblies with plastic for cost or weight reduction? If the answer is yes to most of these questions, large part injection molding may be a perfect fit.
The Cost Factor: Understanding the Investment in Large Part Injection Molding
While large part injection molding offers long-term savings, it requires a significant initial investment. Tooling costs are higher due to the size and complexity of molds, and the machines themselves are more expensive to operate. However, when amortized over large production runs, the per-unit cost becomes very competitive. Additional cost benefits come from reduced assembly, minimized waste, and shorter production cycles. Businesses should carefully analyze both short-term budgets and long-term production needs to determine overall ROI.
Partnering with the Right Manufacturer for Large Part Injection Molding
Choosing the right manufacturing partner is crucial for success. Look for a provider with proven experience in large part injection molding, preferably with in-house engineering support and advanced simulation tools. Ensure they have the press capacity to handle your part size and resin type. Quality assurance processes such as statistical process control and real-time monitoring can greatly improve consistency. Also, open and transparent communication throughout the project lifecycle helps avoid costly mistakes and delays.
Common Challenges and How to Avoid Them
Large part injection molding comes with unique challenges. Warping and shrinkage are more likely in bigger parts due to uneven cooling. Material flow issues can cause incomplete fills or visible defects. Tooling wear and high tonnage requirements may lead to downtime if not properly managed. These risks can be mitigated through proper mold design, regular maintenance, and the use of advanced software simulations. Working closely with experienced molders helps prevent surprises during production.
Future Trends in Large Part Injection Molding
The future of large part injection molding is being shaped by several technological advances. Automation is reducing labor needs and improving consistency. Lightweight yet high-performance materials are expanding the possibilities of part design. Sustainability is also driving innovation, with increased use of recycled and bio-based resins. Smart manufacturing tools, including AI and IoT, are helping molders monitor and optimize processes in real time, enhancing productivity and quality assurance.
Making the Smart Choice for Your Business
Large part injection molding is a powerful manufacturing solution for businesses seeking durability, efficiency, and design flexibility in producing sizable plastic components. While the upfront investment may be higher, the long-term benefits in production speed, part performance, and cost savings often outweigh the initial costs. By understanding the process, evaluating your product fit, and partnering with the right manufacturer, you can unlock the full potential of this technology and give your business a competitive edge.