- May 9, 2025
- Posted by: feinuojixie
- Category: Injection Molding News
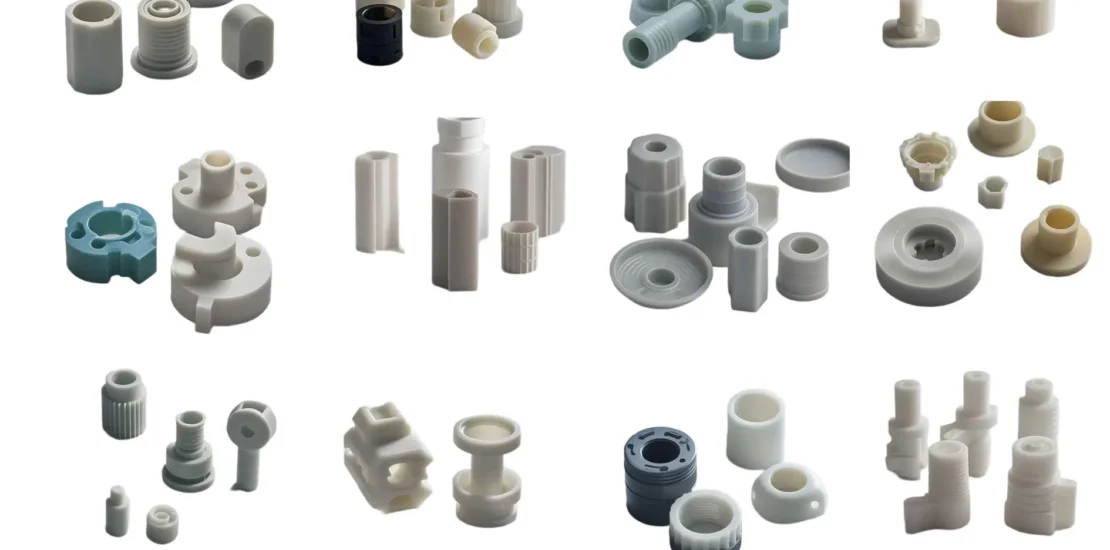
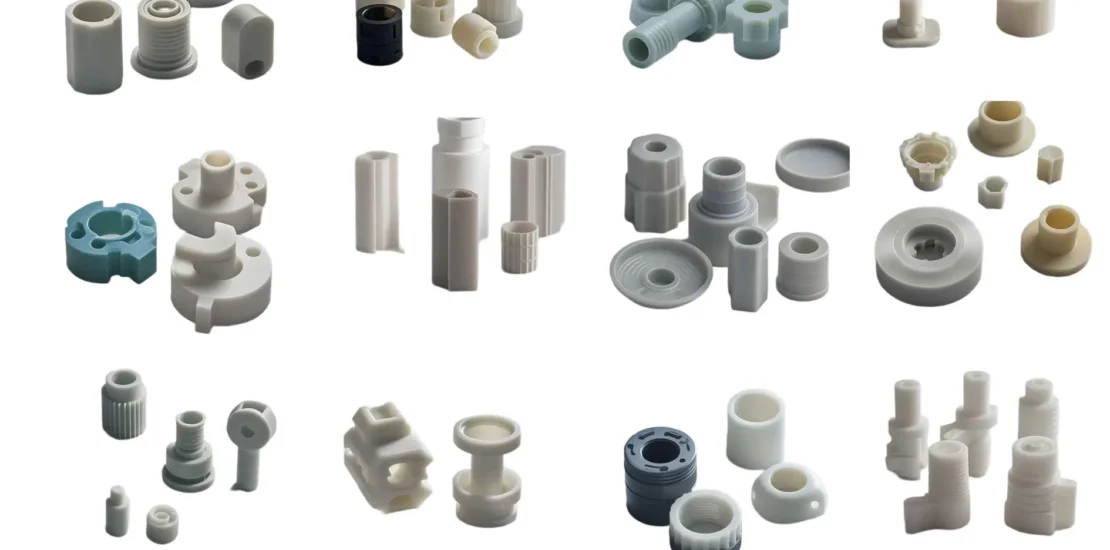
When sourcing components for your product, it can be tempting to go with the lowest bidder. However, when it comes to plastic injection part, cutting costs too far often leads to cutting corners. A seemingly minor flaw in a plastic component can have significant consequences, including product failure, warranty claims, or damage to your brand’s reputation. Recognizing the early warning signs of low-quality plastic injection part is essential to protecting both your product and your business.
How Plastic Injection Part Quality Impacts Your Business
The quality of each plastic injection part directly impacts your product’s performance, lifespan, and customer satisfaction. A defective or poorly manufactured component can result in malfunctioning assemblies, increased production downtime, or costly replacements. Moreover, poor part quality reflects badly on your brand, eroding consumer trust. In industries like automotive, medical devices, or electronics, subpar components can also raise serious safety concerns and legal liabilities. Ensuring top-tier part quality is not just a matter of cost—it’s a strategic investment.
Inconsistent Wall Thickness in a Plastic Injection Part
Uniform wall thickness is critical for structural strength and even material flow during molding. Inconsistent walls often result from flawed mold design or poor process control. This can lead to warping, internal stress, and premature part failure. When inspecting parts, be wary of areas that appear thin or feel fragile. These irregularities compromise the part’s performance under mechanical load or thermal stress, especially in functional applications.
Flash and Burrs on the Plastic Injection Part Surface
Flash occurs when molten plastic escapes the mold cavity and solidifies along the edges, creating unwanted protrusions. Burrs are similar defects caused by worn molds or poor clamping pressure. These imperfections not only detract from the appearance but can also interfere with part function—especially when precise fits or smooth surfaces are required. Excessive flash is a classic indicator that your supplier isn’t properly maintaining molds or managing production settings.
Poor Fit and Assembly in Plastic Injection Part Applications
Precision matters. If the plastic injection part doesn’t fit as intended during assembly, it’s a red flag. Variations in dimensions, warping, or distortion can cause gaps, stress points, or part rejection altogether. Such issues typically stem from inadequate mold calibration, substandard tooling, or incorrect cooling cycles. Testing sample parts in real-world assemblies is a good way to identify this problem early.
Sink Marks and Warping in the Plastic Injection Part
Sink marks appear as sunken areas on the part’s surface and usually result from uneven cooling or thick sections. Warping causes the part to bend or twist, affecting its ability to function as designed. Both defects point to poor control over processing parameters such as cooling time and injection pressure. While cosmetic in some cases, these flaws often hint at deeper structural weaknesses.
Use of Low-Grade Material in a Plastic Injection Part
Not all plastics are created equal. A common cost-cutting tactic is to substitute specified materials with cheaper alternatives or high levels of regrind. While this might lower the unit cost, it severely compromises part performance, UV resistance, chemical stability, and impact strength. Always verify the resin type and grade, and request certificates of material compliance to ensure your part meets your design and safety standards.
Lack of Transparency in Quality Control for Plastic Injection Part
A reputable supplier will have clearly documented quality procedures, inspection reports, and traceable data for every production batch. If your supplier cannot or will not provide this information, it’s a clear warning sign. Inconsistent measurements, missing quality documentation, or a lack of response to inspection requests suggest that quality control is not a priority for them.
No Traceability for the Plastic Injection Part Manufacturing Process
Traceability is essential, especially in industries with strict regulatory oversight. If a defect is found, you must be able to trace it back to its origin—whether it’s the raw material lot, machine setting, or mold cavity. Suppliers who don’t provide full traceability may be trying to obscure shortcuts or mistakes in their production chain, leaving you vulnerable to undetected risks.
How to Audit Your Supplier for Plastic Injection Part Quality
Conducting a supplier audit is one of the most effective ways to ensure you’re getting a high-quality plastic injection part. Start with a physical visit to their facility to assess machinery, cleanliness, and operational standards. Review their certifications (ISO 9001, IATF 16949, etc.) and request to see process documentation, material traceability reports, and sample inspection records. Implement a sampling plan to test parts under real-world conditions before committing to large-scale orders.
Choosing a Reliable Supplier of Plastic Injection Part
A quality-focused supplier doesn’t just deliver parts—they provide value through consistency, transparency, and engineering support. Look for suppliers who are responsive, provide detailed documentation, and invest in equipment maintenance and staff training. Strong technical capability, clear communication, and a proactive approach to problem-solving are all signs of a partner who takes quality seriously.
Don’t Let a Poor Plastic Injection Part Undermine Your Product
A single weak link in your supply chain—like a poor plastic injection part—can sabotage even the most well-designed product. Recognizing the signs of low-quality production and proactively auditing your suppliers can protect your business from unnecessary risks. Don’t let cost-saving temptations outweigh long-term performance and reliability. Your product—and your brand reputation—deserve better.