- April 30, 2025
- Posted by: feinuojixie
- Category: Injection Molding News
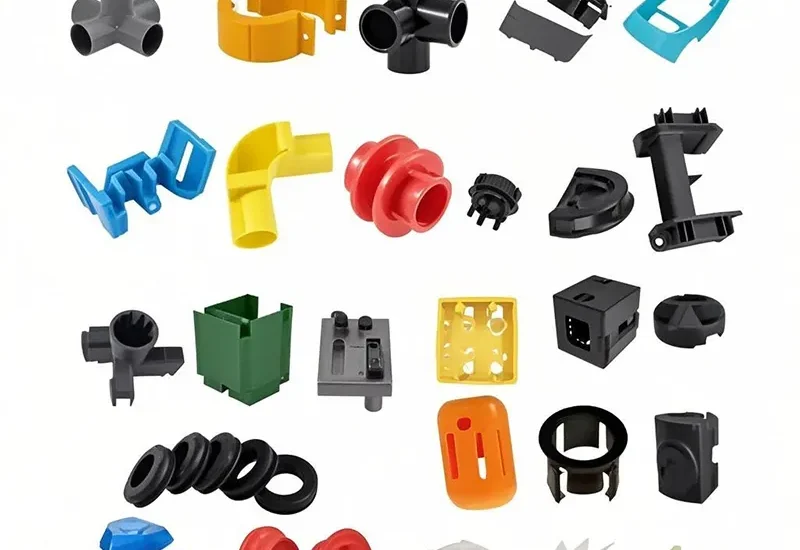
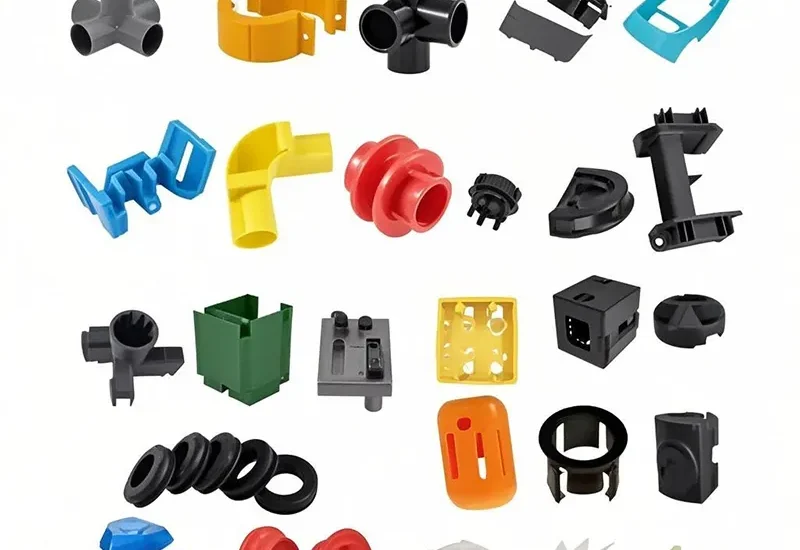
In today’s manufacturing landscape, the demand for strong, lightweight, and cost-efficient components has never been higher. Industries such as automotive, construction, and consumer goods rely heavily on large-scale plastic parts to reduce assembly complexity and improve product performance. This is where large part injection molding plays a crucial role. It enables the production of robust components in high volumes with consistent quality and structural integrity. Unlike traditional methods that may involve multiple steps or assemblies, large part injection molding consolidates production into a single, efficient process. This not only saves time and material but also ensures long-term reliability—making it the go-to choice for manufacturers seeking both durability and cost savings.
Understanding Large Part Injection Molding
Large part injection molding is a specialized process designed for producing sizable plastic components in one seamless operation. Unlike standard injection molding, which focuses on smaller, intricate parts, this method handles much larger volumes of molten plastic and distributes them into precisely engineered molds. The core principles remain the same: plastic pellets are melted, injected into a mold cavity, cooled, and then ejected as a finished part. However, the scale and complexity of large part injection molding require enhanced machinery, stronger molds, and more precise process control. It’s a highly effective solution when strength, consistency, and scale are critical to product success.
Materials That Drive Durability
The longevity and strength of large plastic parts depend heavily on the materials used in the molding process. Common thermoplastics like polypropylene, polyethylene, ABS, and polycarbonate are frequently chosen for their balance of strength, weight, and resistance to environmental stress. In applications requiring superior structural integrity or high-temperature tolerance, reinforced plastics—such as glass-filled nylon—are ideal. Material selection is not just about meeting performance requirements but also ensuring moldability and maintaining cost efficiency. Choosing the right resin can significantly extend the lifecycle of a product while keeping production economical.
Design Considerations for Large Part Injection Molding
Designing for large part injection molding is a strategic process that begins long before production. Engineers must account for factors such as wall thickness, ribbing, flow channels, and draft angles to prevent issues like warping, sink marks, or incomplete fills. Uniform wall thickness helps control shrinkage and stress distribution, while flow paths must be optimized to ensure even filling of the mold. Mold design itself is critical; it must accommodate high volumes of material without compromising precision or structural alignment. Smart design reduces rework, enhances product performance, and accelerates the path from concept to final part.
Cost-Effective Production at Scale
One of the strongest advantages of large part injection molding is its ability to drive down unit costs as production volumes rise. Once the mold is fabricated, each cycle yields a complete part in minutes, with minimal waste. The automated nature of the process reduces labor costs, and the material efficiency means less scrap and regrind. Additionally, integrating features such as inserts, surface finishes, or molded-in branding eliminates secondary operations, saving time and money. Over long production runs, these efficiencies add up significantly—making it an incredibly cost-effective manufacturing method.
Comparing Large Part Injection Molding to Other Manufacturing Methods
When compared to processes like CNC machining, thermoforming, or rotational molding, large part injection molding offers distinct benefits. While machining can deliver precision, it often involves longer cycle times and higher material waste. Thermoforming is fast but lacks the ability to produce structurally complex or highly detailed parts. Rotational molding is ideal for hollow components but can fall short in consistency and surface quality. Large part injection molding, by contrast, achieves high repeatability, dimensional accuracy, and strong mechanical properties—all at a lower cost per unit when scaled appropriately.
Real-World Applications of Large Part Injection Molding
From automotive bumpers and dashboards to appliance housings and storage containers, large part injection molding serves a wide array of industries. Construction sectors rely on it for creating durable parts like access panels and siding elements. In agriculture and heavy equipment manufacturing, molded plastic replaces metal in components that require corrosion resistance without sacrificing strength. The packaging industry uses it to create pallets and bins that withstand heavy loads while remaining lightweight. Its flexibility across applications demonstrates its value as a universal solution for large-format plastic production.
Quality Control in Large Part Injection Molding
Maintaining high standards is essential when producing large components, where minor defects can lead to significant functional or aesthetic issues. Modern large part injection molding facilities use real-time monitoring systems that track temperature, pressure, and fill rate during each cycle. Dimensional checks and mechanical testing ensure that the parts meet specified tolerances and performance benchmarks. Advanced inspection methods such as coordinate measuring machines (CMMs) and ultrasonic testing further enhance quality assurance. These controls prevent defects, reduce downtime, and build confidence in product reliability.
Challenges and How to Overcome Them
Despite its advantages, large part injection molding comes with technical challenges. Managing uniform fill and cooling in oversized molds can lead to warping, shrinkage, or flow imbalances. Venting and gating must be meticulously designed to avoid trapped air and short shots. Additionally, the initial tooling cost can be high, which may deter small production runs. These issues can be mitigated through simulation software during the design phase, expert mold design, and ongoing process optimization. Partnering with experienced manufacturers is also key to navigating these complexities and ensuring a smooth production cycle.
Future Trends in Large Part Injection Molding
The future of large part injection molding is being shaped by advancements in automation, digital monitoring, and sustainable materials. Smart manufacturing technologies enable real-time data analysis, predictive maintenance, and process automation—all of which improve efficiency and reduce downtime. Environmentally friendly materials, including bioplastics and recycled resins, are being integrated into production without compromising performance. Innovations in mold-making, such as 3D-printed inserts and conformal cooling, also contribute to faster cycles and improved part quality. These trends point to a future where large part injection molding is not only more capable but also more sustainable and adaptive.
The Strategic Advantage of Large Part Injection Molding
For companies seeking to build strong, reliable, and economical products, large part injection molding offers an unmatched combination of scale, durability, and cost control. Its ability to produce high-quality parts with precision and efficiency makes it an indispensable tool across a wide range of industries. By understanding the process, materials, design strategies, and emerging technologies, businesses can harness the full potential of this powerful manufacturing method. As demand for large, lightweight, and durable components continues to rise, large part injection molding stands as a key to competitive success.