- March 21, 2025
- Posted by: feinuojixie
- Category: Injection Molding News
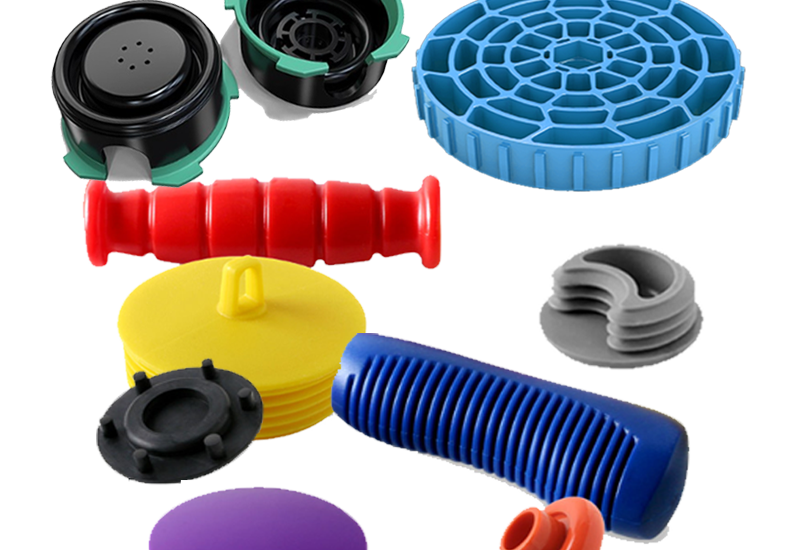
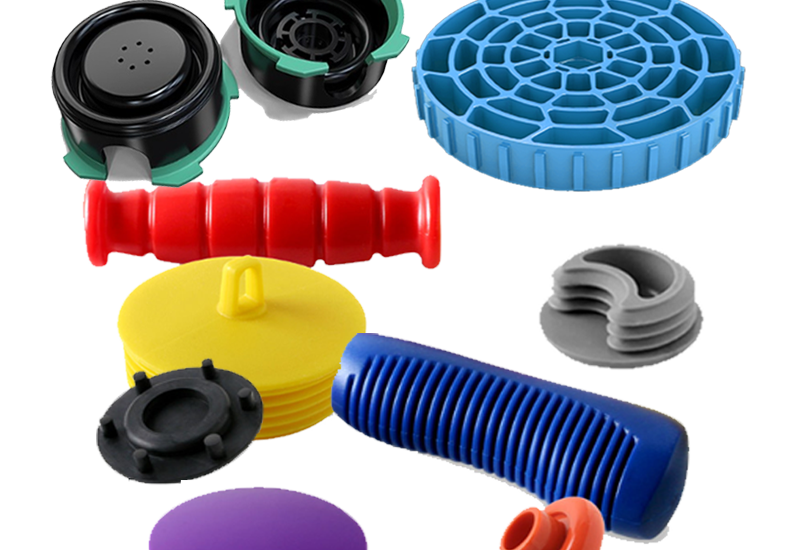
ABS injection moulding is a widely used manufacturing process that plays a crucial role in producing high-quality plastic components across various industries. Known for its strength, durability, and excellent surface finish, ABS (Acrylonitrile Butadiene Styrene) is a popular thermoplastic used in automotive, electronics, and consumer goods.
Precision and efficiency in ABS injection moulding are essential for reducing production costs, minimizing defects, and achieving consistent product quality. However, manufacturers often face challenges such as warping, short shots, and material degradation. Mastering the nuances of ABS injection moulding requires an in-depth understanding of material behavior, mould design, machine settings, and process optimization.
This guide provides expert insights into ABS injection moulding, covering everything from material selection to troubleshooting defects. Whether you are new to the process or looking to refine your skills, these tips will help you enhance precision and efficiency in ABS injection moulding.
Understanding ABS Injection Moulding
ABS injection moulding is a manufacturing process that involves injecting molten ABS material into a mould cavity, where it cools and solidifies into a final shape. This process is widely used due to ABS’s excellent impact resistance, strength, and smooth surface finish, making it suitable for products such as automotive components, electronic housings, and consumer goods.
The success of ABS injection moulding depends on controlling various factors, including temperature, pressure, and cooling time. Any deviation can lead to defects that affect product quality. By understanding how ABS behaves during moulding, manufacturers can optimize the process to achieve precision and efficiency.
Optimizing ABS Material Selection for Injection Moulding
Selecting the right ABS grade is critical for achieving desired properties in the final product. ABS is available in different formulations, each offering unique characteristics such as high impact resistance, UV stability, or improved flame retardancy.
- Additives and Fillers: Glass fibers, flame retardants, and UV stabilizers can modify ABS properties to enhance performance in specific applications.
- Material Flow and Mouldability: The melt flow index (MFI) of ABS determines how easily it fills the mould cavity. Choosing a grade with the appropriate MFI ensures smoother processing and reduces the likelihood of short shots or incomplete fills.
By carefully selecting the right ABS material, manufacturers can optimize production efficiency while maintaining product integrity.
Designing for ABS Injection Moulding Success
Proper part design is crucial for minimizing defects and ensuring smooth production. Here are key design considerations:
- Wall Thickness: Maintaining uniform wall thickness prevents warping and sink marks. Thin walls may lead to weak spots, while overly thick walls increase cooling time and material usage.
- Draft Angles: Incorporating draft angles in part design facilitates easier ejection from the mould, reducing stress and deformation.
- Rib Placement: Adding ribs improves structural integrity without increasing wall thickness, but improper rib design can cause sink marks or voids.
By implementing these design principles, manufacturers can improve part quality and reduce the risk of defects in ABS injection moulding.
Mould Design and Tooling Considerations
The mould plays a vital role in determining the quality and efficiency of ABS injection moulding. Proper mould design ensures accurate part formation and minimizes production issues.
- Mould Material Selection: Using high-quality steel or aluminum moulds enhances durability and precision.
- Temperature Control and Cooling Systems: A well-designed cooling system ensures uniform cooling, reducing cycle time and preventing warping.
- Venting and Gating: Proper venting prevents trapped air that can cause burn marks, while optimized gating ensures even material distribution.
Investing in a well-designed mould results in longer tool life, better product consistency, and higher efficiency in ABS injection moulding.
Injection Moulding Machine Settings for ABS
Fine-tuning machine parameters is essential for achieving consistent quality in ABS injection moulding. Key settings include:
- Temperature: ABS should be processed at the recommended melt temperature (typically between 200°C and 250°C) to avoid degradation.
- Injection Pressure: Maintaining the right pressure ensures proper material flow and minimizes voids or short shots.
- Injection Speed: A balanced injection speed prevents defects such as jetting or weld lines while ensuring complete cavity filling.
Optimizing these parameters enhances product quality while reducing cycle time and material waste.
Enhancing Efficiency in ABS Injection Moulding
To improve efficiency, manufacturers should focus on reducing downtime, optimizing cycle time, and leveraging automation.
- Cycle Time Optimization: Fine-tuning cooling and ejection phases minimizes unnecessary delays.
- Automation and Robotics: Automated handling systems reduce manual labor, increase precision, and speed up production.
- Sustainability Measures: Recycling excess ABS material and reducing energy consumption contribute to cost savings and environmental responsibility.
By implementing these strategies, manufacturers can achieve higher output and lower production costs in ABS injection moulding.
Troubleshooting Common ABS Injection Moulding Defects
Despite careful planning, defects may still occur in ABS injection moulding. Identifying and addressing these issues promptly is essential for maintaining quality.
- Warping: Caused by uneven cooling or internal stresses; can be reduced by optimizing cooling rates and ensuring uniform wall thickness.
- Voids and Weld Lines: Often result from improper injection pressure or material flow; adjusting pressure and gate placement can help.
- Poor Surface Finish: Can be caused by mould temperature fluctuations or contamination; maintaining clean moulds and stable processing conditions prevents this issue.
By systematically troubleshooting defects, manufacturers can enhance product consistency and reduce scrap rates.
Future Trends in ABS Injection Moulding
The ABS injection moulding industry is evolving with advancements in technology and materials. Emerging trends include:
- Smart Moulding Technologies: The integration of AI and IoT enables real-time monitoring and process optimization.
- Industry 4.0 Impact: Data-driven manufacturing enhances precision and reduces waste.
- Eco-Friendly Innovations: Development of bio-based and recycled ABS materials supports sustainability efforts.
These advancements will shape the future of ABS injection moulding, making it more efficient, precise, and environmentally friendly.
Conclusion
Mastering ABS injection moulding requires a comprehensive understanding of material selection, part design, machine settings, and process optimization. By implementing best practices, manufacturers can enhance precision, improve efficiency, and minimize defects in production.
With ongoing advancements in automation and smart manufacturing, ABS injection moulding continues to evolve, offering new opportunities for innovation and sustainability. By staying informed and adopting modern techniques, businesses can achieve superior results and remain competitive in the ever-growing plastics industry.