- March 19, 2025
- Posted by: feinuojixie
- Category: Injection Molding News
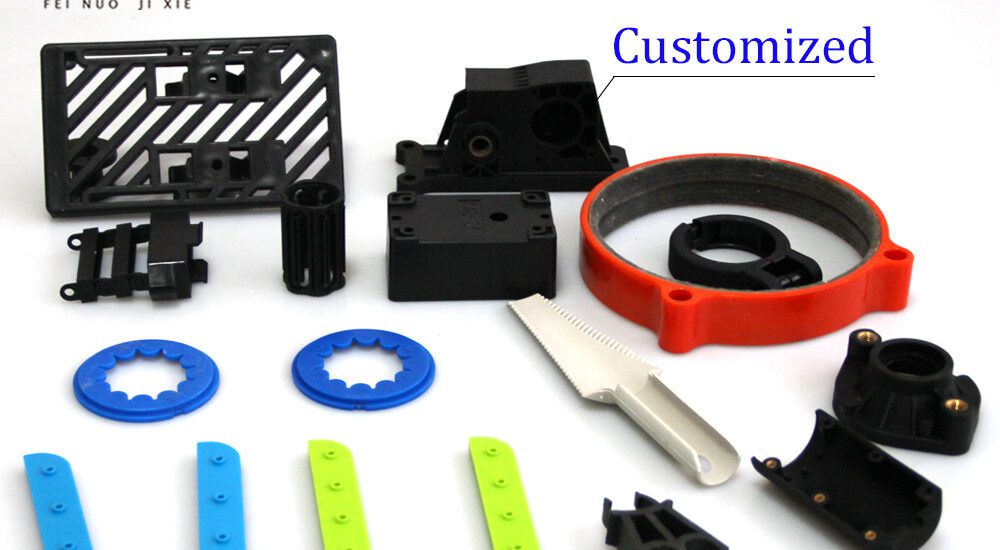
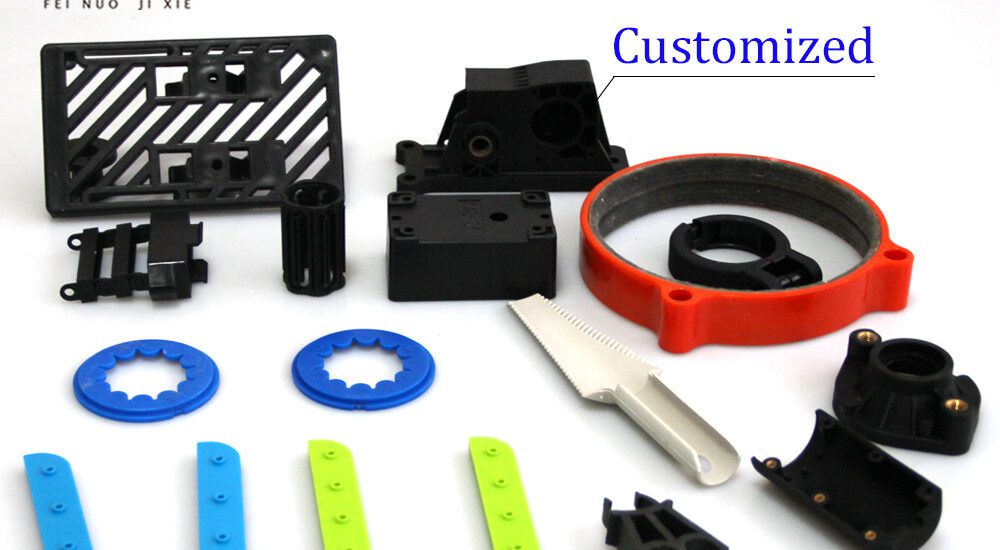
ABS injection moulding is one of the most popular manufacturing processes used in industries such as automotive, electronics, and consumer goods. Its versatility, strength, and cost-effectiveness make it an ideal choice for producing high-quality plastic parts. However, achieving superior durability and consistency in ABS products requires a deep understanding of the material and precise control over the moulding parameters.
This article provides a comprehensive guide to mastering ABS injection moulding, covering essential factors such as material preparation, temperature and pressure optimization, and advanced techniques to enhance product strength. Additionally, it addresses common challenges manufacturers face and offers expert strategies to improve efficiency and reduce production costs. By implementing these best practices, manufacturers can ensure their ABS moulded products meet the highest standards of durability and performance.
Understanding ABS Injection Moulding
What is ABS Injection Moulding?
ABS injection moulding is a process where heated Acrylonitrile Butadiene Styrene (ABS) is injected into a mould to create plastic components. ABS is a thermoplastic known for its excellent impact resistance, strength, and lightweight properties. This makes it a preferred material for various applications that require durability and precision.
Why Choose ABS for Injection Moulding?
ABS is widely used in injection moulding due to its:
- High impact resistance – Ideal for parts that must withstand physical stress.
- Excellent dimensional stability – Maintains shape even under temperature changes.
- Good surface finish – Allows for easy painting, plating, and polishing.
- Chemical resistance – Suitable for use in challenging environments.
These properties make ABS a top choice for manufacturers looking for a balance between durability, aesthetics, and cost-effectiveness.
Common Applications of ABS Injection Moulding
ABS injection moulding is widely used in:
- Automotive – Dashboards, interior trims, and structural components.
- Electronics – Laptop cases, keyboards, and protective casings.
- Consumer Goods – Toys, kitchen appliances, and sporting equipment.
- Medical Devices – Housings for medical instruments and diagnostic tools.
Essential Factors in ABS Injection Moulding
Material Preparation and Drying
Before ABS can be processed, it must be properly dried to prevent defects like bubbles and weak spots. ABS is hygroscopic, meaning it absorbs moisture from the air, which can cause imperfections in the final product. A drying temperature of 80–90°C for 2–4 hours is recommended to remove excess moisture and ensure a smooth moulding process.
Optimizing Injection Temperature and Pressure
Controlling the temperature and pressure during injection is crucial for achieving strong and defect-free parts.
- Injection temperature: Should be maintained between 210–250°C, depending on the ABS grade.
- Injection pressure: Ranges between 50–150 MPa to ensure complete filling of the mould.
- Holding pressure: Applied to prevent shrinkage and improve material distribution.
Mould Design and Cooling System Efficiency
The mould design significantly affects product quality and durability. Key considerations include:
- Gate placement: Ensures even material flow to reduce weak points.
- Cooling channels: A well-designed cooling system prevents warping and speeds up production.
- Venting: Proper venting reduces trapped air, minimizing burn marks and defects.
Techniques for Enhancing Product Strength and Durability
Proper Gate Design for Uniform Material Flow
Gates control the entry of molten ABS into the mould cavity. A well-placed gate helps reduce stress concentration, ensuring even material distribution. Common gate types for ABS injection moulding include:
- Edge gates – Ideal for flat and thin-walled components.
- Submarine gates – Used for automated production with minimal finishing work.
- Fan gates – Prevent warping in larger moulded parts.
Minimizing Internal Stresses Through Controlled Cooling
Controlled cooling prevents internal stresses that could lead to cracks or deformation. Gradual and uniform cooling enhances the strength of ABS products. This can be achieved by:
- Using consistent cooling channels in the mould.
- Maintaining a steady cooling rate to prevent uneven shrinkage.
- Optimizing mould temperature to balance cooling speed and dimensional accuracy.
Reinforcing ABS with Additives for Extra Durability
Additives can enhance ABS properties for specific applications. Common reinforcements include:
- Glass fibers – Improve stiffness and heat resistance.
- UV stabilizers – Prevent discoloration from prolonged sun exposure.
- Impact modifiers – Enhance toughness for high-stress applications.
Common Challenges in ABS Injection Moulding and How to Overcome Them
Avoiding Warping and Shrinkage Issues
Warping occurs when cooling is uneven, causing the material to contract at different rates. To reduce warping:
- Ensure uniform cooling with properly placed cooling channels.
- Use a balanced mould design to distribute stress evenly.
- Adjust injection speed to prevent sudden temperature changes.
Shrinkage happens due to material contraction as it cools. This can be minimized by:
- Using higher holding pressure to compensate for material contraction.
- Increasing mould temperature for gradual cooling.
Preventing Burn Marks and Discoloration
Burn marks appear when ABS is overheated or trapped air ignites. Solutions include:
- Lowering injection speed to reduce frictional heating.
- Improving mould venting to allow air to escape.
- Cleaning the mould regularly to remove carbon buildup.
Discoloration can result from prolonged exposure to high temperatures. To maintain color consistency:
- Optimize processing temperature within ABS’s thermal stability range.
- Use heat stabilizers to prevent material degradation.
Reducing Brittleness and Improving Impact Resistance
ABS parts may become brittle if processed incorrectly. To improve impact resistance:
- Increase material thickness in high-stress areas.
- Use impact-resistant ABS grades designed for heavy-duty applications.
- Optimize cooling rate to prevent rapid crystallization.
Advanced Strategies for Improving Efficiency and Cost-Effectiveness
Optimizing Cycle Time for Mass Production
Cycle time affects productivity and cost. To maximize efficiency:
- Reduce cooling time using effective cooling channel designs.
- Use multi-cavity moulds to produce multiple parts in one cycle.
- Automate demoulding to speed up production.
Automation and Smart Moulding Techniques
The integration of automation and smart technologies enhances precision and repeatability. Some advanced techniques include:
- Robotic part handling for faster production and consistency.
- AI-driven process monitoring to optimize temperature and pressure settings.
- Predictive maintenance systems to reduce downtime and equipment failure.
Sustainable Practices in ABS Injection Moulding
Sustainability is becoming a priority in manufacturing. To make ABS injection moulding more eco-friendly:
- Use recycled ABS to reduce material waste.
- Optimize energy consumption by using efficient heating and cooling systems.
- Implement waste reduction strategies such as reusing excess material.
Conclusion
Mastering ABS injection moulding requires a combination of material knowledge, precise processing control, and advanced mould design techniques. By optimizing factors like temperature, pressure, cooling, and material selection, manufacturers can produce stronger and more durable ABS products. Overcoming common challenges such as warping, brittleness, and discoloration ensures higher-quality output. Additionally, leveraging automation and sustainable practices improves efficiency while reducing costs.