- May 5, 2025
- Posted by: feinuojixie
- Category: Injection Molding News
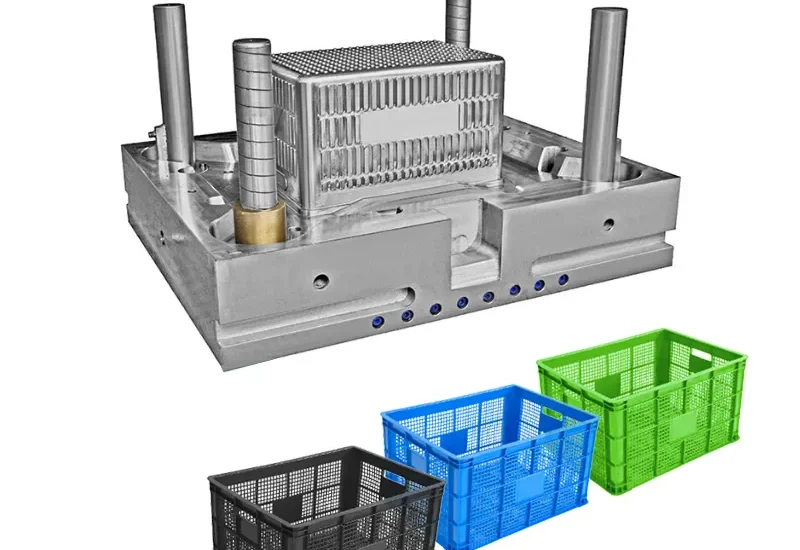
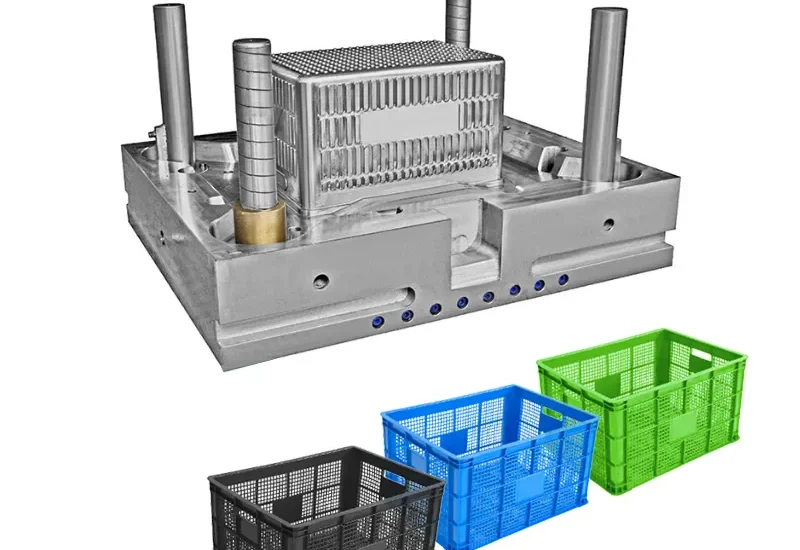
Large part injection molding plays a pivotal role in modern manufacturing, enabling the production of high-quality, durable, and complex components across a variety of industries. As industries continue to demand larger and more intricate parts, mastering this process becomes a key competitive advantage. However, it’s not without its challenges. Unlike standard injection molding, which deals with smaller, more straightforward components, large part injection molding requires a high level of expertise, precision, and advanced technology to ensure successful outcomes. In this article, we’ll explore the fundamental principles of large part injection molding, the common challenges faced during the process, expert tips to overcome them, and the latest innovations shaping the future of this critical manufacturing technique. Whether you’re a manufacturer looking to refine your process or an engineer interested in the complexities of large part production, this guide will provide valuable insights to help you master the art of large part injection molding.
Understanding the Basics of Large Part Injection Molding
Large part injection molding is a specialized form of injection molding that involves the production of sizable, often complex components. Unlike standard injection molding, which typically deals with smaller parts, large part injection molding requires specialized equipment, molds, and a deeper understanding of material behavior. This process uses high pressure to inject molten plastic into a mold cavity, where it cools and solidifies into the desired shape. The key to successful large part injection molding lies in the ability to control various parameters, such as injection speed, mold temperature, and material characteristics, to achieve the desired part specifications.
Common materials used in large part injection molding include high-performance plastics such as ABS, polypropylene, and polyethylene, each chosen for its strength, durability, and resistance to heat. As the parts being produced are often larger and more intricate, the design of the mold itself plays a critical role in ensuring that the final part meets quality standards and is free from defects.
Challenges Faced in Large Part Injection Molding
The process of large part injection molding is far more complex than that of smaller parts, presenting unique challenges for manufacturers. One of the primary difficulties is designing the mold to accommodate the size and complexity of the part. Large molds require precise engineering to ensure that the material flows evenly throughout the cavity, which can be more difficult when dealing with larger volumes of material.
Additionally, temperature control becomes significantly more challenging. Larger parts tend to have more substantial thicknesses, and without adequate cooling, they may warp, crack, or fail to solidify properly. Material flow can also be inconsistent, leading to areas of the part that are weaker than others or fail to meet dimensional accuracy requirements. These issues can result in defects that impact the overall quality of the part, and addressing them requires advanced techniques and specialized equipment.
Expert Tips for Successful Large Part Injection Molding
To master the art of large part injection molding, manufacturers must focus on several key areas. The first step is to ensure precise mold design and engineering. This involves using advanced software tools to simulate the injection process and optimize mold geometry before fabrication. By anticipating potential issues with material flow and cooling, manufacturers can save time and reduce costs associated with trial and error.
Another essential aspect of successful large part injection molding is selecting the right material for the job. While materials like ABS and polypropylene are commonly used, choosing the wrong material can lead to part failure. Experts recommend working with material suppliers to understand the thermal and mechanical properties of the material and ensuring that it aligns with the part’s intended application.
Optimizing injection molding parameters is another critical tip. Factors such as injection speed, pressure, and cycle time need to be carefully controlled to ensure consistent part quality. Adjustments to these parameters can make a significant difference in the final outcome, especially when dealing with large, complex parts. Manufacturers should closely monitor these variables to fine-tune their process and achieve the best results.
Innovative Solutions to Overcome Common Challenges
As large part injection molding presents unique challenges, innovative solutions have been developed to help manufacturers overcome these hurdles. One such solution is the use of advanced cooling techniques. Since cooling is crucial for the proper solidification of large parts, methods such as conformal cooling, which uses 3D-printed molds to create more efficient cooling channels, can significantly reduce cycle times and minimize the risk of warping.
Additionally, multi-material injection molding has gained popularity in producing large parts with complex geometries or varying material properties. This technique allows different materials to be injected into a single mold, enabling the creation of parts with different characteristics, such as rigidity or flexibility, in different areas of the same component. This innovation opens up new possibilities for creating parts that meet the demanding requirements of modern industries.
Addressing material shrinkage and warping is another critical area where innovation has made a difference. Through advanced simulation tools, manufacturers can predict and compensate for shrinkage during the molding process, ensuring parts retain their intended dimensions even after cooling.
Quality Control and Testing in Large Part Injection Molding
Ensuring the quality of large injection-molded parts requires a stringent quality control process. Due to the complexity and size of these parts, manufacturers must conduct thorough inspections at every stage of production. One of the most important steps is to monitor the mold during the injection process to ensure that the material is flowing correctly and that there are no air pockets or inconsistencies in the final product.
Various testing methods are used to evaluate the strength, durability, and dimensional accuracy of large parts. Common tests include tensile testing, impact testing, and visual inspection for defects. Any issues detected during these tests should be addressed immediately to avoid production delays and costly rework.
By integrating real-time monitoring systems and predictive analytics into their processes, manufacturers can detect defects early and make necessary adjustments before the parts are fully produced. This proactive approach can save time and resources while ensuring that the final product meets all performance standards.
Sustainability and Efficiency in Large Part Injection Molding
As environmental concerns become more prominent in the manufacturing industry, sustainability has become a key focus in large part injection molding. Reducing waste and improving energy efficiency are two primary goals for manufacturers looking to minimize their environmental impact. Techniques such as optimizing cycle times and using recyclable materials can help reduce waste produced during the molding process.
Innovations in sustainable materials are also shaping the future of large part injection molding. Bio-based plastics and recycled materials are becoming more prevalent as manufacturers seek ways to reduce the environmental footprint of their production processes. Using materials that can be recycled or repurposed not only helps protect the environment but also offers long-term cost savings for manufacturers.
By adopting energy-efficient technologies and sustainable practices, manufacturers can improve the efficiency of their operations while aligning with industry standards for environmental responsibility.
The Future of Large Part Injection Molding
Looking ahead, the future of large part injection molding is poised for exciting advancements. Automation and artificial intelligence (AI) are expected to play a significant role in improving the efficiency and precision of the molding process. Automated systems can monitor and adjust parameters in real time, reducing human error and ensuring consistent quality across large production runs.
Additionally, as materials science continues to evolve, manufacturers will have access to new, high-performance materials that offer improved strength, durability, and sustainability. These advancements will further expand the possibilities of large part injection molding, enabling the production of even more complex and durable components.
The integration of 3D printing technology and advanced simulation software will also continue to evolve, allowing for faster prototyping, reduced lead times, and improved mold designs. As these technologies mature, the efficiency and capabilities of large part injection molding will only increase, further solidifying its place in modern manufacturing.
Conclusion
Mastering the art of large part injection molding is no small feat, but with the right approach and expert knowledge, manufacturers can achieve outstanding results. By focusing on precise mold design, optimizing material selection and process parameters, and embracing innovative solutions, manufacturers can overcome the challenges associated with producing large parts. Additionally, implementing rigorous quality control measures and embracing sustainability practices will ensure the continued success and growth of the industry. As the technology continues to evolve, staying up-to-date with emerging trends and best practices will be essential for any manufacturer looking to excel in the field of large part injection molding.