- May 6, 2025
- Posted by: feinuojixie
- Category: Injection Molding News
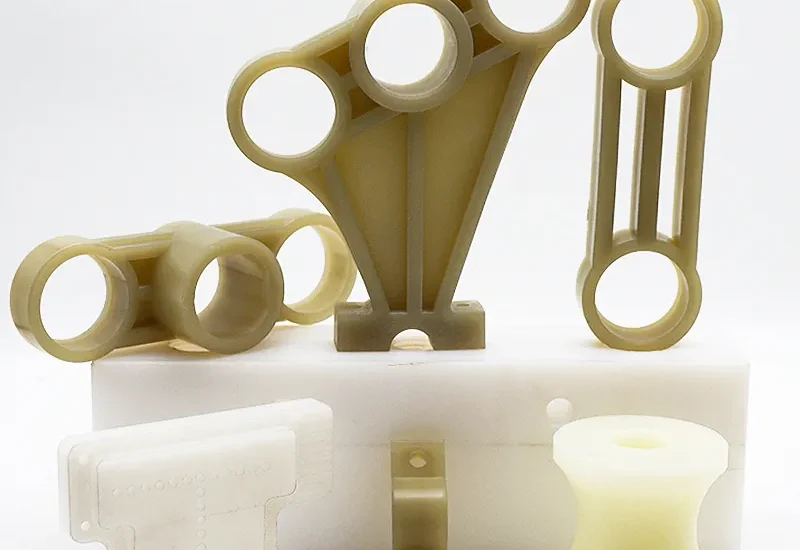
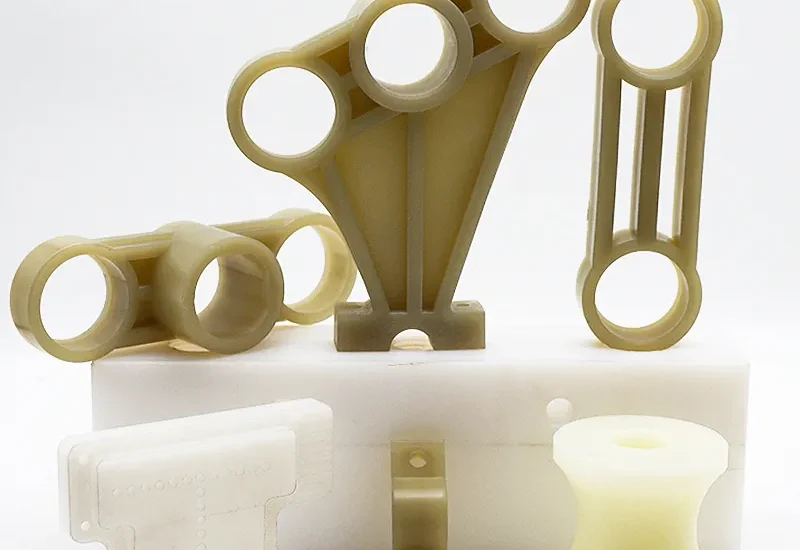
Large part injection molding plays a vital role in manufacturing robust components for industries like automotive, aerospace, and construction. Unlike standard molding processes, the stakes are significantly higher when producing large-scale parts due to the substantial investment in equipment, molds, and raw materials. Inefficiencies in this context not only increase operational costs but also lead to delays, defects, and excessive material waste.
Efficiency in large part injection molding is not simply about speeding up cycle times. It encompasses everything from precise mold design and optimized processing conditions to skilled labor and predictive maintenance. When all these elements align, manufacturers can achieve consistent part quality, reduce scrap rates, and improve profitability.
Understanding the Complexity of Large Part Injection Molding
Large part injection molding introduces a range of technical challenges that are not present in standard applications. The size and weight of the molds require specialized equipment capable of delivering higher clamp forces and longer strokes. Additionally, the resin must fill large cavities quickly and uniformly to avoid issues like short shots, sink marks, or warping.
Handling large parts also demands precise coordination in every step of the process—from mold setup to part ejection. Even slight inconsistencies in temperature or material flow can lead to costly defects. Recognizing the complexity of large part injection molding is the first step toward optimizing it for efficiency.
Choosing the Right Machine for Large Part Injection Molding
Machine selection is one of the most critical factors in large part injection molding. The machine must be capable of accommodating large molds, which often means higher clamp tonnage and extended platen spacing. Choosing a machine with sufficient shot size is essential to ensure complete mold filling without material degradation.
Advanced control systems in modern machines also contribute to efficiency. Features such as real-time monitoring and adaptive process control help maintain consistency throughout production. Investing in a machine tailored to large part injection molding not only improves efficiency but also minimizes downtime and rework.
Optimizing Mold Design for Large Part Injection Molding Efficiency
A well-designed mold lays the foundation for efficient production. For large part injection molding, mold design should prioritize balanced filling, efficient cooling, and easy part ejection. Designers often incorporate multiple gates, optimized runner systems, and conformal cooling channels to reduce cycle times and enhance dimensional stability.
Another critical aspect is the integration of automation-friendly features. Molds designed for robotic handling and in-mold labeling can significantly reduce manual intervention. By optimizing every element of the mold design, manufacturers can achieve faster cycles, better part quality, and fewer disruptions.
Material Selection Strategies for Large Part Injection Molding
The material used in large part injection molding has a direct impact on cycle time, strength, and processing behavior. Engineers must consider the melt flow index, shrinkage characteristics, and thermal stability of the resin to match it with the application requirements.
For example, materials with high flow rates reduce injection pressure requirements and ensure uniform cavity filling. Reinforced resins or additives may enhance mechanical properties but can also affect mold wear and cooling times. Choosing the right material involves balancing performance with processing efficiency, often supported by material testing and simulation.
Process Parameter Control for Large Part Injection Molding
Controlling process parameters is essential for maintaining efficiency and part consistency. In large part injection molding, variables such as injection speed, pressure, barrel temperature, and cooling time must be carefully tuned. Because of the size and complexity of the parts, small deviations can lead to significant quality issues.
Modern injection molding machines allow for closed-loop control systems that automatically adjust parameters during each cycle. This level of control minimizes waste, reduces energy consumption, and improves repeatability. Regular process audits and data analysis further enhance parameter optimization over time.
Leveraging Simulation and Mold Flow Analysis
Simulation tools have become indispensable in large part injection molding. Mold flow analysis helps engineers predict how resin will behave inside the mold, identifying potential issues such as air traps, weld lines, or imbalanced filling before physical molds are built.
By simulating various gate placements, cooling configurations, and material selections, manufacturers can refine their designs and processes for maximum efficiency. The ability to visualize and troubleshoot problems virtually shortens development time and reduces costly trial-and-error on the shop floor.
Automating the Production Line for Large Part Injection Molding
Automation plays a key role in improving both speed and reliability in large part injection molding. Robotic systems can handle heavy molded parts with precision, reducing the risk of operator error and physical strain. Automated mold loading and part removal also decrease cycle time and increase throughput.
Vision systems and sensors can be integrated for in-line inspection, ensuring only quality parts move forward. Even secondary operations such as trimming, assembly, or packaging can be automated. These systems not only boost efficiency but also support consistency in high-volume production.
Implementing Preventive Maintenance on Molding Equipment
Preventive maintenance is vital to avoid unexpected breakdowns and costly downtime, especially in large part injection molding where each production hour is highly valuable. Maintenance programs should include regular inspection of hydraulic systems, heaters, sensors, and mechanical components.
Mold maintenance is equally important. Cleaning, lubrication, and alignment checks prevent flash, wear, and part defects. Some manufacturers use predictive maintenance powered by sensors and analytics to monitor equipment health in real time. A proactive approach ensures longer equipment life and uninterrupted production.
Training and Skill Development for Large Part Injection Molding Teams
Technology and equipment are only as effective as the people operating them. Skilled technicians and engineers are essential for running complex large part injection molding operations. Continuous training in areas such as troubleshooting, process optimization, and equipment programming leads to greater efficiency.
Empowering employees with knowledge also fosters a culture of accountability and continuous improvement. Whether through formal certifications, hands-on workshops, or cross-functional team learning, investing in workforce development delivers long-term operational benefits.
Monitoring KPIs and Continuous Improvement
Efficiency can’t be improved if it’s not measured. Establishing and tracking key performance indicators (KPIs) such as cycle time, scrap rate, machine utilization, and downtime provides a clear view of where improvements are needed. Data-driven decisions are far more effective than assumptions.
Implementing lean manufacturing principles and using structured problem-solving methods like Six Sigma can uncover hidden inefficiencies. By committing to a culture of continuous improvement, manufacturers ensure that their large part injection molding operations remain competitive and adaptable.
Building a Foundation for Sustainable Success
Maximizing efficiency in large part injection molding is not achieved through a single initiative—it requires a comprehensive strategy that spans equipment, design, materials, processes, people, and analytics. Each best practice covered in this blog contributes to a more reliable, productive, and cost-effective molding operation.
As product demands grow and competition increases, manufacturers that embrace efficiency as a core principle will lead the way in delivering high-quality, large-scale plastic parts to the market. The path to success is built on careful planning, consistent execution, and a willingness to evolve with technology and industry standards.