- March 28, 2025
- Posted by: feinuojixie
- Category: Injection Molding News
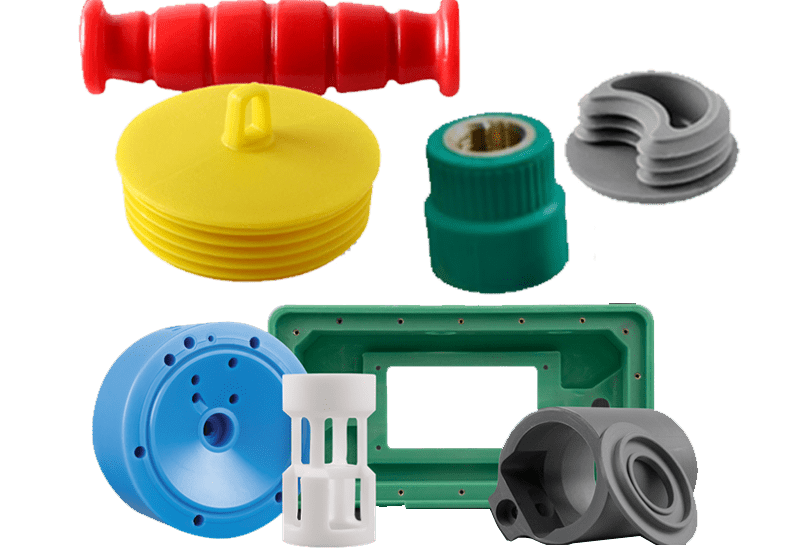
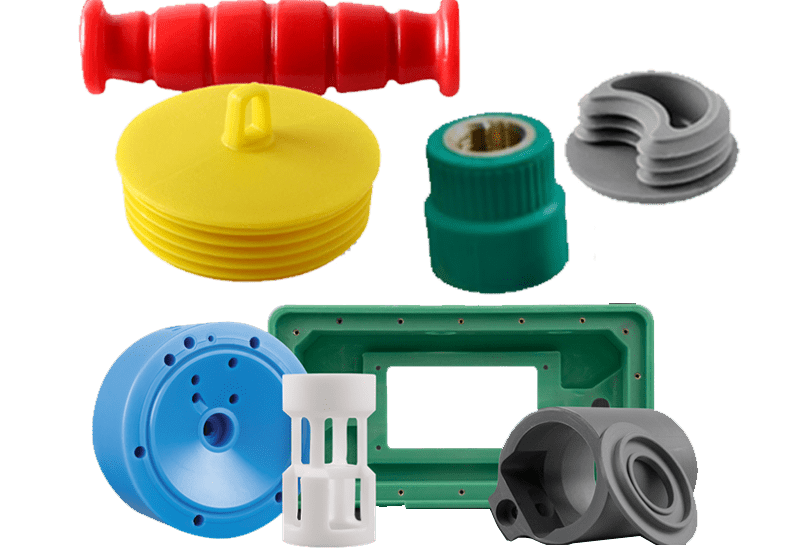
PC ABS injection moulding is a widely used manufacturing process that combines the benefits of polycarbonate (PC) and acrylonitrile butadiene styrene (ABS). This hybrid material offers superior strength, impact resistance, and heat tolerance, making it an ideal choice for various industries, including automotive, electronics, and consumer goods.
As industries continue to demand high-performance materials for durable and lightweight products, PC ABS injection moulding has become an essential technique for manufacturers. This article explores everything you need to know about PC ABS injection moulding, from its material properties to its applications and benefits.
What Is PC ABS Injection Moulding?
PC ABS injection moulding is a manufacturing process that involves injecting molten PC ABS material into a mould cavity to create precise and durable plastic components. This process combines the benefits of polycarbonate (PC) and acrylonitrile butadiene styrene (ABS), resulting in a material that is both tough and flexible.
The process begins by heating and melting the PC ABS resin, which is then injected under high pressure into a mould. Once cooled and solidified, the mould opens to release the finished product. This method allows for mass production of high-quality plastic parts with complex shapes and fine details.
Compared to other moulding techniques, such as extrusion or thermoforming, injection moulding offers greater precision, repeatability, and efficiency, making it a preferred choice for manufacturers across various industries.
Understanding PC ABS Material
PC ABS is an engineering-grade thermoplastic blend that combines the best qualities of both polycarbonate and ABS. This unique composition gives it excellent impact resistance, high heat tolerance, and superior mechanical strength.
Key Properties of PC ABS:
-
Impact resistance: PC ABS is highly resistant to impact, making it ideal for applications where durability is crucial.
-
Heat resistance: The material can withstand high temperatures without deforming or losing its structural integrity.
-
Chemical resistance: PC ABS resists many chemicals, including oils and acids, making it suitable for industrial and consumer applications.
-
Aesthetic versatility: It can be easily colored, textured, or finished to meet design requirements.
-
Easy processing: PC ABS has good flow characteristics, allowing for complex and detailed moulding.
The Injection Moulding Process for PC ABS
The PC ABS injection moulding process involves several key steps that ensure the production of high-quality components:
-
Material Preparation – PC ABS pellets are dried to remove moisture, preventing defects during moulding.
-
Melting and Injection – The material is heated to its melting point and injected into a mould cavity under high pressure.
-
Cooling and Solidification – The molten plastic cools and takes the shape of the mould, forming the final product.
-
Mould Opening and Ejection – The mould separates, and the finished part is ejected for further processing.
-
Finishing and Quality Control – The product may undergo trimming, painting, or coating before final inspection and packaging.
Applications of PC ABS Injection Moulding
Due to its versatility and durability, PC ABS injection moulding is used in a wide range of industries.
Common Applications:
-
Automotive parts: PC ABS is used in dashboards, interior trims, and structural components due to its impact resistance.
-
Electronics: The material is widely used for laptop casings, smartphone bodies, and electrical enclosures.
-
Medical devices: PC ABS is found in medical housings, instrument panels, and protective gear.
-
Consumer products: It is used for home appliances, power tools, and sports equipment.
Key Benefits of PC ABS Injection Moulding
Manufacturers choose PC ABS injection moulding for several reasons, including:
-
Exceptional durability: The combination of PC and ABS results in a strong material that withstands wear and tear.
-
High heat resistance: PC ABS components maintain their shape and performance even under high temperatures.
-
Design flexibility: Complex shapes and detailed features can be achieved with ease.
-
Cost-effectiveness: The efficiency of injection moulding reduces material waste and production costs.
Factors to Consider in PC ABS Injection Moulding
To achieve the best results in PC ABS injection moulding, manufacturers must consider:
-
Proper mould design: A well-designed mould ensures smooth material flow and minimizes defects.
-
Optimal processing conditions: Temperature, pressure, and cooling time must be carefully controlled to maintain product quality.
-
Common defects and solutions: Issues such as warping, sink marks, or incomplete filling can be prevented with proper moulding techniques.
Future Trends in PC ABS Injection Moulding
The field of PC ABS injection moulding is evolving with advancements in technology and sustainability.
-
Innovations in materials: Researchers are developing enhanced PC ABS blends with improved strength and eco-friendly properties.
-
Sustainable manufacturing: Recycling and biodegradable alternatives are becoming increasingly important in reducing plastic waste.
-
Automation and AI: Smart moulding machines with AI integration are improving efficiency and precision in production.
Conclusion
PC ABS injection moulding is a powerful and versatile manufacturing process that combines the best qualities of polycarbonate and ABS. Its durability, heat resistance, and design flexibility make it the material of choice for industries ranging from automotive to consumer electronics.
As technology continues to advance, PC ABS injection moulding will play an even greater role in producing high-quality, cost-effective, and sustainable plastic components. Understanding the process, benefits, and applications of PC ABS can help manufacturers make informed decisions and stay ahead in the competitive market.