- March 27, 2025
- Posted by: feinuojixie
- Category: Injection Molding News
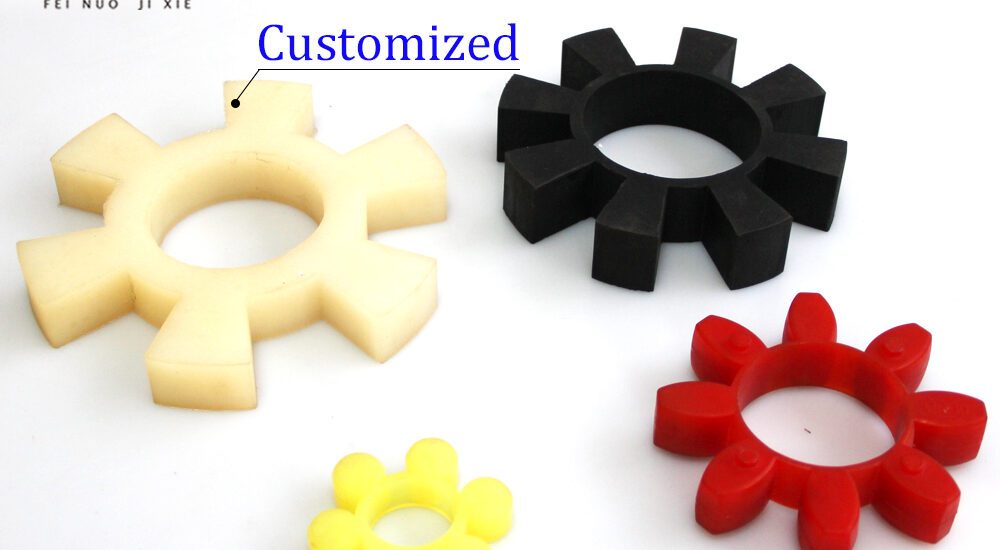
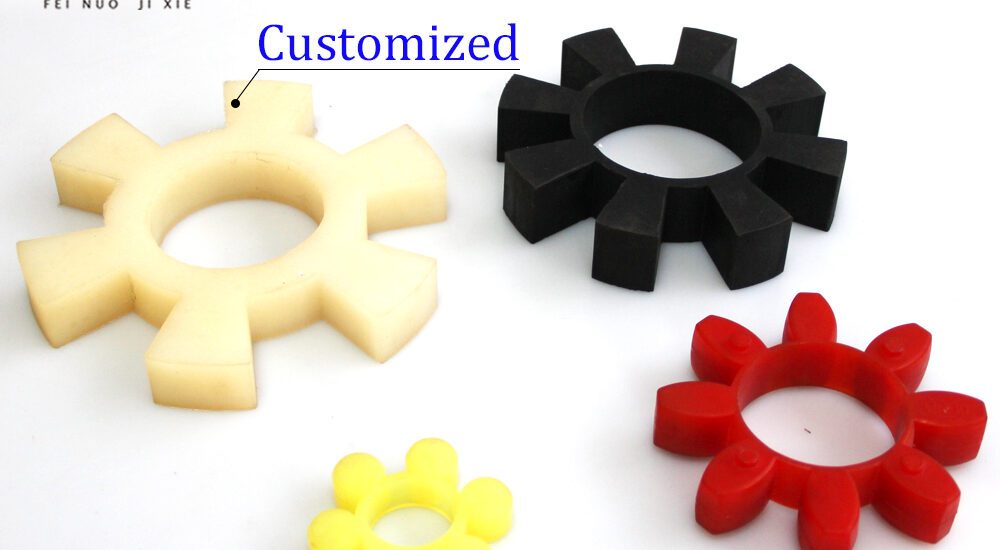
In the world of advanced manufacturing, PC ABS injection moulding has emerged as a game-changer, offering unmatched durability, strength, and performance. This innovative material combines the best properties of polycarbonate (PC) and acrylonitrile butadiene styrene (ABS), making it ideal for applications where toughness and impact resistance are critical.
From automotive components to high-end consumer electronics, PC ABS injection moulding is widely used to create products that withstand mechanical stress, heat, and environmental conditions. Its versatility and superior mechanical properties have made it a preferred choice across various industries.
This article delves deep into the science, process, benefits, and applications of PC ABS injection moulding, revealing why it is the secret behind some of the most durable and high-performance parts in modern manufacturing.
Understanding PC ABS: The Perfect Blend of Strength and Flexibility
PC ABS is a unique thermoplastic blend that brings together the best attributes of its two primary components: polycarbonate (PC) and acrylonitrile butadiene styrene (ABS). PC contributes excellent heat resistance, impact strength, and rigidity, while ABS enhances processability, toughness, and affordability. The result is a material that offers superior mechanical properties compared to standard plastics.
This blend is particularly valuable in PC ABS injection moulding, as it ensures parts with high impact resistance, dimensional stability, and an excellent surface finish. Additionally, PC ABS can be easily customized with additives to improve UV resistance, flame retardancy, and weatherability, making it suitable for both indoor and outdoor applications.
The Injection Moulding Process: How PC ABS is Transformed into High-Quality Parts
The PC ABS injection moulding process follows a precise sequence to ensure optimal product quality. It involves several critical steps:
-
Material Preparation – PC ABS pellets are pre-dried to eliminate moisture, which can cause defects such as bubbling or warping.
-
Injection – The molten PC ABS material is injected into a mould cavity under high pressure to form the desired shape.
-
Cooling and Solidification – The part is rapidly cooled to maintain structural integrity and prevent deformation.
-
Ejection – Once solidified, the part is ejected from the mould for further processing, such as trimming or finishing.
To achieve the best results in PC ABS injection moulding, manufacturers must carefully control processing parameters such as temperature, pressure, and cooling time. This ensures consistent part quality, reduces defects, and maximizes efficiency.
Advantages of PC ABS Injection Moulding Over Other Materials
PC ABS stands out among other thermoplastics due to its exceptional balance of strength, flexibility, and heat resistance. Some of its key advantages include:
-
Superior impact resistance – PC ABS parts can absorb high levels of stress without cracking or breaking.
-
Excellent heat resistance – The material withstands elevated temperatures better than standard ABS.
-
Enhanced chemical resistance – It resists degradation from exposure to oils, fuels, and household chemicals.
-
Outstanding surface quality – PC ABS injection moulding delivers parts with smooth finishes, making them ideal for aesthetic applications.
-
Ease of customization – The material can be modified with additives for additional properties like flame retardancy or UV resistance.
These benefits make PC ABS injection moulding an ideal choice for industries that demand both durability and aesthetic appeal.
Applications of PC ABS Injection Moulding in Different Industries
Thanks to its high-performance characteristics, PC ABS injection moulding is widely used across multiple industries:
-
Automotive – PC ABS is used for durable and heat-resistant components such as dashboards, interior trims, and structural parts.
-
Electronics – The material provides high-impact casings for smartphones, laptops, and medical devices.
-
Aerospace – Its lightweight yet strong nature makes it suitable for aircraft components.
-
Consumer Goods – PC ABS is found in power tools, household appliances, and protective gear.
Each of these applications benefits from the strength, thermal stability, and aesthetic versatility of PC ABS injection moulding.
Key Factors to Consider When Moulding PC ABS
To ensure the highest quality in PC ABS injection moulding, manufacturers must consider several key factors:
-
Material Drying – PC ABS is hygroscopic, meaning it absorbs moisture. Proper drying (typically at 80-100°C for 2-4 hours) is essential to prevent defects.
-
Injection Temperature – A typical range of 230-270°C ensures smooth material flow and prevents degradation.
-
Mould Temperature – Keeping the mould at 60-80°C improves surface finish and dimensional stability.
-
Injection Speed – A moderate speed prevents burn marks while ensuring full cavity filling.
-
Cooling Time – Proper cooling avoids warping and maintains the part’s mechanical integrity.
By optimizing these parameters, manufacturers can achieve consistent and high-quality results in PC ABS injection moulding.
How to Ensure High-Quality PC ABS Injection Moulding
To maximize the benefits of PC ABS injection moulding, companies must follow best practices, including:
-
Precision mould design – Well-designed moulds reduce defects and improve production efficiency.
-
Use of high-quality additives – Enhancements like UV stabilizers and flame retardants extend the lifespan of the final product.
-
Strict quality control measures – Regular inspections help identify issues early and maintain consistency in production.
By adhering to these guidelines, manufacturers can ensure their PC ABS injection moulding processes produce reliable and durable parts.
Future Trends in PC ABS Injection Moulding
As industries evolve, PC ABS injection moulding continues to advance with new trends shaping the future:
-
Innovations in moulding technology – Advanced automation and AI-driven quality control are improving efficiency and reducing waste.
-
Sustainable practices – The industry is moving towards more eco-friendly materials and recycling processes.
-
Growing demand for lightweight, high-strength materials – Industries such as automotive and aerospace are increasingly relying on PC ABS for its durability and weight-saving properties.
With these advancements, PC ABS injection moulding will remain at the forefront of modern manufacturing.
Why PC ABS Injection Moulding is the Future of Durable Manufacturing
PC ABS has revolutionized the way manufacturers produce high-performance parts, offering an exceptional balance of strength, flexibility, and thermal resistance. The PC ABS injection moulding process ensures that products are not only durable but also aesthetically refined and cost-effective.
As industries continue to demand materials that combine toughness, versatility, and sustainability, PC ABS injection moulding will remain a leading solution for manufacturing superior-quality components. By optimizing moulding techniques and embracing technological innovations, manufacturers can unlock the full potential of this remarkable material.