- March 27, 2025
- Posted by: feinuojixie
- Category: Injection Molding News
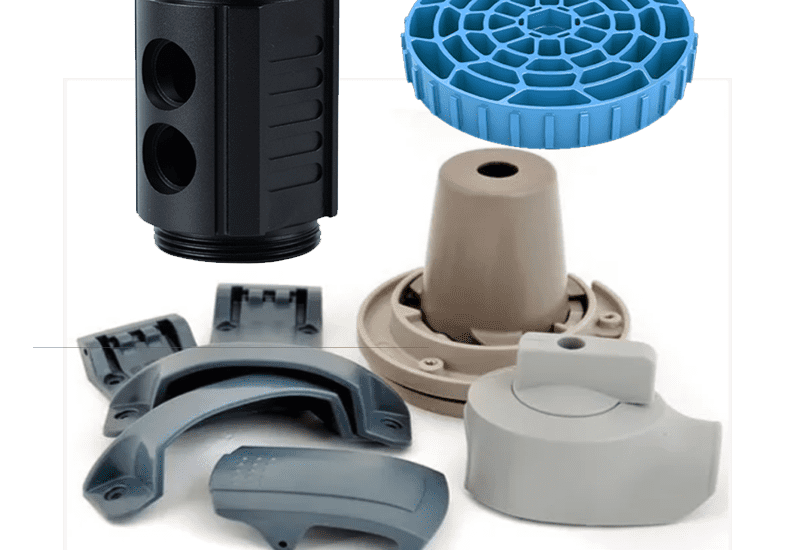
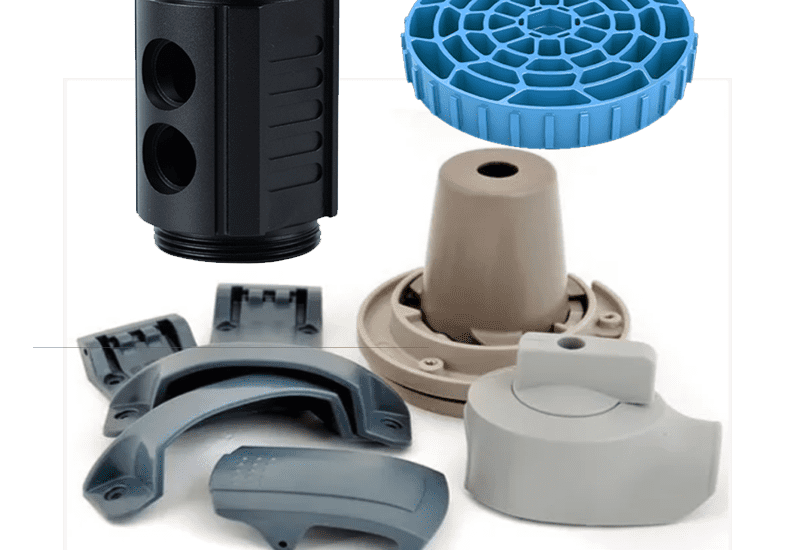
PC ABS injection moulding is a highly versatile and efficient manufacturing process that plays a crucial role in various industries. By combining the properties of polycarbonate (PC) and acrylonitrile butadiene styrene (ABS), this process delivers durable, heat-resistant, and aesthetically pleasing components. Whether for automotive parts, consumer electronics, or industrial equipment, PC ABS injection moulding provides a balance of strength and flexibility, making it a preferred choice for manufacturers worldwide. This guide explores the advantages, applications, and key considerations of PC ABS injection moulding to help you understand its full potential.
Understanding PC ABS Injection Moulding
PC ABS injection moulding involves melting and injecting a blend of polycarbonate and ABS into a mould cavity to create precise and high-quality components. The combination of these materials results in a product that offers impact resistance, thermal stability, and excellent mechanical properties. This process is widely used in industries that require strong yet lightweight materials for their products.
The Advantages of PC ABS Injection Moulding
One of the biggest benefits of PC ABS injection moulding is its exceptional durability. The material’s impact resistance ensures that moulded parts can withstand mechanical stress without breaking. Additionally, its high heat resistance makes it suitable for applications exposed to extreme temperatures. The superior surface finish of PC ABS allows for enhanced aesthetics, while its ease of processing provides design flexibility, enabling manufacturers to create complex shapes with precision.
Applications of PC ABS Injection Moulding
PC ABS injection moulding is extensively used across multiple industries due to its excellent balance of strength and versatility. In the automotive sector, it is used for durable and lightweight components such as dashboards, trims, and structural parts. Consumer electronics benefit from PC ABS in the form of robust casings and enclosures for devices like smartphones and laptops. The medical industry also relies on this material for producing safe and reliable equipment. Additionally, industrial machinery manufacturers use PC ABS for functional parts that require strength and impact resistance.
The PC ABS Injection Moulding Process
The process of PC ABS injection moulding starts with material preparation, where the plastic blend is dried to remove moisture. The next step is mould design and prototyping, ensuring precise dimensions and functionality. During the injection moulding phase, the material is melted, injected into a mould, cooled, and finally ejected as a finished part. Post-processing steps such as trimming and quality control checks help refine the final product to meet industry standards.
Key Considerations for PC ABS Injection Moulding
To achieve optimal results in PC ABS injection moulding, manufacturers must consider factors like mould temperature, injection pressure, and cooling time. Avoiding common defects such as warping and shrinkage requires precise control over these variables. Additionally, selecting the right grade of PC ABS and incorporating additives or fillers can enhance the material’s performance for specific applications.
Comparing PC ABS Injection Moulding with Other Materials
Compared to pure ABS, PC ABS offers superior heat resistance and strength. When contrasted with polycarbonate, PC ABS provides better cost-effectiveness and increased flexibility. In comparison to nylon, PC ABS stands out for its balanced mechanical properties, making it suitable for a wide range of applications.
Cost and Sustainability of PC ABS Injection Moulding
Production costs for PC ABS injection moulding depend on factors such as material selection, mould complexity, and production volume. Manufacturers can reduce costs by optimizing the design and minimizing material waste. From a sustainability perspective, PC ABS can be recycled, making it an environmentally friendly option compared to non-recyclable plastics.
Future Trends in PC ABS Injection Moulding
Advancements in material formulations continue to improve the properties of PC ABS, making it more resistant to heat, impact, and chemicals. Injection moulding technology is also evolving, with automation and AI playing a crucial role in enhancing production efficiency and reducing defects. As the demand for high-performance plastics grows, PC ABS injection moulding is expected to remain a dominant force in manufacturing.
Conclusion
PC ABS injection moulding is a powerful manufacturing technique that combines the strengths of two versatile materials. Its durability, heat resistance, and design flexibility make it an ideal choice for industries ranging from automotive to medical devices. By understanding the benefits, applications, and key considerations of PC ABS injection moulding, manufacturers can make informed decisions and leverage this technology for superior product development.