- March 31, 2025
- Posted by: feinuojixie
- Category: Injection Molding News
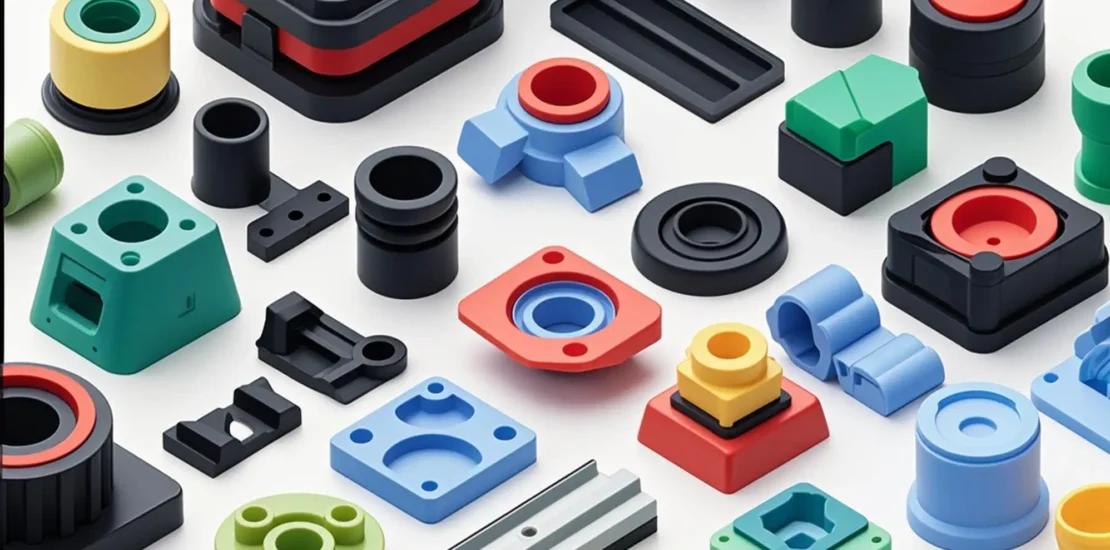
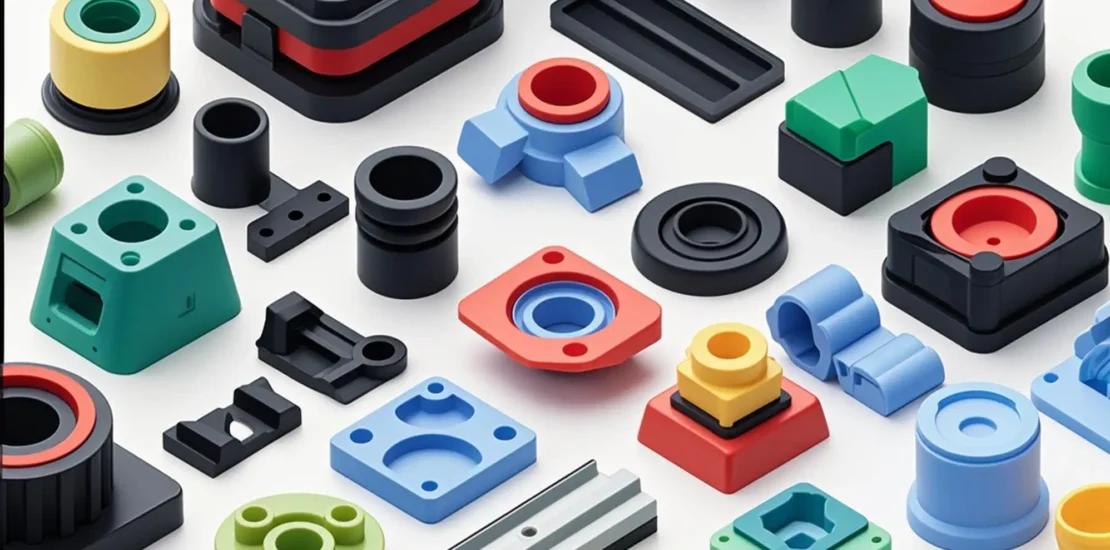
Selecting the right plastic material for injection moulding is a crucial decision that impacts the durability, functionality, and cost of the final product. Among the many options available, PC ABS injection moulding has emerged as a preferred choice due to its unique combination of strength, impact resistance, and thermal stability. However, how does it compare to other commonly used plastics? Understanding the advantages and limitations of PC ABS injection moulding in comparison to materials like ABS, polycarbonate, nylon, and polypropylene can help manufacturers make informed decisions for their specific applications.
Understanding PC ABS Injection Moulding
PC ABS is a blend of polycarbonate (PC) and acrylonitrile butadiene styrene (ABS), combining the best properties of both materials. It offers high impact resistance, excellent mechanical strength, and enhanced thermal stability, making it a versatile choice for various industries. PC ABS injection moulding is widely used in the automotive sector for interior and exterior components, in electronics for durable casings, and in consumer goods requiring both resilience and aesthetic appeal.
How PC ABS Injection Moulding Compares to Other Plastics
While PC ABS offers a unique set of benefits, it is essential to compare it with other popular plastics used in injection moulding to determine the best material for specific applications.
PC ABS vs. ABS Injection Moulding: Strength and Heat Resistance
ABS is known for its affordability and ease of processing, making it a common choice for consumer products. However, PC ABS injection moulding surpasses ABS in terms of heat resistance and mechanical strength, making it a better option for high-performance applications.
PC ABS vs. Polycarbonate Injection Moulding: Impact Resistance and Flexibility
Polycarbonate is highly durable and offers superior impact resistance, making it ideal for applications requiring extreme toughness. However, PC ABS provides a balance between strength and flexibility, making it easier to process while maintaining high impact resistance.
PC ABS vs. Nylon Injection Moulding: Moisture Resistance and Wear Performance
Nylon is often chosen for applications requiring wear resistance and low friction. However, it is highly sensitive to moisture absorption, which can affect its mechanical properties. PC ABS injection moulding, on the other hand, provides consistent performance without being affected by humidity or moisture.
PC ABS vs. Polypropylene Injection Moulding: Cost and Chemical Resistance
Polypropylene is a cost-effective material known for its excellent chemical resistance. However, it lacks the structural integrity and impact resistance of PC ABS injection moulding, making it less suitable for applications requiring durability under mechanical stress.
Applications of PC ABS Injection Moulding
Due to its superior properties, PC ABS is widely used in various industries. Common applications include:
- Automotive: Dashboard panels, bumpers, and structural components
- Electronics: Laptop housings, smartphone casings, and durable enclosures
- Medical Devices: Equipment housings and protective gear
- Consumer Goods: High-impact tools, helmets, and household appliances
Advantages of PC ABS Injection Moulding
The benefits of using PC ABS injection moulding include:
- High impact resistance and durability
- Improved heat resistance compared to ABS
- Superior processing flexibility compared to polycarbonate
- Excellent balance of strength and aesthetics
Potential Limitations of PC ABS Injection Moulding
Despite its many advantages, PC ABS also has some limitations:
- Higher cost compared to basic plastics like ABS and polypropylene
- Requires precise processing conditions to optimize performance
Choosing the Right Material for Your Injection Moulding Project
When selecting a material for injection moulding, consider factors such as mechanical properties, environmental conditions, cost, and processing requirements. PC ABS injection moulding is ideal for applications that require a balance of durability, heat resistance, and aesthetic quality.
Conclusion
PC ABS stands out as a highly versatile and reliable material for injection moulding, offering superior strength, impact resistance, and thermal stability. While other plastics may be more cost-effective or specialized for certain conditions, PC ABS injection moulding remains an excellent choice for manufacturers seeking a high-performance material. By understanding the differences between PC ABS and other plastics, businesses can make the best decision for their specific needs and applications.