- May 3, 2025
- Posted by: feinuojixie
- Category: Injection Molding News
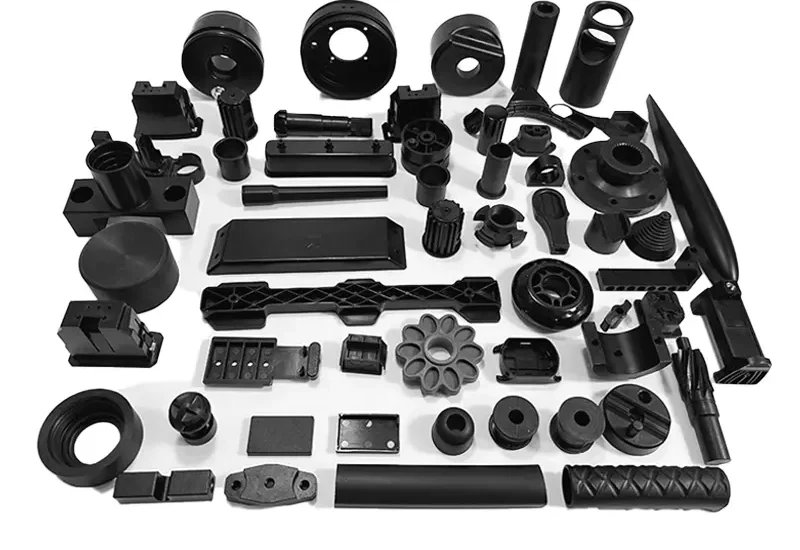
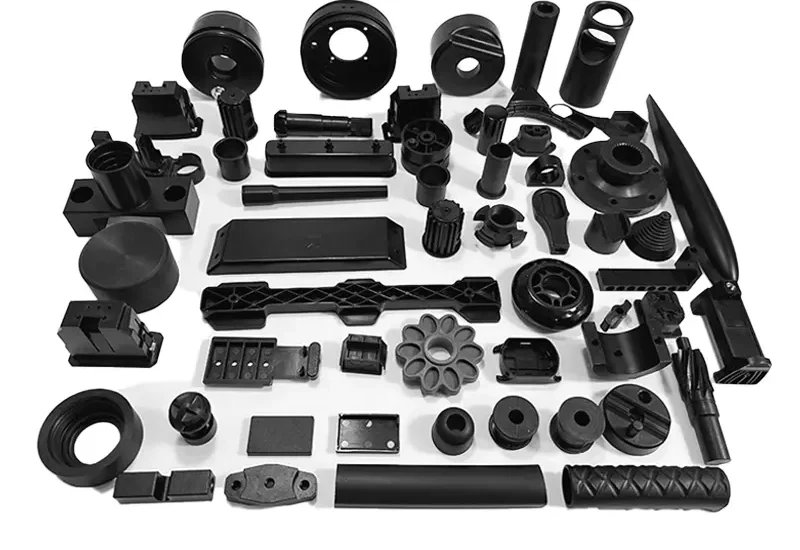
Plastic injection molded parts have become a cornerstone of modern manufacturing, playing a pivotal role in industries ranging from automotive to medical. This versatile production method offers a range of benefits, including precision, efficiency, and cost-effectiveness, which is why it continues to grow in popularity. Whether you’re looking to create a simple component or a complex, multi-functional part, plastic injection molding can provide a solution that meets both performance and budgetary requirements.
In today’s competitive manufacturing landscape, companies are constantly searching for ways to optimize production while maintaining high quality. Plastic injection molding offers just that: a streamlined, reliable process that delivers durable, precise products at scale. This blog will delve into why plastic injection molded parts are crucial to achieving these goals, offering insights into their benefits, applications, and the challenges that come with their production.
What is a Plastic Injection Molded Part?
Plastic injection molded parts are created through a process in which molten plastic is injected into a precisely shaped mold. The material cools and solidifies, taking the form of the mold cavity. This method allows for high precision and the ability to produce parts with intricate details that would be difficult or costly to achieve with other manufacturing techniques.
The process begins with selecting the appropriate material, often thermoplastic resins like ABS, polycarbonate, or polypropylene, depending on the desired properties of the final product. Once the material is chosen, it is heated to a molten state and injected into the mold under high pressure. After cooling, the part is removed from the mold, and any excess material is trimmed away. The result is a part that can be used in various applications, ranging from everyday consumer goods to highly specialized industrial products.
Benefits of Plastic Injection Molded Part
Plastic injection molded parts are known for their durability and cost-effectiveness, which make them an attractive option for mass production. Let’s explore these benefits in detail:
-
Durability: One of the primary advantages of plastic injection molded parts is their durability. The injection molding process produces parts that are strong and resilient, able to withstand a range of environmental conditions and mechanical stresses. Whether it’s exposure to heat, chemicals, or physical impact, these parts are designed to last, reducing the need for frequent replacements and repairs.
-
Cost-effectiveness: Plastic injection molding is considered one of the most economical manufacturing methods, especially for large-volume production. Once the initial mold is created, it can be used to produce thousands or even millions of identical parts. This reduces per-part costs significantly, making it ideal for industries that require high quantities of components. Additionally, the efficiency of the process minimizes waste, further lowering production costs.
Applications of Plastic Injection Molded Part in Various Industries
Plastic injection molded parts are used across a wide range of industries, each benefiting from the strength, precision, and cost savings the method offers. Some notable applications include:
-
Automotive: The automotive industry is one of the largest consumers of plastic injection molded parts. Components like dashboard panels, exterior trim, and under-the-hood parts are often made using this technique. The ability to produce lightweight yet durable parts has been key in reducing vehicle weight and improving fuel efficiency.
-
Medical: Precision and safety are paramount in the medical field. Plastic injection molded parts are commonly used in medical devices such as syringes, diagnostic tools, and implantable devices. The process allows for the creation of highly detailed and sterile parts, which are critical for patient safety and the effectiveness of medical treatments.
-
Consumer Electronics: Modern consumer electronics demand lightweight, durable, and precise components. From smartphone housings to connectors and buttons, plastic injection molded parts provide the reliability and design flexibility needed for these devices. The ability to integrate multiple features into a single part also enhances the functionality of electronics while keeping costs low.
The Precision of Plastic Injection Molded Parts
One of the defining characteristics of plastic injection molded parts is their precision. The process is capable of producing parts with tight tolerances, ensuring that each component is consistent in size and shape. This level of precision is essential for industries such as aerospace, where even the smallest deviation can result in significant performance issues.
For applications requiring high accuracy, molds can be engineered to achieve extremely precise measurements. The result is parts that fit perfectly within larger assemblies, ensuring smooth operation and eliminating the need for extensive post-production adjustments. This level of quality control contributes to the overall efficiency of the manufacturing process, reducing time and cost.
Sustainability in Plastic Injection Molding
In recent years, sustainability has become a key consideration in manufacturing processes, and plastic injection molding is no exception. There are several ways in which this method contributes to more sustainable production:
-
Reducing waste: The injection molding process is highly efficient, with minimal material waste. The design of the mold ensures that only the exact amount of plastic needed for each part is used. Additionally, excess plastic can often be recycled and reused in future production runs, reducing overall material consumption.
-
Recyclable and biodegradable materials: As consumer demand for eco-friendly products grows, the injection molding industry is shifting toward using more sustainable materials. Biodegradable plastics and recyclable resins are increasingly being used, helping reduce the environmental impact of plastic production. These innovations align with global efforts to reduce plastic waste and promote circular economies.
Common Challenges in Plastic Injection Molding and How to Overcome Them
While plastic injection molding offers numerous advantages, it also comes with some challenges. Here are some common issues and strategies to overcome them:
-
Defects: Common defects in injection molded parts include warping, sink marks, and flash. These can be caused by factors like uneven cooling, incorrect mold design, or improper injection speed. To minimize defects, it’s essential to optimize mold design, control the cooling process, and fine-tune injection parameters.
-
Design considerations: To achieve the best possible results, parts need to be designed with injection molding in mind. Features like thin walls or complex geometries can complicate the molding process. Working closely with engineers during the design phase to ensure the part is mold-friendly can save time and money in the long run.
Why Plastic Injection Molded Part is the Future of Manufacturing
Plastic injection molded parts are undoubtedly a critical part of modern manufacturing. With their unmatched durability, cost-effectiveness, and precision, they offer solutions across a wide range of industries. The continuous advancements in materials and techniques only enhance their relevance in the ever-evolving manufacturing landscape.
As industries look to innovate and streamline their production processes, plastic injection molded parts remain at the forefront of design and manufacturing solutions. The ability to produce high-quality, cost-efficient parts on a large scale positions plastic injection molding as a key driver in the future of manufacturing. Whether you’re producing automotive components, medical devices, or consumer electronics, the versatility and reliability of plastic injection molded parts are sure to meet your needs and propel your business forward.