- April 10, 2025
- Posted by: feinuojixie
- Category: Injection Molding News
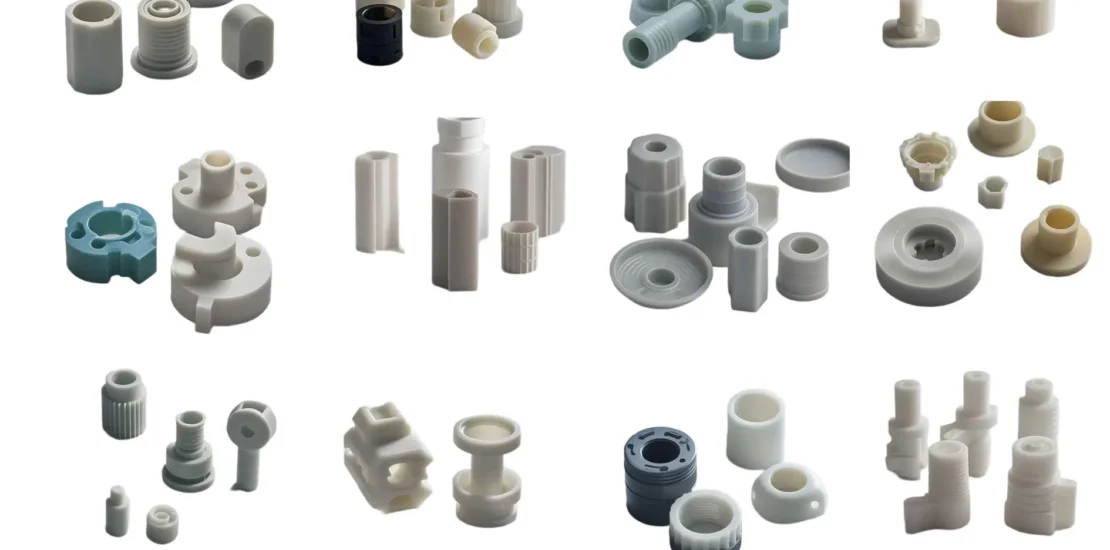
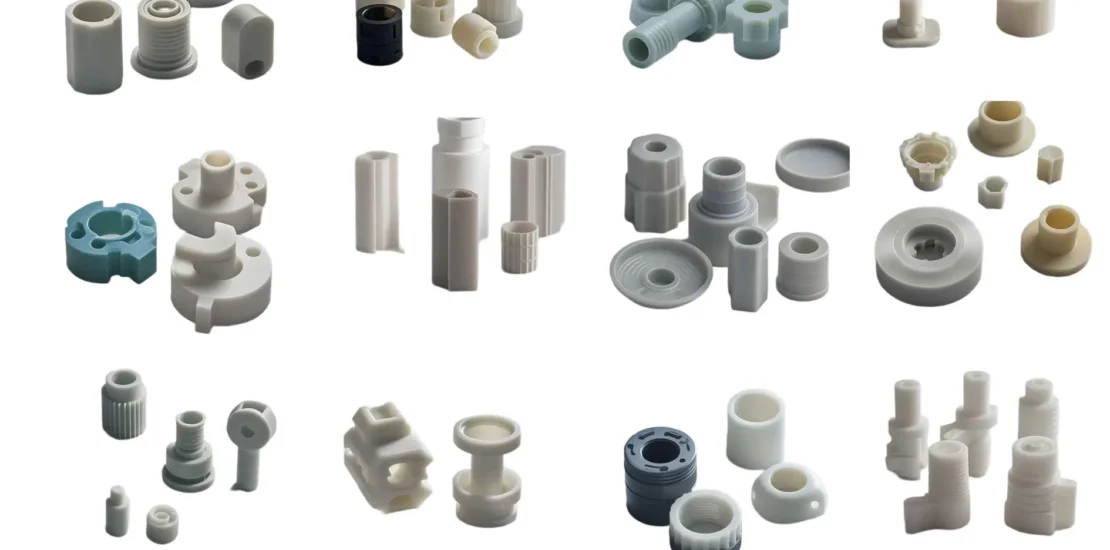
In a world driven by performance, precision, and innovation, plastic injection molding part plays a vital yet often overlooked role. From the sleek dashboard components in your car to the durable housings in your smartphone, these parts quietly power the functionality and quality of the products we rely on every day. Their strength lies in their ability to be precisely engineered, mass-produced, and customized to meet the demands of countless applications. As industries push the boundaries of technology, the need for reliable, cost-efficient, and high-performance components has never been greater—making plastic injection molding part an essential ingredient in the recipe for success.
The Basics of Plastic Injection Molding Parts
Plastic injection molding is a manufacturing process used to produce parts by injecting molten plastic into a mold. The process starts with raw plastic resin, which is melted and then forced into a steel or aluminum mold cavity under high pressure. Once the plastic cools and solidifies, it takes the shape of the mold and is ejected as a finished part.
What makes plastic injection molding part so valuable is the ability to create highly detailed and complex components with tight tolerances. The molds themselves can be custom-designed for virtually any shape or feature, allowing for incredible design freedom and precision. This method is ideal for producing high volumes of parts quickly and efficiently without compromising on quality.
Key Industries Relying on Plastic Injection Molding Parts
The versatility and performance of plastic injection molding part make it indispensable across many industries. In the automotive sector, it’s used for interior panels, engine components, and lighting systems. Medical device manufacturers depend on it for sterile, safe, and precise parts such as syringes, surgical instruments, and housing for diagnostic equipment.
In the world of electronics, plastic injection molding part helps create lightweight and durable enclosures, connectors, and circuit board components. Even in consumer goods—from kitchen appliances to toys—these parts ensure consistent performance, long-lasting durability, and sleek aesthetics. Each industry benefits from the cost savings, customization, and mechanical strength that injection molded parts offer.
Design Flexibility: The Advantage of Plastic Injection Molding Parts
One of the standout advantages of plastic injection molding part is its design flexibility. Unlike traditional manufacturing methods, this process supports intricate geometries, undercuts, and multi-part assemblies in a single mold. That means engineers can consolidate several parts into one, reducing the need for additional fasteners or assembly steps.
This level of flexibility not only simplifies manufacturing but also improves the final product’s strength and efficiency. Whether it’s adding textured finishes, branding details, or custom colors, plastic injection molding enables high customization without increasing production complexity.
Material Selection: Optimizing the Performance of Plastic Injection Molding Parts
The performance of any plastic injection molding part depends heavily on the type of resin selected. Each material brings unique properties—such as strength, flexibility, chemical resistance, or heat tolerance—that can be matched to the intended application.
Common options include ABS for toughness, polycarbonate for impact resistance, and polypropylene for chemical durability. Engineers can also choose from high-performance polymers or reinforced plastics with glass or carbon fibers. The ability to tailor material choice gives manufacturers an edge in achieving optimal functionality and cost-effectiveness.
Precision and Consistency in Plastic Injection Molding Parts
When precision is non-negotiable, plastic injection molding part delivers. The process is highly repeatable, ensuring that each part matches the exact specifications of the original design, even in mass production. This consistency is critical in industries like aerospace and healthcare, where performance and safety are paramount.
Advanced molding machines and quality control systems help monitor variables like temperature, pressure, and cycle time, minimizing defects and variations. The result is a consistently reliable product with tight dimensional accuracy, batch after batch.
Cost-Effectiveness Without Compromising Quality
Despite its advanced capabilities, plastic injection molding part is remarkably cost-effective—especially at scale. Once the mold is developed, the cost per part drops significantly due to the speed and efficiency of the process. This makes it ideal for high-volume production runs where uniformity and durability are key.
In addition to its low labor and material waste, the process also allows for automation, further reducing costs. By delivering high-performance results at a competitive price, plastic injection molding strikes the perfect balance between quality and economy.
Sustainability and the Future of Plastic Injection Molding Parts
As the world shifts toward greener manufacturing practices, the plastic injection molding industry is evolving too. Today, many manufacturers are using recyclable or biodegradable plastics, reducing energy consumption, and optimizing mold designs to minimize waste.
Additionally, innovations like closed-loop recycling systems and bio-based polymers are helping to lower the environmental footprint of each plastic injection molding part. As demand for sustainable products increases, this process will continue to adapt, offering both performance and planet-friendly solutions.
Choosing the Right Manufacturer for Plastic Injection Molding Parts
Not all plastic injection molding manufacturers are created equal. When selecting a partner, it’s important to consider factors such as in-house engineering support, mold design expertise, material knowledge, and quality certifications like ISO 9001 or IATF 16949.
A reliable manufacturer should offer transparency, clear communication, and the ability to scale with your production needs. They should also invest in modern equipment and provide post-production services like assembly, packaging, and logistics. Choosing the right partner ensures that your plastic injection molding part meets expectations every time.
Conclusion: The Unsung Hero Behind High-Performance Products
Behind every high-performance product is a network of smart engineering and efficient manufacturing—and at the heart of it all is the plastic injection molding part. These components may be small, but their impact is massive. They enable innovation, drive down costs, and ensure quality in everything from medical devices to automotive systems.
Whether you’re a product developer, engineer, or business leader, understanding the power of plastic injection molding can help you unlock new levels of performance and efficiency. In a competitive world, it’s the details that make the difference—and plastic injection molding part is one detail you can’t afford to overlook.