- May 8, 2025
- Posted by: feinuojixie
- Category: Injection Molding News
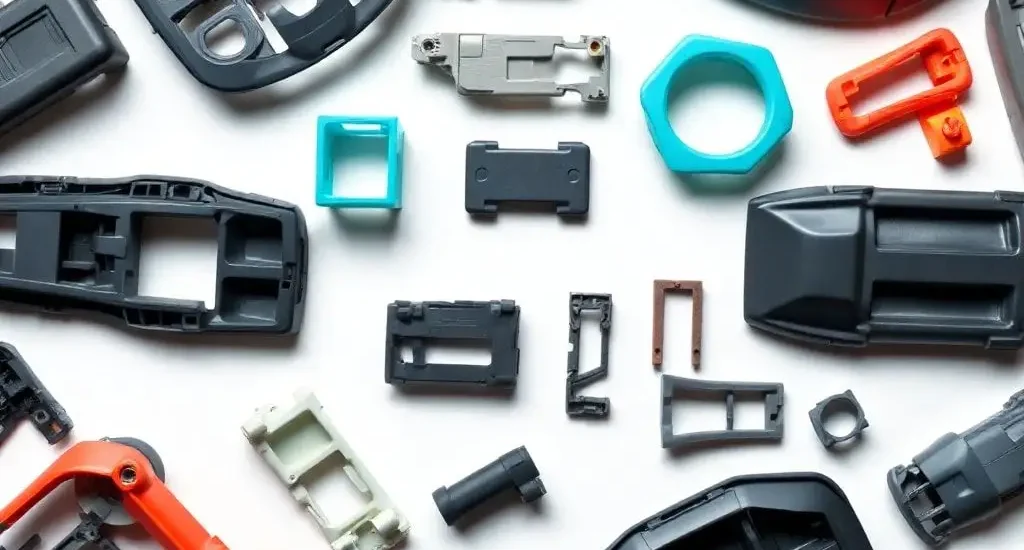
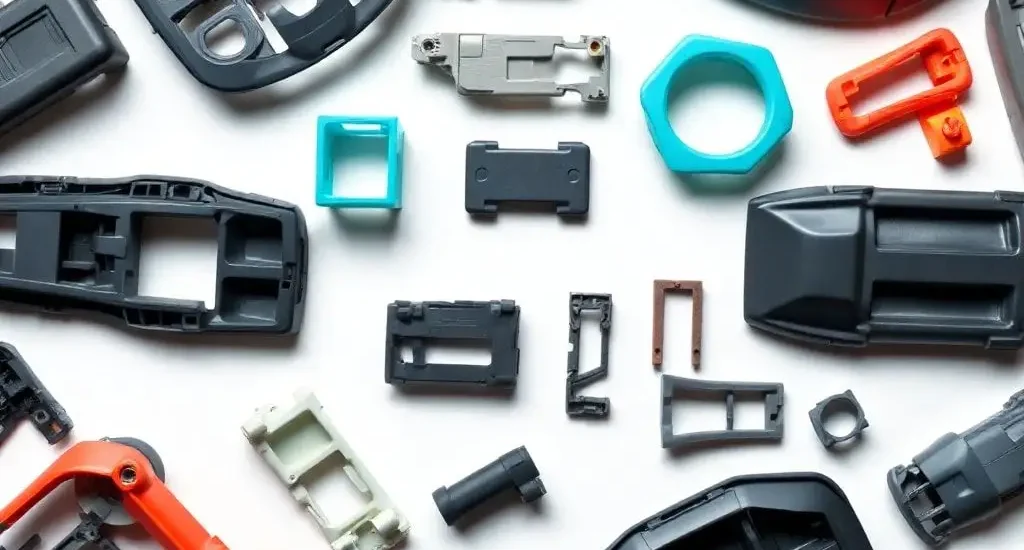
Plastic injection parts are everywhere—from the casing of your smartphone to the dashboard components in your car. These small but critical components drive innovation across consumer products, medical devices, industrial equipment, and more. As a buyer, whether you’re in procurement, engineering, or product development, understanding how these parts are made and what influences their cost, quality, and performance is essential.
Too often, purchasing decisions are made based solely on price or lead time, overlooking key factors like material suitability, tooling design, or manufacturing capabilities. This can lead to product failures, delays, or inflated costs down the line. By demystifying the basics of plastic injection parts, this guide aims to empower buyers with the knowledge needed to make smarter, more informed decisions—ultimately leading to better products and stronger supplier relationships.
What Are Plastic Injection Parts? A Simple Explanation for Buyers
Plastic injection parts are components created by injecting molten plastic into a precisely shaped mold, allowing it to cool and solidify into the desired form. This manufacturing process, known as injection molding, is favored for its speed, precision, and ability to produce complex shapes in high volumes.
For buyers, it’s important to recognize that every plastic injection part begins with two fundamentals: the mold and the material. The mold defines the part’s geometry, while the plastic determines its physical characteristics. This foundational understanding is critical for making informed decisions throughout the sourcing process.
Key Benefits of Choosing Plastic Injection Parts for Your Product
Plastic injection parts offer several compelling advantages that make them a popular choice across industries:
-
High efficiency for mass production: Once the mold is built, thousands—or even millions—of identical parts can be produced quickly.
-
Design flexibility: Intricate shapes, fine details, and internal features can be achieved with high accuracy.
-
Consistent quality: Each part produced is virtually identical, ideal for maintaining strict tolerances.
-
Low cost per unit: While initial tooling is expensive, the per-part cost drops significantly with higher volumes.
-
Material variety: A wide range of thermoplastics allows customization based on mechanical, thermal, and aesthetic requirements.
Understanding these benefits helps buyers align production capabilities with product needs.
Materials Matter: How to Choose the Right Plastic for Your Injection Parts
Material selection is one of the most important decisions when producing plastic injection parts. Each resin has unique properties that affect performance, durability, and cost. Commonly used plastics include:
-
ABS: Strong, lightweight, and impact-resistant—commonly used in consumer electronics.
-
Polypropylene (PP): Chemical-resistant and flexible—ideal for packaging and medical devices.
-
Polycarbonate (PC): High clarity and toughness—used in lenses and safety equipment.
-
Nylon (PA): Strong, wear-resistant—frequently used in gears and mechanical parts.
Buyers should consult with manufacturers to match the plastic to the part’s functional requirements, environmental conditions, and industry regulations.
The Design Phase: What Every Buyer Should Know Before Production
A successful plastic injection part begins with thoughtful design. Poor design choices can increase costs, cause defects, or prevent manufacturability altogether. Key design considerations include:
-
Wall thickness: Uniform thickness helps avoid warping and sink marks.
-
Draft angles: Slight tapers in vertical walls allow easy removal from the mold.
-
Ribs and gussets: These features strengthen parts without adding bulk.
-
Undercuts: Avoid where possible, as they complicate tooling and raise costs.
Buyers should work closely with design engineers to optimize the part before finalizing the mold.
Tooling Essentials: Understanding the Mold That Shapes Your Plastic Injection Part
The mold is the heart of the injection molding process. It is a custom-built tool, typically made from hardened steel or aluminum, that defines the shape and surface finish of the part. Key points buyers should understand:
-
Tooling cost is upfront and significant, especially for complex or multi-cavity molds.
-
Mold lifespan varies by material and maintenance, with steel molds typically outlasting aluminum.
-
Lead times for mold creation can range from weeks to months, so early planning is crucial.
Investing in high-quality tooling pays off in the long run with improved part quality and reduced downtime.
Quality Control: Ensuring Consistent and Reliable Plastic Injection Parts
Maintaining quality throughout production is essential. Reputable manufacturers implement strict quality control measures such as:
-
Dimensional inspections using calipers, CMMs, or laser scanning to ensure part accuracy.
-
Material certification to confirm resin specifications and traceability.
-
Process monitoring to track temperature, pressure, and cycle time consistency.
Buyers should request inspection reports and consider working with manufacturers certified under ISO or other industry standards.
Common Buyer Mistakes to Avoid When Ordering Plastic Injection Parts
Even experienced buyers can fall into common traps that affect product success. Watch out for these mistakes:
-
Vague or incomplete specifications: Always provide detailed drawings, tolerances, and surface finish requirements.
-
Underestimating lead time: Tooling, revisions, and sampling take time—plan accordingly.
-
Choosing the wrong material: Cutting costs with a lower-grade plastic can lead to part failure.
-
Ignoring mold ownership and maintenance terms: Clarify who owns the mold and who’s responsible for upkeep.
Avoiding these pitfalls protects your investment and ensures smooth production.
Cost Breakdown: What Influences the Price of Plastic Injection Parts
The price of a plastic injection part is influenced by several factors:
-
Material cost: Some resins are significantly more expensive than others.
-
Tooling complexity: More intricate molds require more time and expertise to build.
-
Part geometry and size: Larger or more detailed parts take longer to mold and cool.
-
Order volume: Higher quantities reduce the cost per unit.
-
Cycle time: Shorter molding cycles reduce manufacturing time and cost.
Understanding these cost drivers helps buyers make strategic decisions that balance quality and budget.
Working with a Manufacturer: What Buyers Should Ask and Expect
Choosing the right manufacturing partner is just as important as the part itself. Buyers should evaluate:
-
Experience in your industry: Look for manufacturers who understand your specific product needs.
-
In-house tooling and design capabilities: This speeds up iterations and problem-solving.
-
Communication and support: A responsive team can prevent issues before they arise.
-
Transparency in quotes and lead times: Make sure you get a full breakdown and realistic expectations.
Asking the right questions up front builds a foundation for long-term success.
Making Smart Decisions When Buying Plastic Injection Parts
Plastic injection parts are central to modern manufacturing, and smart sourcing decisions begin with knowledge. By understanding the process, materials, design factors, and supplier dynamics, buyers can avoid costly missteps and ensure their parts meet functional, quality, and financial goals.
Whether you’re launching a new product or optimizing an existing one, take the time to understand what goes into every plastic injection part. It’s not just a component—it’s a cornerstone of your product’s success.