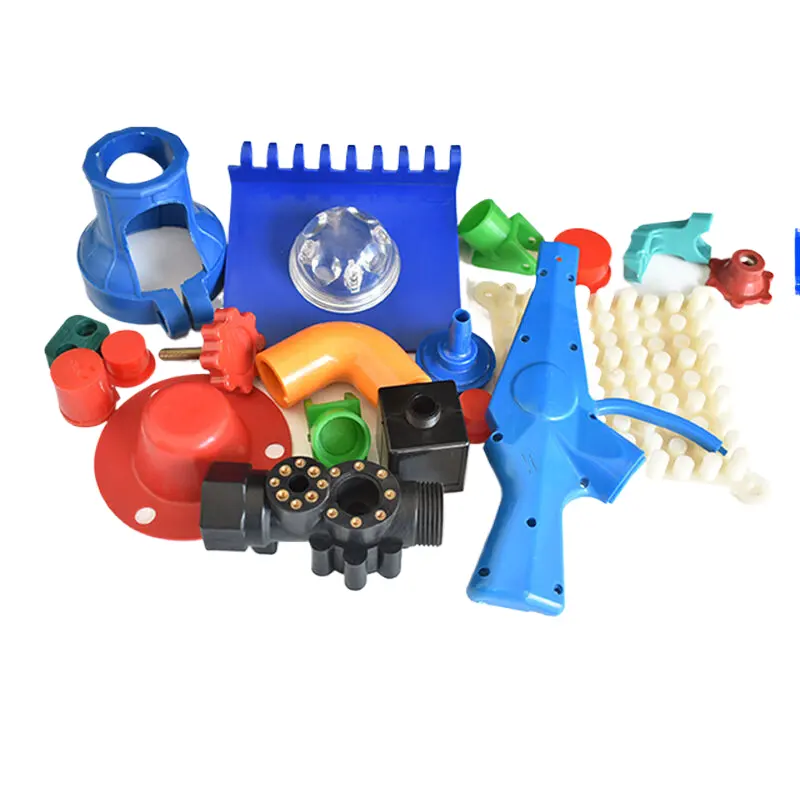
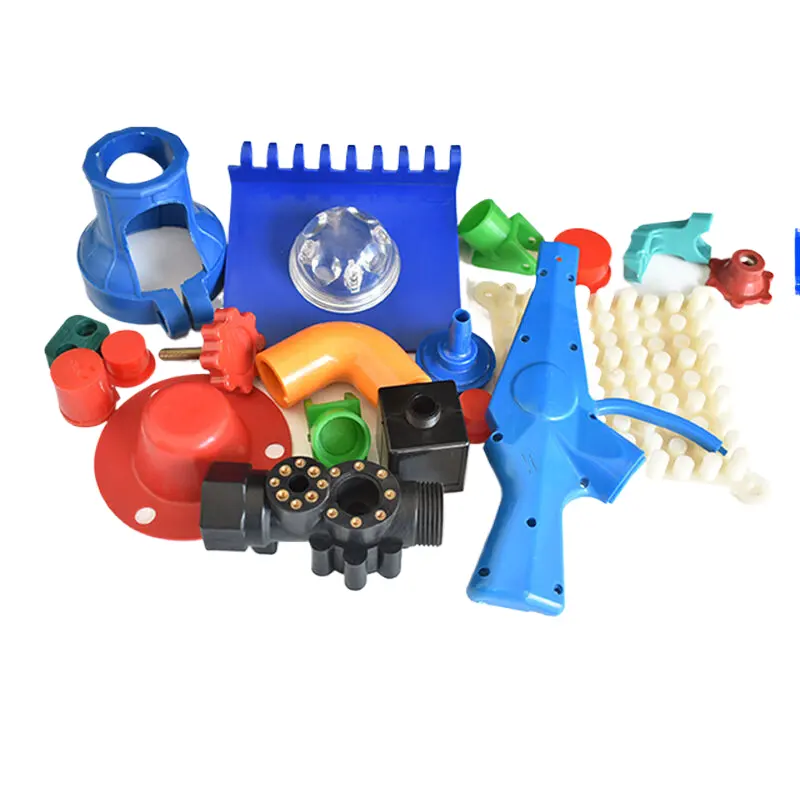
The Advantages of ABS Injection Moulding in Automotive Parts
ABS injection moulding offers numerous advantages that make it the go-to method for manufacturing automotive components. These benefits contribute significantly to the growing use of ABS in the industry.
Durability and Strength: Why ABS is Ideal for Automotive Applications
ABS is well-regarded for its ability to withstand high impact, making it perfect for automotive parts that need to endure collisions, weather elements, and daily wear. Its toughness allows it to maintain its structural integrity even in high-stress environments, ensuring parts are reliable and long-lasting. From bumpers to engine covers, ABS ensures safety and performance.
Cost-effectiveness and Efficiency of ABS Injection Moulding
The injection moulding process itself is highly efficient, allowing manufacturers to produce large quantities of parts in a relatively short amount of time. ABS is also cost-effective, providing a balance of price and performance. This allows automotive manufacturers to keep production costs down without compromising on the quality of the parts, making it an excellent choice for mass production.
About this product
Customized Solutions: Our company offers customized machining and manufacturing services for specialized plastic products, allowing customers to specify their desired material, color, and design for a tailored fit.
Wide Material Options: We support a variety of materials, including ABS, PA66, PP, PC, PMMA, PSU, PCTG, TPE, TPU, and PBT, ensuring that our products meet the specific requirements of our clients.
High-Quality Wear Resistance: Our plastic injection molding parts exhibit exceptional wear resistance, making them suitable for industrial applications where durability is crucial.
Support for Customization: Our products can be tailored to meet the unique needs of each customer, with support for customization of model numbers and designs.
Industrial-Grade Quality: Our products are manufactured using advanced plastic injection molding techniques, ensuring high-quality results that meet the expectations of industrial clients.
The ABS Injection Moulding Process for Automotive Parts
The process of ABS injection moulding is at the heart of producing high-quality automotive parts. Here’s a breakdown of how it works:
A Step-by-Step Guide to the Injection Moulding Process
The process begins with the preparation of ABS pellets, which are heated until they reach a molten state. This molten material is then injected into a mould under high pressure. Once the material fills the mould, it is allowed to cool and solidify, taking the shape of the part. The part is then ejected from the mould and undergoes quality checks before being sent for final assembly or finishing.
How ABS Material is Prepared and Injected into Moulds
ABS pellets are carefully fed into a hopper, where they are heated and melted by the machine’s barrel. The liquid ABS is injected into precisely designed moulds, which are created to match the specifications of the intended automotive part. The pressure forces the molten ABS to fill every corner of the mould, ensuring a perfect shape.
The Cooling and Solidification Process
Once the ABS is injected into the mould, the cooling process begins. The mould is cooled by circulating water or air around it, allowing the ABS to solidify. The cooling time varies depending on the part’s size and complexity. A key advantage of ABS is its quick cooling rate, which helps speed up production and reduces manufacturing costs.
Quality Control Measures During Production
Throughout the entire process, quality control measures are in place to ensure that the parts meet the stringent requirements of the automotive industry. Each part is inspected for defects such as warping, discoloration, or weak spots, which could compromise its performance. Advanced testing methods are used to check the durability, strength, and dimensions of each part, ensuring that only the highest-quality components make it to the final assembly.
There are no reviews yet.