- February 19, 2025
- Posted by: feinuojixie
- Category: Injection Molding News
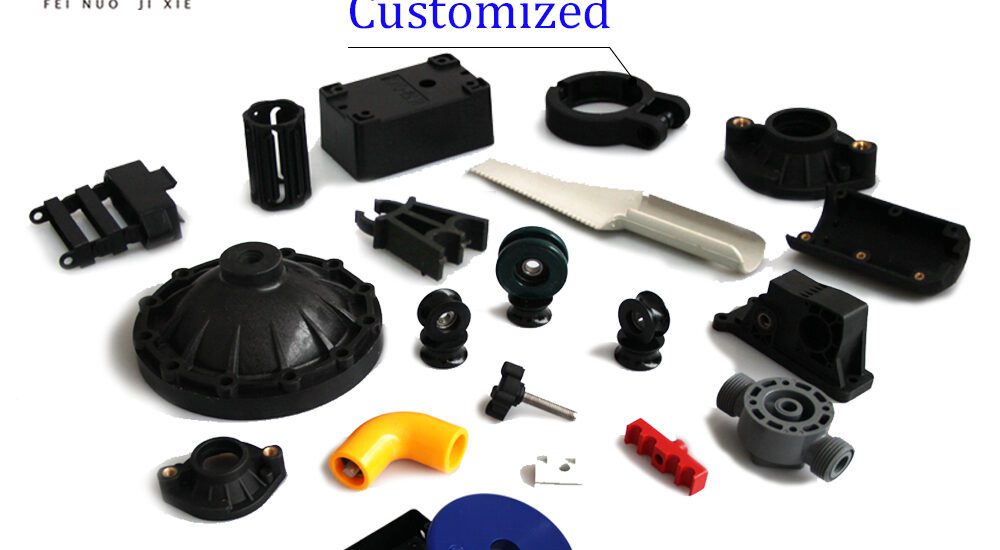
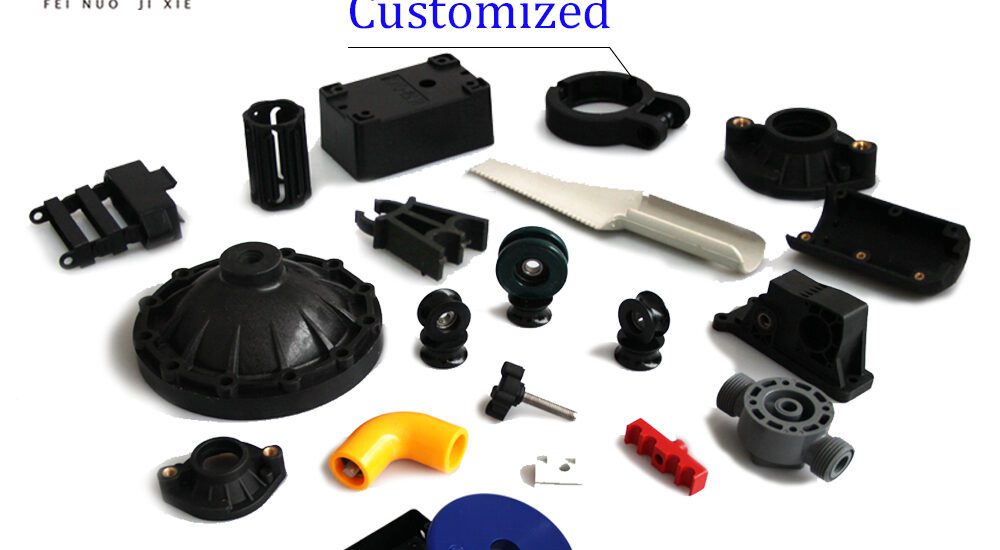
In the highly competitive world of product manufacturing, standing out is crucial. Custom injection molded parts have emerged as a game – changer, offering a plethora of opportunities for businesses to revolutionize their products. This article will delve deep into the realm of custom injection molded parts, exploring their significance, functionality, and the numerous benefits they bring to product development.
The Basics of Injection Molded Parts
Injection molding is a manufacturing process where molten material, typically plastic, is injected into a mold cavity. Once the material cools and solidifies, it takes the shape of the mold. Common materials used in injection molding include ABS, polypropylene, and polyethylene. Understanding these basic concepts is the foundation for appreciating the potential of custom injection molded parts.
The Power of Customization
One – size – fits – all solutions rarely work in product design. Custom injection molded parts allow manufacturers to tailor components to their exact needs. Whether it’s a unique shape, size, or functionality requirement, custom injection molding can meet those demands. This level of customization enables products to stand out in the market, providing a distinct competitive edge.
Cost – Efficiency and Injection Molded Parts
While the initial investment in mold creation for custom injection molded parts may seem high, in the long run, it proves to be highly cost – effective. Mass production using injection molding significantly reduces the per – unit cost. Additionally, the precision of the process minimizes material waste, further contributing to cost savings over large – scale production runs.
Design Flexibility
Custom injection molded parts offer unparalleled design flexibility. Complex geometries, intricate details, and unique aesthetics can be achieved with relative ease. This flexibility empowers designers to bring their most innovative ideas to life, creating products that are not only functional but also visually appealing.
Quality Assurance
Quality is non – negotiable in product manufacturing. Custom injection molding processes are highly controlled, ensuring consistent quality across every part produced. The use of high – quality materials and advanced manufacturing techniques results in parts that are durable, reliable, and meet the strictest industry standards.
Case Studies
Real – world examples speak volumes. Let’s look at a few case studies. Company A, a consumer electronics firm, used custom injection molded parts to create a sleek and ergonomic smartphone case. This not only enhanced the product’s appearance but also improved its grip and durability. Company B, in the automotive industry, utilized custom injection molded parts to reduce the weight of their vehicle components while maintaining strength, leading to better fuel efficiency.
How to Get Started
If you’re convinced of the benefits of custom injection molded parts and want to incorporate them into your product development, the first step is to find a reliable injection molding supplier. Look for a company with a proven track record, advanced equipment, and a team of experienced engineers. Then, work closely with them to define your design requirements, select the right materials, and start the prototyping process.
Conclusion
Custom injection molded parts are more than just manufacturing components; they are the key to revolutionizing your products. From cost – efficiency and design flexibility to quality assurance and product differentiation, the advantages are clear. Don’t miss out on the opportunity to take your products to the next level. Embrace custom injection molded parts today and stay ahead in the competitive market.