- February 21, 2025
- Posted by: feinuojixie
- Category: Injection Molding News
No Comments
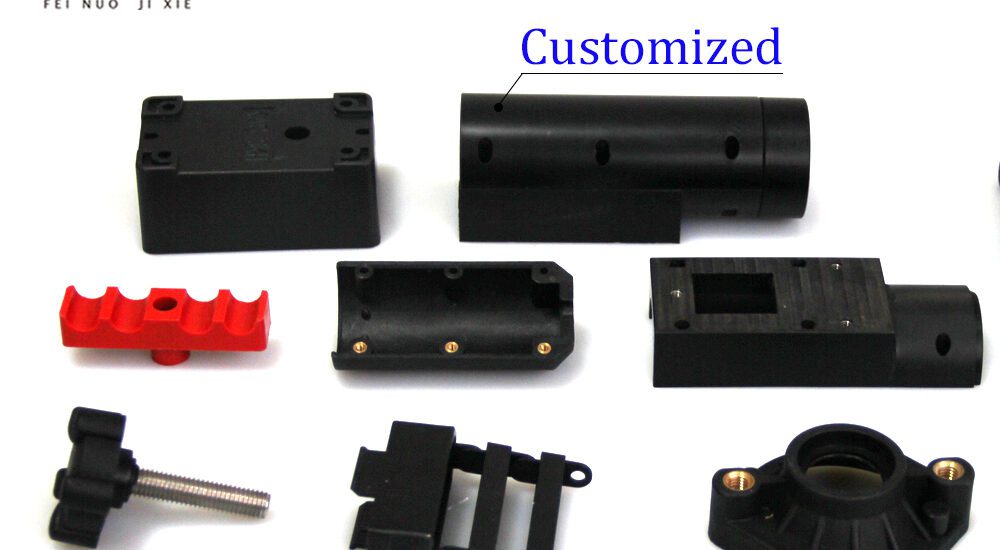
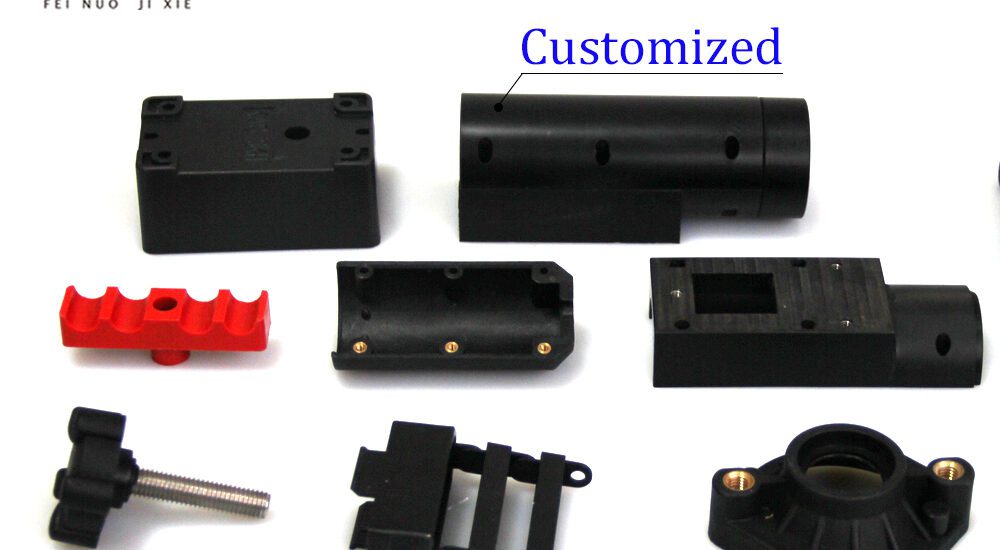
In the highly competitive world of product manufacturing, standing out and achieving innovation is no easy feat. However, there’s a powerful tool that can make a significant difference – custom injection molded parts. These parts have the potential to transform your products from ordinary to extraordinary, opening up new possibilities for design, functionality, and cost – effectiveness. In this blog post, we’ll explore how custom injection molded parts can revolutionize your products and why they are becoming an essential choice for forward – thinking manufacturers.
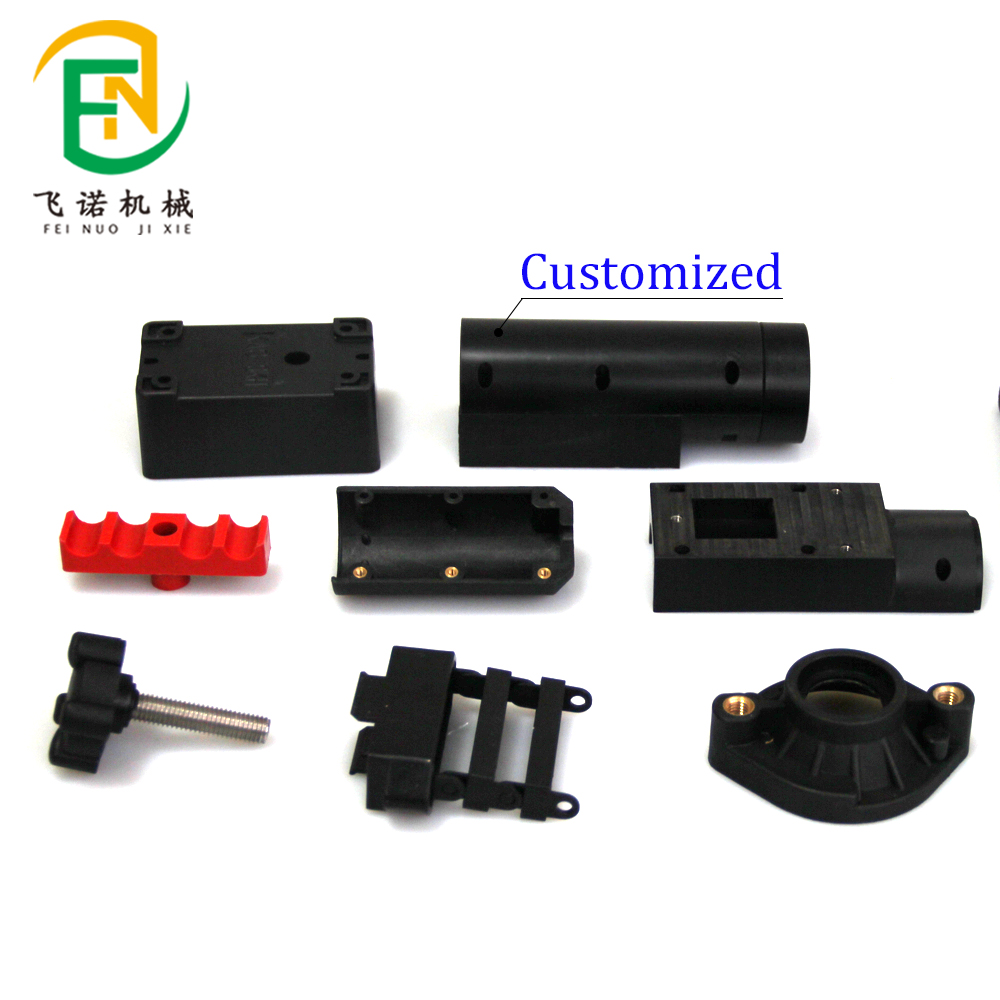
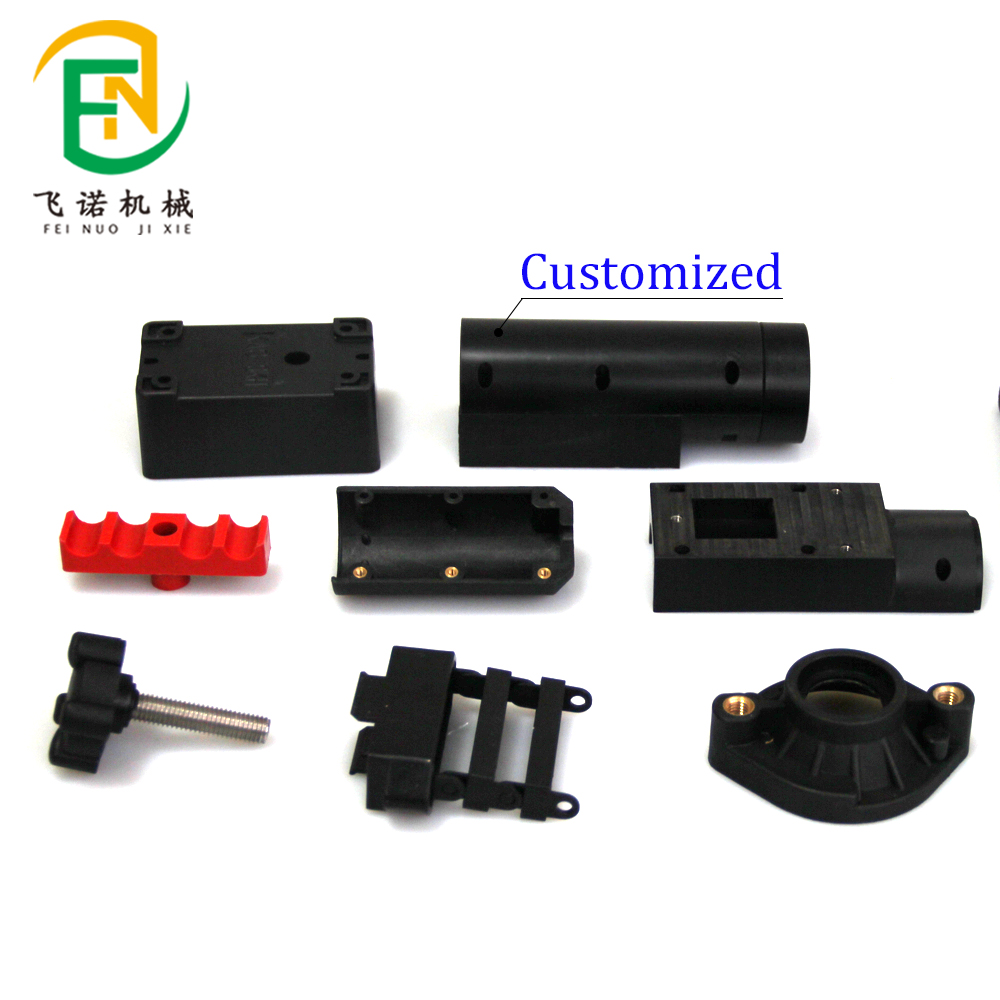
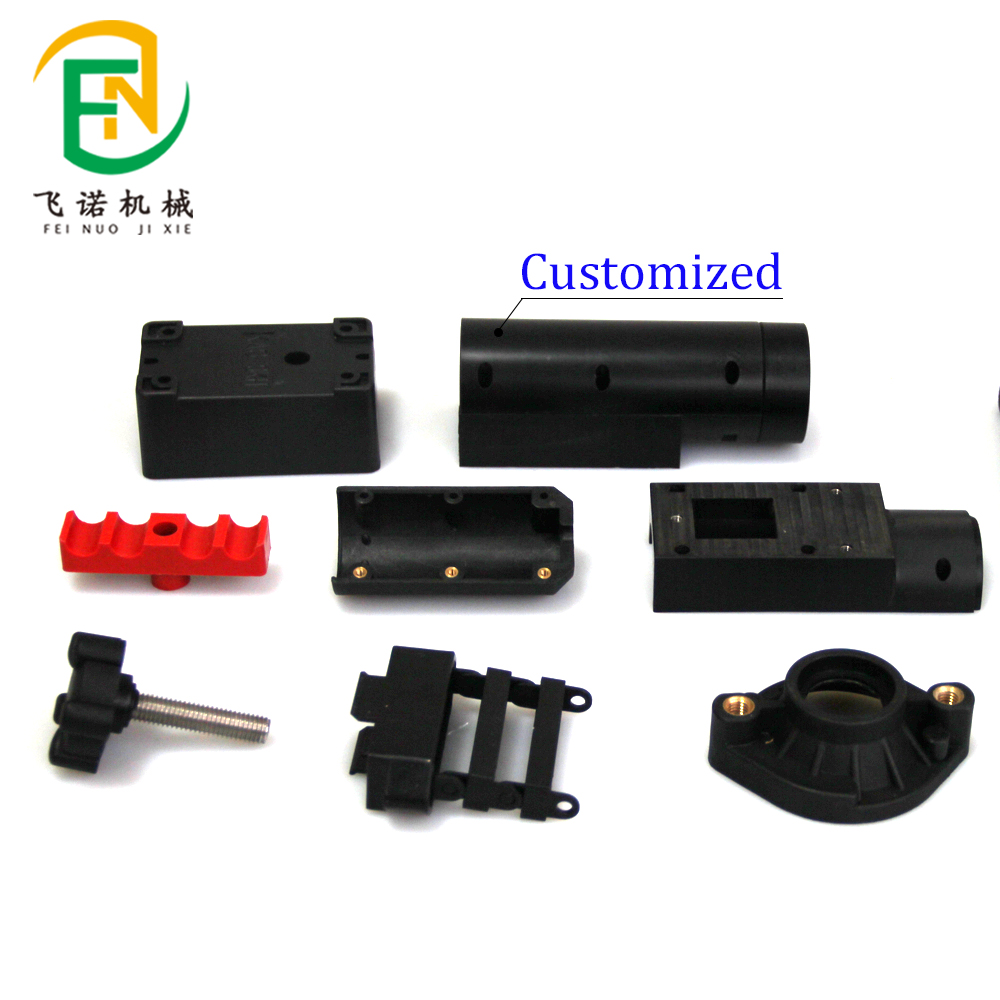
Understanding Injection Molded Parts
Injection molding is a manufacturing process where molten material, usually plastic, is injected into a mold cavity. Once the material cools and solidifies, it takes the shape of the mold. Injection molded parts can be made in a wide variety of shapes and sizes, from tiny components to large and complex structures. The materials used in injection molding range from common plastics like polyethylene and polypropylene to high – performance engineering plastics, offering different mechanical, chemical, and thermal properties.
The Advantages of Custom Injection Molded Parts
Cost – effectiveness
In the long run, custom injection molded parts can be extremely cost – efficient. Although the initial investment in mold creation may seem high, the cost per unit decreases significantly as production volume increases. This is because the mold can be used to produce thousands or even millions of parts, spreading the mold cost over a large number of units.
Design Freedom
One of the most remarkable advantages is the design freedom it offers. Designers can create intricate geometries, undercuts, and thin – walled structures that would be difficult or impossible to achieve with other manufacturing methods. This allows for the creation of products with unique shapes, improved ergonomics, and enhanced functionality.
High Production Efficiency
Injection molding is a high – speed manufacturing process. Once the mold is set up, parts can be produced in a matter of seconds to minutes, depending on the complexity of the part. This high production rate makes it suitable for large – scale production runs, reducing lead times and getting products to market faster.
How Custom Injection Molded Parts Can Revolutionize Your Products
Performance Enhancement
Custom injection molded parts can be engineered to meet specific performance requirements. For example, in the automotive industry, injection molded plastic parts can replace heavier metal components, reducing the vehicle’s weight and improving fuel efficiency. At the same time, by choosing the right materials and design, these parts can maintain or even improve the structural integrity and durability of the product.
Aesthetic Innovation
With the design flexibility of injection molding, companies can create products with sleek, smooth surfaces and unique shapes. This not only makes the product more visually appealing but also helps it stand out on the shelves. In the consumer electronics market, for instance, injection molded parts enable the creation of slim, stylish devices that consumers love.
Case Studies
Case 1: Consumer Goods
A leading consumer goods company wanted to launch a new line of kitchen appliances. By using custom injection molded parts, they were able to create a unique, ergonomic design that was easy to grip and operate. The parts were made from a heat – resistant plastic, ensuring the safety and durability of the appliances. As a result, the new product line was a huge success, increasing market share and customer satisfaction.
Case 2: Medical Devices
A medical device manufacturer needed to develop a new diagnostic tool. Custom injection molded parts allowed them to create a compact, lightweight device with precise internal components. The parts were made from biocompatible materials, meeting strict medical standards. This innovation improved the accuracy and ease of use of the diagnostic tool, leading to better patient outcomes.
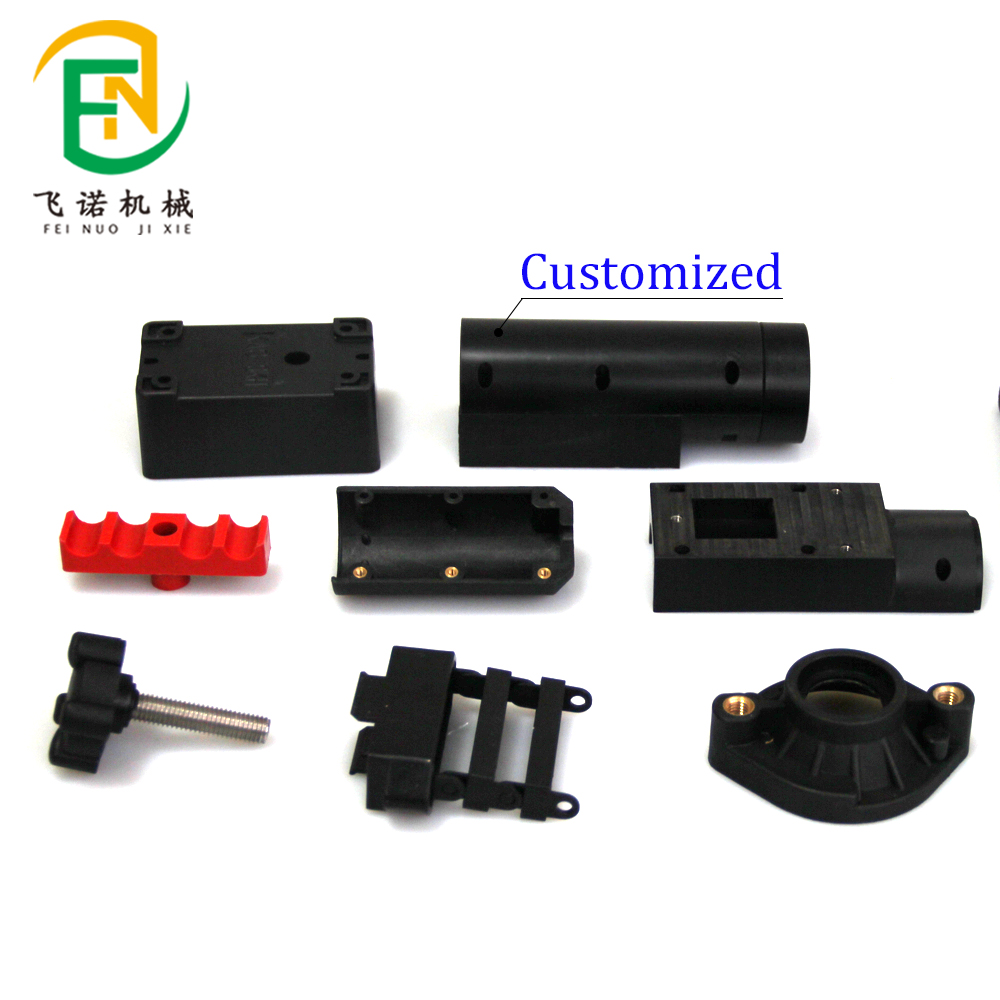
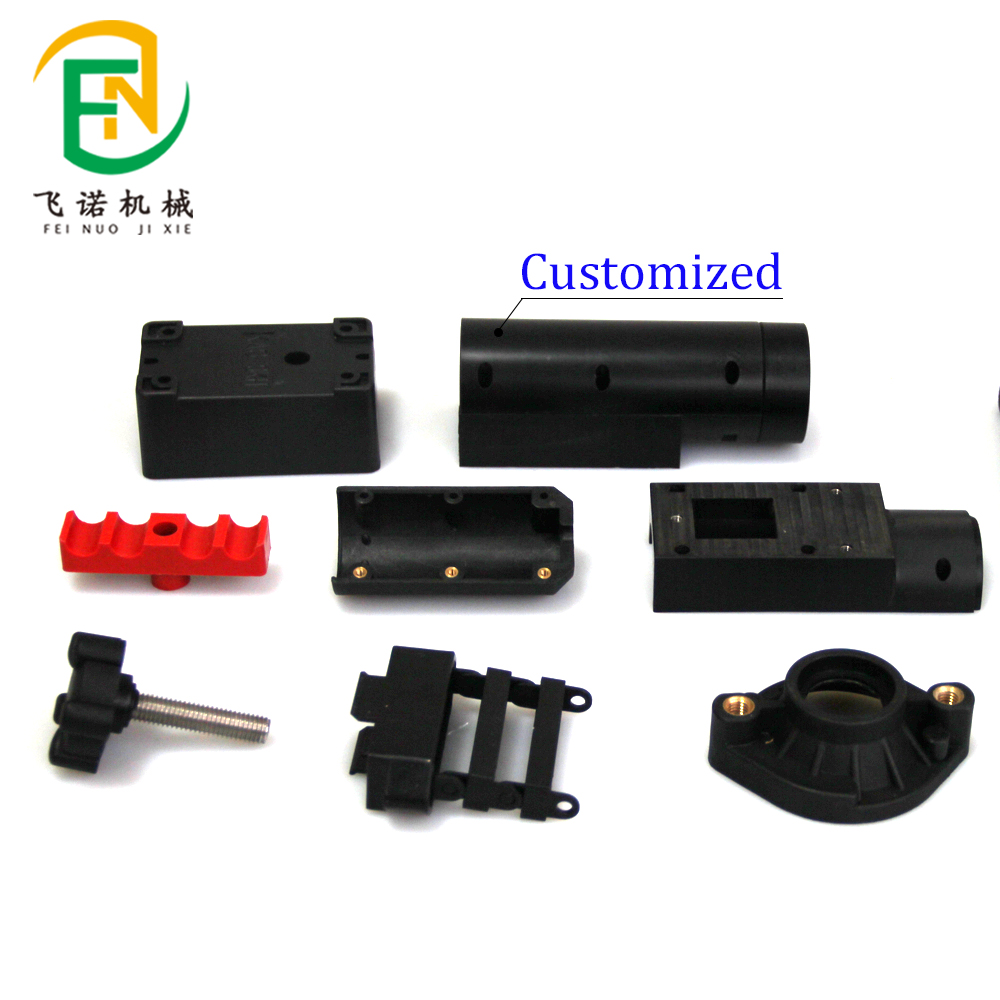
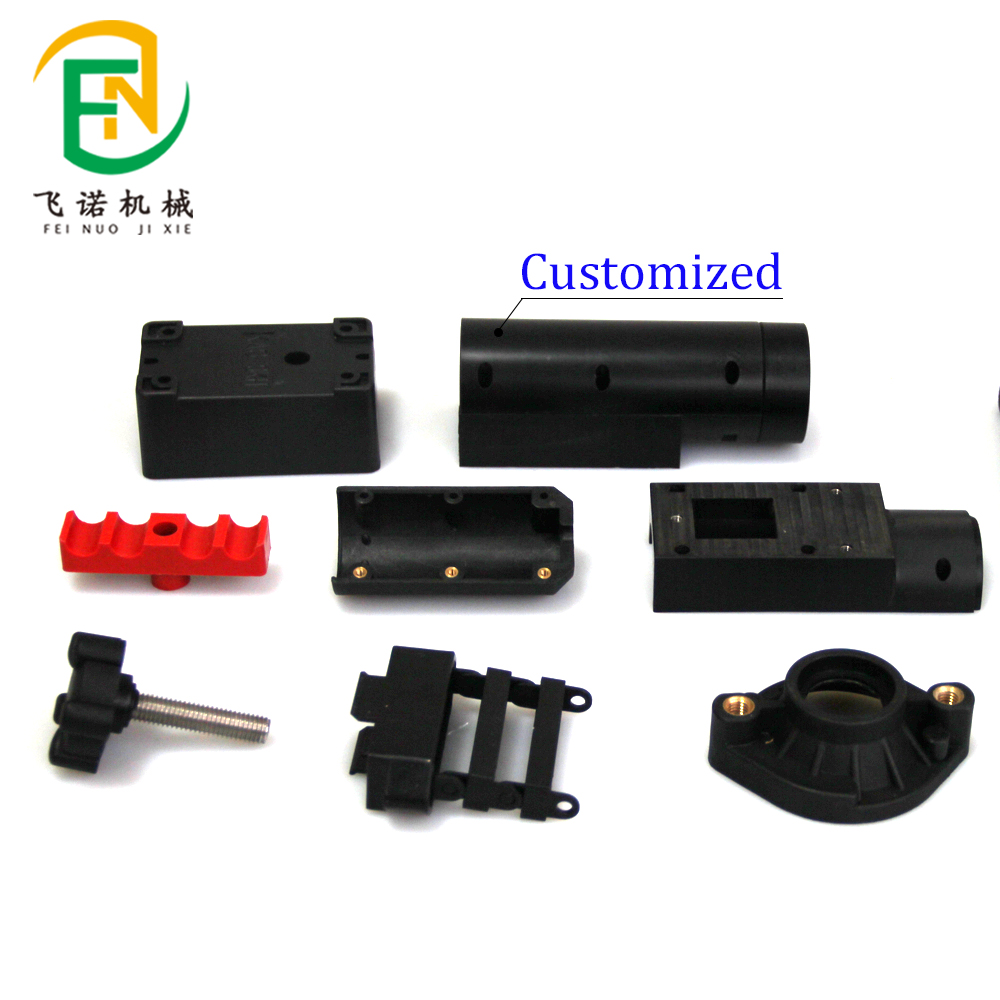
Choosing the Right Injection Molding Partner
Selecting the right injection molding partner is crucial. Look for a company with a proven track record, advanced manufacturing equipment, and a skilled engineering team. They should be able to provide design assistance, prototyping services, and high – quality production. Additionally, consider their ability to meet your production volume requirements, delivery schedules, and quality control standards.
Conclusion
Custom injection molded parts are a game – changer in the world of product manufacturing. They offer a combination of cost – effectiveness, design freedom, and high – performance capabilities that can revolutionize your products. By understanding the benefits of injection molded parts, learning from successful case studies, and choosing the right injection molding partner, you can take your products to the next level. Don’t miss out on the opportunity to leverage this powerful manufacturing technology and stay ahead in the competitive marketplace.