- April 18, 2025
- Posted by: feinuojixie
- Category: Injection Molding News
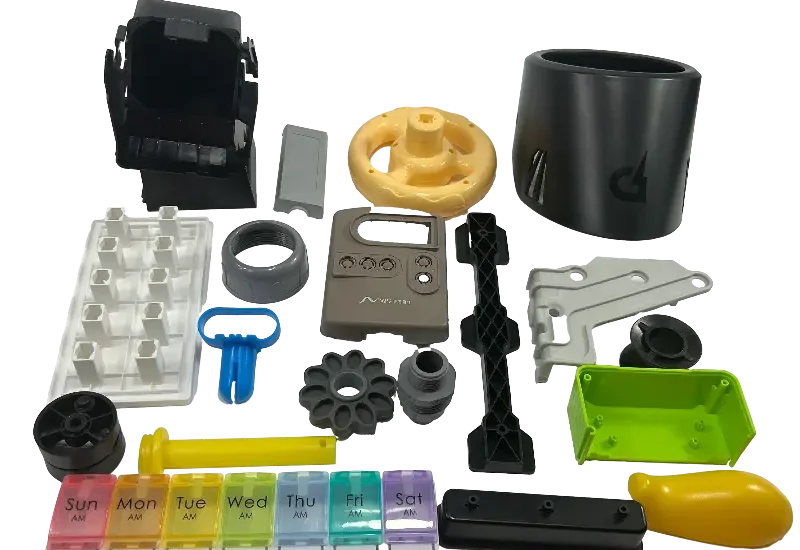
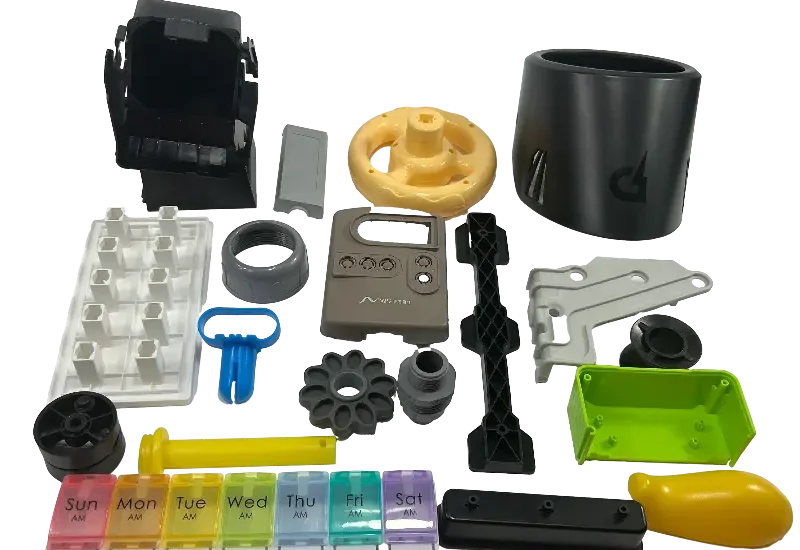
In a world where product longevity defines brand reputation and user trust, the durability of injection molding parts stands as a core pillar of successful design. Whether used in automotive components, consumer electronics, or industrial devices, these parts often face years of mechanical stress, environmental exposure, and repetitive motion. If they’re not designed for long-term use, performance failures and costly recalls can quickly follow.
Durability isn’t just about making parts stronger—it’s about designing them smarter. A part that performs flawlessly over time saves money, reduces waste, and ensures safety. That’s why understanding how to engineer injection molding parts for durability is critical for product developers, designers, and manufacturers alike. In this guide, we’ll explore the essential elements of long-lasting injection molded design, from selecting the right materials to refining geometries and stress points.
Understanding the Fundamentals of Injection Molding Design
Before mastering durability, it’s essential to grasp the foundational principles that guide injection molding part design. The process involves injecting molten plastic into a mold cavity, where it cools and solidifies into a final part. Durability begins here—with decisions made at the design stage.
Key factors like material flow, gate placement, and cooling rates directly affect the part’s final strength. If molten plastic doesn’t flow evenly, internal stresses or weak spots can form. Uneven cooling can cause warping or shrinkage, compromising fit and function. Understanding these factors allows designers to anticipate challenges and build resilience into the part from the start.
Choosing the Right Materials for Injection Molding Parts
The longevity of an injection molding part is largely dictated by the material it’s made from. Not all plastics are created equal—some are tough and impact-resistant, while others are brittle or degrade under UV light or chemicals.
For example, polycarbonate offers excellent toughness and clarity, making it suitable for parts requiring impact resistance. Nylon resists wear and absorbs stress well, ideal for gears or mechanical components. ABS balances strength and ease of molding but may not perform well under prolonged UV exposure.
Choosing the right resin involves more than just mechanical properties—it’s also about matching the part’s environment. High heat? Go for PEEK or PPS. Harsh chemicals? Consider fluoropolymers. The material you choose lays the groundwork for everything else.
Designing for Structural Integrity and Load-Bearing Performance
Durability means standing up to real-world forces, and that starts with smart structural design. Wall thickness, support features, and geometry all play critical roles in how injection molding parts handle loads over time.
Uniform wall thickness is key—it prevents uneven cooling and internal stresses that lead to warping or cracking. Reinforcing ribs can add strength without excessive material use, but their placement and size must be calculated to avoid creating stress points.
Draft angles—small tapers on vertical walls—are also essential. They ensure easy ejection from the mold and prevent surface damage. Overlooking these details can weaken the part and lead to early failure in service.
Reducing Stress Concentrations in Critical Areas
Stress concentrations occur where forces are focused, often at corners, notches, or sudden changes in geometry. These areas are more likely to crack or deform under load, reducing the life of an injection molding part.
To combat this, designers should use generous radii instead of sharp corners and smooth transitions between different part features. Holes and cutouts should be placed strategically, away from areas under tension. By smoothing out geometry and spreading forces evenly, the risk of fatigue and breakage is greatly reduced.
Enhancing Durability with Proper Wall Thickness and Ribs
Wall thickness and ribs work together to create a lightweight yet durable design. However, too thick, and the part may suffer from sink marks or voids. Too thin, and it may be too fragile for its application.
The ideal approach is to keep walls as uniform as possible, with strategic variations where strength is needed. Ribs are a great way to reinforce areas under load without adding bulk. But they must be designed correctly—usually about 60% of the wall thickness and with rounded bases to avoid stress concentrations.
Properly balanced wall and rib design delivers both structural integrity and manufacturing efficiency.
Accounting for Environmental and Operational Conditions
Injection molding parts often have to perform in less-than-ideal conditions—exposed to heat, moisture, chemicals, UV light, or mechanical wear. Designing for durability means anticipating these challenges.
For high-temperature environments, materials like PPS or PEEK maintain stability and resist deformation. For outdoor applications, UV-resistant additives or inherently stable resins like ASA can prevent yellowing and brittleness. Chemical resistance is critical for parts exposed to oils, solvents, or cleaning agents.
Operational conditions matter, too. If a part is clicked or twisted frequently, it needs to be fatigue-resistant. Considering the lifecycle and exposure of a part ensures it holds up to real-world use.
Optimizing Mold Design for Long-Term Performance
A great part design is only as good as the mold that forms it. Mold design plays a huge role in part durability by affecting how material flows, fills, and cools.
Proper gate placement ensures even filling and avoids weld lines or weak spots. Venting allows trapped air to escape, preventing voids. Cooling channel layout impacts how evenly the part solidifies—uneven cooling causes warping, internal stress, and premature failure.
Durability-focused mold design takes time and precision, but it results in better part quality and longer performance life.
Quality Testing and Validation for Durability Assurance
Before going to market, injection molding parts must pass rigorous tests to prove they can handle the demands of their intended use. Skipping validation can lead to costly warranty claims or even dangerous product failures.
Fatigue testing simulates repetitive use to uncover long-term wear issues. Impact testing ensures the part can withstand drops or shocks. Thermal cycling exposes it to temperature extremes to check for cracking or warping.
These tests provide insights into potential failure modes and allow adjustments before mass production—saving time, money, and reputation in the long run.
Design for Maintenance and Serviceability
Durability isn’t only about resistance to wear—it’s also about how easily a part can be repaired, cleaned, or replaced. Designing with maintenance in mind extends the life of the entire product system.
Snap-fit joints, modular designs, and standardized fasteners allow for quick part replacements. Smooth surfaces reduce grime buildup and simplify cleaning. Labeling or color-coding can guide assembly or repair crews.
Thinking ahead about how a part will be used, maintained, and eventually serviced is a powerful tool in maximizing lifespan and sustainability.
Long-Term Thinking in Injection Molding Part Design
Creating durable injection molding parts is more than a checklist—it’s a mindset. It means thinking beyond just “what works today” and into “what will still work years from now.” From material selection and geometry to mold design and testing, every decision matters.
By focusing on structural integrity, environmental resistance, stress reduction, and quality validation, designers can produce parts that perform reliably throughout their lifecycle. In doing so, they reduce failures, cut costs, and build products that earn long-term trust. Mastering the secrets of durable design isn’t just good engineering—it’s good business.