- March 10, 2025
- Posted by: feinuojixie
- Category: Injection Molding News
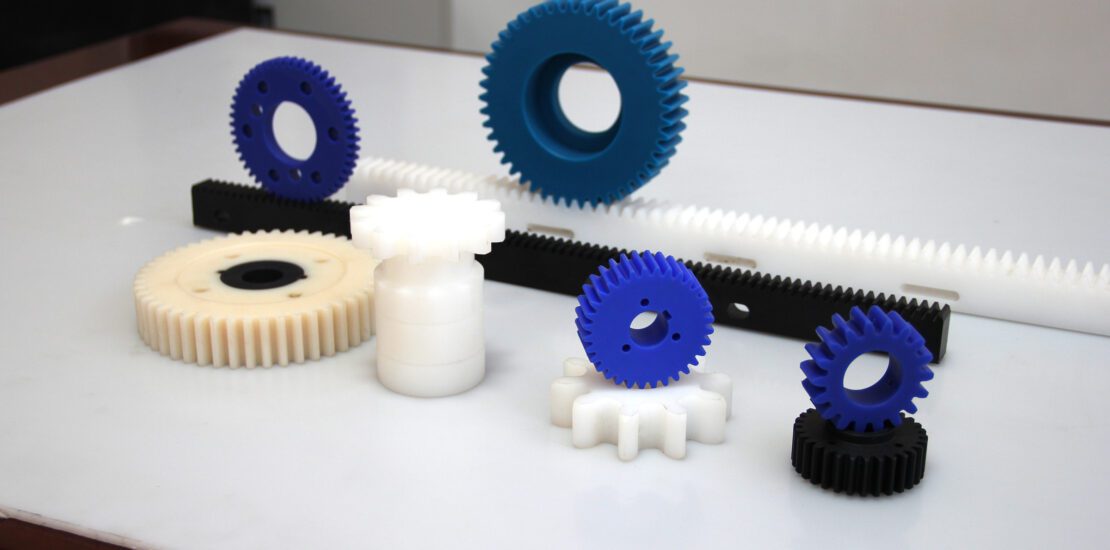
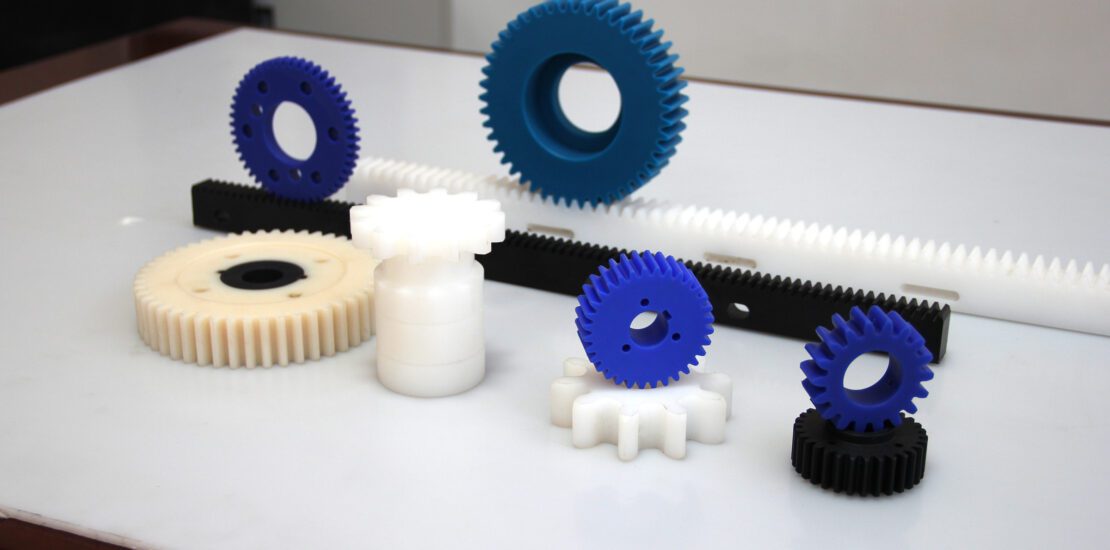
Injection moulding plastic part plays a vital role in modern manufacturing, offering precision, efficiency, and versatility across various industries. This article explores the art of creating high-quality injection moulding plastic part, detailing the process, benefits, industry applications, and key considerations for achieving perfection.
Understanding Injection Moulding Plastic Part
What Is Injection Moulding Plastic Part?
Injection moulding is a manufacturing process that involves injecting molten plastic into a precisely designed mould cavity. Once cooled and solidified, the plastic part is ejected, ready for use. This technique allows for the mass production of complex and durable plastic part with exceptional accuracy and consistency.
Key Components of an Injection Moulding Plastic Part
A well-crafted injection moulding plastic part depends on several critical factors:
- Material Selection – The choice of plastic resin affects the part’s strength, flexibility, and heat resistance.
- Mould Design – Precision-engineered moulds ensure repeatability and dimensional accuracy.
- Injection Moulding Machine – Advanced machinery controls temperature, pressure, and cycle time to optimize production.
- Cooling and Ejection Systems – Proper cooling ensures uniform part quality, while efficient ejection prevents defects.
The Manufacturing Process of Injection Moulding Plastic Part
Material Selection for High-Quality Plastic Part
Different plastic materials offer unique properties. For example:
- ABS (Acrylonitrile Butadiene Styrene) – High impact resistance and durability, ideal for automotive and consumer products.
- Polypropylene (PP) – Lightweight and flexible, commonly used in medical and food packaging.
- Polycarbonate (PC) – Strong and heat-resistant, perfect for electronics and aerospace applications.
Choosing the right material is essential to achieving the desired properties in the final plastic part.
Precision in Mould Design for Injection Moulding Plastic Part
A high-quality mould determines the accuracy of the final product. Factors such as wall thickness, draft angles, and gate placement must be carefully designed to ensure seamless production and defect-free parts. Advanced CAD software and simulation tools help engineers refine mould designs before manufacturing begins.
The Role of Temperature and Pressure in Moulding Plastic Part
Precise control of temperature and pressure is critical to maintaining the integrity of the plastic part.
- Temperature Regulation – Ensures uniform melting and solidification, preventing warping and shrinkage.
- Injection Pressure – Determines the flow of molten plastic into the mould cavity, ensuring complete filling and high structural strength.
Quality Control and Testing for Injection Moulding Plastic Part
To ensure defect-free production, manufacturers use various quality control techniques:
- Visual Inspection – Detects surface imperfections such as warping, flash, or sink marks.
- Dimensional Accuracy Tests – Ensures the part meets specified measurements using precision instruments.
- Mechanical and Stress Testing – Evaluates durability under real-world conditions.
Industry Applications of Injection Moulding Plastic Part
Automotive Industry: Enhancing Performance and Safety
Injection moulding plastic part is widely used in vehicle interiors, exteriors, and engine components. Lightweight yet durable plastic part contributes to fuel efficiency, safety, and overall vehicle performance.
Medical Sector: Precision in Healthcare Equipment
The medical industry relies on sterile and biocompatible plastic part for surgical tools, diagnostic devices, and pharmaceutical packaging. Injection moulding ensures consistent quality and compliance with regulatory standards.
Consumer Goods: Everyday Products with Superior Quality
From kitchenware to electronic enclosures, injection moulding plastic part is essential in manufacturing durable, aesthetically pleasing, and functional consumer goods.
Aerospace and Electronics: Meeting High Standards
In aerospace, injection moulding plastic part must withstand extreme conditions, while the electronics industry depends on precision-moulded plastic part for circuit board housings and connectors.
Advancements in Injection Moulding Technology
Automation and AI in Injection Moulding Plastic Part Production
Modern factories incorporate robotics and AI-driven quality control systems to improve efficiency, reduce defects, and enhance production speed. Automated monitoring ensures every plastic part meets strict quality standards.
Sustainable Injection Moulding Plastic Part: Eco-Friendly Innovations
With growing environmental concerns, manufacturers are adopting:
- Recyclable and Biodegradable Plastics – Reducing plastic waste and environmental impact.
- Energy-Efficient Machines – Cutting energy consumption while maintaining high production output.
- Closed-Loop Recycling Systems – Reusing scrap materials to minimize waste.
3D Printing and Rapid Prototyping for Injection Moulding Plastic Part
3D printing allows manufacturers to create prototype moulds quickly, enabling rapid testing and design adjustments before full-scale injection moulding begins. This reduces costs and development time.
Key Considerations for Choosing the Right Injection Moulding Partner
Expertise and Experience in Plastic Part Manufacturing
Choosing a manufacturer with extensive experience ensures high-quality results. Expertise in mould design, material selection, and process optimization is essential for producing durable and precise plastic part.
Customization and Scalability of Injection Moulding Plastic Part
A reliable manufacturer should offer flexible solutions to accommodate both small-batch and large-scale production while maintaining quality standards.
Cost Efficiency and Lead Time in Production
Optimizing cycle time, material usage, and waste reduction can significantly impact cost efficiency. A well-equipped manufacturer can balance affordability with premium quality.
Conclusion
Injection moulding plastic part continues to revolutionize industries with its precision, versatility, and cost-effectiveness. By understanding the process, material selection, and technological advancements, businesses can achieve superior-quality plastic part tailored to their needs. As innovations in automation, sustainability, and 3D prototyping continue to evolve, the future of injection moulding plastic part promises even greater efficiency and design possibilities.