- March 18, 2025
- Posted by: feinuojixie
- Category: Injection Molding News
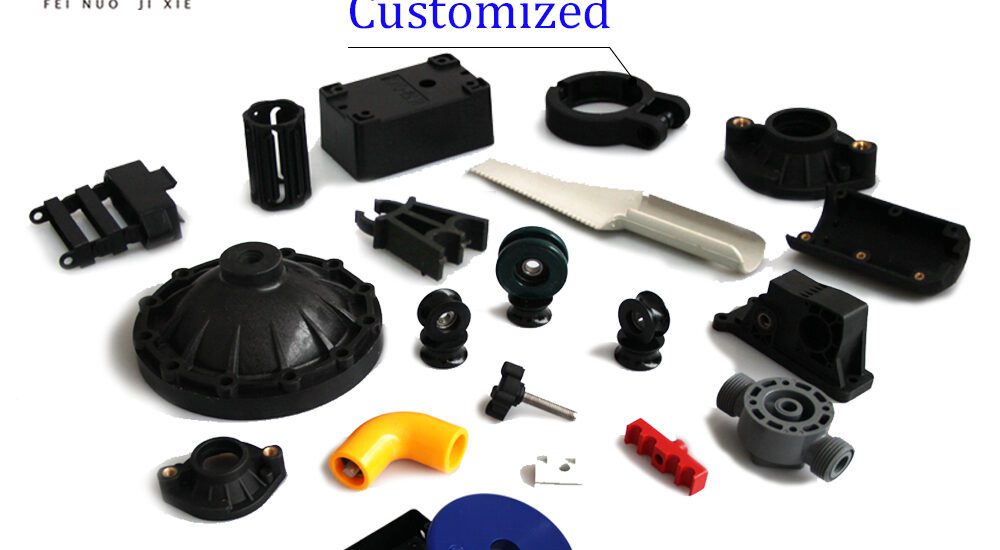
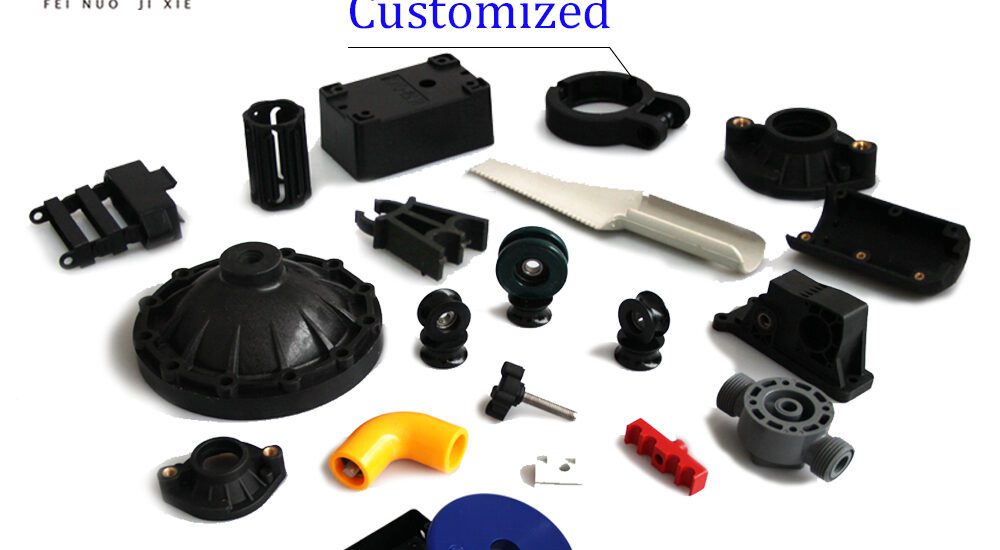
ABS injection moulding is a key manufacturing process that enables the production of high-quality plastic parts with exceptional strength, flexibility, and durability. ABS, short for Acrylonitrile Butadiene Styrene, is one of the most popular thermoplastics used in injection moulding due to its outstanding mechanical properties and ease of processing.
This guide provides an in-depth look into ABS injection moulding, from its material properties and step-by-step moulding process to its applications across different industries. Whether you are a manufacturer looking to optimize production or a designer interested in material selection, understanding the fundamentals of ABS injection moulding is crucial for achieving the best results.
What Is ABS and Why Is It Ideal for Injection Moulding?
Composition of ABS Plastic
ABS (Acrylonitrile Butadiene Styrene) is a thermoplastic polymer composed of three main monomers: acrylonitrile, butadiene, and styrene. Acrylonitrile provides chemical resistance and heat stability, butadiene enhances toughness and impact resistance, while styrene contributes to rigidity and a smooth surface finish. The combination of these elements makes ABS highly versatile and ideal for various applications.
Key Properties of ABS
ABS exhibits a unique balance of strength, flexibility, and durability. Its impact resistance allows it to withstand mechanical stress without breaking, while its moderate heat resistance ensures stability in environments with temperature fluctuations. Additionally, ABS has good electrical insulation properties, making it suitable for electronic applications.
Why ABS Is Suitable for Injection Moulding
ABS is widely used in injection moulding due to its excellent flowability, allowing it to fill complex moulds with fine details. It also has a relatively low melting point, which helps reduce energy consumption during the moulding process. Furthermore, ABS can be easily modified with additives to enhance its properties, making it adaptable for different industrial needs.
The ABS Injection Moulding Process: Step-by-Step
Material Preparation
Before the moulding process begins, ABS granules must be dried to remove moisture, as excess moisture can cause defects such as bubbles and weak spots. Proper drying enhances the final product’s quality and consistency.
Injection Phase
In this stage, ABS granules are heated in a barrel until they reach a molten state. The molten material is then injected into a mould under high pressure to ensure even distribution. The mould design plays a crucial role in determining the final shape, surface texture, and structural integrity of the part.
Cooling and Solidification
Once injected, the molten ABS starts cooling inside the mould. The cooling rate must be carefully controlled to prevent warping or shrinkage. Proper cooling ensures that the final product maintains its intended shape and dimensions.
Ejection and Finishing
After the part has solidified, it is ejected from the mould. Some parts may require additional post-processing, such as trimming excess material, painting, or surface treatment, to achieve the desired aesthetic and functional properties.
Advantages of ABS Injection Moulding
High Impact Resistance
ABS is known for its toughness, making it ideal for products that require durability, such as automotive components, toys, and protective gear.
Excellent Surface Finish
The smooth surface of ABS allows for easy painting, polishing, and texturing, providing flexibility in design and customization.
Cost-Effectiveness
ABS is an affordable material with a relatively low processing temperature, reducing production costs. Its recyclability also contributes to cost savings in manufacturing.
Chemical and Heat Resistance
ABS offers good resistance to many acids, alkalis, and oils, making it suitable for applications exposed to harsh environments.
Common Applications of ABS Injection Moulding
Automotive Industry
ABS is widely used in car interiors, dashboards, trim panels, and other components due to its durability and heat resistance.
Consumer Electronics
Many electronic devices, including laptop cases, phone housings, and remote controls, are made from ABS because of its insulating properties and aesthetic appeal.
Medical Equipment
ABS is used in medical devices such as casings for diagnostic equipment and handheld instruments due to its easy sterilization and impact resistance.
Household Products
From kitchen appliances to storage containers and toys, ABS is found in a variety of everyday household items thanks to its strength and processability.
Challenges and Solutions in ABS Injection Moulding
Warping and Shrinkage
Uneven cooling can lead to warping and dimensional inaccuracies. To prevent this, optimizing mould design and controlling cooling rates is essential.
Surface Defects
Issues like flow lines, bubbles, and sink marks can occur due to improper injection settings. Adjusting injection speed, temperature, and pressure can help eliminate these defects.
Mould Maintenance
Regular cleaning and maintenance of moulds are necessary to ensure consistent production quality and prevent defects caused by residue buildup or wear.
Tips for Optimizing ABS Injection Moulding Efficiency
Proper Mould Design
Ensuring uniform wall thickness, appropriate venting, and a well-designed gating system can improve product quality and minimize defects.
Optimal Processing Parameters
Maintaining the correct injection temperature, pressure, and cycle time helps achieve consistent results and reduces production waste.
Material Handling Best Practices
Storing ABS granules in a dry environment and using proper drying techniques before moulding prevents moisture-related defects and enhances final product quality.
Future Trends in ABS Injection Moulding
Sustainable Practices
With growing environmental concerns, manufacturers are incorporating recycled ABS materials and biodegradable additives to reduce plastic waste.
Advanced Manufacturing Techniques
Automation, robotics, and AI-driven quality control systems are improving efficiency, reducing defects, and optimizing production speed.
Innovations in Material Science
New ABS formulations with enhanced properties, such as higher heat resistance and improved strength, are expanding its applications in high-performance industries.
Conclusion
ABS injection moulding is a highly efficient and versatile manufacturing process used in various industries, from automotive to consumer electronics. Its durability, ease of processing, and cost-effectiveness make it a preferred choice for producing high-quality plastic components. By understanding the fundamentals of ABS injection moulding, optimizing processing techniques, and adopting innovative technologies, manufacturers can achieve superior results and stay ahead in an ever-evolving market.